On the Way to Net Zero
Renewables are part of the strategy to make a house energy-efficient, but conservation comes first.
Synopsis: This article is part two of the Fine Homebuilding House: California 2018 build, and describes the envelope details and mechanical systems chosen to make the house as energy-efficient as possible. The article includes details of the mineral wool insulation, window selection, and exterior air barrier, as well as the heating and cooling systems. A drawing of the mechanicals displays how the air-source heat pumps are the heart of the mechanical system along with a low-load HRV. The combination of these efficiency measures and building envelope details helps determine the size of the PV array needed to reach net-zero energy performance.
Once the majority of the structural framing is complete, we tackle the critical areas that affect its performance: air-sealing, insulation, and efficient mechanical systems. In a house that has a complicated air barrier like ours, some of the air-sealing and insulating happens during framing, so sequencing is key to not overlooking important air-sealing details. Once the performance of the building envelope is maximized and the mechanical systems are as efficient as possible, the amount of PV needed to take an all-electric house net-zero is more attainable. The goal isn’t to just put a lot of solar panels on a roof—it’s to use as little energy as possible and then offset this energy use to create a zero-net-energy (ZNE) home that is also comfortable and healthy. As Dave always says, it makes sense to go after the low-hanging fruit of efficiency first!
Our attention to a building’s comfort and efficiency always begins early in the design. Dave models our houses in the Passive House energy-modeling program WUFI to see the effects design decisions have on performance. The energy model—and our understanding of our microclimates—informs our decisions around insulation, windows, and mechanical systems. While our projects, including our home, usually far exceed the Title 24 requirements, we are mindful of the decisions we make along the way. We want to meet our performance goals, but we also pay attention to rebate opportunities in the California Advanced Homes Program by meeting benchmarks that earn a Tier 3 rating (the ZNE tier) and lower the HERS score.
Minimize air infiltration
On our house, we’re using plywood sheathing for the roof and walls because it’s more robust and stands up to water better than the commodity OSB we see on many local builds. The Delta-Vent SA that we use as a water resistive barrier (WRB) comes in 59-in.-tall rolls so that it covers the sheathing quickly like other building wraps, but this self adhesive product tenaciously sticks to our plywood sheathing, creating an effective airseal in one step. One of things we really like about using this product is that it’s part of a family of products; we don’t have to worry about compatibility issues between flashing tapes and WRBs. And because it’s a self adhesive WRB, it simplifies window flashing by sealing directly to the rough opening without additional flashing tape.
The plywood roof deck is the air barrier at the top of the house, as we have an unvented roof assembly. Here we taped all of the plywood seams with Delta Multi- Band as a belt-and-suspenders approach to ensure an airtight assembly. After the seams were taped we rolled out Delta-Vent S (not self-adhering) and underlayment, taped all seams, and taped the edges to the roof deck.
Follow the build in three parts• Foundation & Framing In this three-part series, we explore the design and construction of a new contemporary net-zero home in California. This installment recounts the efficiency measures and building-envelope details that will determine the size of the PV array needed to reach net-zero energy performance. Follow the build at FineHomebuilding.com/California2018 and via our social channels. |
Select efficient windows
During the design phase, we consider which window manufacturer makes sense for the performance of the house, the budget, and the aesthetic goals. We have installed Zola European Windows on several of our previous high-performance and Passive House projects and have found their price point to be better than comparable Passive House– certified windows. With a manufacturer like Zola, we are able to optimize the glassto- frame ratio and design for large glazing units. The triple-pane glass is not only less expensive than the frame, its performance is also much higher. So in our house there are a relatively low number of window units, but they have a large amount of glazing. The windows are tuned to allow for solar heat gain where needed, and we paired substantial fixed units with the operable tilt-turn units to get the most out of the overall window performance.
Target air leaks and thermal bridges
Air-sealing is critical to our house’s performance. Our practice is to place the air barrier at the exterior of the sheathing, for multiple reasons: We don’t have to worry as much about lighting-fixture selections or how to air-seal fire sprinkler heads, and it’s relatively easy for subcontractors to understand. also, when it’s on the sheathing, the air barrier is protected behind exterior insulation.
On past projects, we’ve achieved excellent blower-door results by taping the seams of all of our structural sheathing with flashing tape and then installing a water-resistive barrier (WRB) as a drainage plane. For our house, we’re doing the air-sealing and WRB in one step with dorken’s delta-vent S and Sa. it’s important to us that our assemblies are able to dry to both the inside and outside so that moisture vapor doesn’t get trapped. We use vapor-open WRBs/air barriers on the walls (the Sa) and the roof (the S) so that they work with our mineral-wool insulation on the interior and exterior to allow drying in either direction.
The flavors of mineral wool
Available in batt and board forms, mineral wool comes in different densities tuned to the application. ComfortBatt is the interior batt insulation. While it’s the least dense mineral-wool product used on this house, it’s significantly denser than fiberglass batts. ComfortBatts are slightly wider than the cavities they fill and the compression holds them in place.
The exterior walls are covered with ComfortBoard 110—the denser of the tworigid-sheet products commonly available. The denser version was chosen to lessen the chances of oil-canning with the metal cladding mounted directly to the Comfort- Board without battens. The same material is also used as subslab insulation.
The roof sheathing is covered with TopRock dd. This dense sheet product is intended for low-slope roofs and provides thermal properties and will mute the sound of rain on the metal roof.
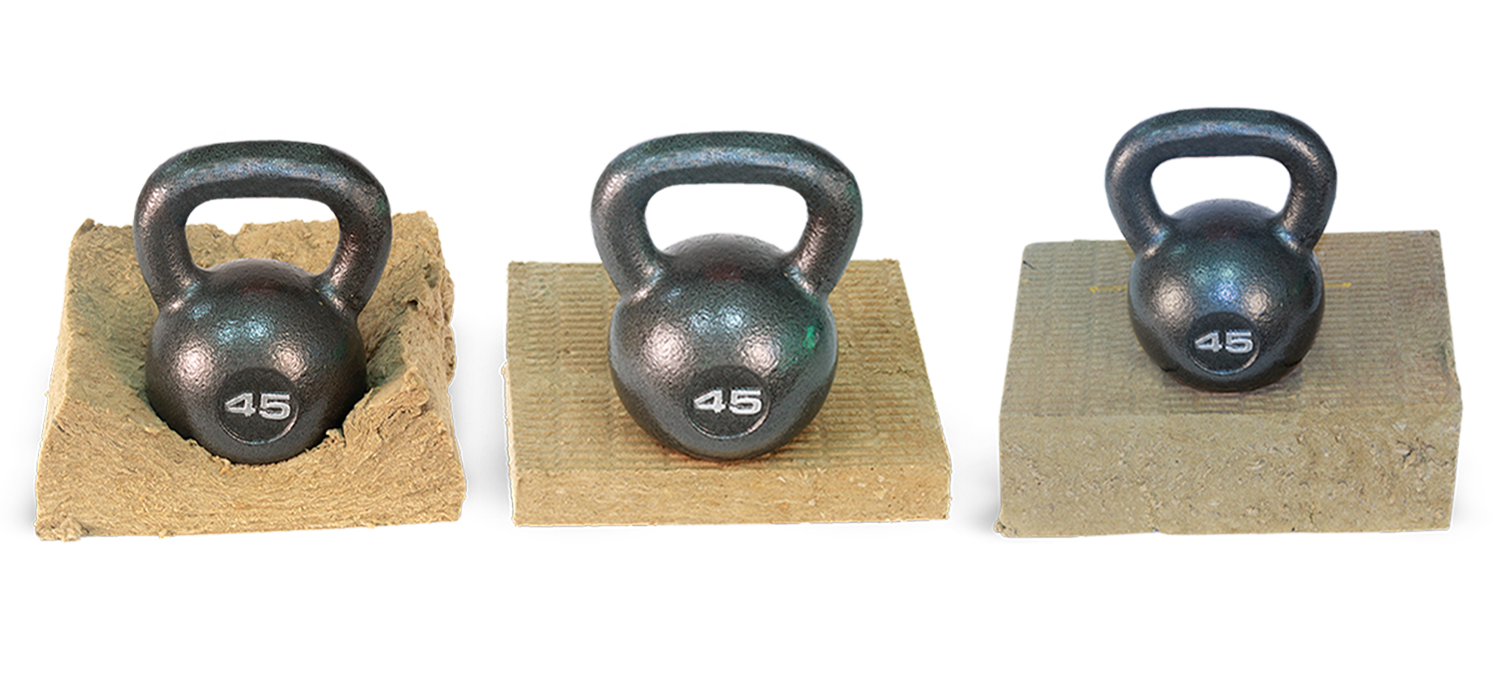
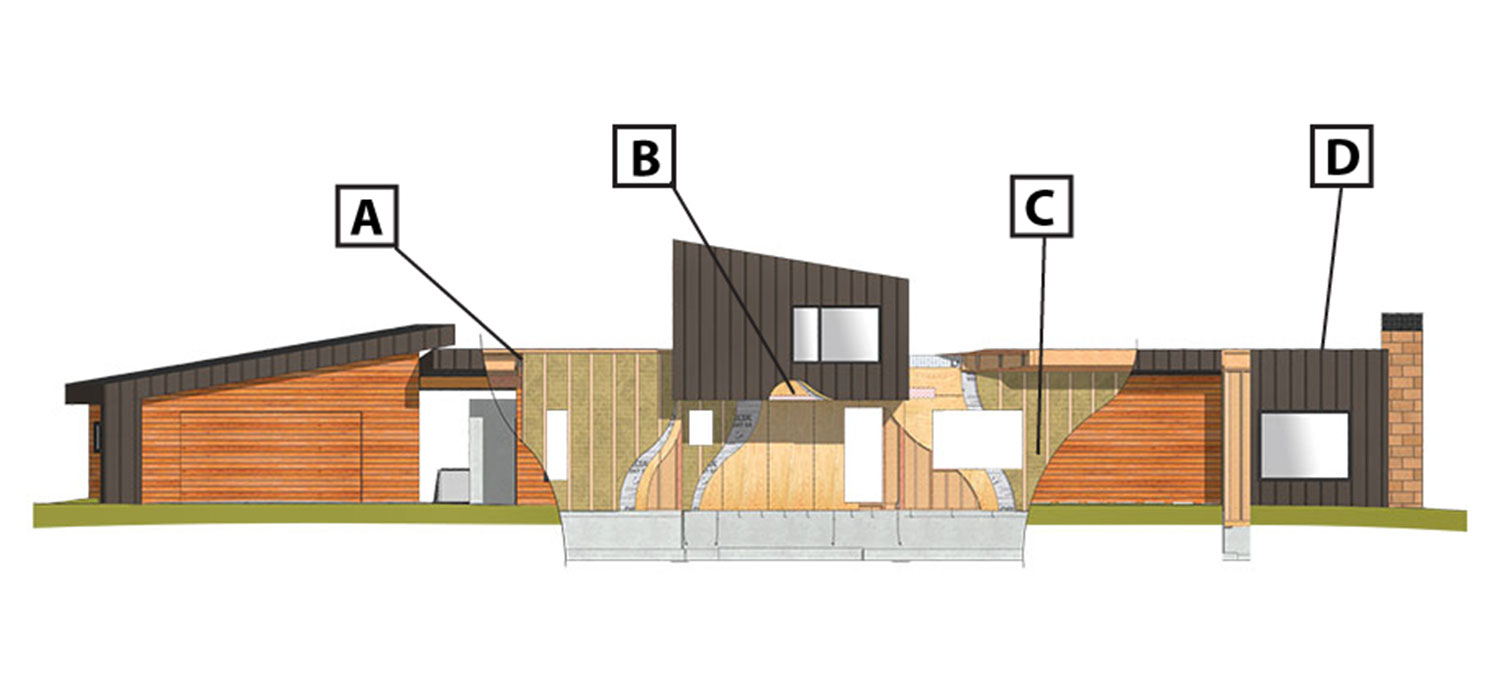
Insulation from rocks
With the air-sealing complete, we turned our attention to insulating the envelope. Our typical approach is to insulate on the interior and exterior and optimize the insulation values for the climate. To prevent condensation on the sheathing, we balanced the total amount of exterior insulation to be at least 30% of the interior cavity insulation. A house with a simple form and less surface area requires less insulation than we are putting into our house. With our complex architectural form, we had to boost our insulation values to reach the Passive House level of performance that we’re targeting.
We have an R-80 roof assembly, an R-39 wall assembly, and an R-60 elevated floor system. The cantilevered floor/porch ceiling at the front entry is treated as the mirror image of our roof assembly, with exterior insulation on the underside of the floor joists for a thermal-bridge-free floor that also reaches R-60.
We aren’t dogmatic about avoiding all foam products (we use them when dictated by budget or remodeling constraints). Our preference, though, is to use as little rigid foam or spray foam as possible. Building redundancies into high-performance assemblies makes sense to us, so we particularly like using mineral wool as the exterior insulation, as it is vapor open and ensures that our assemblies will have the ability to dry toward the interior or exterior. Manufactured from basalt and slag from the steel and copper industries, mineral wool is fire resistant, doesn’t off-gas, is bug resistant, and has no mold food source. On our house, we used Rockwool ComfortBatts to fill the 24-in.- o.c. framing bays, and they fit nice and tight into the wall framing on the interior. On the exterior, we used several different Rockwool board products. The board formulations are available in different densities, so we’re able to use it as subslab insulation, beneath the metal roofing and metal cladding, and with the cedar siding. The exterior insulation allows us to create a thermal break between the cladding and the framing. No good deed goes unpunished, though, and the trade-off of using exterior insulation is that trimming and detailing the cladding is trickier and more labor intensive.
Eliminate thermal breaks
To eliminate thermal bridges at porches, overhangs, and the balcony we used Maine Deck Brackets as standoffs between the framing and the element. At the south-facing second-floor master-bedroom balcony, these aluminum brackets act as a standoff for the ledger and we’re able to run insulation behind the balcony ledger with just a thin metal fin between the balcony and wall framing. Working with our structural engineer during the design process, we devised a way to hang the balcony with threaded rods off the roof system, so the second story appears to be one volume projecting out beyond the first story (yet the balcony is thermally broken from the house). Similarly, we detailed the uninsulated roof areas of the overhang and the porch with ledgers mounted to Maine Deck Brackets to allow for nearcontinuous exterior insulation. The porch and eave ledgers are installed 5 in. above the roof deck so that the plywood of these uninsulated roof sections aligns with the exterior roof insulation, creating a seamless plane.
European windows
We expect the air barrier to get us below 1.0 aCH50, but we want our house to have Passive House–level performance, so we’re aiming for 0.6 aCH50 or less. Past projects have taught us that once we’ve air-sealed the framing, the air leaks that we can’t address are through the windows and doors. Finding truly airtight windows and especially doors that are manufactured in the United States and that offer the aesthetic quality we seek remains an ongoing challenge. We want doors and windows that provide performance to match the rest of our assembly and that are wood clad and beautifully crafted. This is most important for the doors, as they are the most frequently used component and often one of the leakiest. We chose Zola european Windows and settled on their Thermo Clad line, as the glass package is well-suited for our climate and offers fours seals on the doors and operable windows for a very effective air-seal. The factory- finished interior is not only a higher quality than we can get with site finishing, but is less than the cost of having a painter finish raw wood.
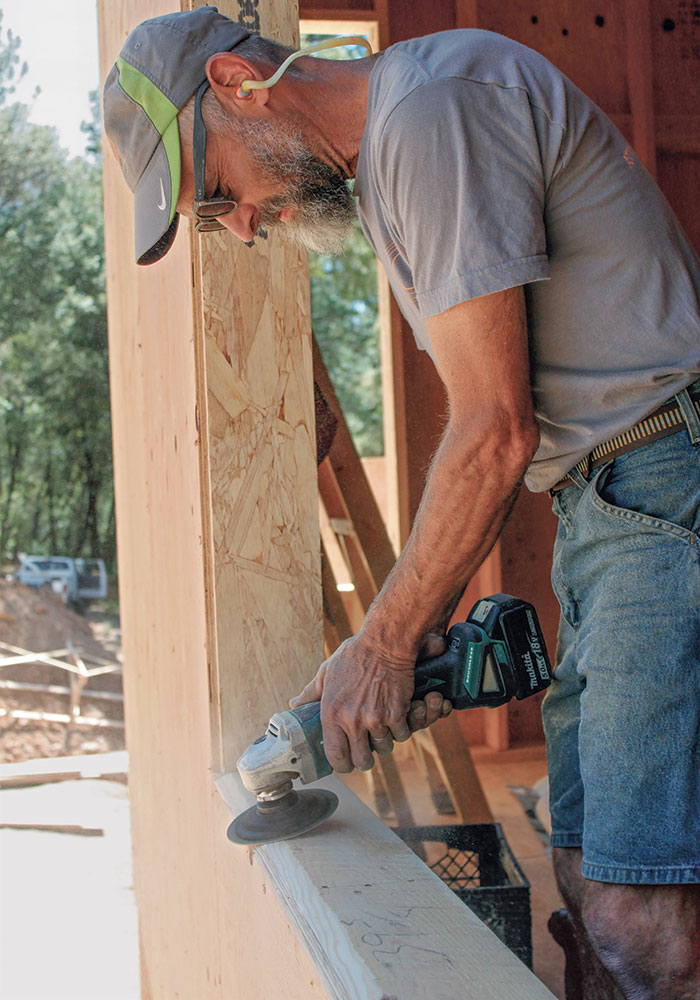
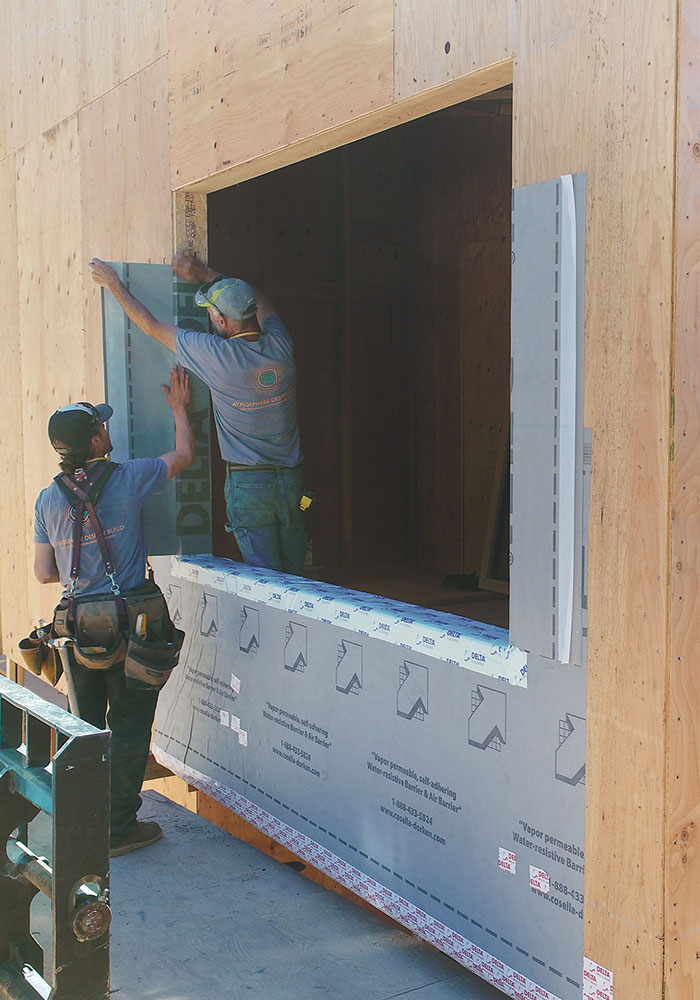
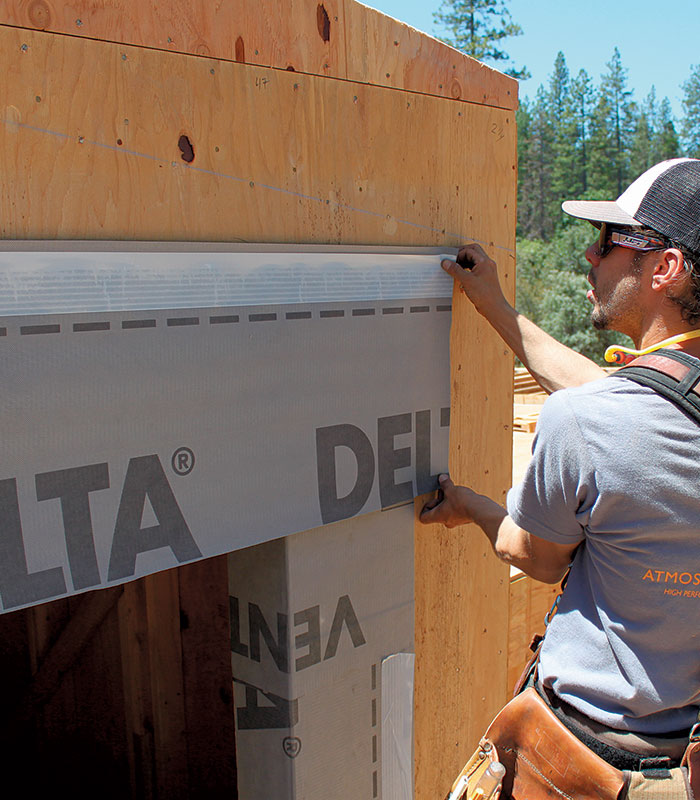
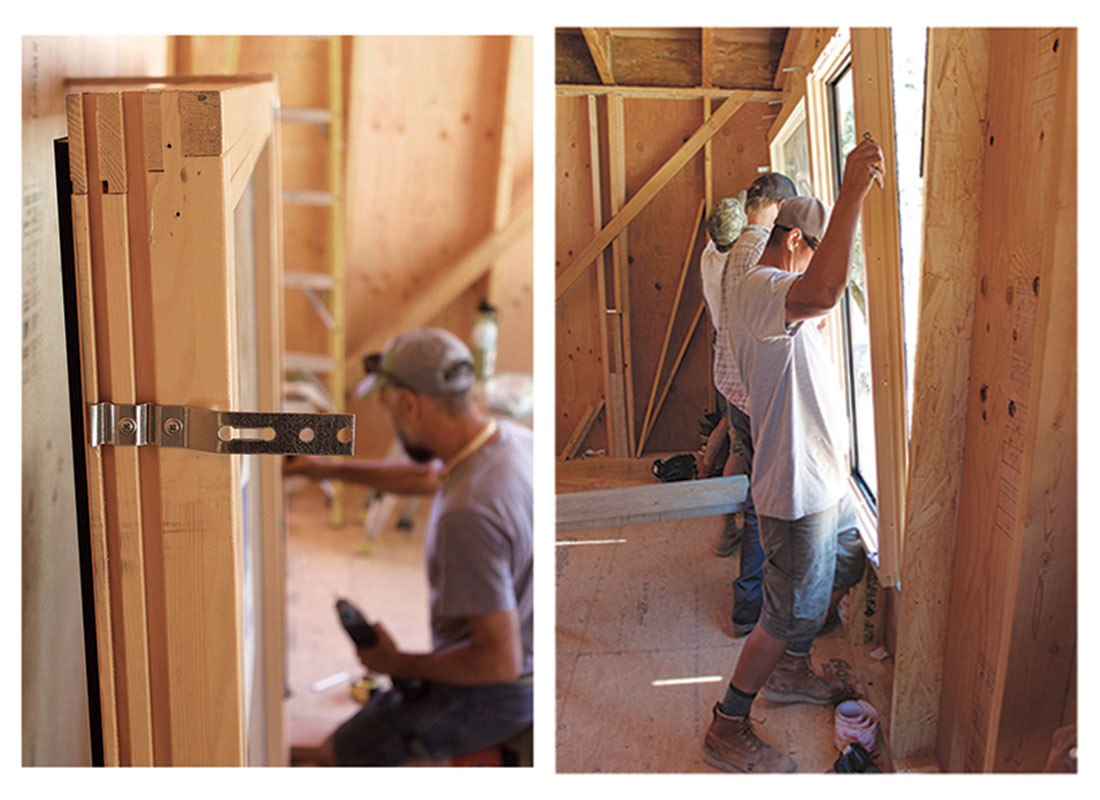
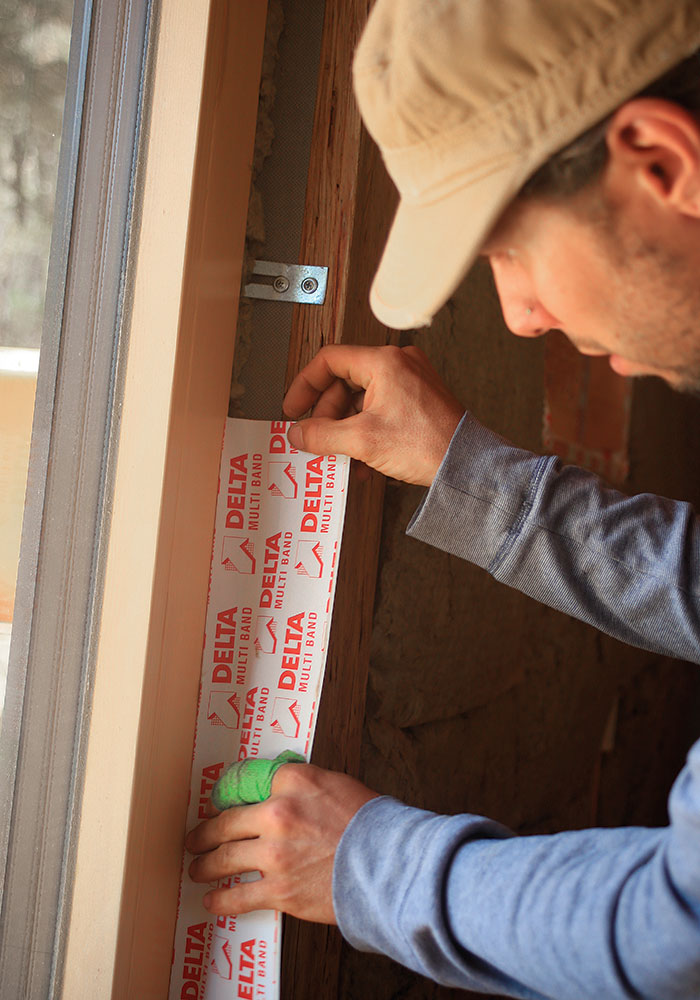
A small cooling system
Mitsubishi minisplits take care of the heating and cooling. We calculated heating and cooling loads for our home and found ourselves faced with an interesting challenge. The calculated loads for the home came to roughly 1 ton for the whole home. And while our house has low loads, it has some compartmentalization and is multiple stories. We wanted to be able to operate the home in two zones, upstairs and downstairs, and wanted to make sure that there wouldn’t be much room to-room variance in temperature. As Dan Perunko and Gavin Healy, our mechanical contractors at Balance Point Home Performance, say, “People often conflate efficiency and comfort, and while they intersect with each other, it’s important to figure out what expectations the occupants have for considerations like system responsiveness.”
Mela’s preference would have been to use a ducted unit for the obvious aesthetic reasons. However, ductless minisplits fit better into our budget, and we were able to meet the climate control goals with three ductless units. The downstairs load is 8000 Btu and the upstairs is 4000 Btu. The upstairs unit will likely be used more to meet cooling demand.
Because the first floor of our house is over 60 ft. long, it’s better suited to two wall heads to reduce hot and cold spots, but it’s unlikely that all three units will run at the same time. There may be times when just one of the smaller units is running (which allows for more adjustability, if, for instance, we want the bedrooms cooler for sleeping). Despite the high summer temperatures in our area, there should be long stretches when we let the air conditioners sit idle. With our tight, well insulated house and a typical 30° temperature swing at night, we can flush the house with cool night air and close it up during the day. However, the poor air quality that comes with more frequent forest fires and a longer fire season means this strategy isn’t always feasible.
The capacity of Mitsubishi’s smallest heads still exceeds the loads in our two smaller zones. However, by installing three completely separate minisplit units, our overall labeled efficiency is higher. And we expect that the separate pieces of equipment cycling independently from each other will minimize the potential inefficiencies that are driven by oversizing.
Mechanicals shrink the PV array
Heat pumps, which extract heat from one place and move it to another, are efficient because they have a COP greater than one—in other words, for each unit of energy consumed in operation, it can put out more than one unit of heating or cooling.
Air-source heat pumps are the heart of the house’s mechanical system—we use them for space heating and cooling and for domestic hot water. With Passive House–level airtightness, the house relies on an HRV for mechanical ventilation.
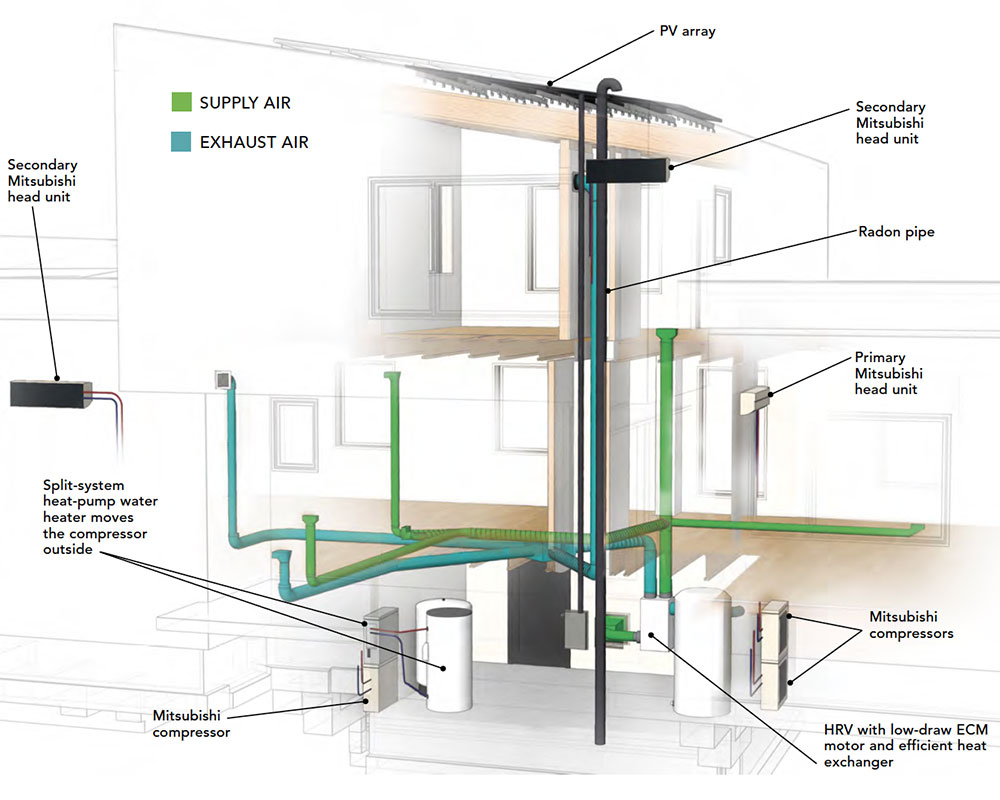
Low-load HRV
Residential indoor-air quality benefits greatly from mechanical ventilation and filtration and is a necessity in an essentially airtight house. Our mechanical contractors had in their inventory a European-manufactured HRV no longer sold in the U.S. and recommended it for our house. It checks all of the boxes we need in an HRV: It can be set up to automatically boost supply makeup air when the kitchen exhaust or laundry dryer is running, it has a low-draw ECM motor, and the heat exchanger is very efficient.
Heat pump with a twist
We’ve also chosen an air-source heat pump for hot water. The Sanden water heater is a unique product. The compressor is mounted outside with the minisplit compressors and it shares many of the same features: slimline construction, inverter motor, and ability to operate to -20°F. The outdoor compressor is able to heat water to 175°F. The compressor on more-conventional heat-pump water heaters is located with the tank and typically means cool air is dumped in the house during the heating season. With Sanden’s split system there’s no energy penalty in the winter. It doesn’t have a (comparatively inefficient) electric-resistance backup element, so we installed the 115-gal. tank for a high firsthour rating. The large storage tank allows us to load shift electric use by shutting down the compressor during high time-of-use rates and rely on the stored hot water. Also, the larger tank will allow for better tank stratification, which improves the performance of all heat-pump water heaters.
It’s important when selecting products to consider their life-cycle implications, not just their operating performance. That’s why we really like the CO2 refrigerant Sanden uses. It has a global-warming potential of 1, compared to the commonly used R138a with a global-warming potential of 1438.
Based upon our tight, well-insulated envelope and efficient all-electric mechanicals, we will easily be net-zero energy with the 6.5kw PV roof-mounted array. Often, we install smaller systems and then observe the occupant usage over a year to determine whether more panels are needed. But given that we are going after several rebates and incentives set to change in 2019, we opted for a PV system that will likely make our home net-positive and will keep us net-zero energy if we are able to get an electric vehicle at a later date. With the hard work of the performance details behind us, we’re turning our attention to the aesthetic details in the next installment.
2018 California SponsorsThe Fine Homebuilding House is supported by a host of industry sponsors. As a brand, we’re not comfortable telling you to put products in your homes that we wouldn’t put in ours. So, we’ve worked closely with our design and build team to identify appropriate products to include in this build. Our sponsorship model is built upon an invitation-only basis. Visit FineHomebuilding.com/California2018 for a complete list of project partners and for more information on the materials used in the build. |
Mela Breen and David Good are the founders of Atmosphere Design Build, a design/construction firm in Northern California.
Photos by Kevin Nielsen, except where noted.
From Fine Homebuilding #278
To view the entire article, please click the View PDF button below.
Plus, read about the overall design of this house:
View Comments
Very curious about the dryer vent which appear to have a pipe that exhausts to outside.
Where is the make-up air coming from for the dryer ?
Why not use a ventless dryer like a Whirlpool YWED7990FW (this is what we used in our air tight house)
Steve
Good work