Open Up a Ceiling With a Steel Sandwich
Bolted between rafters, an angled steel flitch plate can eliminate the need for rafter ties in cathedral ceilings.
Synopsis: Everyone loves a cathedral ceiling, but when you remove the framing that makes most ceilings flat, you remove the lumber that keeps the walls from spreading apart. There are a few conventional solutions: a structural ridge beam, exposed collar ties, and scissors trusses. An unconventional option is to use a welded steel flitch plate sandwiched between two common rafters. This method gives more headroom than scissors trusses and is far cheaper.
My company specializes in designing and building small homes. I like to vault ceilings in small rooms — bedrooms and screened porches, commonly — that normally would have flat ceilings.
People love cathedral ceilings because they add drama and presence to interior spaces. A vaulted ceiling can make a small room look large rather than cramped and confined. So why are cathedral ceilings usually reserved for living rooms or other large public areas while small rooms get stuck with flat ceilings? Cost.
Scissors trusses or structural ridge beams are the common, expensive methods for incorporating cathedral ceilings in houses. For the past few years, though, my company has overcome this economic problem by using angled steel flitch plates supplied by a steel fabricator. The V-shaped plate is angled to match the roof peak, and it’s sandwiched between common rafters. Angled steel flitch plates work well for pyramid roofs but can be used to open gable roofs, too.
Scissors trusses don’t cut it
For years, I’ve been building vaulted ceilings using scissors-truss kits from my local truss supplier, but scissors trusses have a number of drawbacks: less space for insulation at the top plate, scheduling headaches, and cost. Did I mention that they’re also a pain in the neck to install? Getting the little trusses to line up for a smooth roof and ceiling is fussy at best; my crew and I often have to strap the ceilings with 1x4s to get them smooth enough for drywall. The truss package for the last pyramid hip ceiling I built, for a 16-ft. by 16-ft. bedroom, cost $1,600. The three-week lead time added insult to injury. There had to be a better way.
My engineer came up with an angled flitch-plate detail that creates a V-shaped beam capable of supporting 2×12 framing and that adds only $180 to the framing costs. It’s like a 160-lb. Simpson Strong Tie. The welding must be done by an American Welding Society certified welder using a full-penetration weld; you can’t just do it on site. The first time I brought one of these angled-flitch drawings to my welder, he wanted a plywood template. Now I can fax him a diagram, and he has the flitch plate ready for me to pick up in a week, complete with clean holes.
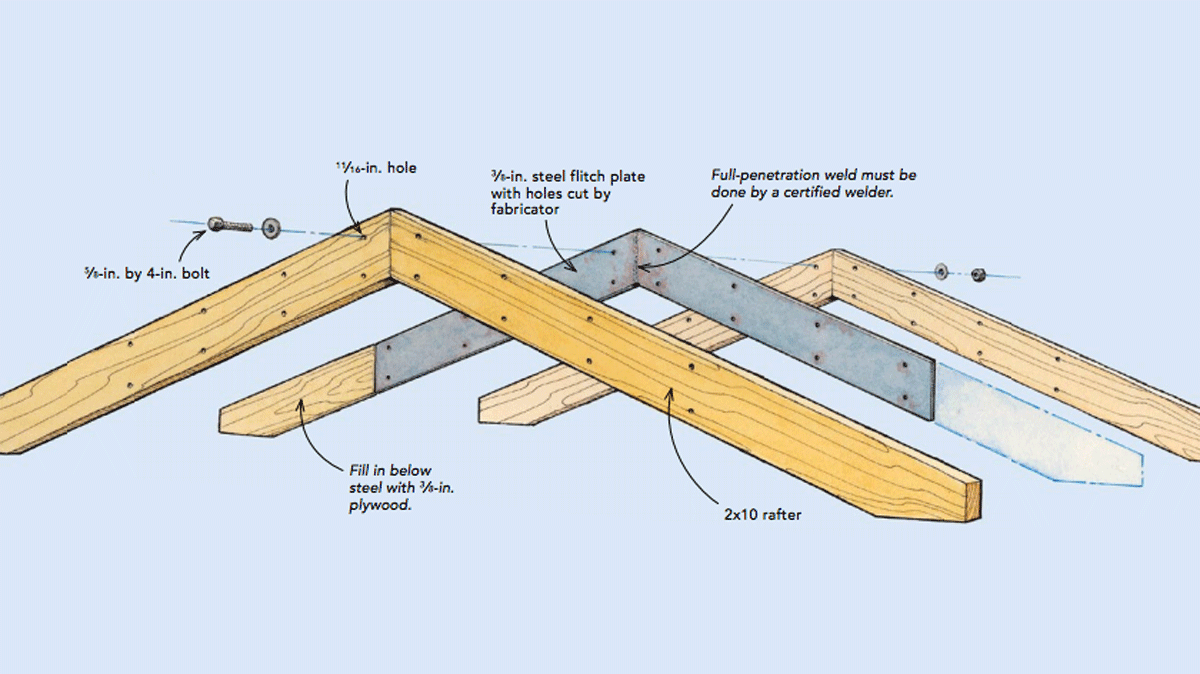
This flitch solves all the problems of scissors trusses: It has a full 10 in. for insulation over the top plate, it keeps the ceiling the same pitch as the roof, and it ensures that the roof and ceiling planes are smooth every time. Yes, the steel is heavy, and getting all those holes to line up takes some planning. But the assembled flitch beam is much less awkward to handle than scissors trusses, and it costs about $1,000 less for that 16-ft. by 16-ft. room.
The holes are bigger than the bolts
The holes in the steel should be cut by the fabricator, preferably with a high-pressure hydraulic “piranha” punch. Do not blast holes in the steel with a cutting torch because the holes will be ragged and will catch at the drill bit while you’re using the steel as a template to drill holes into the wood.
From Fine Homebuilding #178
Fine Homebuilding Recommended Products
Fine Homebuilding receives a commission for items purchased through links on this site, including Amazon Associates and other affiliate advertising programs.
Shingle Ripper
Protective Eyewear
Hook Blade Roofing Knife