A Fast Foundation for an Addition
Thanks to interlocking foam forms, you can form, pour, and insulate any small foundation in a single day.
Synopsis: Insulated concrete forms require no special tools, can be set up quickly and are accessible to do-it-yourselfers. A veteran concrete contractor takes us through the process of installing the forms and pouring the foundation for a family-room addition. Rebar installation and proper bracing are both discussed.
Four years ago, a builder asked me to form and pour a crawlspace foundation for a small addition using insulating concrete forms (ICFs). I had never worked with ICFs before. He was a good customer, though, so I rolled my eyes and agreed. I grabbed my friend and fellow contributing editor Mike Guertin, figuring we could muddle our way through just about anything. Less than two hours later, we were ready to pour, and I was sold.
Since then, I have used ICFs to form everything from full basements to two-story houses. Along the way, I’ve discovered many benefits of building with ICFs, but I especially like them for small-addition foundations, like the 18-ft. by 18-ft. foundation featured here, because they can be installed so quickly. In fact, I’ve talked contractors and homeowners through the process over the phone.
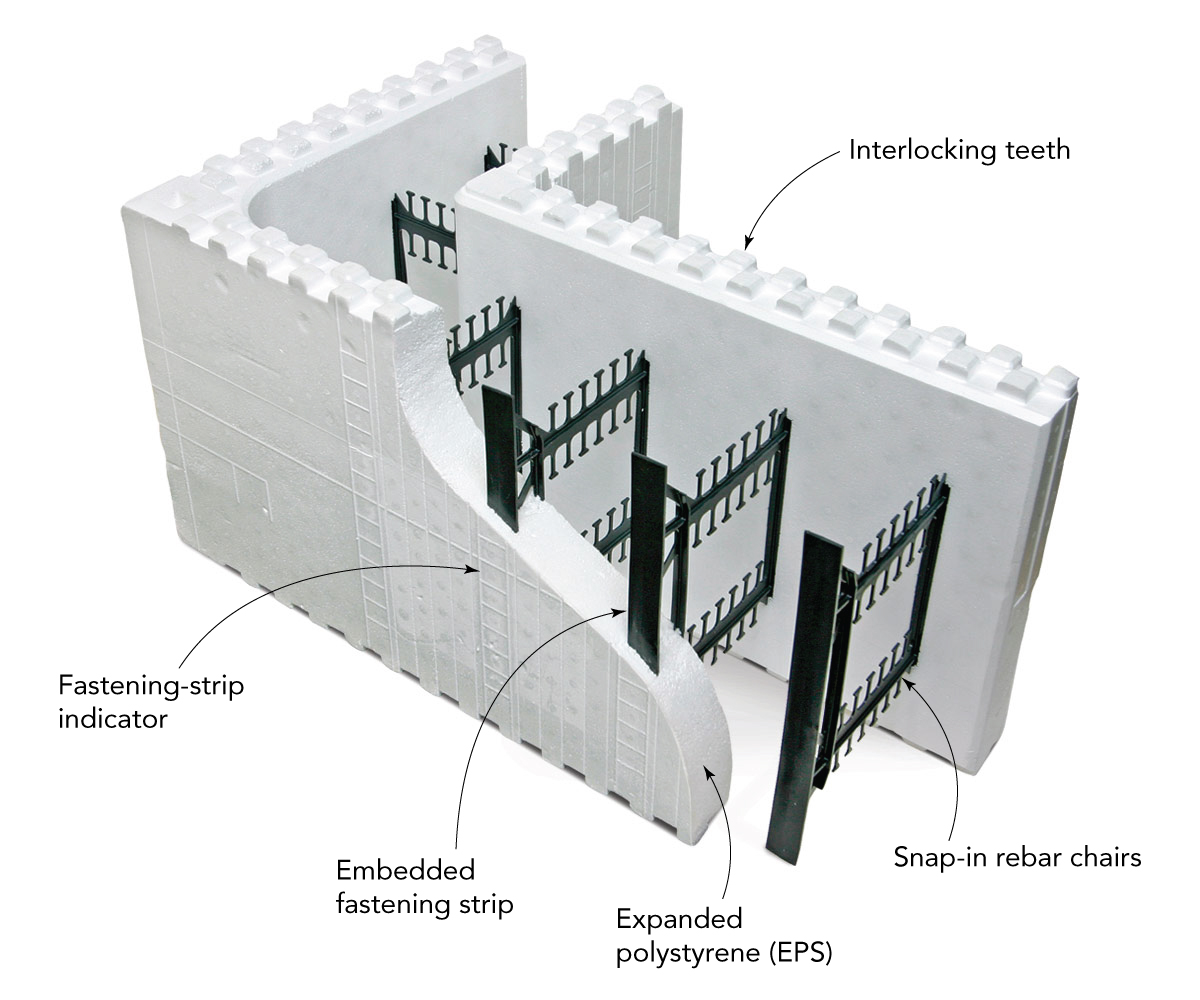
Because ICFs are so easy to install, I can save a lot of money in labor by doing the job myself rather than paying a subcontractor. For instance, this job cost a bit more than $1400: $900 for the blocks, and about $550 for the 7-1/2 yd. of concrete. ICFs are available in several styles, each suited for different types of walls. I prefer the flat-wall type — even though it requires more concrete than other styles — because it emulates the more familiar poured-concrete wall.
My ICF of choice is called iForm (www.rewardwalls.com). The best thing about this ICF system is that because there is no top or bottom, the blocks can be installed in any direction; even corner blocks can be flipped to fit a right or left corner.
To estimate the number of blocks needed for a job, I start by dividing the length of each wall by the length of a single block. When added together, this tells me how many blocks I need in each course. Next, I divide the required height of the wall by the height of one block; this tells me how many courses I will need. When multiplied together, these two numbers give me the total blocks needed. I also like to add one extra block for each side of the foundation in case I run into problems.
Establish a dead-level first course
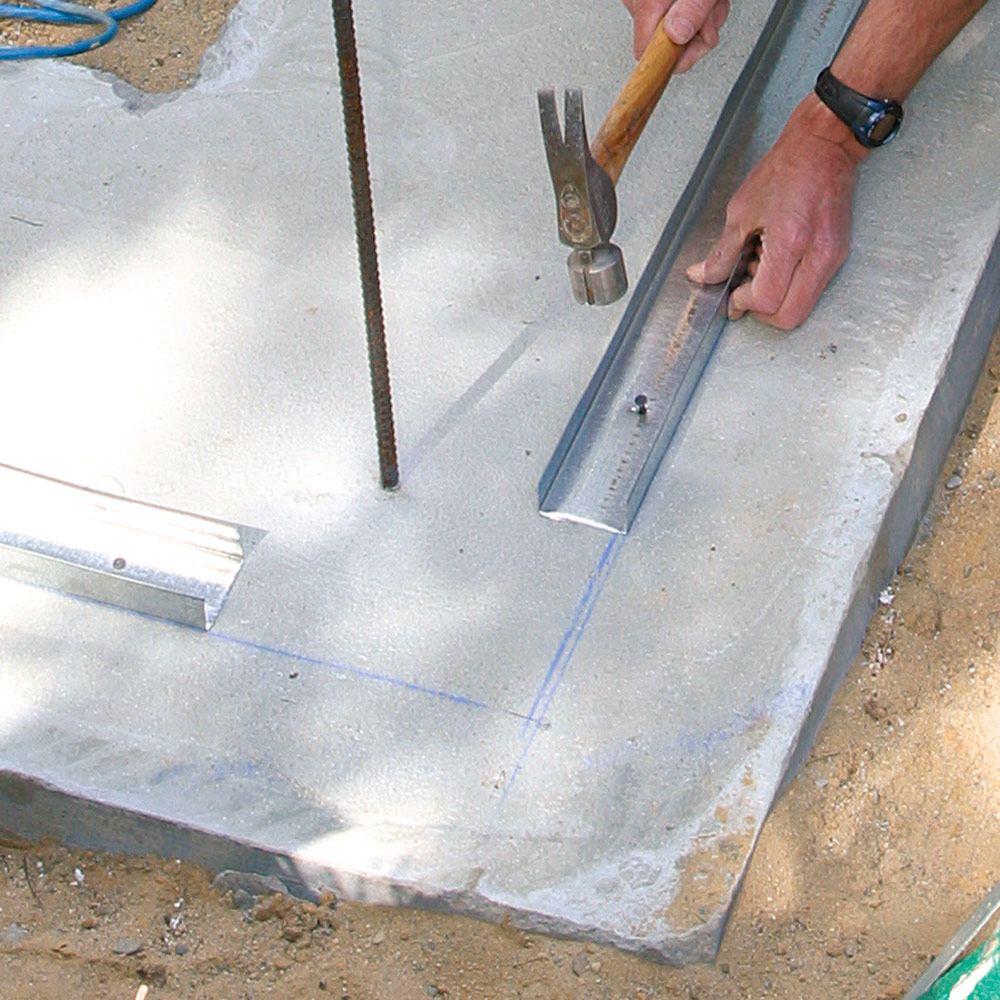
To start, I sweep the standard concrete footing clean and snap chalklines representing the outside perimeter of the foundation (see Forming and Pouring Footings, FHB #119). Next, I cut 2-1/2-in. light-gauge steel-stud track to length and fasten it along the chalklines with masonry nails. The metal track, which normally is sold as top and bottom plates for steel-stud wall systems, just happens to be the right width to hold the iForm blocks firmly in place.
Before I start installing the blocks, I check the footing for level. The key to a quick, accurate installation is a dead-level first course. If the footing is more than 1/4 in. out of level, I have some adjusting to do. This can be done by trimming the bottom of the blocks or by lifting them with shims, and later filling in any gaps with expanding foam.
Because each block is 16 in. tall and the overall foundation height often isn’t a multiple of 16, I usually have to trim one course to get the correct finished height. If this is the case, I prefer to cut the bottom of the first course so that the top course is a full-height block. The blocks can be cut quickly to a uniform height on the tablesaw, using the rip fence as a guide.
Corners come first
Because the corners are the weakest points in the foundation, they are the first blocks to be installed on each course. This ensures that I won’t have to compromise their strength by cutting them to fit the rest of the blocks. After I lay the corners, I fill in with straight blocks.
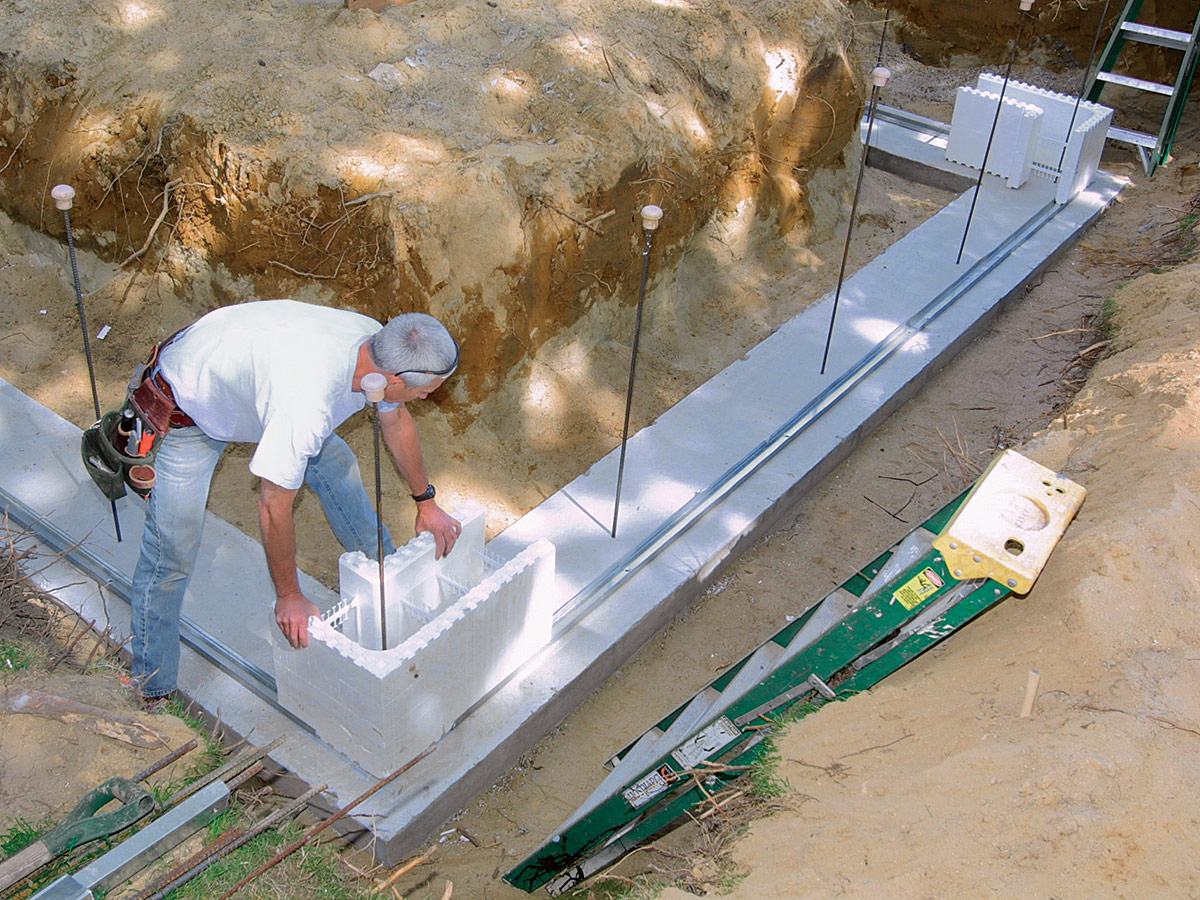
As I work my way out of each corner, I usually have to trim one block on each side of the foundation to get the right fit. The iForm blocks have vertical lines at 1-in. increments on the sides, so I can take my jigsaw and cut by eye, using the nearest inch line as a guide. It’s best to cut a little short rather than a little long; any extra length will push the corners out of square.
Block by block, I work my way toward the existing foundation. Butting the ICFs against a flat surface (poured concrete or concrete block) simply involves cutting the last blocks to the correct length and inserting rebar into the existing wall. But on this job, the existing foundation was fieldstone that had a very irregular surface. Thanks to the easy-working properties of the ICFs, I was able to scribe the blocks to fit against the old foundation. I didn’t need any rebar anchoring the new wall to the old because the rough fieldstone offers a strong bonding surface that poured-concrete and block walls do not.
Reinforce the forms with plastic and steel
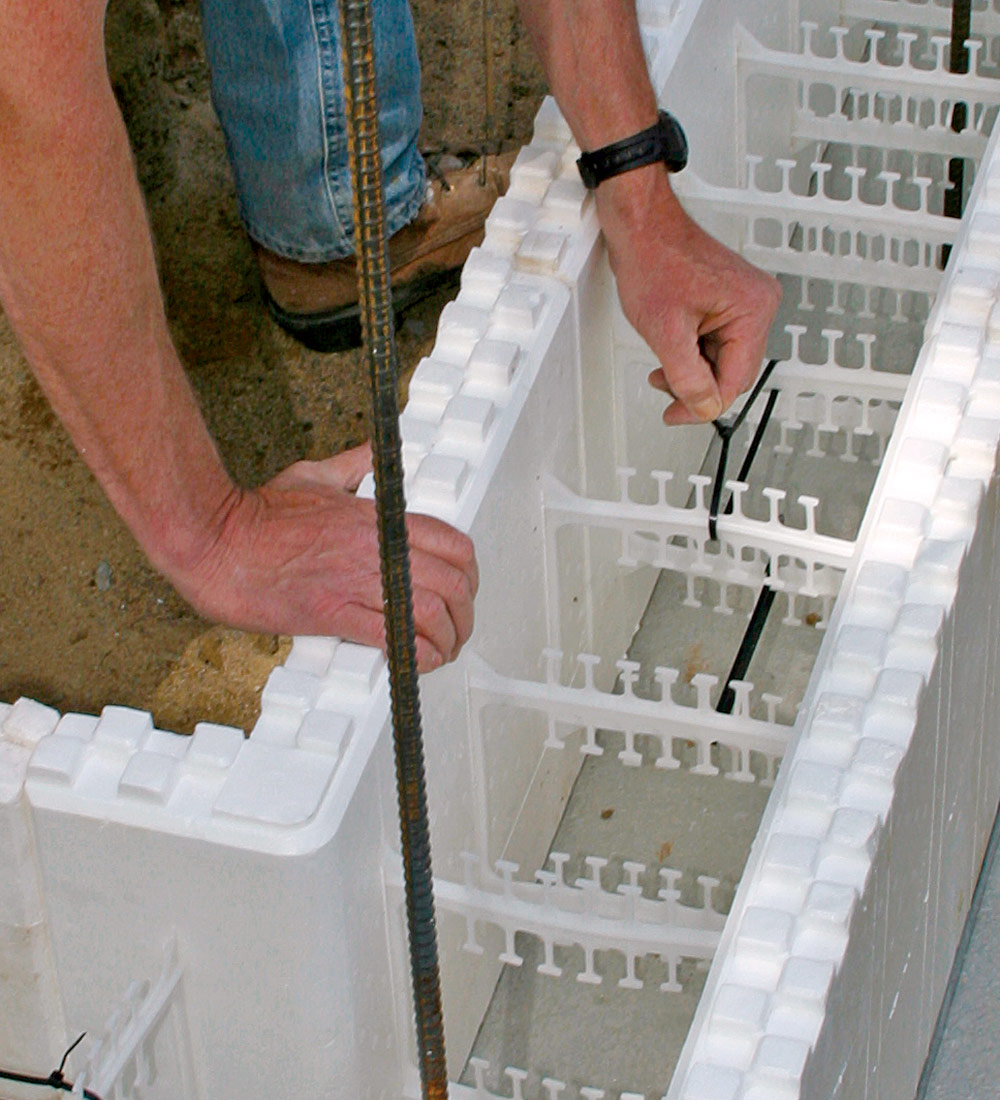
Once the first course is laid, I reinforce the corners by securing the corner blocks to adjacent straight blocks with zip ties. Available at any hardware store, zip ties are thin plastic straps used for bundling cables and wires. I also use zip ties to tie together the two blocks that form the vertical seam. Then I snap in a row of 1/2-in. rebar and overlap it by at least 18 in. in the corners. The rebar chairs of the block I use are formed to allow two pieces of rebar (up to 5/8 in. dia. each) to be snapped together, one on top of the other, eliminating the need for wire ties. That’s a real time-saver.
On the next course, I flip the corner blocks end for end so that the seams will stagger. I build up the corners pyramid style, making sure to attach the corner blocks to adjacent straight blocks with zip ties before stacking the next unit.
After measuring the diagonals of the foundation to make sure it’s still square, I lay the rest of the straight blocks in place, reinforce the vertical seams, and scribe the ends as before. Staggering the cut seams in successive courses is not an option because ICFs with interlocking teeth almost never line up correctly; therefore, one of the two rows of teeth would have to be cut off to get the forms to seat properly.
Handling vents and openings
To create a hole for crawlspace access, I build a permanent frame using pressure-treated lumber. The bottom of the frame is separated into two halves with a gap in the middle so that I can watch for voids underneath during the pour.
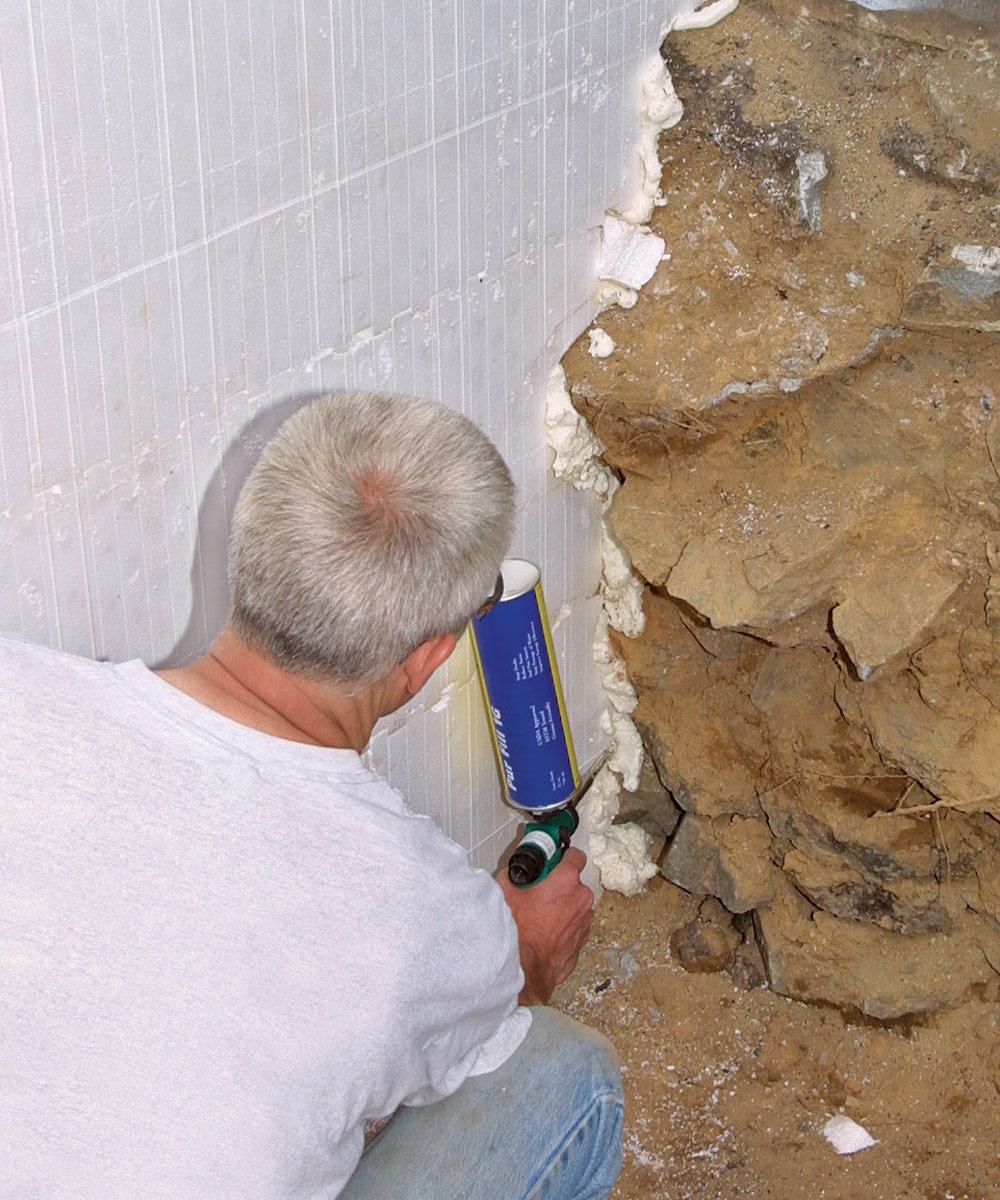
When I use steel vents meant for poured-concrete walls, I run into two problems. The first is that traditional vents are made for 12-in.-wide walls, but the ICF walls I use are 13 in. wide. This means the vent has to be recessed an inch on the inside of the crawlspace. Also, there is no easy way to secure vents during the pour. I’ve managed to solve this problem by placing a heavy rock on top until the pour is finished.
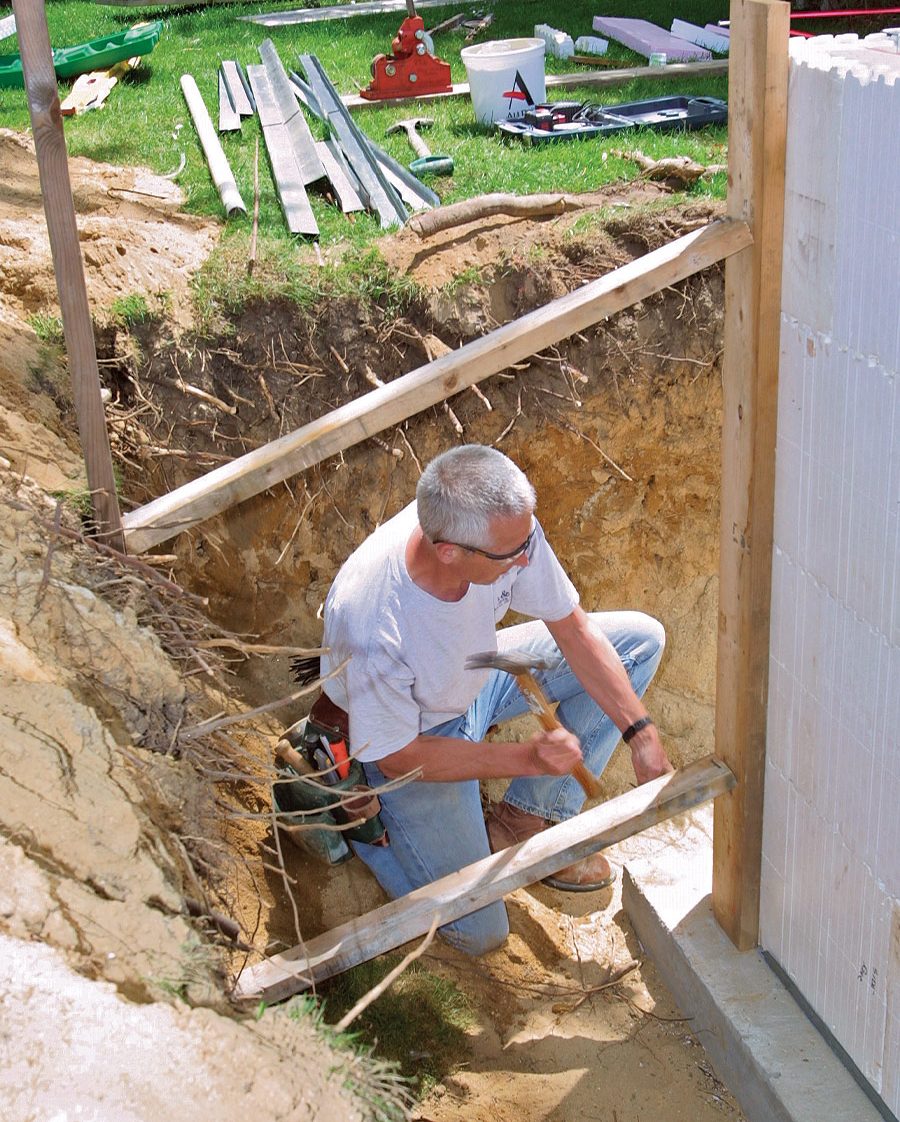
Getting ready for the pour
I straighten the top of the walls with steel track, which keeps the interlocking teeth from clogging with concrete. I also string up a dry line about an inch or two above the outside perimeter of the walls. After snapping in the top row of rebar, I reinforce the vertical cut seams in the blocks by gluing them together with foam and screwing plywood scabs into the embedded fastening strips across both sides.
It doesn’t take much concrete to move an unbraced wall, but it doesn’t take much time to brace it either. As concrete is poured into the wall, it tends to push the blocks away from the existing foundation. To prevent this, I brace the ends of the wall opposite the existing foundation. Because the blocks I use lock together so tightly, bracing the sides of the foundation isn’t necessary. However, if you use another brand of ICFs, check the instructions.
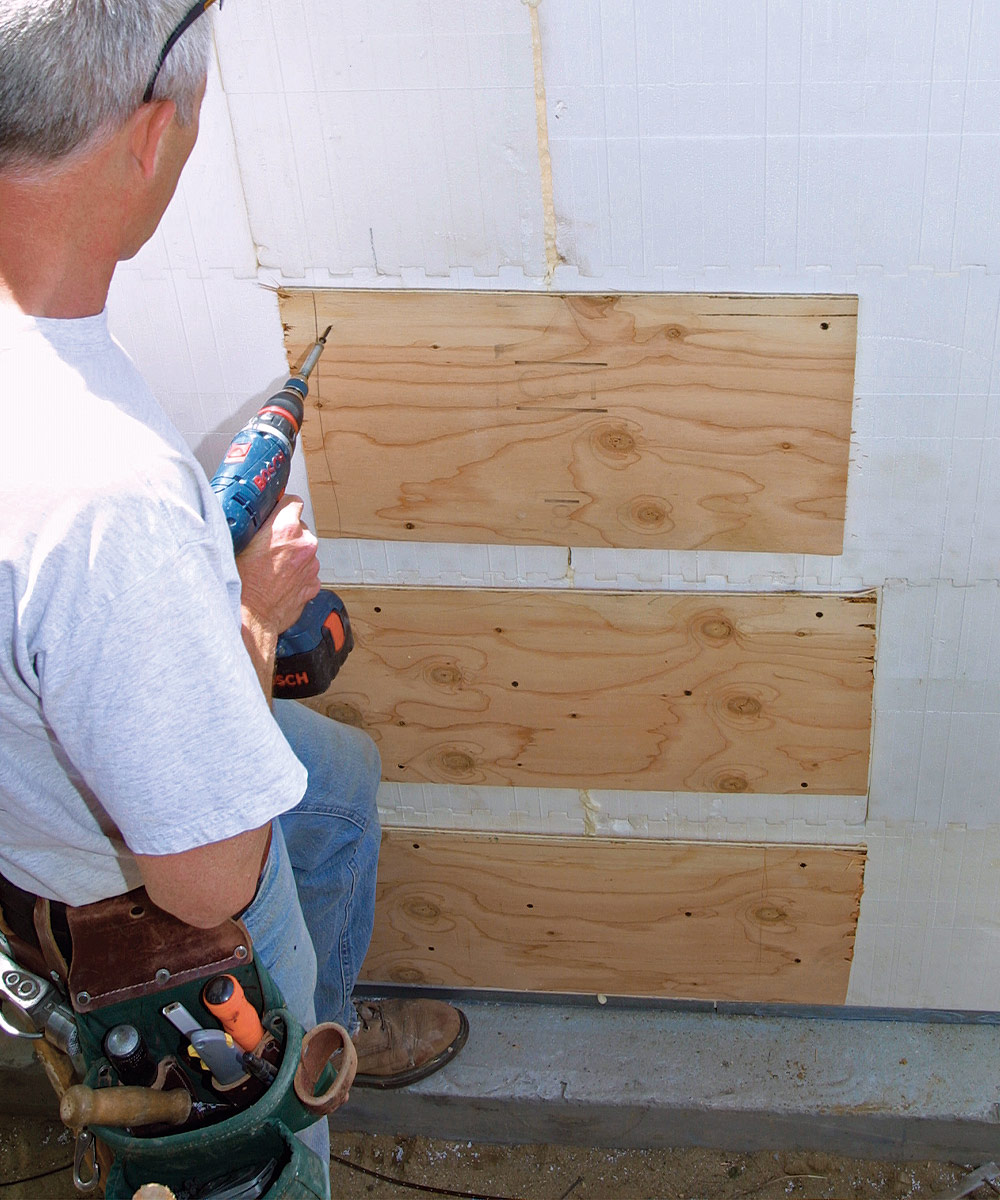
The pour is the trickiest part
Most ICF manufacturers list how many blocks can be filled by 1 cu. yd. of concrete. For instance, 1 cu. yd. of concrete fills 7-1/2 13-in.-wide iForm blocks. So I simply count the number of blocks in the foundation, divide it by 7-1/2, then round up to the nearest 1/2 yd.
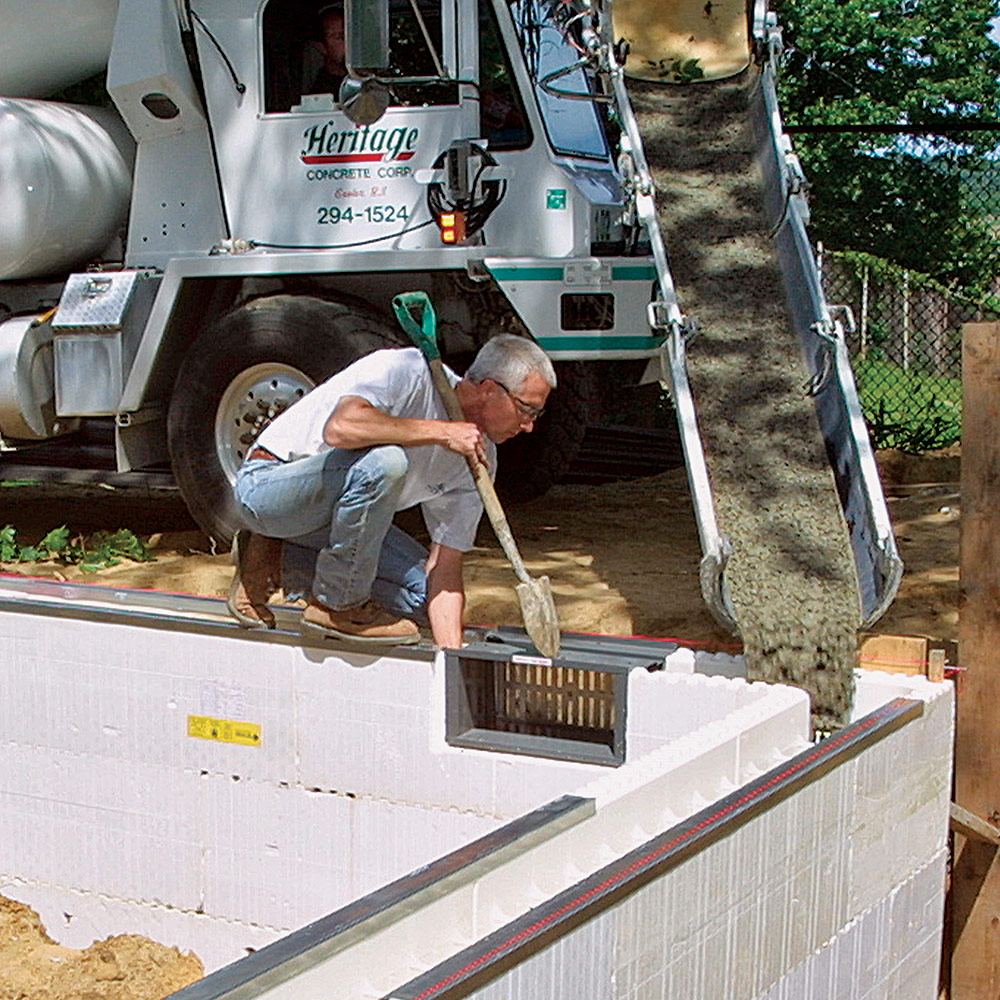
The design and engineering of ICF blocks are based on a 3000-psi concrete strength, but double-check your local code and the ICF manufacturer’s specs to make sure you pour the right type of concrete in the foundation. I usually order 3000-psi concrete with 1/4-in. to 3/8-in. peastone aggregate. I’ve found that concrete with aggregate larger than 3/8 in. is difficult to pour and consolidate in the ICFs.
Pouring the concrete is the trickiest part of the process. Because the concrete needs to flow between the webbing of each ICF block, the consistency of the concrete is important. The lower the slump, the less water is mixed with the concrete, and the stiffer it will be. But a higher slump of 6 or 7 may result in substandard strength.
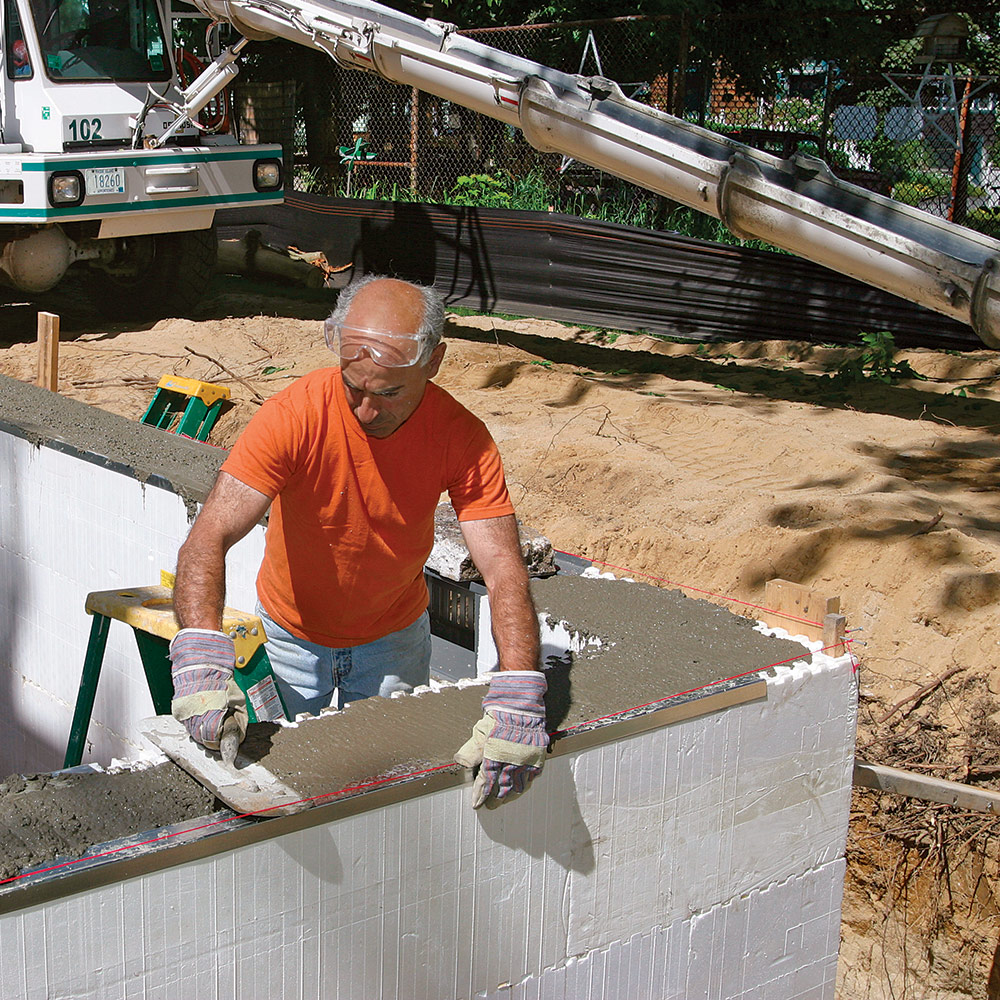
As with all three-wall foundations, I first anchor the corner blocks by filling them about halfway with concrete. Keeping the concrete at a 4 slump, I continue pouring the rest of the walls to the halfway mark. Then I have the truck driver loosen the concrete to about a 5 slump, start back at the corners again, and continue with the top half of the pour.
During the pour I constantly watch for voids forming, walls bowing, or gaps and seams opening up between the forms. I just use a stick to poke the concrete beneath the vents because I don’t like to use a vibrator unless absolutely necessary. If gaps or seams open up, I stop the pour and reinforce the area with plywood scabs. Then I give the concrete a little time to set up, usually by continuing the pour in another area.
Once the wall has been topped off, I float it level with a trowel, using the steel track as a guide. Then I install the anchor bolts. One last adjustment can be made simply by pushing or leaning on the wall to tweak it straight—and my foundation is formed, insulated, and poured in record time.
Building with ICFsPros
Cons
|
Rick Arnold is a builder in Wickford, R.I., and the author of Working With Concrete (The Taunton Press, 2003). Photos by Roe A. Osborn, except where noted.
Sources:
Founded in 1995, the Insulating Concrete Form Association (ICFA) is a growing group of professionals ranging from manufacturers to ready-mix suppliers, all focused on educating builders about the benefits of ICFs.
Fine Homebuilding Recommended Products
Fine Homebuilding receives a commission for items purchased through links on this site, including Amazon Associates and other affiliate advertising programs.
Plate Level
Smart String Line
100-ft. Tape Measure