Upfront Carbon Emissions in Home Construction
Choosing materials and methods that lower upfront emissions is key to reducing our climate impact.
The earth’s average temperature has risen by about 1.1°C (2°F) since the beginning of the Industrial Revolution. This increase has been caused mainly by human activities, especially the burning of fossil fuels, which release carbon dioxide (CO2) and other heat-trapping greenhouse gases into the atmosphere. The warming that has already occurred has increased the frequency and intensity of heat waves, droughts, floods, and tropical storms. It has also led to rising sea levels and larger, more destructive wildfires. According to the Intergovernmental Panel on Climate Change, even worse disruption can be avoided by keeping total warming below 1.5°C (2.7°F). To do this, we will need to cut carbon emissions in half by 2030.
While carbon has become a buzzword used to quantify climate impacts, the term is shorthand for CO2 and other greenhouse gases (GHGs). The terms low carbon and decarbonization refer to lowering GHG emissions. The construction and operation of buildings accounts for nearly 40% of global GHG emissions. This figure includes operational emissions, which are the GHGs that buildings (both new and existing) emit while in use, and upfront emissions—those released during the extraction, manufacturing, transportation, and assembly of building materials. Building codes like the IECC and certifications like the EPA’s Energy Star and the DOE’s Zero Energy Ready Home have focused on reducing operational emissions and energy consumption. But reducing upfront emissions, which occur before a building is occupied, is also critical to achieving the large, rapid cuts in GHG emissions needed to stay below the 1.5°C threshold.
The need to tackle upfront emissions comes at a time when the building industry is already struggling with labor shortages, material costs, and economic uncertainty. But there is some good news. Free software tools can help architects and builders calculate a project’s upfront emissions. These tools reveal that most emissions come from just a few building components. With smart design and materials selection, we can minimize or avoid the highest-emitting products. In the process, we can often achieve large reductions in climate impact at little or no added cost.
How homes contribute to greenhouse gas emissions
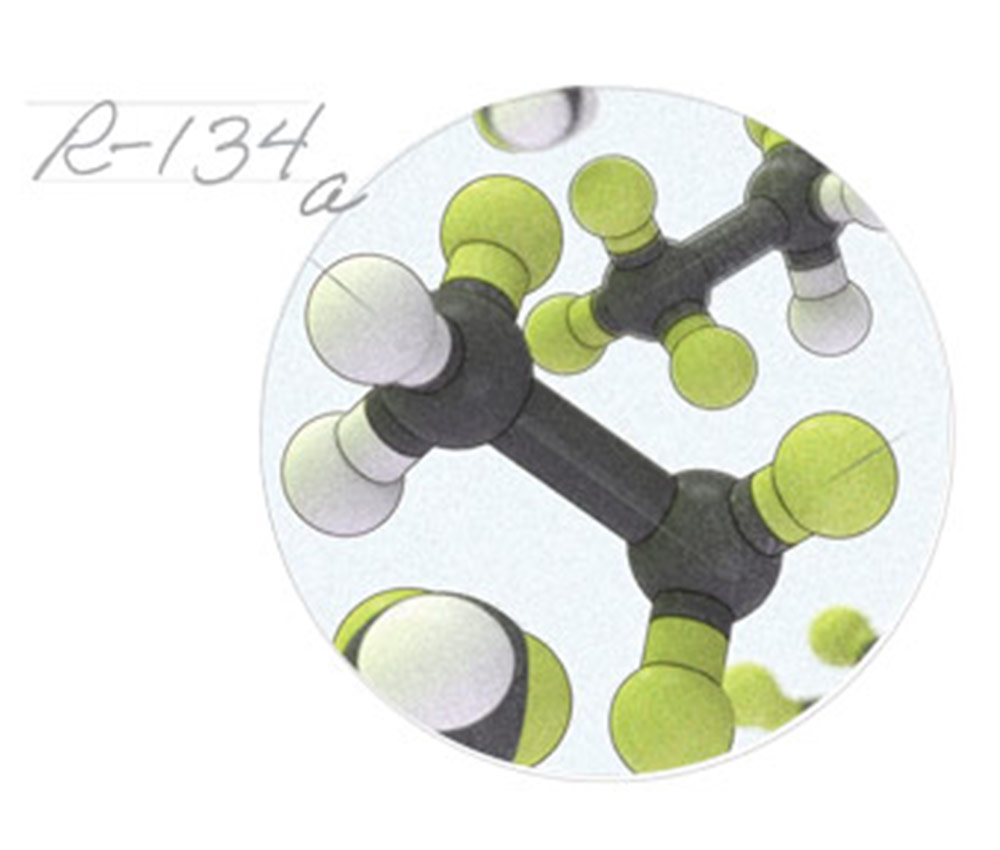
Carbon is an element in the periodic table that exists in various life-forming and life-sustaining molecule configurations. While carbon has become the term commonly used in the context of climate change, what we’re really talking about are greenhouse gases. These are the gases that trap heat in the earth’s atmosphere, raising global temperatures. The most common greenhouse gas emissions from the building industry are carbon dioxide (CO2), methane (CH4), nitrous oxide (N2O), and fluorinated gases like the HFCs used as refrigerants and in the blowing of some foam insulations. Deforestation, burning fossil fuels, agriculture, cement manufacturing, and other human activities have significantly increased the levels of these gases in the atmosphere. CO2 is the most prevalent of the greenhouse gases, and the rising concentration of CO2 is the primary cause of increases in global temperatures. In the carbon conversation, CO2 is often used as a catchall term to refer to all greenhouse gases and is used synonymously with the term carbon.
Focus on upfront emissions
In the last few decades, architects and builders have learned a lot about reducing energy use and operational emissions. We’ve gotten good at reducing heating and cooling needs through better insulation, meticulous air-sealing, and high-performance windows and doors. We’ve also found that we can eliminate the on-site burning of natural gas, oil, and propane by replacing fossil-fuel heating equipment, water heaters, and appliances with heat pumps and other all-electric technologies. The GHG emissions generated by an all-electric home are shrinking as fossil-fuel power plants are replaced by wind turbines and solar panels. This emissions-reduction pathway—efficiency, electrification, and decarbonization of the grid—works for both new and existing homes.
As we’ve learned to reduce the amount of GHGs buildings emit while in use, attention has turned toward the emissions associated with the building process. This is often discussed as embodied carbon emissions—a term that is similar to, but not synonymous with, upfront carbon emissions. Upfront emissions include the extraction, manufacturing, transportation, and assembly of building materials before a building is occupied. Embodied emissions include upfront emissions, plus any other nonoperational emissions that occur throughout a material’s life cycle (during maintenance or renovation, for example).
Carbon in conversationGlobal warming potential(GWP) measures the heat-trapping impact of a greenhouse gas over a specific time frame, usually 100 years. CO2, the most abundant greenhouse gas, is assigned a GWP of 1. GWP values express a gas’s warming effect relative to CO2. Methane has a GWP of 27.9; over a 100-year period, emitting a pound of methane causes 27.9 times as much warming as a pound of CO2. Some HFCs have GWP values greater than 800. GWP is used to calculate a product’s total climate impact, including CO2 and other greenhouse gases, in CO22 equivalents (CO2e). Life cycle assessment(LCA) is a procedure for evaluating a product’s environmental impact. This includes its greenhouse gas emissions from the extraction of raw materials through manufacturing, construction, active use, and end of life (“cradle-to-grave emissions”). Upfront carbon emissionsUpfront carbon emissions are CO2 and other greenhouse gases released during the extraction, manufacturing, transportation, and assembly of building materials—all of which occur before a building is occupied. Embodied carbon emissionsEmbodied carbon emissions refer to nonoperational greenhouse gas emissions that occur over the full life cycle of a building. This includes upfront emissions, and those that occur during maintenance and renovation and at the building’s end of life. Operational emissionsOperational emissions are the greenhouse gases emitted by day-to-day activities in an occupied building: heating, cooling, ventilation, lighting, and the use of appliances and electronics. Operational emissions include on-site burning of fossil fuels and the consumption of grid electricity generated from the burning of fossil fuels. |
The magnitude of upfront emissions can be quite large. A 2021 study by Passive Building Canada and Builders for Climate Action found that building a single-family home resulted in an average release of 40 metric tons (44 short tons) of CO2-equivalent GHGs (see “Calculating upfront emissions,” below). That is about as much as nine gasoline-powered cars emit in a year—and as much as the operation of that home might emit in decades of use.
Unlike operational emissions, which are spread out over several decades of a building’s life, upfront emissions are front-loaded; each new building puts a large pulse of GHGs into the atmosphere at the time of its construction. And unlike operational emissions, which can shrink over time as the electric grid shifts toward renewables, upfront emissions are locked in once the building is built. For these reasons, cutting upfront emissions is increasingly seen as key to the quick reductions needed to limit global warming to 1.5°C.
The World Green Building Council (WGBC) has set ambitious targets: a 40% reduction in embodied emissions by 2030, tapering to net-zero emissions by 2050—with “significant” upfront emissions reduction. Architecture 2030, a group focused on mitigating climate change, advocates for an even faster drawdown: 45% by 2025, 65% by 2030, and net-zero by 2040.
Calculating upfront emissions
A building’s total upfront emissions equals the sum of the upfront emissions from its components. These emissions are calculated by multiplying the quantity of each material used by the CO2 emitted per unit produced (plus the warming impact of other greenhouse gases, which are converted to CO2 equivalents, or CO2e). The total upfront emissions can then be reported as tons per building, kilograms per square meter, or pounds per square foot of living space.
Material quantities are relatively easy to calculate: cubic yards of concrete, squares of roofing, and square feet of insulation. Determining the CO2e emitted per unit of material is considerably more complicated. The process used to calculate these material emission factors is known as a life cycle assessment, or LCA. As its name suggests, a full LCA tallies a product’s CO2e emissions from “cradle to grave”—from the extraction of the raw materials through manufacturing, construction, use, and demolition or recycling. An LCA also looks at other impacts such as water use, smog, and ozone depletion. When looking at upfront emissions, the focus is on the product-stage (“cradle-to-gate”) emissions, which occur up to the point when the construction material leaves the factory, as well as on the emissions that take place during transportation to the site and during construction and installation.
Product-stage emissions include CO2e produced by logging and mining equipment and by the trucks, trains, and ships that transport materials to mills and factories. They also include emissions from electricity and fossil fuels used in manufacturing. In addition, they account for CO2e emitted by the raw materials themselves as they are processed. Looking at product-stage emissions can highlight the impacts of GHGs. Among the most important are hydrofluorocarbons (HFCs). HFCs are used as blowing agents in some types of extruded polystyrene (XPS) foam board and closed-cell spray foam. A pound of R-134a, an HFC used in XPS, causes 1430 times as much warming over 100 years as a pound of CO2 (i.e., its global warming potential, or GWP, is 1430).
Burning fossil fuels, blowing foam with HFCs, and heating limestone to make Portland cement all contribute to upfront emissions. By contrast, plant-based building materials, such as cellulose insulation made from recycled newspaper and cardboard, can store carbon captured from the air in a long-lasting building assembly. In the case of cellulose, this carbon would otherwise be released into the atmosphere as those waste products decay in landfills. Because the amount of CO2 captured and stored in cellulose during the growth cycle of the tree prior to its life cycle as a paper product exceeds the amount emitted in its manufacture, cellulose insulation is considered to have negative upfront emissions.
Concrete has a high cost, use a better mix and use less of it
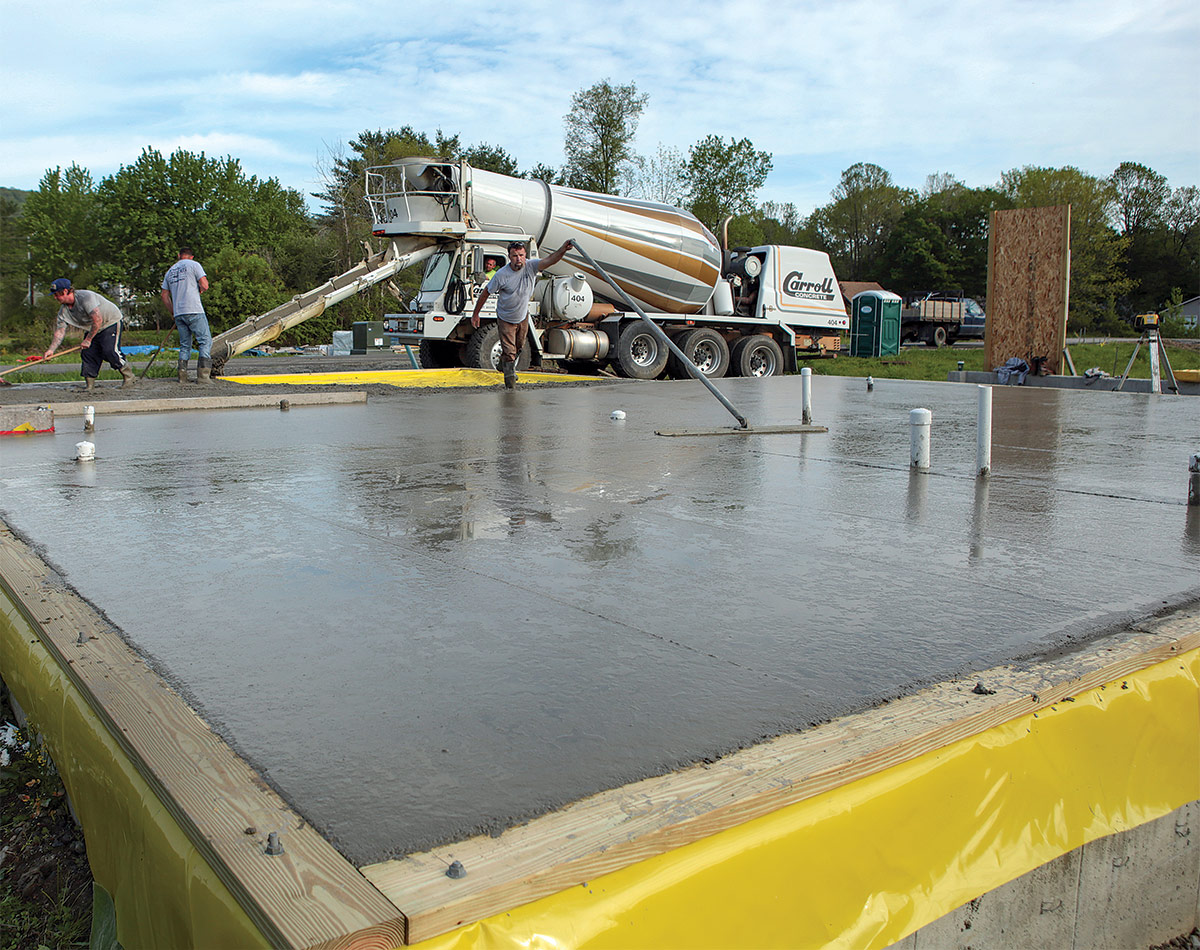
Humans produce more concrete than any other material. Its strength, durability, and low cost make it popular for buildings and infrastructure. But these benefits come with a hefty upfront cost: Concrete production accounts for 6% to 8% of global emissions. Conventional concrete is made by mixing Portland cement and aggregate (sand and gravel) with water. This mixture sets rapidly but continues to cure for several weeks. Although Portland cement makes up only about 15% of the mix, it accounts for about 90% of concrete’s total material emissions.
Manufacturing Portland cement is an energy-intensive process. The raw materials—crushed limestone and silica-bearing rocks or clays—are fed into a rotary kiln and heated to around 1450°C (2640°F). At these temperatures, the calcium carbonate in limestone breaks down into calcium oxide and CO2. The CO2 escapes into the atmosphere, while the calcium oxide combines with silicates to form calcium trisilicate. This emerges from the kiln as clumps known as “clinker,” which are ground into a fine powder to make the Portland cement. Producing a ton of Portland cement results in nearly a ton of emissions—about half from heating fuels and the other half from the chemical breakdown of the carbonate.
Portland cement is produced in large central plants, then shipped to local ready-mix facilities. There it is combined with water and aggregate and transported to job sites. Some is also used to make concrete masonry units (CMUs) and precast concrete assemblies. One way to reduce concrete’s upfront emissions is to reduce the amount of Portland cement in the mix. A fraction of the Portland cement—in some cases as much as 50%—can be replaced by gypsum, raw limestone, or a class of additives known as supplementary cementitious materials (SCMs). While some SCM-heavy mixes have longer setting times and less early strength, long-term strength and durability are unaffected. Common SCMs include fly ash, a by-product of coal-fired power plants, and mineral slag, produced in the smelting of iron ore. Certain clays, shales, and volcanic rocks can also be used as SCMs.
Architects and builders can reduce upfront emissions from concrete by designing structures to minimize below-grade walls. They can also specify low-carbon mixes that contain higher fractions of fly ash, mineral slag, and other SCMs. For slab-on-grade construction, using frost-protected shallow foundations (FPSFs) rather than conventional footers can also reduce concrete use. In CMU block walls, grouting only the top course and the cells that contain rebar can reduce the amount of Portland cement needed.
What about wood? Growing trees capture CO2 from the air, and some of this is stored in timber products in the home. But in a typical logging operation, less than 50% of a tree’s mass is used. The rest—roots, limbs, and branches—is left to decay, releasing CO2 back into the atmosphere. Logging and milling machinery contribute further emissions, as does the breakdown of organic matter when forest soils are disturbed and exposed to sun and rain. All these factors mean that while wood-based assemblies emit much less than comparable steel or concrete ones, they may emit more than they store, depending on the circumstances. Sourcing wood products from well-managed forests (such as those certified by the Forest Stewardship Council) can help. Many of the forestry techniques that lead to healthier ecosystems—building narrower roads, extending harvest cycles, and protecting sensitive sites—can reduce emissions.
Product-stage emissions can be found in the environmental product declarations (EPDs) provided by manufacturers or trade associations. The data has also been compiled in software tools, saving practitioners from having to track down EPDs for individual products. One such tool is BEAM (Building Emissions Accounting for Materials), a spreadsheet-based tool developed by a team led by Chris Magwood of Builders for Climate Action in Peterborough, Ont., and Jacob Deva Racusin of New Frameworks in Essex Junction, Vt.
Tools like BEAM can be used in multiple ways: to determine which components contribute most to a home’s upfront emissions, to explore how changes in design affect those emissions, to weigh options for specific components and assemblies, and to create benchmarks based on previous projects and “business as usual” construction that can be used to set reduction targets for current and future projects.
Magwood’s team used BEAM to calculate upfront emissions for 503 housing units in the Toronto area. As previously mentioned, the average emissions were 40 metric tons per home. The lowest emissions, 9.5 tons, belonged to a small townhouse. The highest, 827.1 tons, belonged to a 15,880-sq.-ft. mansion. More than 70% of the upfront emissions in these homes came from three components: concrete (33%), insulation (26%), and cladding (13%). A follow-up report by the Rocky Mountain Institute (RMI) found similar results in 418 homes in the European Union, British Columbia, and the southeastern U.S.
Insulation makes an impact, avoid foam when you canIn the climate story, insulation is both a hero and a villain. Installed properly, insulation can dramatically reduce the need for heating and cooling, shrinking both on-site fossil-fuel use and power-plant emissions. Well-insulated homes require smaller heating and cooling equipment, making them easier to electrify. But insulation materials, particularly foam boards and spray foams manufactured with HFCs, can be major contributors to a home’s upfront carbon emissions. Foam boards include extruded polystyrene (XPS), expanded polystyrene (EPS), and polyisocyanurate (polyiso). Until recently, the XPS available in North America had a major drawback: Its blowing agent—the gas that expands to create the pockets that give it its insulating properties—was a hydrofluorocarbon, HFC-134a. New XPS products with lower-GWP blowing agents are now available in some places, but even with these improvements, polyiso and EPS have much lower upfront emissions than XPS. Spray polyurethane foam (SPF) comes in two main types: open-cell and closed-cell. Much of the closed-cell foam used today is blown with HFC-245fa (with a GWP of 858), giving it very high upfront emissions. Within the last decade, closed-cell foams blown with low-GWP hydrofluoroolefins (HFOs) have become widely available, and some states have banned HFCs in closed-cell foams. Open-cell SPF has much lower upfront emissions than closed-cell SPF, because it is blown with water and CO2 and applied at a lower density. ![]() The energy-intensive manufacturing process of mineral wool contributes to its moderate upfront emissions. Fiberglass is manufactured using a process similar to mineral wool, but because the density of fiberglass batts is lower, so are the upfront emissions. Cellulose insulation is made with recycled paper, and manufactured using less energy than other insulation types. When installed in a building, cellulose stores the carbon that was photosynthesized by the trees it originally came from, instead of releasing it into the atmosphere as it decays. For this reason, cellulose is considered to have negative upfront emissions. How do we ensure that insulation keeps houses warm and the climate cool? Where appropriate, we can substitute low-emission insulation such as cellulose or wood fiber for higher-carbon alternatives like spray foam and mineral wool. For applications that require board insulation, we can select EPS or polyiso over XPS. When using closed-cell SPF, we can specify foam with HFO blowing agents. We can also look for low-emission ways to improve energy performance: air-sealing, duct sealing, and efficient HVAC equipment. A sliding scaleSome insulation materials have high upfront emissions, while others take very little energy to manufacture and are even carbon-storing once installed. The scale below shows upfront emissions for each insulation type at an insulating value of R-10. Values are expressed in kgCO2e/m2, which quantifies the total greenhouse gas emissions as a carbon dioxide equivalent. ![]() |
Practical steps
Concrete and insulation are the major players when it comes to upfront carbon emissions. Focusing on just these two components can produce large emissions savings at minimal expense. A 2021 report from RMI found that for a midrise, stick-built multifamily building, careful materials choices could reduce upfront emissions by 41%. These savings—achieved mainly by specifying low-carbon concrete and replacing high-GWP foam board with lower-emitting insulation products—would add less than 0.5% to the project budget.
Even deeper cuts can be made when upfront emissions are considered early in the design process. Efficient use of space is important; since upfront emissions scale with the quantities of materials used, they can be reduced by designing the smallest structure that meets the user’s requirements. Right-sizing structural components can also help; slabs, walls, floors, and roofs should be designed to meet the required loads but should not be overbuilt. Advanced framing reduces lumber use and thermal bridging while providing a sturdy structure. It can improve energy performance while cutting material costs and upfront emissions—a triple win. Some of the deepest cuts can be achieved by preserving and renovating existing buildings. This approach—which reuses energy-intensive structural components—can reduce upfront emissions by 50% to 75% compared to building new.
To achieve the rapid reductions in emissions called for by the WGBC and Architecture 2030, we’ll need to look at projects already in our pipelines. BEAM and other such tools can help us understand our starting points and identify the biggest—and most cost-effective—opportunities for reduction. Targeted changes to building design, together with a focus on low-carbon concrete and insulation products, can put us on the path to these goals.
Carbon calculations
The BEAM estimator is a free spreadsheet-based tool that can be downloaded from the Builders for Climate Action website. Users enter the dimen-sions of building assemblies, then select materials for each from the menus provided. BEAM then calculates the upfront emissions for each component and the building as a whole.
Material carbon emissions by section
Top 10 highest-impact materials
Jon Harrod is a writer, HVAC project manager, and building science consultant based in Ithaca, N.Y.
Drawings: John Schreiner
RELATED STORIES
- Systems and Products for an All-Electric Small Home
- Simple Techniques for Lowering the Cost of Zero-Energy Homes
- House+: Carbon and Energy Conservation
Fine Homebuilding Recommended Products
Fine Homebuilding receives a commission for items purchased through links on this site, including Amazon Associates and other affiliate advertising programs.
A House Needs to Breathe...Or Does It?: An Introduction to Building Science
Graphic Guide to Frame Construction
All New Kitchen Ideas that Work