Crown-Molding Fundamentals
Backing ripped from 2x4s and a well-planned crown-molding installation scheme take a lot of the guesswork out of this challenging job.
Synopsis: A finish carpenter describes the techniques and tools he uses to install crown molding quickly and accurately, and offers tips for dealing with out-of-square corners, wavy walls, and saggy ceilings.
The first time I installed crown molding, I couldn’t believe how easy it was. The builder I was working with knew exactly where every stud, truss chord and piece of blocking in the condo complex was located. The walls were flat, the corners square, and the ceiling level; there were no outside corners and no extra-long runs. I wouldn’t find out that I’d been lucky rather than smart until a year later when I tried to put up crown in an old Victorian town house, where nothing was plumb, level or square, and it seemed as if no framing existed beneath the plaster.
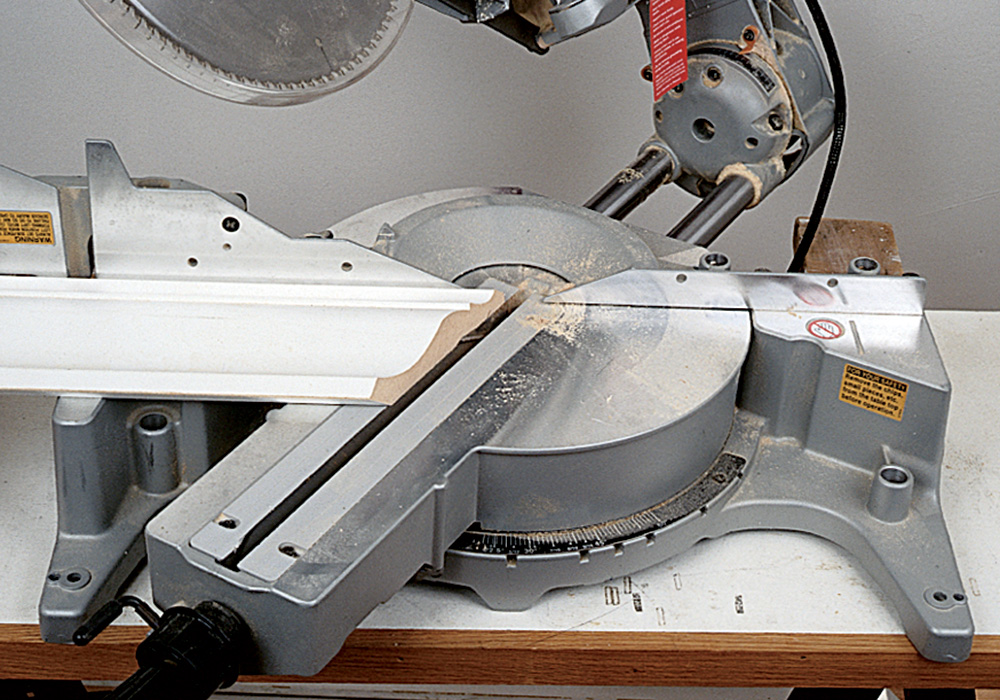
Angled between the ceiling and the wall, crown molding inhabits a three-dimensional space, making it one of the most demanding types of trim to install. When the wall turns a corner, crown makes two turns: One is along the ceiling plane, and one is along the walls, requiring compound cuts to join the pieces. Any discrepancy in either plane introduces a twist or bow that can alter the angles. Crown also is affected by shifting house movements acting on both planes, so it needs to be nailed securely to a stable surface to ensure that the joints don’t separate over time.
Every crown gets backing
Even when I’m following a first-rate framing crew, experience has taught me to check every corner with a framing square and to note any serious irregularities. (A gap between the square and the wall corner of even 1 ⁄8 in. can make it difficult to close the joint on a large piece of hardwood crown). At the same time, I eyeball the wall and ceiling intersection, looking for any irregularities that might hinder the crown molding from making full contact. If I encounter a saggy ceiling or a wavy wall, I take the time to figure out if corrective measures are needed.
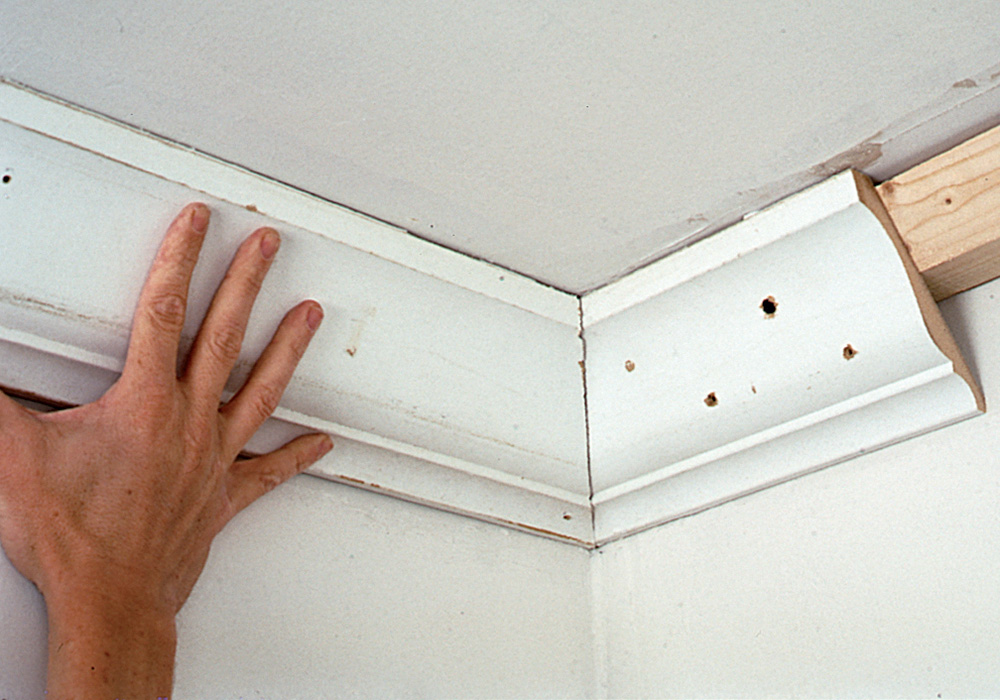
Even when everything is square and true, I still have to make arrangements for fastening the crown. Simply nailing into the studs and ceiling joists secures the crown only along the top and bottom edges. Inevitably, the edge splits, or the small finish nails don’t find good purchase and give out after a few years of seasonal movement. I avoid such aggravations by installing a backer of rough framing lumber that allows me to nail the crown wherever I want.
For modest-size crown, my typical backer is a straight 2×4 ripped at a bevel to match the spring angle of the crown. Rather than cut the backer to fill the space behind the crown completely, I lay it out and cut it so that the beveled face is about 1 ⁄4 in. shy of the back of the crown. This gap allows enough wiggle room to fine-tune the joints if needed. The crown still firmly contacts the ceiling and wall at the edges, but its meaty belly is pinned with a stout finish nail.
I find it’s usually easier to run the backer continuously. But if I’m running low on backer material or if I want to avoid high spots in the wall or ceiling, I may run the backer in sections—whatever it takes to give me nailing every 16 in. to 24 in. On walls long enough to require two lengths of crown, I figure out in advance where the joints will be and leave about a 16-in. gap between backer sections to accommodate the method I use to preassemble scarf joints.
Plan the installation to avoid double-coping
Before I start chopping up the molding, I scope out the installation order. To avoid coping two ends of the same piece of molding and to eliminate the time and fuss of resetting my saw for each cut, I try to set up all my copes on the same end of each piece. Most right-handers find it easier to cope right, butt left. The direction doesn’t matter as much as staying consistent; find what suits you and stick to it.
If the room has an outside corner, I usually start from there. Otherwise, I start with the trim on the longest wall opposite the door. I install this piece with one coped end and the other end butted square into the corner.
When I set up all the cuts in the same direction, the coped end of the first piece of the molding must be installed against a temporary block. This block is a scrap piece of crown, about a foot long, that is screwed temporarily to the backer. I nail the first piece of crown near the center and toward the butt end only. This placement gives me enough support to hold up the entire length of crown, but it leaves the coped end free so that I can slip the last full-length piece of crown in place of the starter block when I finally get there.
Pinch sticks make for easy, accurate measurements
Because joint compound tends to build up in the corners, it’s hard to get an accurate measurement by bending a tape measure into a corner. For long lengths of crown, I add a heavy 1⁄16 in. to all my measurements; then I put a slight back-cut on the square end. That way, even if the piece of crown is slightly long, it can be sprung into place, and the point at the crown’s bottom edge digs into the wall.
To measure for short lengths of crown, I always use pinch sticks, butting one end to the previously installed length and the other to the opposite wall.
By holding the two sticks together and sliding them until one end of each hits the wall, I get an accurate representation of the distance that can be transferred easily to the molding. Once I have the distance, I mark the sticks with two lines for positive realignment, and I use a spring clamp to hold the sticks together when transferring the length to the molding.
Outside miters must fit precisely
If the corner is crisp and square, I measure the length for an outside miter by holding the stock in place and marking the bottom edge of the molding where it meets the outside corner. (Bear in mind that drywall corner bead pushes the corner out slightly, so you may have to back-plane the miter to get a tight fit.)
Plaster corners may be rounded slightly, making it hard to measure the exact length along the crown’s bottom edge. If the walls are reasonably square to each other (and only the corner is rounded), I mark the ceiling by tracing along the top edge of a piece of molding, first along one side of the corner, then along the other. Where these lines cross on the ceiling marks the long point of each miter cut.
If you have to assemble more than one outside corner, consider cutting them all at once. I still try to map my cuts so that all the cuts for the copes angle the same direction. Rooms with bump-outs often have a few small pieces of crown. Wherever a small piece must be
coped on one end and mitered on the other, I cope the piece before I cut it to length. In this case, I might have to tack up the coped length of the outside corner temporarily so that it can be removed later to fit the last piece of crown that laps behind it.
Dual compound-miter saw makes cutting crown less confusing
If there’s any secret to cutting crown, it’s simply this: Keep track of which edge of the molding is the bottom and which edge is the top. Doing so eliminates a lot of head scratching when you’re standing at the saw trying to remember how the molding will sit when actually nailed into place. I try to group similar cuts together. That is, I first cut all the scarf joints, then cut all the outside-miter joints, then move on to the inside-corner cuts. This strategy saves time with any trim. But with crown molding, it’s especially helpful because it lets me keep track of the three-dimensional orientation of the molding. The methods you use to cut inside and outside corners depend on the type of saw you’re using. With a conventional miter saw—and narrow crown—I use a simple jig that holds the crown in the saw at the precise angle in which it will be installed (see “Choosing and Using a Miter Saw“).
Unless you’ve got a huge miter saw, such as the 15-in. Hitachi C15FB, you need to use a sliding compound-miter saw if the crown is wider than 51⁄2 in. A sliding compound-miter saw allows you to cut the crown flat on the saw table. With most sliding miter saws, the motor head pivots in only one direction; this means that you have to line up either the top or the bottom edge of the molding on the fence to get the cut in the right direction, so you wind up flipping material a lot.
Recently, I began using one of the new dual compound-miter saws. I admit I was skeptical at first that such a big lug of a saw would offer much of an advantage—unless I was dicing up huge pieces of lumber. But a dual compound-miter saw tilts in two directions, so you never have to flip the molding around. This is a big plus in a tight workspace. With the dual compound-miter saw, I always keep one edge against the fence and move the saw head to the left or right depending on whether I am cutting an inside or outside miter, left or right.
With any compound-miter saw, you still need to find the correct miter and bevel settings. These settings change, depending on the spring angle of the crown molding you’re installing, and there’s no obvious correspondence between all the angles. I always keep handy a chart that lists the angle settings for the most common spring angles. For moldings that aren’t included on the chart, I use the Bosch Miterfinder (www.boschtools.com) to calculate the angle settings, or I simply make a reasoned guess and cut a couple of test pieces until I get the angles right. Then I write those numbers down so that I won’t forget them.
Two tips to make the job go smoothly
Backing the crown means you never have to search for a stud. Framing lumber ripped to match the spring angle of the crown provides continuous nailing for the molding.
A framing square and a scrap of crown determine the backer dimensions. After ripping the material on a tablesaw, the author
uses 3-in. screws to attach the backer to the framing.
Installing crown to avoid double-coping. Starting off with a coped joint (fit to a temporary scrap of crown) ensures that the final piece of crown won’t have to be.
This one comes out. Held up with a pair of drywall screws, a scrap of crown serves as a gauge to cope the first piece of crown molding.
Coping inside corners
It’s possible to assemble inside corners with a miter. However, even if the corner is perfectly square, most miter joints open after a few seasons of expansion and contraction. I prefer to cope crown molding. A coped joint is a marriage of opposites. On one side, the molding is cut square and butts tight to the wall. On the other side, the molding is “coped” to match the profile of its neighbor.
A coped joint starts with a compound miter, the same as for an inside miter. The contoured edge along the face of this cut defines the profile to be coped. I mark the edge of this profile with the flat of a pencil lead so that it’s easier to see as I cut it with a coping saw. I always back-cut slightly by tilting the coping saw past 90° to ensure that the two pieces of molding intersect only along the profile line. When cutting with a coping saw, I typically saw toward the curve from different directions so that I don’t have to twist the saw and risk breaking the fragile edge of the profile.
Outside corners are simple…
Marking the long point is generally more accurate than marking the short point. To establish the long point of an outside miter, trace the top edge of a scrap of crown onto the ceiling, on both sides of the corner, then measure to the intersection of the two.
…unless they aren’t square
When I encounter an obtuse or acute angle corner, I use a couple of sticks and a bevel board to measure the exact miter angle. The bevel board is nothing more than a square piece of wood with some carefully drawn angled lines (from 0° to 90°). I made mine using a simple protractor and a sharp pencil. To get the exact bevel angle for an out-of-square corner, start with two short scraps of wood that overlap at the corner:
- Mark the long point of the angle on the upper piece.
- Mark the short point on the same piece.
- Find the angle on the marked piece with a bevel square.
- Then lay the bevel square on the bevel board and read the angle.
A more modern alternative is the Bosch DWM40L Miterfinder. This ingenious device can measure any angle to within one-tenth of a degree; then with the push of a button, it gives you the miter and bevel angles for any crown molding.
What to do when the wall is longer than the stock
If a wall is longer than the crown stock available, you need to splice (or scarf) two lengths together. Rather than attempt to fashion a good fit on the wall, I create my scarf joints first.
For scarf joints, I depend on two critical devices: a biscuit and a splint. I begin by cutting a 20° bevel and a 20° miter—or 20/20 compound cut—on one end, and a corresponding 20/20 compound cut on the mating piece. I prefer a compound cut because it’s easier to hide the joint; to make this cut on a standard miter saw, use the jig.
With the molding and the biscuit joiner lying flat on the same surface, I make biscuit slots in each piece.
The slot should fall in the center thickness, not through the contoured face of the molding. The long point of the bevel on the compound cut holds the biscuit joiner away from the surface in which the slot is cut, but by setting the biscuit joiner to a
maximum depth, I can fit a smaller #0 biscuit into the slot.
To fasten the two pieces more securely, I cut a strip of 1⁄4-in. thick lauan to act as a splint across the back and to bridge the joints. I fasten the splint with plenty of glue, using 1⁄2-in. staples and a standard staple gun to hold the strip until the glue
cures. After securing the splint to the scarf joint, I smooth out the joint with sandpaper. Until they’re securely fastened in place, I make sure to handle these scarfed pieces with extra care; they can snap in two easily.
Build a jig or buy a new saw?
If you have to cut crown on a standard miter box, an auxiliary plywood fence with a stop applied to the front edge ensures that the molding is held at the correct angle in relation to the blade (photo below). Because the saw head on a dual compound saw tilts in two directions, you never have to flip the molding around to set up the correct cutting angle, which is a big advantage when working in tight or crowded quarters.
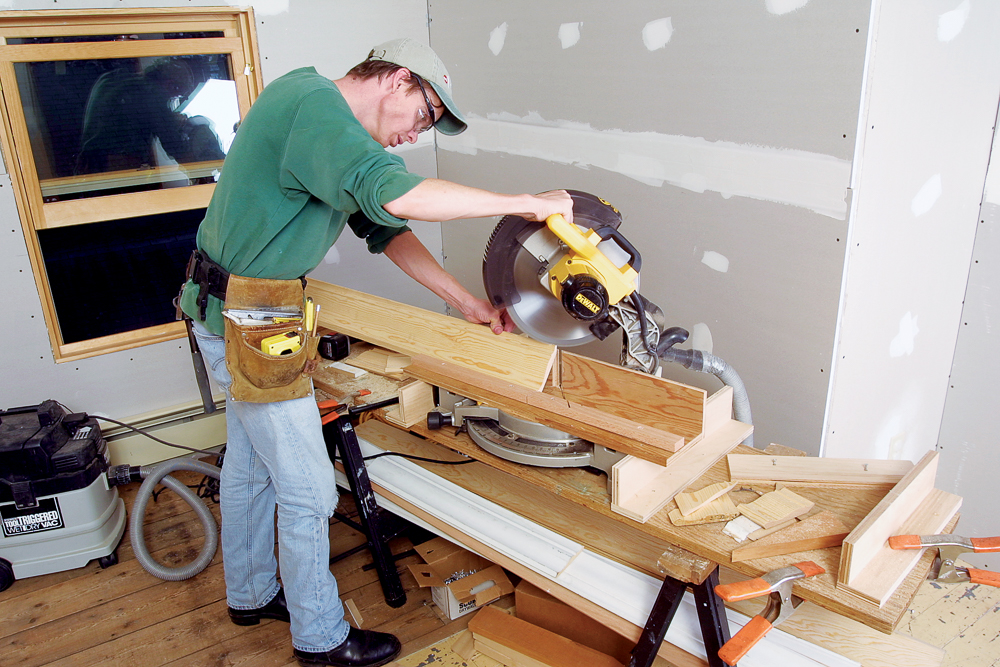
Saggy ceilings and wavy walls demand special attention
In old houses, where walls and ceilings aren’t smooth, I begin by mapping the planes with a level and string to find the low points on the ceiling. Long lengths of crown are surprisingly flexible and may move with gentle bumps and shallow dips. Most of the time, however, some remedy is required.
One way to solve this problem is to scribe the top edge of the molding to the ceiling. When scribing, I don’t want to bite too deeply into the top edge, or the scribe will be easily visible. Generally, I don’t remove more than a third of the top reveal.
Another fix is to skimcoat the wall or ceiling surface with plaster or joint compound to conceal gaps after the crown has been installed. In this case, I install the crown in line with the high spots. To float the mud, I make a screed from a short piece of mangled crown molding that has a notch in it that keys with the edge of the installed crown molding. This screed allows me to apply the mud to a depth that precisely covers the gap. I usually make the screed about 18 in. long, something that gives me a long, thin taper of mud that seamlessly feathers into the existing surface.
Drawings courtesy of Dan Thornton; Photos by Andrew Kline and Tom O’Brien
RELATED LINKS
- Upside Down and Backward Works Best for Crown Molding
- Crown-Molding Fundamentals
- The Secret to Coping Crown Molding
From Fine Homebuilding #152