What to Consider When Choosing Insulation
With the material's implications for the building envelope, the environment, and installer and homeowner health, R-value is just the beginning
Synopsis: Former FHB editor Brian Pontolilo suggests an approach to choosing insulation based on several criteria: R-value, air permeability, vapor permeability, moisture tolerance, ease of installation, global-warming potential, cost, and toxicity. Using these criteria, he profiles 12 different types of insulation.
Choosing the most appropriate type of insulation should be part of an overall strategy of materials selection. The underlying purpose of green building is not to develop marketing brochures that will help sell “green” houses in suburban subdivisions, but to make decisions that genuinely benefit people and the planet. This makes a strong case for finding ways to use insulation and other materials with low carbon emissions.
When I was asked to help teach a class on how to choose insulation, I knew that it would have to include examples of different ways to insulate slabs, basements, and crawlspaces; walls, ceilings, and roofs; and tricky areas like rim joists and kneewalls. I also hoped I could offer a systematic approach to evaluating products so that the folks who participated in the class could learn to determine for themselves if a particular material was right for their specific project. To do this, I started to develop a list of criteria to consider when choosing insulation. When I thought I was done, I ran it by a few colleagues and asked a few designers and builders some specific questions about how they settle on insulation in their work. I ended up with seven or so points that need to be considered when choosing insulation. Then I started to rethink my approach altogether, but we’ll get to that a little bit later. First, here’s the list of factors I came up with.
Mineral wool![]() “Mineral wool” refers to both rock wool, which is spun from molten filaments of basalt or another type of rock, and slag wool, made from blast-furnace slag. Mineral wool contains an average of 70% post-industrial recycled content and needs no chemical flame retardants. It is available in unfaced batts, in semi-rigid panels, and for use in blow-in applications in walls and attics. Brand names include Rockwool and Thermafiber. In panel form, mineral wool can be used below grade and as a continuous layer of insulation on exterior walls to reduce thermal bridging. Mineral wool is air and vapor permeable and provides high fire resistance. Availability may be limited in some areas. R-value: R-2.9 to R-4.3 per in. |
What is Net Carbon Emissions?
Net carbon emissions is a way to account for the climate effects of a material and is an indicator of global-warming potential. Here it is measured in kgCO2e/m2, which quantifies the carbon released as a result of producing and installing this material as a carbon dioxide–emissions equivalent. Materials with negative values store more carbon than they take to produce and install. The numbers that appear in this article are reported by Builders for Climate Action for a layer of insulation with an insulating value of R-10.

R-value
How well insulation slows heat transfer is quantified as R-value. The higher the number the better when it comes to R-value. When you see an R-value listed, it’s important to know if it is the total R-value for a product or an R-value for the material, which is usually given as R-value per inch. For example, you can buy an R-13 fiberglass batt designed to be installed in a 2×4 wall, and R-13 is the total insulating value for each batt. If you are blowing loose-fill fiberglass insulation into an attic, however, the product is likely sold at around R-3 per inch. The total R-value will depend on how deep you blow the insulation, as well as its density.
Because standardized R-value testing measures all three types of heat transfer—conduction, radiation, and convection—R-value is R-value. In other words, whether it is fiberglass insulation or spray foam doesn’t matter when it comes to R-value. The marketing material provided by some insulation manufacturers may try to make you think otherwise. Don’t be fooled. One product may do a better job of air-sealing than another, but that has to do with air permeability, not R-value. Of course, installation matters, and your insulation will only perform as well as the installation. Ultimately, the R-values you need in an assembly will be determined by code requirements and performance goals.
Air permeability
A continuous air barrier is a key component of any high-performance home, and it’s even more important than insulation for durability, energy performance, and comfort. (If air is passing through your insulation, it increases convective heat loss.) When it comes to air permeability, insulation falls into one of two basic categories: air permeable or air impermeable. You can use air-impermeable insulation as the primary air barrier in your building assembly, but that’s not to say that air-impermeable insulation is always the better choice.
It’s becoming very common for air-sealing to be done on the exterior of the building envelope, with taped sheathing, for example. With a well-detailed exterior air barrier, an air-permeable insulation like mineral wool will perform just fine in the walls.
There are times when an air-impermeable insulation makes sense. One common example is the use of rigid foam to retrofit insulation from the interior at the rim joists of older homes. The rim area is prone to air leakage. So installing air-impermeable rigid foam, and sealing it in place with canned spray foam or caulk, not only increases thermal performance at the rim joist but also stops air infiltration from outside. It also keeps potentially moisture-rich interior air from reaching the sheathing and condensing (turning into water). That’s where vapor permeability comes into play.
Fiberglass
Fiberglass insulation is widely available in batt and loose-fill form. Batts come in two standard widths for wood-frame construction and are commonly available with formaldehyde-free binders. Batts consist of spun glass fibers and come with or without a facing, such as kraft paper or foil. Careful installation is essential to avoid gaps that reduce effectiveness. Batts are not an air barrier and can’t be used below grade.
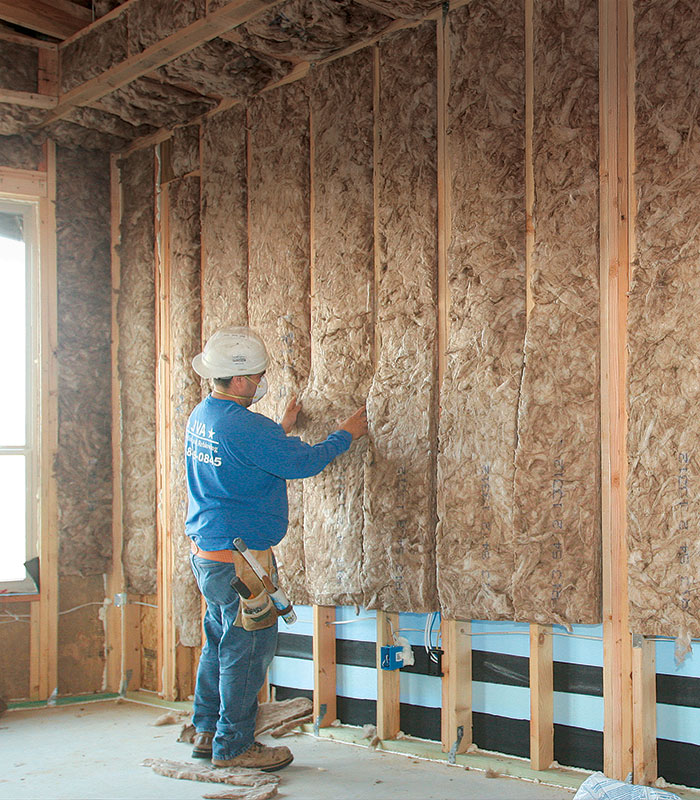
In loose form, fiberglass can be blown onto attic floors or, in higher densities, into wall and ceiling cavities. It’s available by the bag from big-box retailers. The fibers fill voids more effectively than batts, reducing air leaks, but blown-in fiberglass is not considered an air barrier. Loose-fill in an attic has DIY potential, but dense-pack application requires better equipment and more skill. Use above grade in walls, ceilings, and attics.
R-value: R-3.1 to R-4.2 per in. (batt); R-2 to R-4.2 per in. (blown), depending on density
Cost: Low
Net carbon emissions: Low (R-3.6 batt, 1.2; R-2.6 blown, 1.8)
Toxicity: Low, but wear a face mask and long sleeves to reduce skin and bronchial irritation (some brands are advertised as no-itch)
Installation: Batts and loose-fill in attics are accessible to homeowners as well as pros, but beware of sloppy work that reduces effectiveness. Dense-pack fiberglass is best left to professionals.
Cellulose
Cellulose is shredded newspaper or cardboard and is available by the bag or in batt form. There are no rigid panels. Cellulose has strong environmental credentials, and it’s a favorite among many green builders because it has high recycled content. Unlike fiberglass, which has about the same R-value, cellulose sequesters carbon. It can absorb moisture from the air and then release it when the air dries out. But because it readily absorbs water, plumbing and roof leaks can go undetected. It’s used as loose-fill in attics and as dense-pack and in batt form in enclosed wall and ceiling cavities. Dense-pack cellulose installed at 3.5 lb. per cu. ft. is more resistant to air leaks than fiberglass, but cellulose is not an air barrier. It can be used in above-grade applications only. DIYers can rent blowers for loose-fill, but dense-pack calls for professional tools and skills. It is typically treated with borate as a fire retardant.
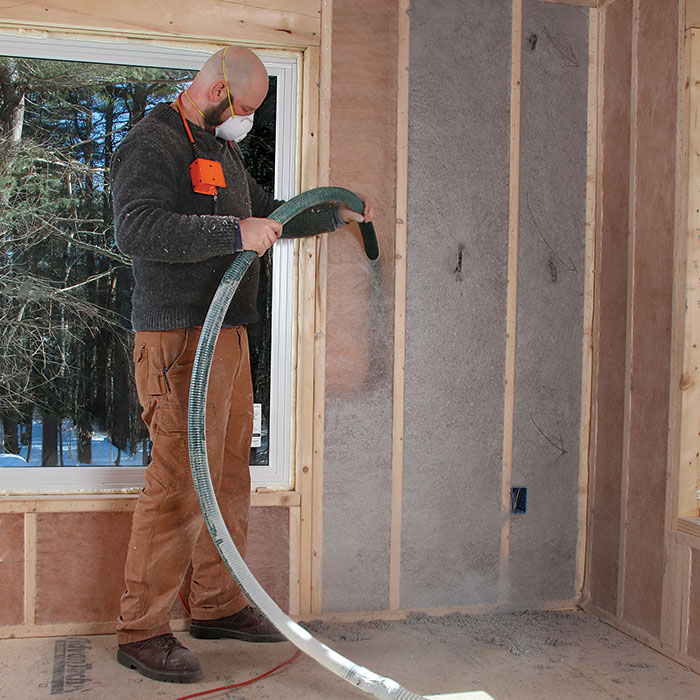
R-value: R-3.2 to R-3.8 per in.
Cost: Low (somewhat more than blown-in fiberglass)
Net carbon emissions: Sequesters carbon (R-3.7 dense-pack, –1.8)
Toxicity: Low
Installation: Similar to blown-in fiberglass. DIYers can tackle loose-fill in attics, but hire a professional installer for dense-pack. Wear a face mask.
Spray foam
Available in two basic types—closed-cell and open-cell—spray polyurethane foam has some unique performance characteristics but also raises a few environmental concerns. At 2 lb. per cu. ft. (vs. 1⁄2 lb. per cu. ft. for open-cell foam), closed-cell foam is the denser of the two. Closed-cell foam also acts as a vapor retarder, while open-cell foam is vapor open, a difference that becomes important in some applications. Open-cell foam uses water or carbon dioxide as the blowing agent, an environmental advantage, while blowing agents in closed-cell foam remain a sore point among green builders. Newer versions of closed-cell foam use hydrofluoroolefin (HFO) blowing agents, with a relatively low global-warming potential, but older formulations use a hydrofluorocarbon (HFC) with a much higher climate impact. (Icynene has developed a medium-density, closed-cell foam that is blown with water.) While these differences are important, both open- and closed-cell foam share an ability to fill wall and ceiling cavities very effectively and are excellent air barriers. Both are expensive, especially closed-cell foam, but it comes with a higher R-value. Both types are made by mixing two components on-site as they are sprayed by the installer.
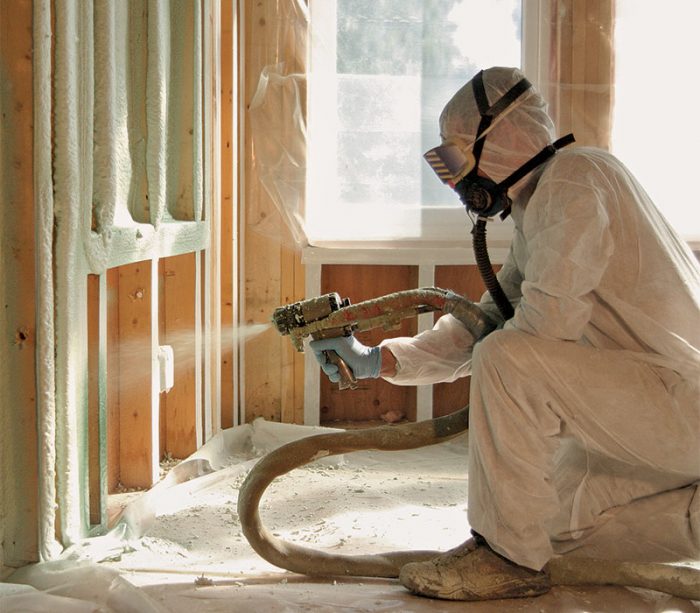
R-value: R-3.5 to R-3.6 per in. (open-cell); R-6.5 per in. (closed-cell)
Cost: High
Net carbon emissions: Moderate to very high (R-4.1 HFO-blown open-cell, 2.9; R-6.6 HFC-blown closed-cell, 23.2)
Toxicity: Stay out of the house during installation. There are reports of lingering odors and/or off-gassing that affect chemically sensitive people.
Installation: Open-cell has a much higher rate of expansion and typically is allowed to overfill cavities and be cut back when cured. Care must be taken not to apply closed-cell foam in too thick a layer, which can cause a fire. Premises should be vacated while foam is applied. Odors from closed-cell foam can linger, but properly mixed and applied insulation is inert once cured.
Vapor permeability
Air permeability and vapor permeability are connected. Vapor permeability, which is measured in perms, describes a material’s ability to allow water vapor to pass through it. At above 10 perms, insulation is considered “vapor open.” Mineral wool falls into this category, meaning that water vapor can pass through unimpeded. At 10 perms or less, insulation is considered a vapor retarder (meaning that water vapor passes through, but at different rates) in one of three classes defined by the International Residential Code (IRC):
• Class I: Less than or equal to 0.1 perm. Foil-faced rigid foam falls into this category.
• Class II: Greater than 0.1 perm but less than or equal to 1.0 perm. The IRC puts kraft-faced fiberglass batts in this range, though some may become more vapor open as humidity levels rise.
• Class III: Greater than 1.0 perm but less than or equal to 10 perms. Unfaced rigid-foam insulation generally falls into this category.
To determine if the insulation you are using has an appropriate perm rating for your project, you need to understand the vapor profile and condensing surfaces of the assembly. For example, if you are building in a cold climate, where it is advantageous to slow outward vapor drive in the winter, a kraft-faced fiberglass batt may make sense. If you were to use a low-perm exterior insulation on the same wall—say, foil-faced rigid foam—you may choose an unfaced batt so the wall could dry more readily toward the interior should it get wet.
Mike Xenakis, building performance lead at New Frameworks, a construction company in Vermont, says that prioritizing bio-based insulation like cellulose has pushed his company toward vapor-open wall assemblies. “That means we need a robust air barrier,” he explains. “We’re typically building homes with one or less air changes per hour. We do mid-stream blower-door tests and a lot of quality control on the air barrier.”
Moisture tolerance
The most common example of when the moisture tolerance of an insulation matters is when it is used in contact with the earth or outside the building envelope, where fibrous insulation is typically not a viable choice. When insulating beneath a slab or on the outside of a basement, the most commonly used insulation types are EPS or XPS rigid foam, because they hold up to wetting. (Both can work, but many green builders avoid the high global-warming potential of XPS.) Because it is water resistant, mineral wool can also be used in these applications, though it is less common.
“I like GPS [graphite extruded polystyrene] and Rockwool under slabs,” wrote builder Travis Brungardt in an email. “But if Glavel continues to get cheaper, it’s an ideal underslab insulator—especially in remote areas where access for trucks and heavy equipment is challenging.”
Another example of builders choosing insulation for its moisture tolerance is the common option of dense-pack cellulose in double-stud walls, though for different reasons. Dense-pack cellulose is a so-called hygric buffer, meaning that it can absorb, distribute, and release moisture without degradation. “[Cellulose] is an affordable material, has very low embodied energy, can be repaired, and works very well as a buffer when vapor drive spikes,” wrote Dan Kolbert in “A Case for Double-Stud Walls” (FHB #291). “It can hold and redistribute vapor, releasing it to the dry side, in ways that foam, fiberglass, or [mineral] wool can’t.”
Installation details
There are at least as many ways to install insulation as there are insulation types. Some insulation can be installed by a homeowner or general contractor fairly well. Blown-in attic insulation comes to mind. Other types, like open- and closed-cell spray foam, require experienced professionals. In either case, it is critical to know how the material is properly installed and what prep is required.
For example, before you rent a machine and start blowing loose insulation into your attic, make sure all air-sealing work is complete, or you’re wasting your time. Sometimes environmental conditions are critical. For a proper spray-foam installation, the chemical components must be warm, and the ambient and surface temperatures must fall in a specific range. If an installer tells you these things don’t matter, be wary. A spray-foam installation gone wrong is not an easy thing to make right.
“We prioritize the ability to do a great job on the install with ease and comfort,” wrote Brungardt. “Similarly, we like the ability to readily confirm proper installation. You need more than a walk-through look-around and will have to break out the IR camera if spray-foaming, dense-packing cellulose, or using faced batts.”
Expanded polystyrene
EPS is a lightweight rigid foam used in a variety of applications: as a continuous layer of insulation in exterior wall and roof assemblies to cut thermal bridging, under slabs, and on the outside of foundation walls. Unfaced EPS is vapor permeable and available in a number of densities with corresponding compressive strengths. Higher densities do better below grade. The blowing agent for EPS is pentane, a hydrocarbon. EPS does not contain hydrochlorofluorocarbons—potent greenhouse gases—and so is preferred by many green builders. EPS manufacturers in the United States have replaced a brominated flame retardant called HBCD with a polymeric retardant, which is thought to be safer. EPS’s thermal performance does not degrade over time. GPS (graphite polystyrene) is an EPS variant that is infused with graphite. It has a characteristic gray color and a higher R-value than conventional EPS. It is more common in Europe than the U.S. and has lower carbon emissions than traditional EPS.
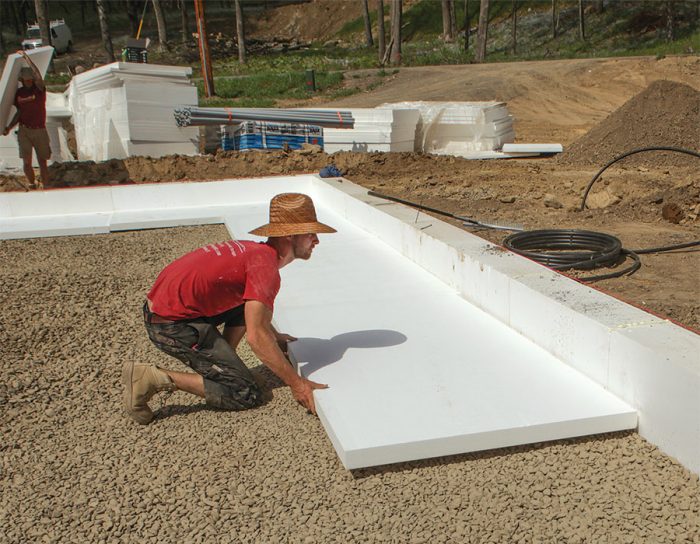
R-value: R-3.6 to R-4.2 per in. (GPS, R-4.7 per in.)
Cost: Moderate
Net carbon emissions: Moderate (Type II R-4, 6.6; GPS Type II, 4.9)
Toxicity: Low
Installation: Used in wall and roof assemblies, under slabs (at the correct density), on foundation walls, and in insulating concrete forms. Lightweight and easy to handle.
Extruded polystyrene
XPS is another common rigid foam with slightly higher R-values than EPS. One of the principal chemical differences between the two is that all XPS has until recently been made with a hydrofluorocarbon blowing agent with more than 1400 times the global-warming potential of carbon dioxide (HFC-134a). This alone steers many green builders toward another insulation choice. However, Owens Corning announced a switch to a new XPS formation that eliminates HFC-134a. XPS is not as vapor permeable as EPS (about 1 perm for an unfaced, 1-in.-thick panel), it is somewhat higher in cost, and its thermal performance declines over time (“thermal drift”) as the blowing agent slowly dissipates and is replaced with air. Exactly where the R-value bottoms out is unclear, but it’s estimated that XPS will decline to R-4.5 in the first 20 years, and eventually to R-4.1 or R-4.2. It is available faced and unfaced. There are three makers in the U.S.: Owens Corning, Dow, and Kingspan.
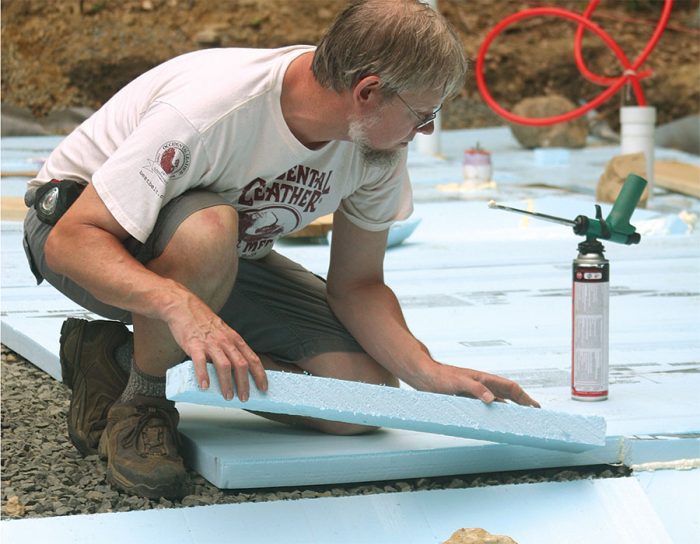
R-value: R-5 per in. (when manufactured)
Cost: Moderate
Net carbon emissions: High to extremely high (Owens Corning NGX, 14.3; conventional HFC-blown XPS, 98.7)
Toxicity: Low
Installation: Similar uses as EPS
Polyisocyanurate
Polyiso completes the trio of commonly used rigid-foam insulation materials. Because of the method used to manufacture it, it is always faced. Foil facing makes it vapor impermeable. One big difference in the field is that polyiso is not rated for ground contact, so it’s never used below a slab or to insulate foundation walls from the outside. One of its principal uses is as roofing insulation. Polyiso is subject to thermal drift, with its R-value dropping from about R-6.5 per in. at the time of manufacture to about R-5.6 or R-5.7 per in. over time. Polyiso also has another quirk: Its thermal performance goes down with the temperature, from R-5.6 or R-5.7 when it’s 75°F to about R-4.8 when the mercury drops to 25°F, although manufacturers are looking for ways to counter this problem. Like EPS, polyiso is blown with pentane, a compound with a relatively low global-warming potential. Polyiso is more expensive than XPS and EPS and is not recyclable.
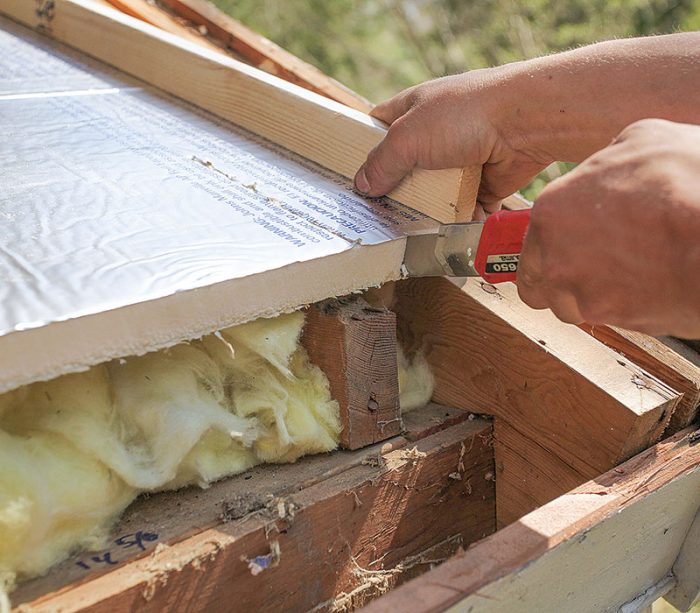
R-value: R-6.5 when manufactured, declining to R-5.7 over time (lower in cold temperatures)
Cost: Moderate
Net carbon emissions: Moderate (5)
Toxicity: Low
Installation: Used like other foam-panel insulation materials
Wood fiber
Wood-fiber insulation comes in several forms, including rigid panels, batts, and loose material that’s blown into enclosed cavities in the same manner as cellulose or fiberglass. Timber HP is the only U.S.-based manufacturer, though the company’s board, batt, and loose-fill products are still being developed. Two imported brands are Steico and Gutex, both manufactured in Europe. Though imported options are expensive, wood fiber has appealing characteristics: It is manufactured from a renewable resource without petrochemicals, it has no embodied carbon, and it has low toxicity. Panels are nonstructural and vapor-open. Wood fiber is often used as a continuous layer of insulation on roofs and exterior walls. European products come in odd sizes.
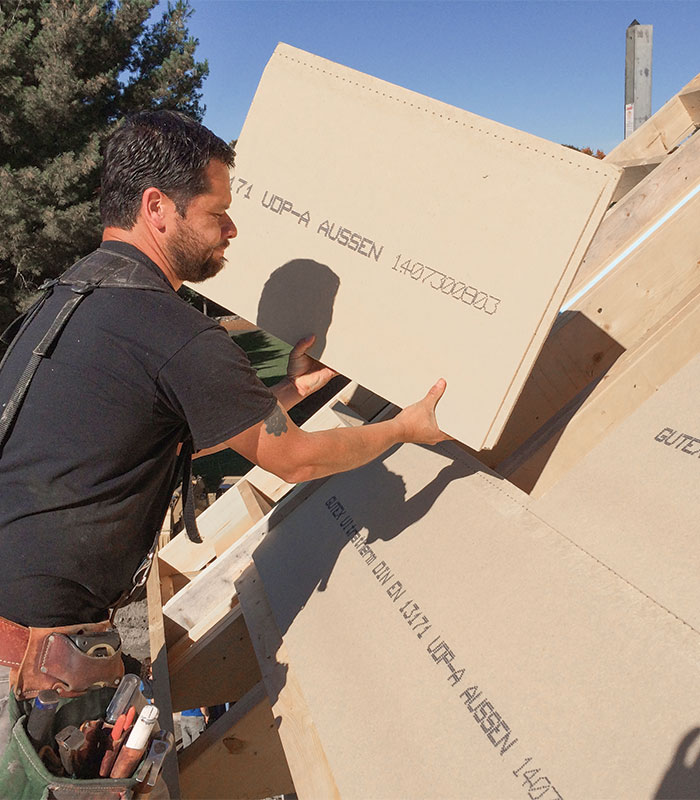
R-value: R-2.7 to R-3.7 per in. (panels); R-3.9 to R-4 per in. (batts); R-3.6 to R-3.8 (blown-in)
Cost: High
Net carbon emissions: Sequesters carbon (R-3.8 batts, –1.9)
Toxicity: Very low
Installation: Loose wood fiber is handled like cellulose; panels go up like rigid foam and can remain exposed to the weather for a number of weeks without damage.
Global-warming potential
Today, every building material should be evaluated for its environmental impact. It’s not always an easy equation, and including this criterion doesn’t make decisions any simpler. Sometimes a better-performing material may also come with a greater climate cost. XPS rigid foam performs excellent below grade. It also has one of the highest global-warming potentials of all insulators. Cellulose has a minimal environmental impact, but you can’t use it to insulate below your slab. Sometimes we can change the building assembly to make a more sustainable option work. When we can’t, compromises need to be made.
Costs
Every building project has a budget, so every material choice comes with a cost; therefore, cost deserves a place on this list. It may also be the most challenging factor to discuss. First, there’s the practical reason that costs vary from one region to the next. We can generalize—fiberglass is probably at the low end of the cost range all around the country; mineral wool is often a premium product. On the other hand, spray foam and cellulose costs vary widely based on how common and available they are in a given region.
The other reason it is difficult to discuss cost is because of the impact an insulation choice has on the rest of the budget. I’ve talked to enough designers and builders over the years to know that it’s much easier to sell clients on nicer flooring or a tiled shower than on energy improvements like insulation. I’ve also learned that client education is an often-overlooked piece of the puzzle. If your clients understand that more or better insulation is part of a robust envelope, which means they will spend less on their mechanical system, there’s a better chance that they’ll spring for it. I’ve often been impressed when I visit high-performance homes at how much the owners know about the nuts and bolts of their house. This is usually a credit to the architect or builder who did a good job of educating them throughout the process.
“It’s our duty,” says Xenakis. “We have to help our clients understand that there are upfront costs, there are overtime costs, and there are environmental costs. We have to weigh it all, specific to each job.”
Cotton batts
Made principally from denim scraps with some additional synthetic fiber, cotton batts can be used only above grade in wall and roof assemblies. Unfaced batts are air permeable and come in oversized widths for a friction fit in framing cavities. Some installers complain it is difficult to cut and doesn’t always bounce back after compression. Like other types of batt insulation, it must be fitted carefully around wires, pipes, and other obstructions in wall and ceiling cavities. It is more expensive than fiberglass and mineral wool batts, but Bonded Logic, which manufactures Ultra Touch, promotes its no-itch natural fiber content. It is treated with borate for fire resistance and includes high recycled content (80% postconsumer).
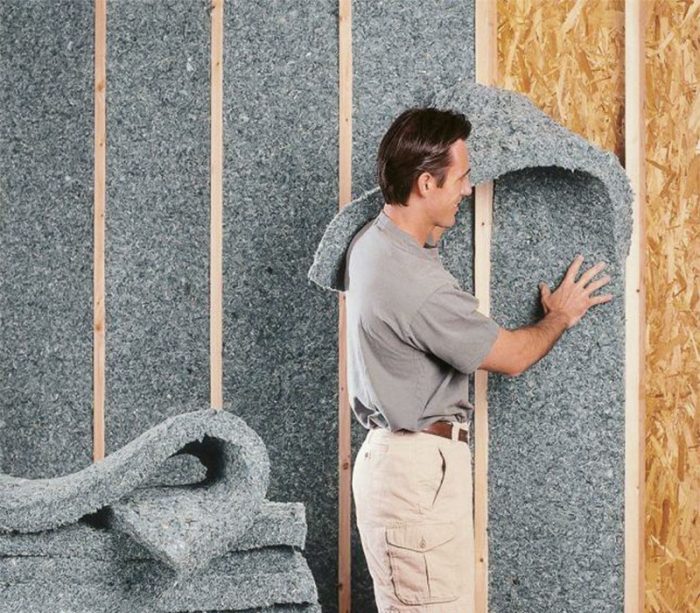
R-value: R-3.5 to R-3.7 per in.
Cost: Moderate
Net carbon emissions: Moderate (R-3.6 batt, 2.3; R-4.4 loose fill, 3.4)
Toxicity: Low
Installation: Similar to other friction-fit batts, but not as easy to trim. Manufacturers emphasize “no itch” qualities.
Straw
Straw has extremely attractive environmental credentials. It is reclaimed agricultural waste, a raw material that is completely renewable and, regionally, widely available. It has very low toxicity, good fire resistance, and very high carbon capture. Straw mostly is used in the form of bales that are assembled into walls on-site and then finished with stucco or plaster. It’s also available in panel form. EcoCocon, a European manufacturer operating in the United States as Build With Nature, offers a 15.7-in.-thick structural insulated panel with an R-value of 38. The load-bearing panels with a continuous layer of wood fiberboard insulation cost about $18 per sq. ft. (but this number includes the wall structure as well as insulation). Straw-bale construction is not common, but proponents are passionate about its advantages. It has low R-value per inch, but thick walls make up for it. Bales can be used as structural components or as infill in wood- or steel-framed structures. Straw bales are susceptible to water damage, so buildings need wide roof overhangs, careful flashing over windows and doors, and separation from moist materials. It offers high DIY potential.
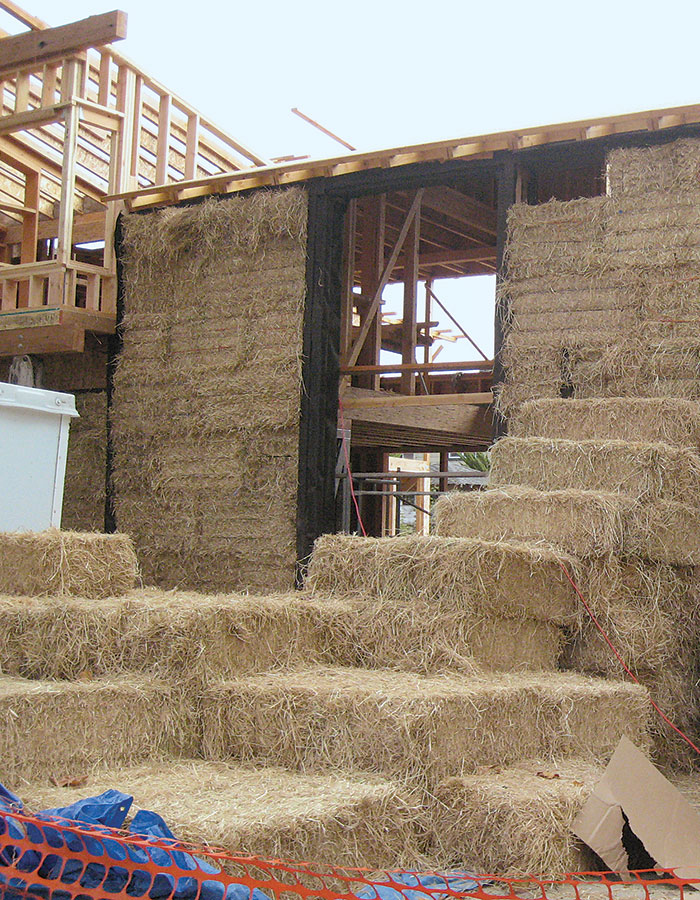
R-value: R-1.4 to R-2.4 per in.
Cost: Low (bales) to high (prefabricated panels)
Net carbon emissions: Sequesters carbon (R-2.9, –14.5)
Toxicity: Very low
Installation: Straw bales can be incorporated into buildings as infill or structural components as a low-tech building method friendly to owner/builders. Straw panels are comparable to other types of structural insulated panels (SIPs).
Hemp
Hemp is another renewable agricultural material that scores well on the carbon sequester scale, second only to straw. But hemp insulation has struggled to gain a toehold in the market, and supplies of hemp insulation are spotty. A Kentucky company called Sunstrand LLC was producing R-13 batt insulation for 2×4 walls, but the company filed for Chapter 7 bankruptcy. A Quebec-based company, MEM Inc., continues to produce hemp blocks as well as sheets of hemp insulation 3-1 ⁄ 2 in. and 5-1 ⁄ 2 in. thick, with R-values of R-13 and R-20, respectively. The insulation is 88% hemp and 12% polyester. Hempcrete is another form of hemp insulation. It’s mixed from hemp hurds (the cores of the plant), plus lime and water, and formed into blocks in steel or metal frames or tamped into moveable lifts to make larger wall sections. The low-density material is not load-bearing. It is vapor permeable. Hemp can be ordered from companies such as American Lime Technology. For more information, contact the U.S. Hemp Building Association.
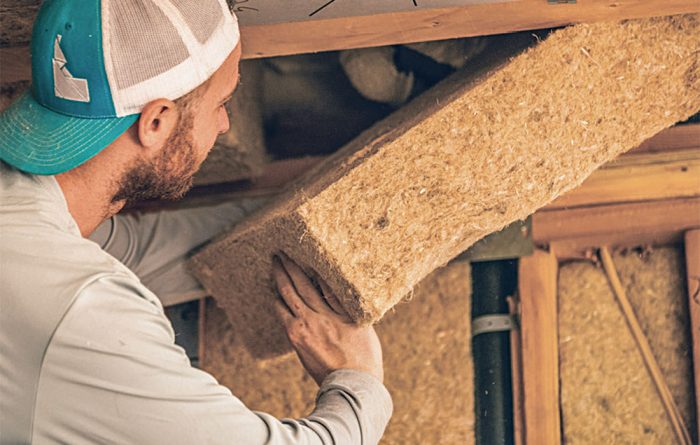
R-value: R-1.2 to R-3.7 per in.
Cost: Moderate
Net carbon emissions: Sequesters carbon (R-3.7 batt, –3.1)
Toxicity: Very low
Installation: Hemp panels are installed between studs on 16-in. centers. Hempcrete blocks and wall sections can be made on-site and may have the same DIY appeal as straw-bale construction.
Cork
Manufacturers point to the strong environmental credentials of cork insulation—100% renewable, recyclable, and about as green as it gets if you don’t figure in transportation from the western Mediterranean where cork oaks grow. ThermaCork, a supplier, lists panels from 1 ⁄ 2 in. to 3 in. thick. Expanded corkboard is made from the outer bark of the trees, which reportedly suffer no harm in the harvesting process and may live to be hundreds of years old. Eco Supply Center is a U.S. distributor for ThermaCork. The company says that 95% of cork products come from Portugal and that cork insulation was once common in the United States, having even been used at the White House. It is semi–vapor permeable (2 perms at 2 in. thick).
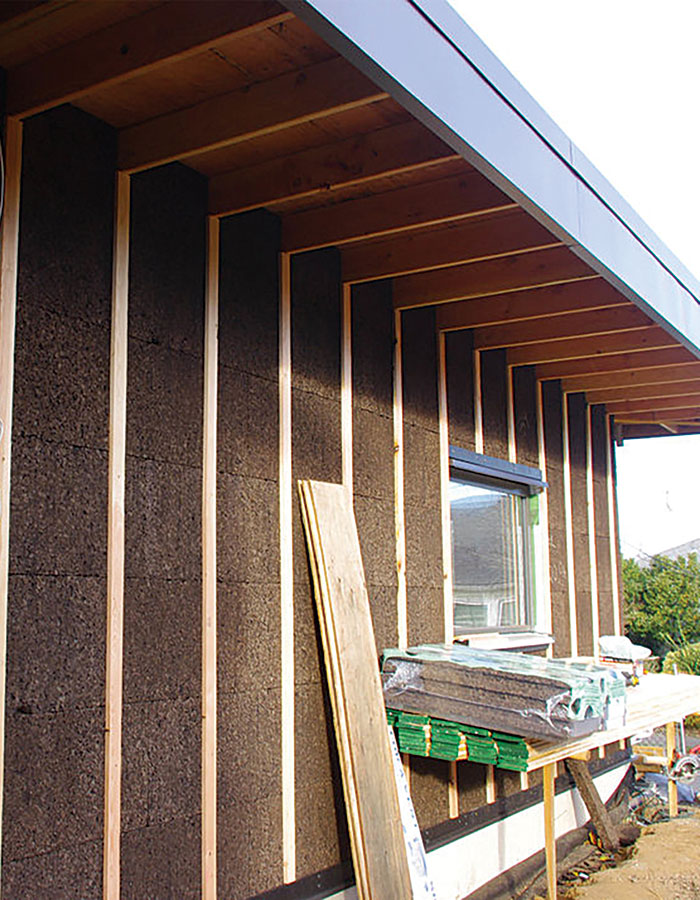
R-value: R-3.6 to R-4.2 per in.
Cost: High
Net carbon emissions: Not available
Toxicity: Very low
Installation: Installed like other board insulation. Some versions can be used as exterior cladding, where it weathers from a chocolate brown to a concrete-like shade.
And the list goes on
I recently insulated below a basement slab with EPS rigid foam that I ordered from a company located a couple hours from where the product was manufactured. Had I not been fortunate to be emailing with designer Michael Maines, who turned me on to Branch River Plastics at the time that I needed to order the insulation, I would have used next-gen XPS from the local big-box store at a higher financial and environmental cost.
I got lucky, but availability is a real issue. If you want to use wood fiber as exterior continuous insulation, you probably can’t run down the street to get it. But as Maines pointed out to me, when we are building custom homes, we have the time to do the research and source the best products for the job. Maines was the one who suggested I add “availability” to my list of criteria for choosing insulation.
Peter Pfeiffer, principal at Barley/Pfeiffer Architecture in Austin, Texas, brought another consideration to my attention: sound attenuation. In the hot and humid climate where most of his projects are located, he prefers a flash-and-fill insulation system, with a flash coat of closed-cell spray foam to provide R-value, vapor control, and additional air-sealing (though he specs a primary exterior air barrier at the sheathing), and a fill of dense-pack cellulose that he says can effectively hold and redistribute excess moisture created inside the house. Pfeiffer calls this a perfect system and includes the fact that it makes for a quiet interior, which is important to many urban homeowners.
There’s even more to consider: What happens to a material at the end of its initial service life? Rigid foam and mineral wool, for example, can often be reused. If insulation can be left exposed—in an unfinished basement, for example—most foam plastics must be covered with something that provides a code-required fire rating. And there are health concerns for installers and folks with chemical sensitivities; at a minimum, make sure you and your installers are taking the appropriate safety precautions for whichever type of insulation you are installing, and educate your clients on the potential risks of off-gassing.
What are your priorities?
I’m wondering now if my list isn’t flawed from the start. I came at the topic with efficiency and comfort top of mind. But it seems that any insulation can accomplish this. And the air-, water-, and vapor-control layers can ensure that the building enclosure is durable and tight.
I didn’t create this list with an order of importance in mind. I started with the most obvious consideration (R-value) and ended with cost—which is ultimately important to the person writing the checks but has no implication on the quality of an assembly. Reviewing the list now, I am concerned that global-warming potential and human health are toward the end, where they could be interpreted as less important than the other considerations. Maybe human health and global-warming potential should be prioritized. Maybe the question shouldn’t be “How do I choose the best insulation?” but “How do I use the most environmentally friendly insulation with the least risk to human health to create a comfortable and efficient house?”
Isn’t that what’s most important?
—Brian Pontolilo is a former editor at Fine Homebuilding and Green Building Advisor.
—Scott Gibson, a frequent writer for both FHB and GBA, contributed to this article.
From Fine Homebuilding #316
Fine Homebuilding Recommended Products
Fine Homebuilding receives a commission for items purchased through links on this site, including Amazon Associates and other affiliate advertising programs.
Loctite Foamboard Adhesive
Nitrile Work Gloves
Great Stuff Foam Cleaner
View Comments
I am restoring a 100+ year old house in Tennessee, built out of masonry blocks (rock faced block fashionable in the 1920's). There is no framing or, of course, insulation against the exterior walls. There is no capillary break between walls and the foundation (built out of the same blocks). I have been advised (by insulation professionals) to use and NOT to use nearly every single material listed in this article. unfortunately, one pro's logic for or against a certain material runs diametrically counter to the next one's. I am currently leaning toward offsetting the framing by 3-4 inches and spraying closed cell foam against the block but would greatly appreciate some sound advice for this situation.
Thank you for the comprehensive overview of insulation options. With respect to polyisocyanurate (polyiso) insulation, manufacturers do offer products intended for ground contact applications such as below grade and below slab. While long regarded as a roof insulation product, different facers allow the product to be used in a wide variety of applications (e.g., continuous wall insulation and below grade). The industry trade association has made information available on below grade uses of polyiso insulation (https://www.polyiso.org/page/TB601). Manufacturers also publish installation instructions for below grade applications. Perhaps the authors can update the article after a review of this information.