How Good Is Your Air Barrier?
If your goal is extremely low air leakage, choose your materials carefully.
Pointing to benefits ranging from lower energy costs to healthier indoor air, building scientists have long recommended that houses be constructed so they are essentially airtight. Model building codes have followed suit by gradually requiring tighter as well as better-insulated dwellings.
The 2021 International Residential Code (IRC) sets specific airtightness standards for new houses, verified with a blower-door test. Maximum permitted air leakage—described as air changes per hour at a pressure difference of 50 pascals, or ACH50—varies by climate zone and whether the builder follows a prescriptive or performance path to code compliance.
As a result, even builders skeptical about airtight construction should be meeting these minimum standards. Builders and designers who work on high-performance houses left these code minimums in their rear-view mirrors years ago. At the far end of this spectrum are buildings certified by the Passive House Institute, whose benchmark is 0.6 ACH50—very tight indeed.
Creating airtight houses requires a range of techniques and materials. An air barrier is not a single material but a combination of materials that together form a continuous air-impermeable layer that should be readily identifiable on construction drawings. Various flashing tapes, sealants, and gaskets are essential parts of the puzzle, but a lot of the heavy lifting is done with materials that cover big areas—sheathing, drywall, housewrap, and peel-and-stick membranes.
How airtight each of these materials is has an impact on the overall airtightness of the building. The more rigorous the airtightness standard, the more important the physical characteristics of the material. The time to ensure airtightness is while the house is being put together. Revisiting the problem later and trying to correct air leaks is expensive and time consuming.
As Laverne Dalgleish, executive director of the trade group Air Barrier Association of America (ABAA), says, “You’ve got one chance to do this without costing you a phenomenal amount of money to do a retrofit.”
First, what is an air barrier?
An air barrier is just one of the four control layers that need to be managed to maintain healthy, comfortable, and energy-efficient spaces. Water, vapor, and thermal (temperature) are the other three, and while many of the materials chosen to build the envelope of a home can operate as more than one control layer, this article will focus just on air barriers. An ideal air barrier should be strong, durable, continuous around the entire building enclosure, and, of course, air impermeable. “Air barriers keep outside and inside air out of the building enclosure,” Joseph Lstiburek wrote in a paper published by the Building Science Corporation. “Air barriers can be located anywhere in the building enclosure—at the exterior surface, the interior surface, or at any location in between.”
In other words, the air barrier can be in the form of exterior sheathing or a combination of sheathing and a membrane, it can fall in the middle of the wall as a layer of spray polyurethane foam or another impervious material, or it can be on the inside of the building, as a layer of gypsum drywall or specialized building paper.
One air barrier is essential. Some builders and researchers think there should be more than one air barrier in a building—one on the inside and one on the outside.
Air impermeability is key, but what exactly does that mean? In technical terms, it means that air leakage is limited to a certain volume of air at a certain air pressure. The industry standard for a specific material like drywall, housewrap, or sheathing is 0.02 L/s/m2 (liters per second per square meter) at a pressure of 75 pascals.
Materials leakier than this don’t qualify as an air barrier, and builders looking to meet rigorous airtightness standards should think twice about using them.
What material testing reveals
Some materials are assumed to be effective air barriers. They include structural panels such as plywood and oriented strand board, or OSB (at least 3⁄8 in. thick); concrete, flexible water-resistant barriers; and gypsum board.
A number of these materials have been tested, either by their manufacturers or by independent third parties such as the ABAA, using a standardized test—ASTM E2178. Test results can sometimes be found in the fine print from a manufacturer, although you may have to dig a bit to find them. At its website, ABAA posts results of its own testing of a variety of materials used as air barriers. There are 10 self-adhered sheet membranes on the list of tested products, including Siga’s Majvest 500 SA, used by Maine builder Dan Kolbert on a double-stud wall last year. That product showed an air-leakage rate of 0.0003 L/s/m2, many times better than the air-barrier standard. When tested as part of an assembly (using a different ASTM test method), air leakage was 0.004 L/s/m2. These results show that the material is a good choice for an air barrier. The same list includes products from the Henry Company, Polyguard, Demilec, and Dörken, among others.
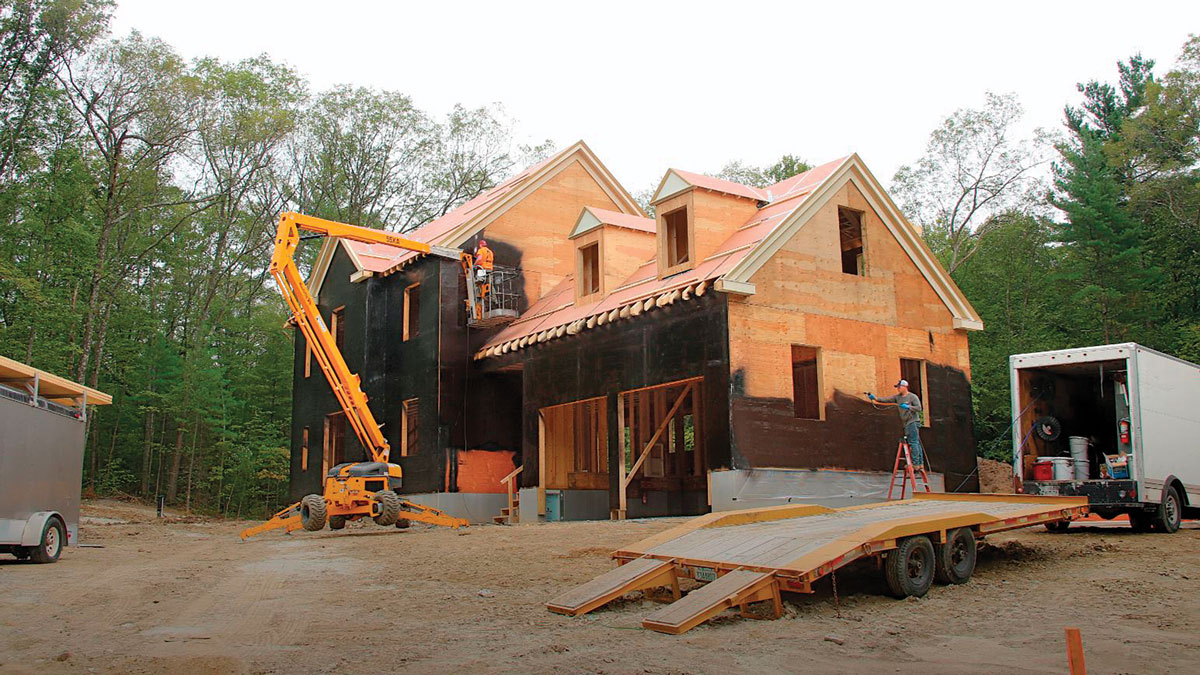
Results also are posted for fluid-applied membranes, medium-density spray polyurethane foam, mechanically fastened commercial building wrap, some rigid board insulation such as Styrofoam, and factory-bonded membranes to sheathing, like Georgia Pacific’s DensElement Barrier System. Some of these products show up routinely on commercial jobs but not so much on residential job sites.
According to Dalgleish, the nonprofit ABAA will test materials submitted by association members, who pay a $5000 fee to join. There are no results at the website for plywood or OSB, Dalgleish says, because no one has submitted them for testing. Likewise, the Oak Ridge National Laboratory, a well-known research facility, says it has the means to test material and assemblies that would be used as air barriers but has not been asked to do so. So there is no data to be mined there.
Don’t bank on OSB alone
Although OSB is assumed to be a reliable air barrier, a round of private testing by RDH Building Science in Waterloo, Ont., found
otherwise. The company was approached by Huber Engineered Woods, which manufactures Zip System sheathing, and was asked to test Zip System, plywood, and OSB for airtightness.
Testing was very limited, involving just one sample of plywood and three samples of OSB, along with three Zip System panels. (The manufacturers of the OSB and the plywood were not identified.) Zip System sheathing is souped-up OSB, coated with a resin-impregnated kraft paper for water and air resistance. Huber executives no doubt felt pretty good about the RDH experiment; it showed extremely low rates of air leakage for 7⁄16-in. Zip sheathing.
Commodity OSB didn’t do as well. None of the samples met the air-barrier standard, and one showed five times the air leakage that would be permitted. After the samples had been put through a wetting and drying routine to simulate job-site conditions, the results were even worse.
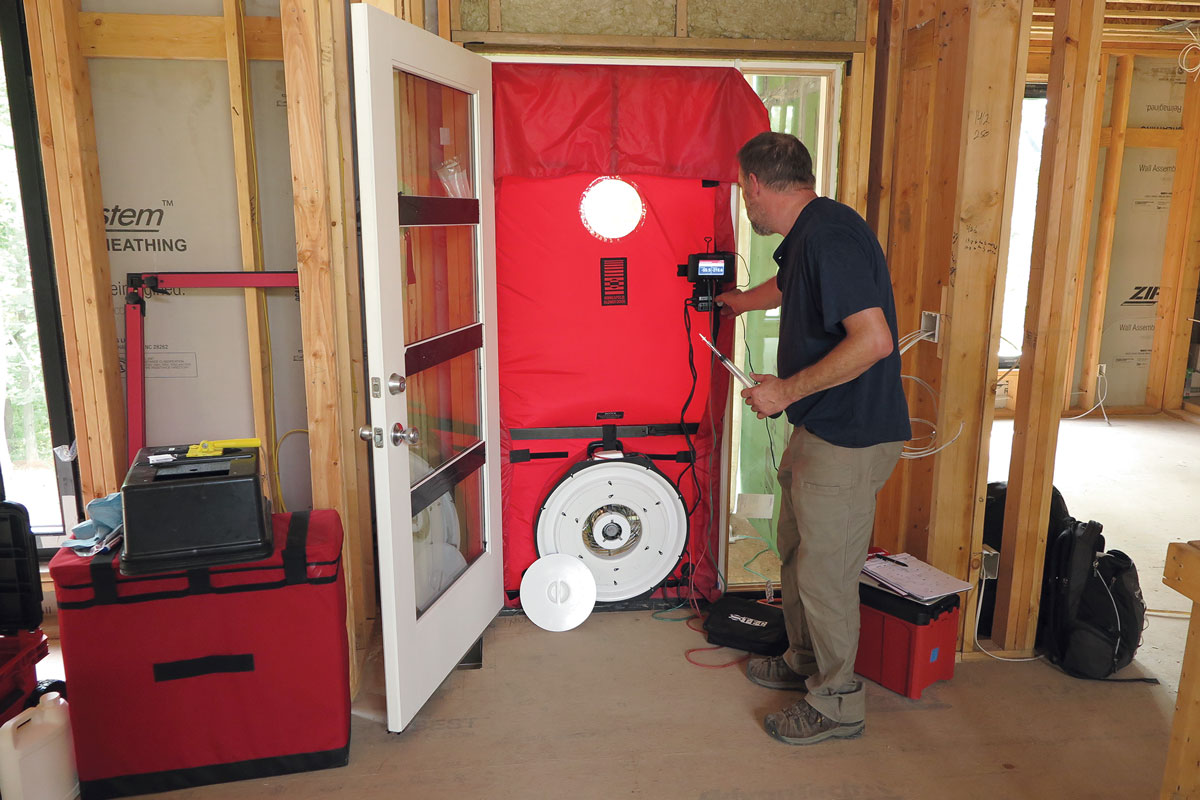
Jonathan Smegal, the lead researcher on the project for RDH, was careful to point out that OSB manufacturers are not making claims about the material’s airtightness. OSB is marketed as structural sheathing, not an air barrier. But given the fact that many builders have been using it for that purpose, the test results were not encouraging.
Dalgleish is not surprised. “Not at all,” he says. “That’s one of the beefs we have with the code. The code has listed a bunch of materials that you don’t have to test. My personal position, and the ABAA’s position, is the same: If you don’t test it, you don’t know.”
He adds that manufacturers working in a very price-competitive market are watching for ways to reduce costs and may change manufacturing techniques or product ingredients when the opportunity presents itself. Such changes may not affect a product’s structural properties, but they could change its air permeability. “Something manufactured five years ago that was fantastic may not be the same material today,” Smegal said.
Air barriers as part of an assembly
Performance of the material itself is one consideration, but materials become part of assemblies. In the RDH tests, plywood was tested alone, then tested again after wetting and drying, and again after it was covered with a layer of taped Tyvek housewrap. At this last stage, Smegal’s group nailed on sections of vinyl siding to see how that affected airtightness. Predictably, leakage went up as the Tyvek-plywood assembly was peppered with nail holes.
Smegal predicted that a house using a similar assembly as its air barrier should easily be able to pass code-required blower-door testing, but probably would not be able to achieve Passive House tightness. It might be hard, he said, to get the house down to a range of 1 to 1.5 ACH50.
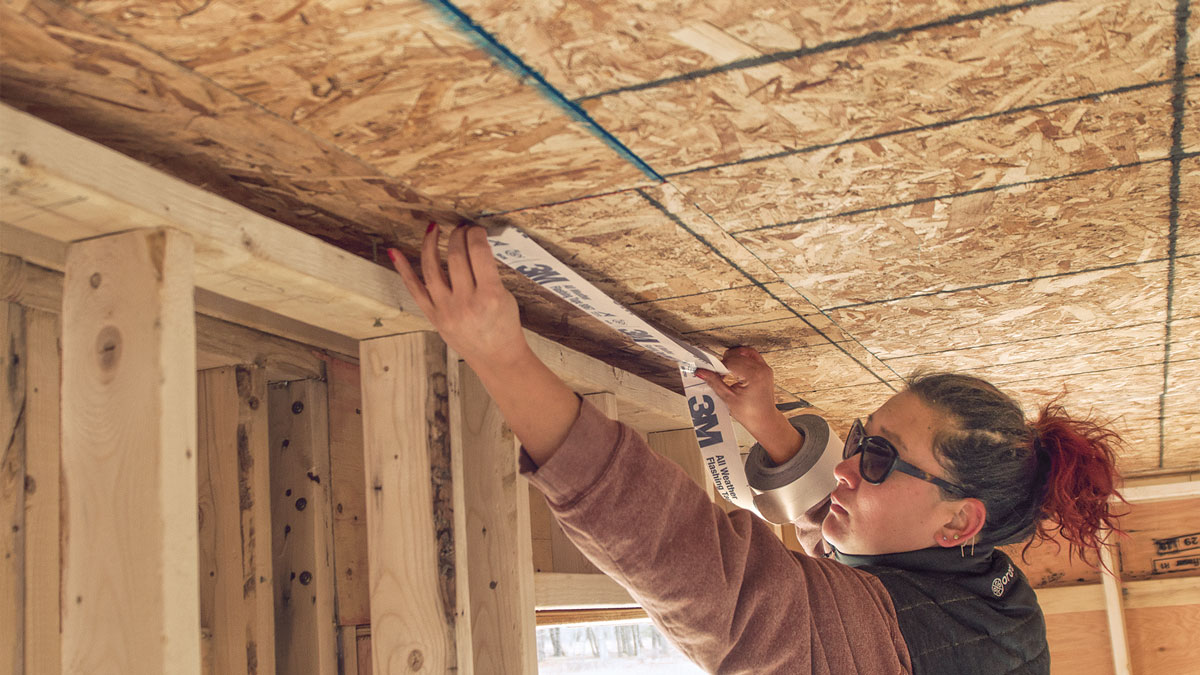
Whole-house results also depend heavily on other parts of the air barrier—components such as windows and doors, seals around plumbing or electrical service entrances, gaskets or sealants under bottom plates on exterior walls, and the many other parts and pieces of the assembled whole. As Smegal pointed out, just because one part of the assembly does not meet the material definition of an air barrier, that does not necessarily mean the building can’t be reasonably tight when complete.
Kohta Ueno, a senior researcher for Building Science Corporation, adds that it’s often the edges and margins of an assembly where air leaks occur, not through a material itself. “We all know that details and connections are where air barriers fail,” Ueno says. “I have done plenty of forensic investigations where they’ve done a beautiful job on the wall, and a fantastic job on the roof, and basically where they came together something happens and you have a 1⁄8-inch gap going hundreds of feet around the building. That adds up to a massive air leak.”
Proper installation may be one of the most important details of all. “Everything comes down to the workmanship,” says Carl Seville, a Georgia building consultant and green-building certifier. “Well-installed housewrap is better than badly installed Zip.”
In the case of housewrap, the material may qualify as an air barrier, but unless it’s installed carefully it will be leaky. If the housewrap is being used solely to shed water, a simple weather lap will be fine. But that won’t be good enough if the housewrap is supposed to be detailed as the air barrier. “Can you detail a mechanically fastened housewrap as an air barrier?” Ueno asks. “You can, but I seldom see that done very effectively.”
When materials are easy to install, it often improves their performance as an air barrier, which helps explain why Huber’s Zip System sheathing is so popular. Nail it up, seal seams with Zip tape, and you’re essentially done (although walls must still be connected to the rest of the air barrier to make it continuous).
Some prefer interior air barriers
Ueno is among those who think that exterior air barriers—in the form of taped sheathing or either liquid-applied or self-adhering membranes—are the best approach. Some builders take the opposite view. One of them is Ben Southworth of Garland Mill in Lancaster, N.H., a high-performance builder with Passive House training.
On the outside of the building, Southworth applies a combination of pressure-treated plywood and Zip System sheathing and tape, but his principal air barrier is on the inside of the house. He uses a vapor-open European membrane such as Intello over the studs. After blowing insulation into the cavities, he carefully tapes the seams. He then adds 2×3 strapping to create a service cavity before installing the interior finish. This approach protects the air barrier from damage, and wiring and plumbing lines are routed through the service cavity, meaning fewer penetrations through the air barrier.
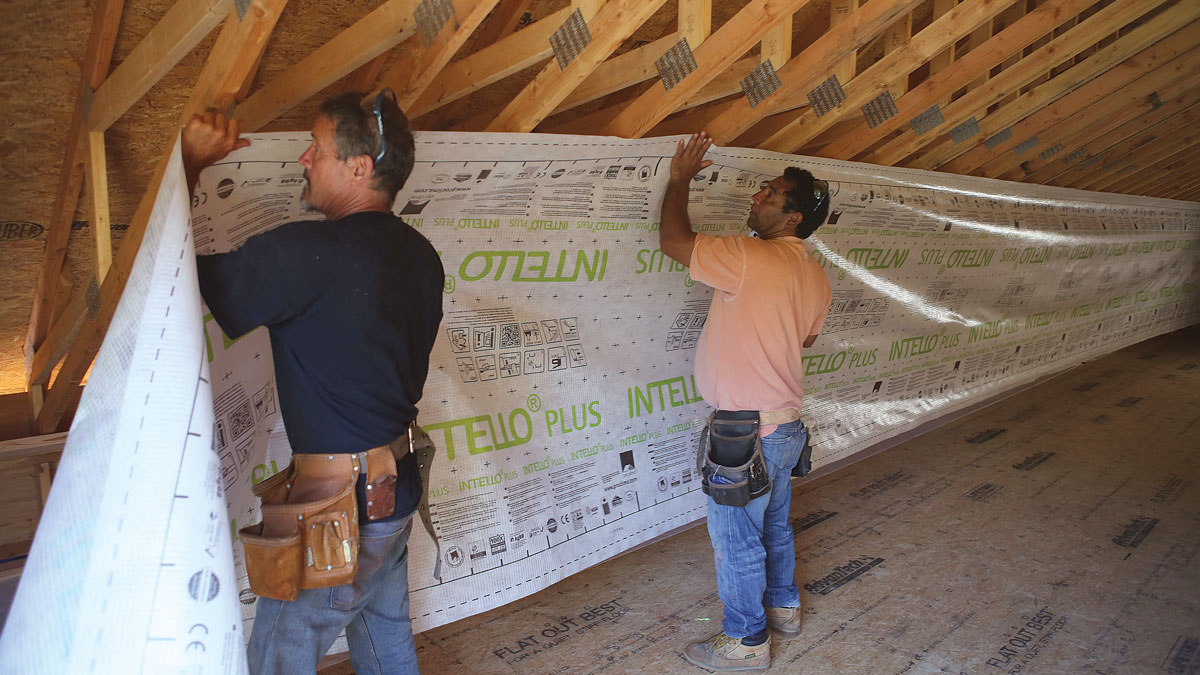
Southworth can easily hit the Passive House airtightness standard, and he thinks an interior barrier makes the most sense. “That’s how they taught us,” Southworth says of his Passive House instructors. “We’re really trying to keep all air, particularly moist air, off the exterior sheathing, that condensing surface,” he continues. “It makes more sense to me to have our line of defense be that interior paper rather than the sheathing.”
The interior mechanical chase makes the building more resilient, and it allows plumbing or electrical lines to be added later without disturbing the air barrier. With sheathing on the exterior sealed at the edges and seams, Southworth is, in effect, using two air barriers, and he routinely gets very low blower-door test results. “It’s not the only way,” he says, “but it’s how we do it.”
Spray polyurethane foam is an air barrier
Spray polyurethane foam is used chiefly as a thermal control layer, but it also can act as an air barrier provided that it’s applied in a thick-enough layer. Open- and closed-cell foams have different densities. An open-cell foam must be applied in a thicker layer than a closed-cell foam in order to qualify as an air barrier. Air permeability varies by manufacturer, but air barriers are commonly created with 3 in. of open-cell and as little as 1 in. of closed-cell insulation.
A foam’s air permeability is reported in a document called an Evaluation Service Report published by the International Code Council Evaluation Service (ICC-ES). These reports are available online. Once you know the type of foam the installer will use, you can look up the report and know exactly how thick the foam should be applied in order to be considered an air barrier.
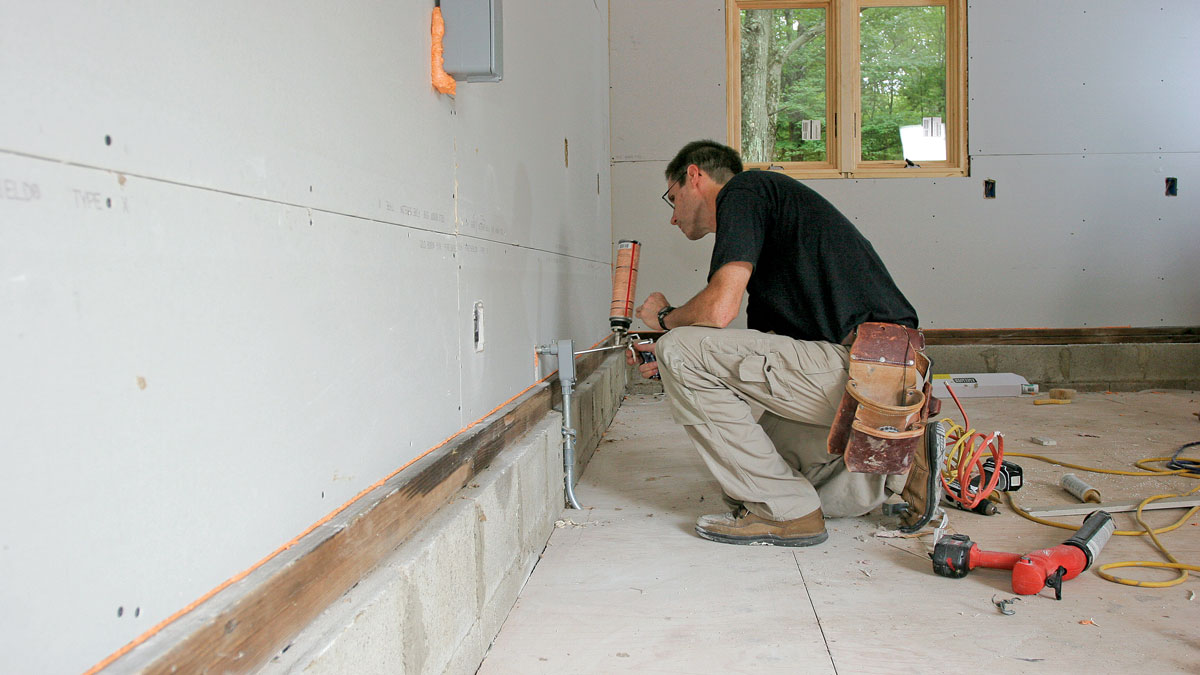
When it comes to spray foam, there are a couple of things to keep in mind. First, spray foam is manufactured at the job site by mixing two chemicals together. However unlikely, it is possible that it will be mixed or applied incorrectly. Second, spray foam doesn’t always make it to areas where leaks occur, such as the seam between a double top plate on an exterior wall.
“Spray foam is a fantastic air barrier where it is,” Ueno says. “It does nothing where it’s not. So any time you have a wood-to-wood joint where it’s not covered up by the spray foam, all of those are potential air-leakage locations.”
AeroBarrier seals from the inside
Another option is a product called AeroBarrier, a liquid sealant that is atomized and forced into gaps and holes in the building enclosure when the building is pressurized. AeroBarrier is a substitute for caulks, tapes, and other air-sealing materials. Airtightness can be verified in real time by technicians, and the company says just about any level of airtightness is attainable. Costs average about $1.50 per sq. ft. of floor area.
One adherent to the AeroBarrier method is Pioneer Builders, a spec builder in Port Orchard, Wash., which typically has four or five houses underway at any one time. According to company vice president Bryan Uhler, Pioneer often aims for an airtightness level of 3 ACH50, sometimes lower, and has found AeroBarrier to be the most cost-effective way to get there. Crews don’t have to take any special air-sealing steps during construction—that’s a big time saver. And AeroBarrier comes in near the end and seals up the building envelope in a matter of a few hours. He likes the system because it saves time and makes job sites safer by eliminating some ladder work.
Costs cover a wide range
Most builders are looking to minimize costs. Some materials used as air barriers are available at just about any lumberyard or big-box store. They include OSB, Zip System sheathing, plywood, and housewrap. Sealing tapes, such as those from Zip or 3M, also are easy to find. Lumber and sheathing prices spiked during the pandemic but have subsided somewhat in recent months. OSB at 7⁄16 in. thick was available for $0.55 per sq. ft. in October in Portland, Maine, while 15⁄32-in. plywood was $0.75 per sq. ft. and 7⁄16 in. Zip sheathing was about $1 per sq. ft. Housewrap cost $0.16 per sq. ft.
Other materials—particularly specialty European membranes—are a little harder to find and are typically more expensive. The Siga Majvest 500 self-adhering membrane that Dan Kolbert uses was $1.12 per sq. ft. from Performance Building Supply in Portland, Maine. Intello Plus (an interior vapor-variable membrane) was $0.45 per sq. ft. at 475 High Performance Building Supply in New York City. Intello X, an exterior version, was $0.48 per sq. ft. The same company also sells a liquid-applied air barrier called Visconn that can be brushed, rolled on, or sprayed. A 2-1⁄2-gal. container costs about $200, which boils down to between $1.18 and $1.60 per sq. ft. depending on how it’s applied. More-complicated applications, such as self-adhering membranes or liquid-applied membranes, also require more labor than taped plywood or Zip sheathing. That’s another cost factor.
![]() The mist that sealsAeroBarrier is a unique approach to air-sealing a building enclosure. An atomized sealant is forced into cracks in the building envelope under pressure, doing the work of caulks, tapes and other conventional sealants quickly and effectively. ![]() |
Think about the airtightness goal
Builders seeking simple code compliance—3 or 5 ACH50—have more room for error in both technique and material selection than someone looking for Passive House levels. Ueno likens air-sealing strategies to having a budget: The tighter the house needs to be, the smaller the budget of total holes in the building enclosure. In a Passive House, covering large expanses of the exterior with commodity OSB as the primary air barrier may use up a disproportionate amount of your total budget of air leaks, leaving little room for error on closing up all the small potential leaks elsewhere. But if the aim is 3 or 5 ACH50 to meet local code requirements, the choice of a particular type of sheathing or self-adhered membrane may not matter as much.
As Ueno puts it, “The goal you have for your project definitely will start to dictate which approach you will take for air barriers.” In in his view, that means an exterior air barrier is the best choice, Ben Southworth’s success with interior air barriers notwithstanding. “If you’re pursuing ultrahigh performance, an exterior air barrier just basically works better,” he says. “That’s how you end up with these fantastically airtight houses. You can see it, you can inspect it, you can ensure continuity.”
From Fine Homebuilding #305
To view the entire article, please click the View PDF button below.
RELATED LINKS
- A Practical Air-Sealing Sequence
- Are There Reasons to Make Homes ‘A Little Bit Leaky’?
- What’s the Science Behind a Code-Built Wall?
Fine Homebuilding Recommended Products
Fine Homebuilding receives a commission for items purchased through links on this site, including Amazon Associates and other affiliate advertising programs.
Respirator Mask
Great Stuff Foam Cleaner
Caulking Gun