Careful Layout for Perfect Walls
Everything from rafters to kitchen cabinets fits better when you get the walls square and the studs in the right places.
Synopsis: Here you’ll learn how to check the floor frame for square corners, which is the first step in framing walls. Then the author, a general contractor, walks you through the layout process, explaining the framer’s shorthand and offering tips for faster and more accurate framing.
Framing walls is one of the most fun parts of building a house. It’s fast, safe and easy, and at the end of the day, it’s satisfying to admire the progress you’ve made. Before cranking up your compressor and nail guns, though, you need to think through what you’re going to do. You need to locate every wall precisely on the subfloor, along with every framing member in those walls.
Layout starts in the office
For one of our typical houses, layout and framing for interior and exterior walls start in the office a few days before my crew and I are ready to pick up the first 2×6. First, I review the plans carefully and make sure that all the necessary information is there.
I need the locations and dimensions of all the rough openings, not only for doors and windows but also for things such as fireplaces, medicine cabinets, built-ins, dumbwaiters and the like. I also make sure the plans have the structural information I need for layout, such as shear-wall and bearing-wall details and column sizes.
At the site, one of Spier’s many corollaries to Murphy’s Law is that errors never cancel each other out; they always multiply. If the floor is anything but straight, level, flat and square, the walls are going to go downhill (or uphill) from there. So before you get to layout, do whatever it takes to get a good floor, especially the first: Mud the sills, shim the rims, rip the joists. Sweep off the subflooring, and avoid the temptation to have a pile of material delivered onto it.
Snap chalklines for the longest exterior walls first
I’ve learned over the years that it’s best to snap the plate lines for the entire floor plan before building any of it. Problems you didn’t catch on the prints often jump out when you start snapping lines.
When framing floors, I take great care to set the mudsills flush, square and in their exact locations. Because the edges of floor framing and subflooring are not always perfect, though, I use a level to plumb up from the mudsills and establish the plate lines, measuring in the stock thickness from the level. I generally start with the longest exterior walls and the largest rectangle in the plan. When I have the ends of the longest wall located, I snap a line through the marks.
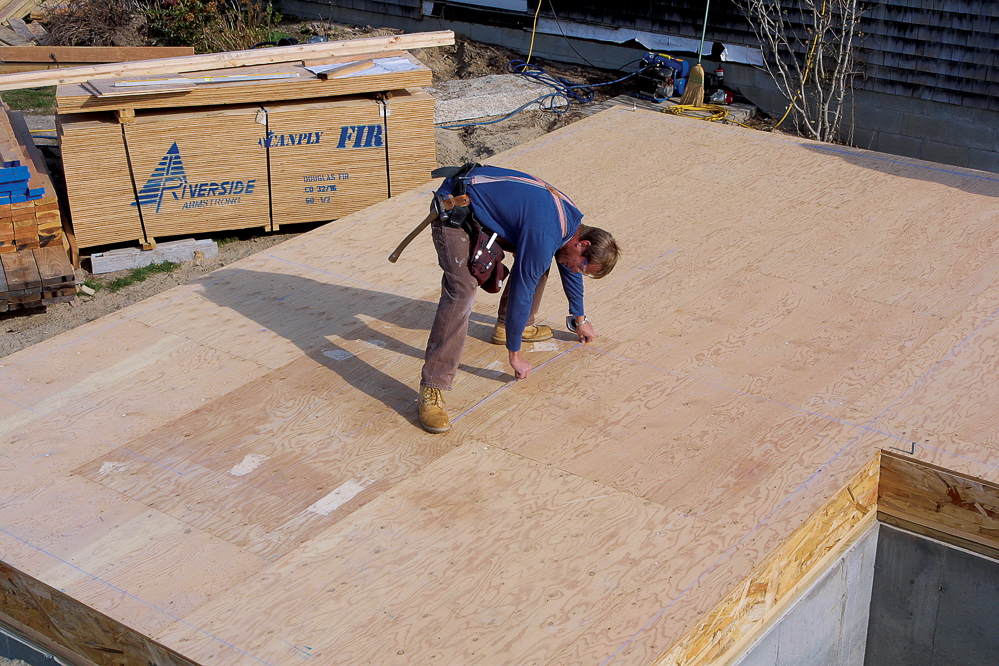
Once I’ve established the line for the first wall, I move to the parallel wall on the opposite side of the house. I measure across the floor from the first line to the opposite mudsill (again using a level to plumb up from the mudsill to the floor height) at both ends; if the lengths differ slightly, I use the larger measurement. I snap through these points, which gives me two parallel lines representing the long sides of the largest rectangle. It’s okay if the plates overhang the floor framing by a bit, but I watch for areas that might need to be shimmed or padded for instance, where a deck ledger needs to be attached to the house.
Establish the right angles
I locate three corners by measuring in from the mudsills. The fourth corner I locate by duplicating the measurement between the first and second because I need sides of equal lengths to create a rectangle. I check this rectangle for square by measuring both its diagonals. If I’ve done everything right so far, the diagonal measurements should be very close, perhaps within 1⁄4 in. I shift two corners slightly if I need to, making sure to keep the lengths of the sides exact until the diagonals are equal. Now, perpendicular lines are snapped through the corners, completing the rectangle.
Because I started arbitrarily with one long wall, I may find now that the rectangle, while being perfectly square, is slightly askew from the foundation and floor. Also, some of the complicated foundations that I work on can have wings or jogs that are slightly off. If I can make everything fit better by rotating the rectangle slightly, I take the time to do it now.
Smaller rectangles complete the wall layout
With the largest part of the plan established, I lay out and snap whatever bays, wings and jogs remain for the exterior walls. I use a series of overlapping and adjacent rectangles, which I can square by keeping them parallel to the lines of the original rectangle. I again check the right angles by measuring the diagonals.
Often, the plan calls for an angled component such as a bay. If these components are at 45°, I lay them out from right angles by forming and diagonally bisecting a square. For angles that are not 45°, I either can trust the architect’s measurements on the plans, or I can use geometry and a calculator. The latter method is more likely to be accurate.
When all the exterior walls have been laid out, I turn my attention to the interior walls. Again, I start with the longest walls and work to the smallest, snapping lines parallel and square to the established lines of the exterior walls. I snap only one side of each plate, but I mark the floor with an X here and there to avoid confusion about where the walls will land. I also write notes on the floor to indicate doors, rooms, fixtures, bearing walls and other critical information.
It’s a rare architect who dimensions a plan to the fraction of an inch with no discrepancies, and an even rarer builder who achieves that accuracy. So first, I lay out critical areas such as hallways, stairwells, chimneys and tub or shower units, and then I fudge the rest if I need to.
One last critical issue when reviewing the plans and laying out walls is watching for elements of the design that need to stay symmetrical. If the foundation contractor made one wing a bit wider than another, you don’t want to build all three floors before realizing that the ridgelines of the two wings needed to match up. Make sure symmetrical elements are aligned at the first layout stage.
Make plates from the straightest lumber
While I snap the walls, the crew is busy cutting and preparing material from the piles of stock. I have them set aside a pile of the straightest lumber. With the chalklines all snapped and with this material in hand, I start cutting and laying out the plates (top and bottom members) for the exterior walls. In this step of layout, we set the plates side by side on the layout line, and every wall-framing member is located and labeled. With this information, we assemble the walls on the floor, then raise them into place. I often call out measurements and have someone cut and hand up the material to keep mud, snow and sawdust off the floor during this crucial phase.
As a rule, we plate the longest exterior walls to the corners of the house, and the shorter walls inside them. This approach sometimes needs to be modified—for instance, to accommodate structural columns, hold-down bolts or openings adjacent to corners. Sometimes an obstruction or a previously raised wall dictates which wall can be built and raised first. The goal here is to build and raise as many walls as possible in their exact positions, especially the heavier ones. Moving walls after they’re raised is extra work and no fun.
Before starting any framing, I established a common-stud layout for the entire structure based on two long perpendicular walls from which layout for the rest of the house framing can be measured. This common layout keeps joists, studs, cripples and rafters throughout the house vertically aligned from the foundation to the ridge, which makes for a strong, straight and easily finished structure. We use this common layout to locate butt joints between pairs of plates because code and common sense dictate that these joints land on a stud or a header.
As my crew and I measure and cut the pairs of wall plates, we lay them on edge along their layout lines, sometimes tacking them together with just a few 8d nails to keep the plates held together and in place.
Window, door and stud layout at last
When all the exterior plates are in place, it’s finally time to lay out the actual framing members. I always start with the rough openings for windows and doors. Most plans specify these openings as being a measured distance from the building corner to the center of the opening, which works fine. You can allow for the sheathing thickness or not, but once you choose, be consistent, especially if openings such as windows have to align vertically from floor to floor. Obviously, if an opening such as a bay window or a front door is to be centered on a wall, center it using the actual dimensions of the building, which may differ slightly from the plan.
Rough openings are a subject worthy of their own article, but in a nutshell, I measure half the width of the opening in both directions from the center mark. I then use a triangular square to mark the locations of the edges of trimmers and king studs, still working from the inside of the opening out. Various other marks, such as Xs or Ts, identify the specific members and their positions.
Next, I mark where any interior-wall partitions intersect the exterior wall. At this point, I just mark and label the locations; I decide how to frame for them later. I also locate and mark any columns, posts or nailers that need to go in the wall. I lay out any studs that have to go in specific locations for shelf cleats, brackets, medicine cabinets, shower valves, cabinetry, ductwork and anything else I can think of. Doing this layout now is much easier than adding or moving studs later.
Finally, I lay out the common studs on the plates. Studs are commonly spaced either 16 in. or 24 in. o. c. to accommodate standard building products. By doing the common-stud layout last, I often can save lumber by using a common stud as part of a partition nailer. I almost never skip a stud because it’s close to another framing member, which, I’ve learned the hard way, almost always causes more work than it saves. I occasionally shift stud or nailer locations to eliminate small gaps and unnecessary pieces. I keep the plywood layout in mind here, though, so that I can use full sheets of sheathing as much as possible.
Inside walls go more quickly
Once the exterior walls are built and standing, I cut the interior-wall plates and set them in place. Where two walls meet, I decide which one will run long to form the corner so that the walls can be built and raised without being moved. Also, facing a corner in a particular direction often provides better backing for interior finishes, such as handrails or cabinetry, and sometimes is necessary to accommodate such things as doorways or multiple-gang switches.
When the plates are cut and set in place, I do the stud layout. Just as with the exterior walls, I do the openings first, then nailers and specific stud and column locations. Next, I mark the locations of intersecting walls and finally overlay the common-stud layout on the plates.
Where walls come together
Where one wall meets the middle of another, I use a partition post if the situation dictates it, but more often, I opt for an L-nailer. To make an L-nailer, I use a wider stud on the flat next to a common stud whenever possible. It’s faster and easier; it accommodates more insulation; and it saves the subs from drilling through those extra studs and nails.
If I use U-shaped partition posts (a stud or blocks on the flat flanked by two other studs) in an exterior wall, I need to make sure to fill the void created by the partition post with insulation before the sheathing goes on.
With the interior plates all there, we can nail in the studs, raising walls as we go. I mark key areas where studs should be crowned or specially selected, such as areas with long runs of cabinetry, and also studs that might need to be left out to allow installation of things too wide to be carried though the doors. I also nail double top plates to as many walls as possible if they don’t interfere with the lifting process.
Setting the stage for the rest of the house
For the most precise wall layout, plot a series of rectangles that includes every wall. The larger the rectangle, the more accurate the wall position. Begin with the longest walls, and lay out the largest rectangle using diagonal measurements. Working off established lines and square corners, work down to the smallest rectangle.
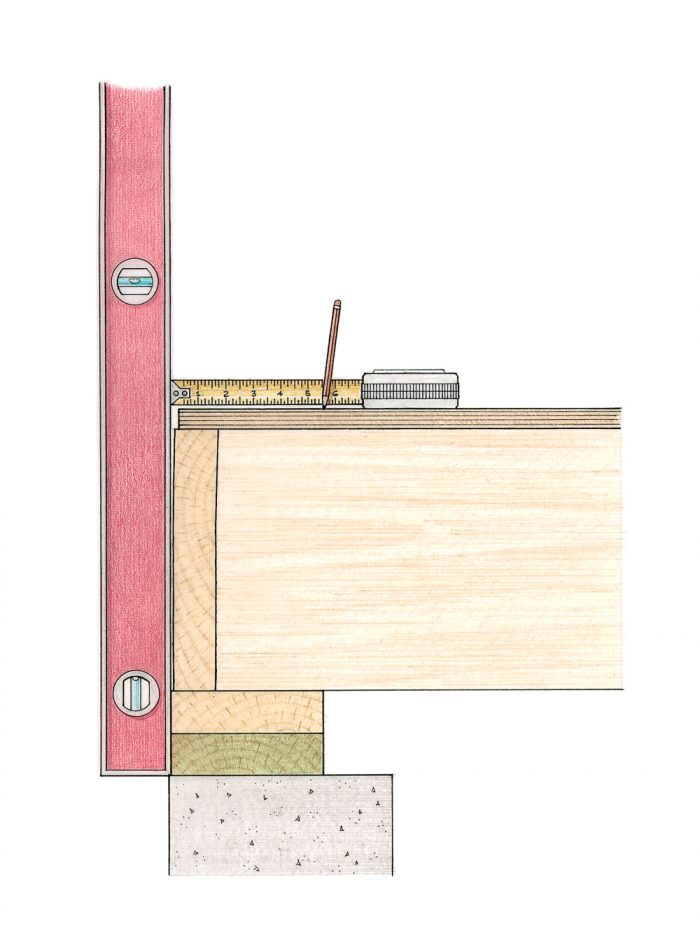
1. Starting with the longest walls, measure and square the largest rectangle.
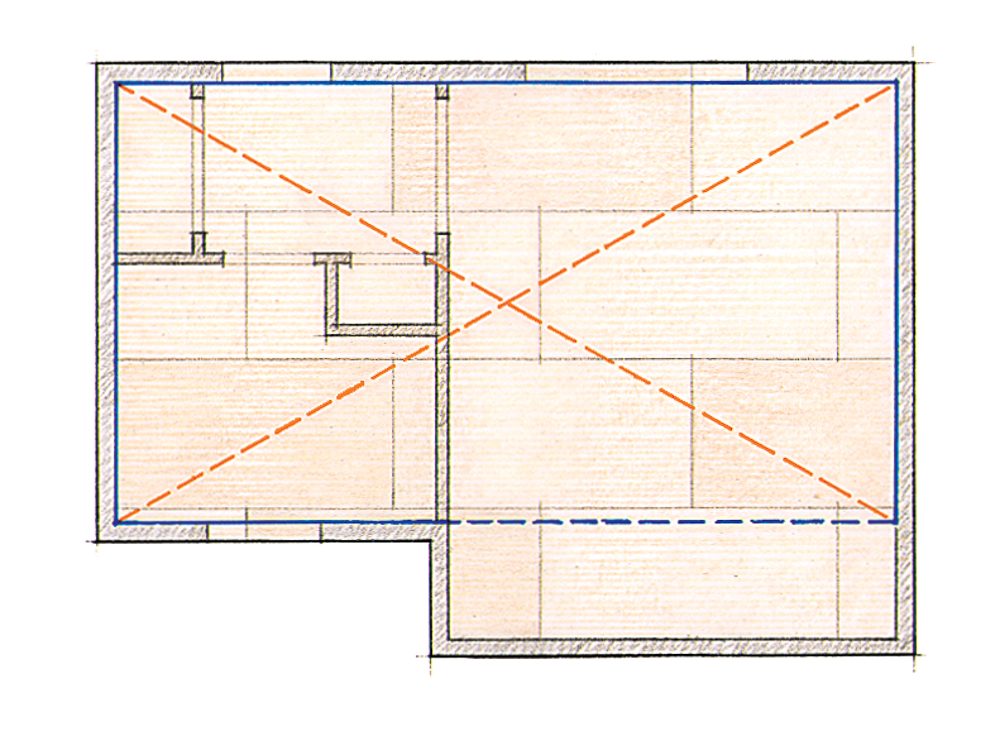
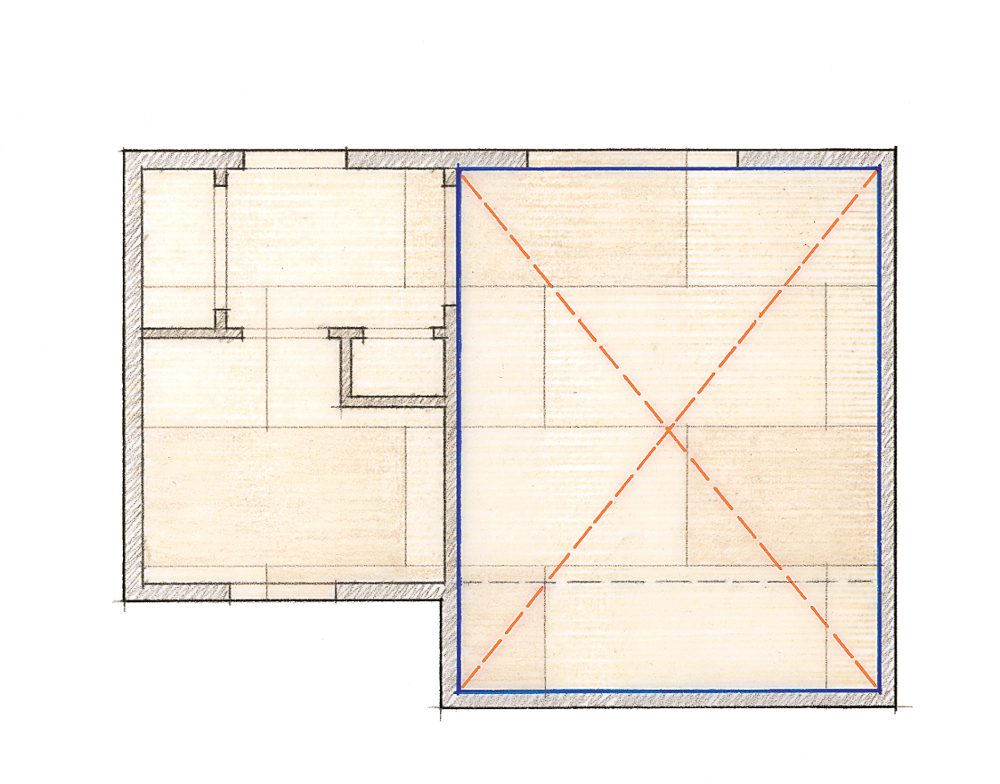
3. Now measure off the outside and form a rectangle for the longest interior wall.

4. Last, form rectangles for the remaining interior walls.
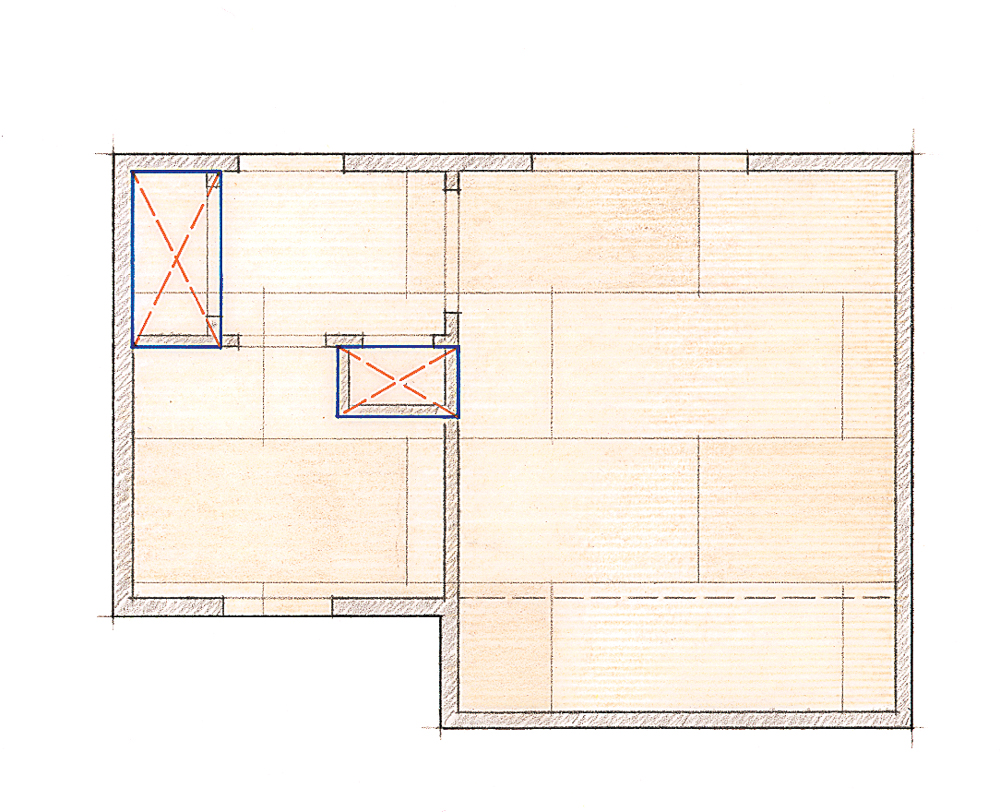
Align framing from mudsills to roof for the strongest house
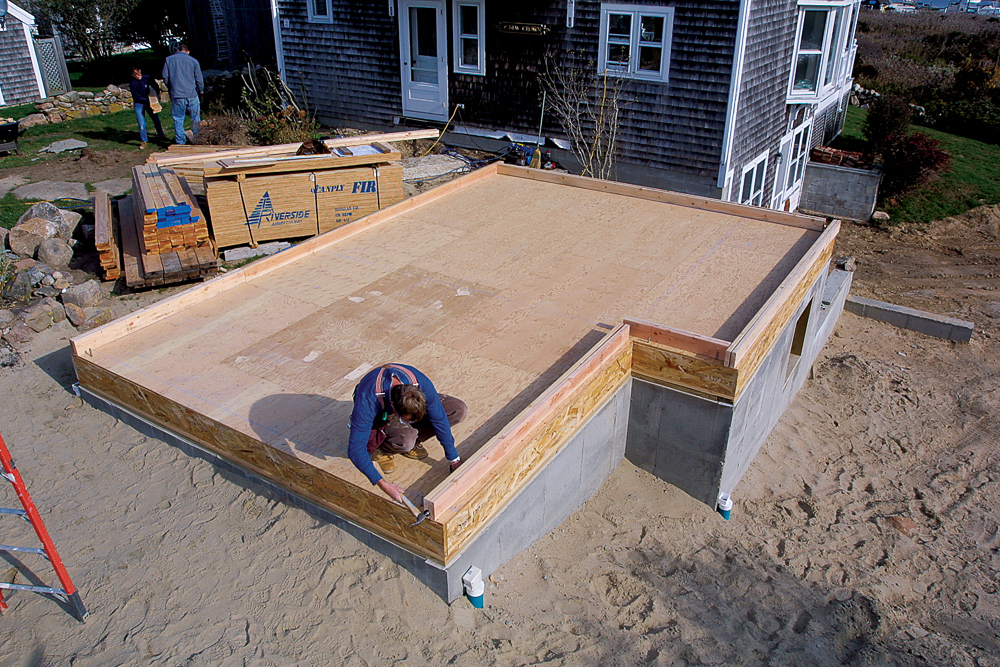
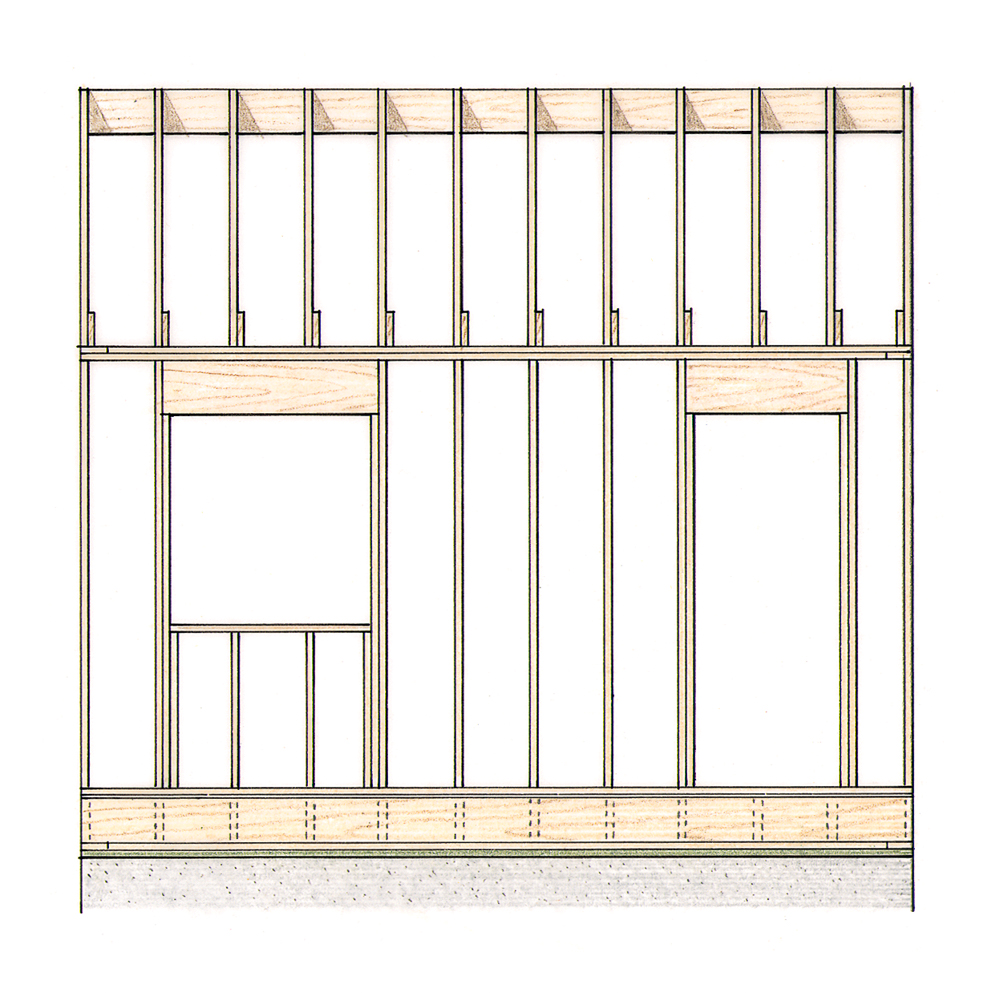
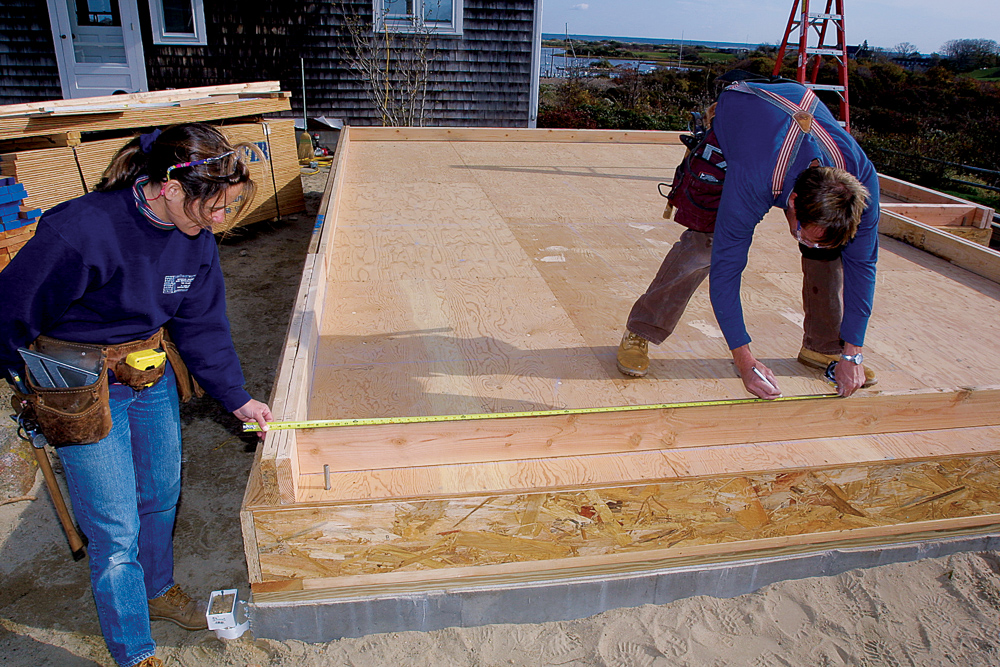
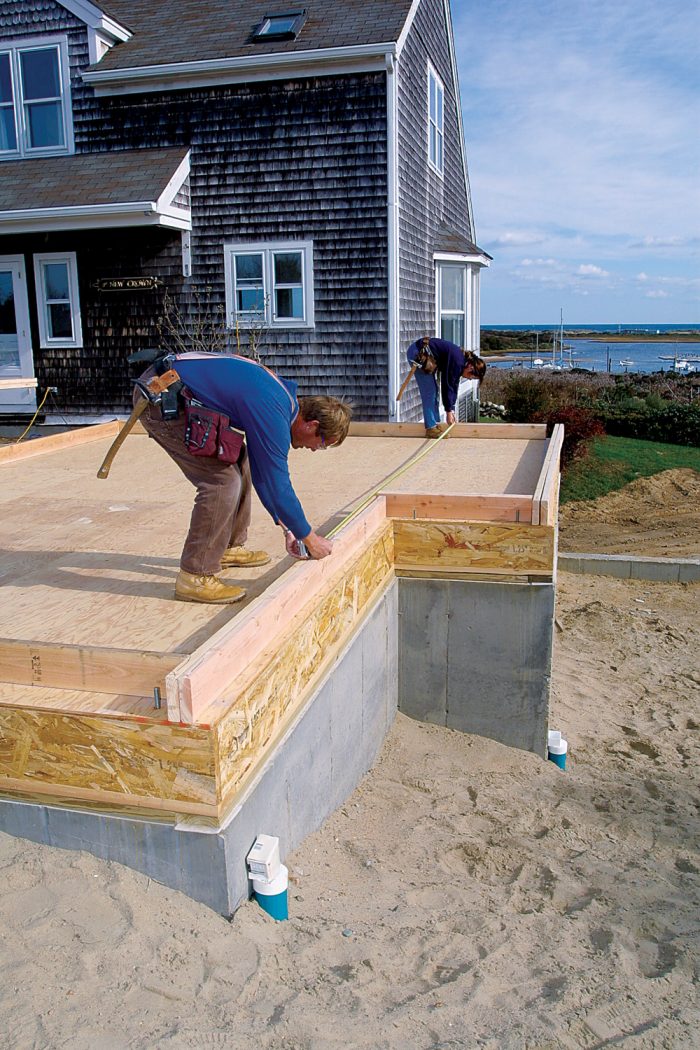
Two quick layout tips
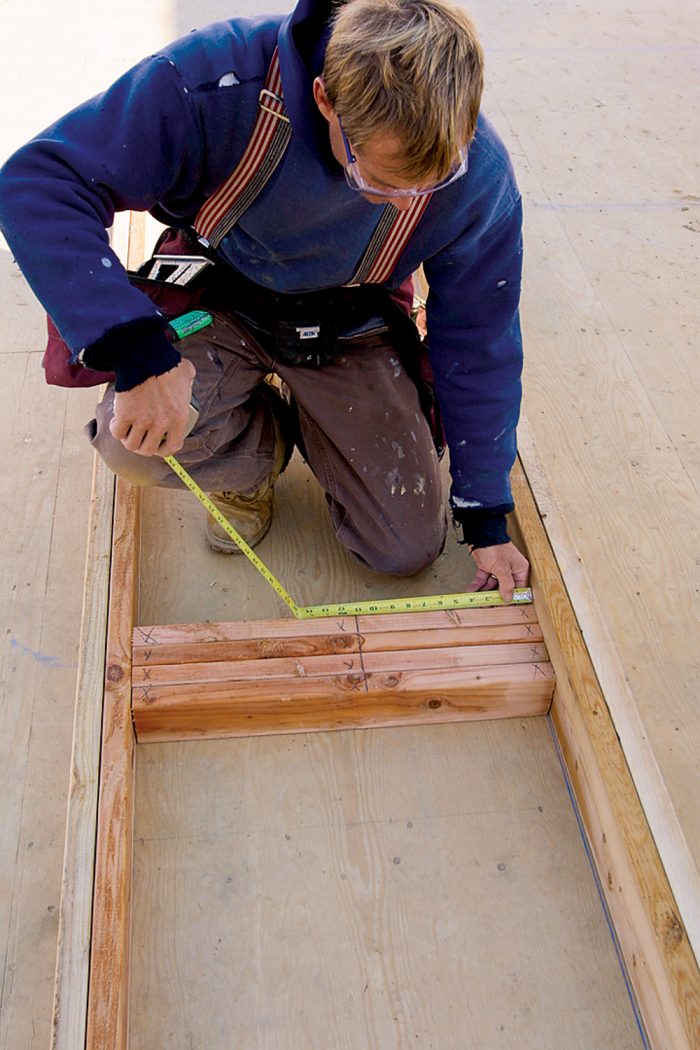
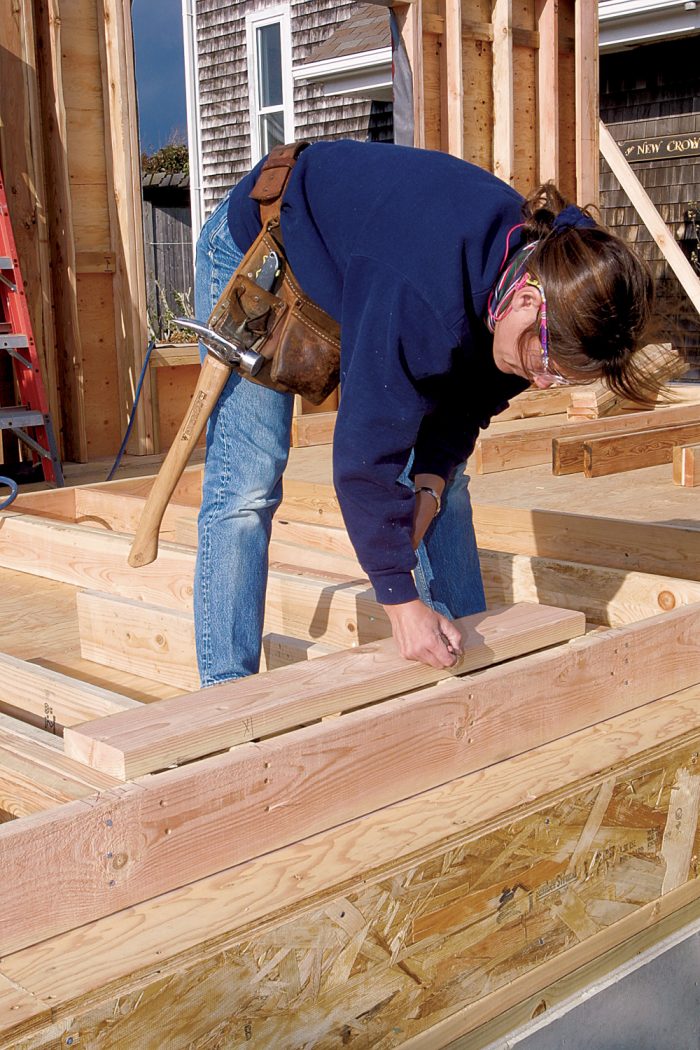
Photos by Roe A. Osborn. Drawings by Vince Babak.
Related stories:
To read the entire article, click the View PDF button below.
From Fine Homebuilding #156
Fine Homebuilding Recommended Products
Fine Homebuilding receives a commission for items purchased through links on this site, including Amazon Associates and other affiliate advertising programs.
Protective Eyewear
100-ft. Tape Measure
Magoog Tall Stair Gauges