Insulating Glass Keeps Getting Better
Windows are still a weak link in a home's thermal envelope, but innovative insulating glass units promise better performance in the future.
Synopsis: Since the introduction of the insulating glass unit (IGU), there have been steady advancements in window assemblies that improve a home’s thermal performance. Contributing editor Scott Gibson describes the progression of IGU design, from the invention of low-e coatings and where they are applied, to the addition of glazing beyond double panes, to suspended films and different types of insulating gas and gives a glimpse into future technologies.
Andersen Windows’s 1952 introduction of their welded, insulating glass panel was a big deal. Consumers could buy an assembly that married two sheets of glass and an insulating layer of air in a single product. For untold numbers of homeowners, Andersen’s commercial launch meant an end to the drudgery of storm windows. More important, it was the start of an industry that in the last 70 years has incrementally improved the thermal performance of windows several times over.
Multipane insulating glazing units, or IGUs, combine metallic coatings and inert gas fill in assemblies that make houses more comfortable and lower heating and cooling costs. By tweaking the characteristics of low-emissivity (low-e) coatings and applying them selectively, glassmakers can customize IGUs for specific needs and climates. But, even with the best coatings and gases, glassmakers are fighting an uphill battle.
The best glazing makes a poor insulator when compared to the exterior walls of a high-performance house. Walls in an energy-efficient home might be rated at R-40, for example, while the high-quality triple-pane windows might have a U-factor of 0.15, the equivalent of just R-6.6. The 2018 International Energy Conservation Code calls for a minimum U-factor of only 0.32—roughly R-3—for windows in even the coldest parts of the country.
At the same time, work continues on new technologies that could make better windows more widely available. Innovations include triple-pane designs with an ultrathin center pane, suspended-film units with as many as eight internal layers and a center-of-glass insulating potential of more than R-19, and vacuum insulating units nearly as thin as a single pane of glass.
What low-e coatings did
For all of the benefits of Andersen’s welded insulating glass, it had some limitations. The introduction of low-e coatings in 1982 was the next big step forward. Exact formulations of these coatings vary by manufacturer, says Steve Urich, director of programs for the National Fenestration Rating Council, but they all are microscopically thin layers of metal that reflect radiant energy back to its source—either inside or outside the window.
There are two methods of applying the coatings, called hard coats and soft coats. Hard-coat applications (also called pyrolytic coatings) date from the late-1990s and are still in use. The coating is applied to the surface of the glass as the glass is manufactured—it’s essentially baked into the surface. It can’t be scraped off. Soft coats, also called sputter coats, are applied in vacuum deposition chambers. They are not as robust as hard coats and can’t be exposed to the air, so manufacturers apply them only to surfaces that will be sealed. When a low-e coat is applied to the surface facing the room, it will be a hard coat. Soft coats are more effective at controlling solar heat. Emissivity coefficients may dip all the way to 0.015, meaning that more than 98% of the radiant energy is reflected, says Jim Larsen, director of technology marketing at Cardinal Glass.
Manufacturers have become increasingly adept at manipulating low-e coatings to control the amount of heat and light that pass through the glass, despite the inherent difficulties of applying uniform layers of metal only 2500 nanometers thick. Larsen says that in multicoat low-e coatings, anti-reflective and silver layers limit solar heat gain (infrared light) while maintaining as much visual light as possible.
“We’re playing with the physics of light,” Larsen says. “These are precision optical filters, and the individual layer thicknesses are critical toward maintaining first and foremost the color balances of the coating.”
The constituent parts of the low-e coating are only one factor. Another is where they are applied. Low-e coatings reflect radiant energy back to its source. In this way, if the exterior surface of the glass is coated, radiant energy from the sun will be reflected back to the outside, minimizing heat gains inside the window and inside the house. Likewise, a low-e coating applied to the room-facing side of a multipane unit will reflect radiant energy generated inside the house back inside. In winter, this characteristic will help the house retain heat.
From double to triple pane
Advanced low-e coatings steadily dropped the U-factor in IGUs, from the 0.6 or 0.65 for the original Andersen panels to 0.35 in the early 1980s. It was the addition of argon, an inert gas, later in the 1980s that gave glassmakers another tool to work with and helped bring U-factors down to about 0.3. Heavier than air, argon better resists the convective currents inside the sealed center of the window. Argon also has lower conductivity than air, reducing conduction and improving the center-of-glass thermal performance by about 20%, Larsen says.
With it, manufacturers pushed the double-pane window to its full potential. It consisted of two panes of 1⁄8-in. glass, a 1⁄2-in. space filled with argon, and an added low-e coating on the room side of the glass. U-factors dropped to about 0.25 or lower.
Triple-glazed windows were the next jump up. The conventional assembly is three pieces of 1⁄8-in. glass and two 1⁄2-in. spaces, a low-e coating in each cavity. The additional gas and ability to play with low-e coatings on more surfaces increases performance considerably. The downside is that the window is often too heavy for common double-hung window sashes that slide up and down. The glazing is 50% heavier than a double-pane and 1-3⁄8-in. thick. These IGUs won’t fit in the 3⁄4-in.
glazing pocket in a standard window frame.
On to suspended film
This unfortunate reality pushed manufacturers toward windows that substitute a thin polymer sheet for the interior layer of glass—the suspended-film window. Southwall Technologies became the face of this industry with its Heat Mirror film, making it possible to produce triple- or even quad-paned windows of the same weight as double-paned glass units. But the window units were susceptible to leaky seals at the perimeter of the glazing that allowed insulating gases to escape and moisture to get inside. Seal failures in windows manufactured by Hurd became a widely publicized nightmare for the industry. Yet Heat Mirror film, now owned by Eastman Chemical, remains a viable option in multipaned windows and is still in use by manufacturers such as Alpen High Performance Products.
“The whole industry really got a black eye that led some fabricators away from suspended film,” Alpen CEO Brad Begin says of the Hurd debacle. “It’s not that difficult a process, but if you do it poorly or don’t pay attention to quality, like any window, any IG of any sort, you’re doomed to a high level of premature failures in the field.”
Today, Heat Mirror film is made by a joint venture of DuPont and Teijin, then shipped to Eastman where it gets a low-e coating in a vapor deposition chamber, and then sent on to manufacturers to be turned into IGUs. Once the film and glass layers are assembled, the units are put into ovens and baked at 205°F for 45 minutes, Begin says. The film shrinks and tensions itself around the spacers at the units’ ends, becoming essentially invisible.
As long as the seal holds, the window unit should be problem-free. Despite lingering doubts over suspended-film IGUs, Begin says Alpen provided 13,000 units for a project at the Empire State Building in New York City nine years ago and has yet to receive a report of a single failure.
Newer glazing designs also allowed manufacturers to begin using krypton, another inert gas with better insulating properties than argon. Its optimal gap is 7 mm (about 1⁄4 in.), half that of argon, according to Dr. Charlie Curcija, a researcher at the Lawrence Berkeley National Laboratory. Krypton isn’t ideally suited to IGUs with a 1⁄2-in. gap between panes of glass, but it has proved useful in glazing where internal spacing between panes of glass or suspended film is less than that.
Kensington is among the companies that sell suspended-film windows, offering krypton-filled Heat Mirror units with center-of-glass R-values as high as R-10. No company, however, has embraced the suspended-film technology as completely as LiteZone Glass Inc., a Canadian startup that sells an IGU with a center-of-glass R-value of 19.6. How? by making the units up to 7.6 in. thick.
Greg Clarahan, the company’s CEO, says the IGUs have been in development for the last five years and went into production in November 2019. The company, he says, had two objectives: to make IGUs with “extraordinarily high” insulating values, and to make them robust enough to last the life of the building. Designers embraced the need for a thicker glass unit in order to increase thermal performance at the vulnerable edge of the IGU.
“The thickness of the glass unit is key to improving the overall window thermal performance and giving you a more uniform temperature on the inside of the glass, and a more uniform thermal transmission through the whole assembly, including the edge and the frame,” Clarahan says.
Thicker IGUs, however, presented a problem. The thickest unit LiteZone makes has eight suspended films between two sheets of glass. If all of those spaces were sealed, it would create a pressure differential problem, so LiteZone designed the unit with what Clarahan calls a “pressure equalization conduit.” It’s a small breather tube that equalizes air pressure in all of the chambers with air outside the unit. Dessicant chambers built inside the tube keep water vapor from collecting inside the units, Clarahan says, and should be effective for at least 60 years.
The company added one more feature. Instead of using heat to shrink the film inside the unit, they devised a spacer for the edge of the unit, which keeps the film in suspension with tiny springs. Because the film is not heated, it’s subjected to less stress, says Clarahan. The windows also show excellent sound attenuation.
The cost of thin triples is falling
Suspended films are one way of reducing the weight of multiple-pane IGUs. Curcija describes another, called the “thin triple,” that is getting a lot of attention in the industry. It consists of an ultrathin glass layer between 0.7 mm and 1.1 mm thick (0.027 in. and 0.04 in.) between two outer layers of 3-mm glass (0.118 in.). With krypton fill, the unit fits in a 3⁄4-in.-wide glazing pocket—the same as a conventional double-pane unit.
Thin triples are just beginning to get a toehold in the U.S. and now have less than a 1% market share, Curcija says. When first commercialized a dozen years ago, these units faced a steep uphill battle for market acceptance because they weren’t cheap to make. Only Corning produced the superthin glass the design hinged on, and it cost $8 to $10 per sq. ft. Plus, krypton was expensive, on the order of 100 times the cost of argon.
In the last five years, two things have happened, according to Curcija. First, other glass companies started floating the thin glass, using the conventional process by which standard window glass is made on a bed of molten tin. That reduced the cost to about 50 cents per sq. ft, on a par with regular glass. The surge of interest in LED lighting prompted a rise in the production of xenon gas, and it turns out that krypton is a byproduct of the process. Krypton is now about one-quarter the price it used to be, and the overall premium for a thin triple is about $2 per sq. ft. over a conventional double-glazed IGU.
“With a thin triple, you can go up to R-10,” Curcija says, “and so if you consider a $2 per sq. ft. premium, that’s a big jump from R-4 at a reasonable cost.” For this reason, Curcija expects commercial interest in thin-triple IGUs to rise. Already, Andersen has adopted it for its commercial Renewal line of windows. Ply Gem, the largest window manufacturer in the U.S., also appears interested. Even Alpen, which continues to promote the benefits of suspended-film windows, sees potential advantages with thin-triple units.
Mark Montgomery, senior vice president of marketing for U.S. windows at Ply Gem, says the company currently makes 1-in. and 7⁄8-in. triples. “We are experimenting with the 3⁄4-in.
dimension referred to as ‘thin triple,’” he writes in an email. “But [we] can currently meet higher performance levels today.”
Don’t look for a wholesale conversion to the thin triple anytime soon. But Begin says the thin glass center layer is easier to work with than a suspended film, has the potential to speed up production, and permits the use of warm-edge spacers instead of the stronger stainless-steel spacers that some suspended-film IGUs need.
This last point is crucial. Suspended films shrunk in an oven exert a sizeable pull on the perimeter spacers that can destroy the seals, but the thin glass doesn’t have to be stretched, creating fewer problems.
“At the end of the day, both technologies provide kind of the same thing,” Curcija says, “but in terms of durability and quality, glass is better than thin film.”
Larsen, however, paints a much less rosy picture of the thin triple. Cardinal is making some of these IGUs, but they cost about twice as much as a conventional triple and the very thin glass in the center of the assembly has a high breakage rate. That’s pushed Cardinal to using a 1.6-mm center layer instead.
“This thin-glass concept is half strength,” Larsen says. “Would you buy half-strength glass and expect to use it at the same size you would double-strength? No. Just our handling breakage rates are way higher.”
Thin triples face other hurdles, he added. A big one is that the thin glass is too thin to be tempered, a heat treatment that increases strength. Tempered glass is a big part of the market—40% of all IGU sales for Cardinal.
Finally, there’s the issue of the krypton gas fill. Larsen says the cost estimates from Lawrence Berkeley Labs are unrealistically low, and the industry in general already does a poor job of getting enough gas into IGUs. To be effective, 90% of the sealed interior space should be filled with gas, but standard practice in the industry is focused on production speed, not actual results, and gas fills in products on the market may be as low as 20%.
“There’s a whole lot of interest in it,” Larsen says of the thin triple. “What happens if you only get 20% krypton fill level on these windows? Instead of it being an R-8 piece of glass, it’s an R-4 piece of glass. It’s the same thing you had with a double-pane low-e. You haven’t gained anything.”
Work continues on vacuum insulation
Argon and krypton both are better insulators than air, but no infill gas at all—a vacuum—would be a big step up in thermal efficiency with an R-value potential of 10 to 14 (U-factor from 0.1 to 0.07) in a unit as thin as a single-pane glazing, Curcija says.
Vacuum insulated glass (VIG) units are already being produced by a Japanese manufacturer called Nippon Sheet Glass (NSG). Chinese manufacturers and Guardian Glass in the U.S. also have started to make R-10 VIG units, according to Curcija. (We attempted to reach Guardian, but did not get a reply.)
There are technical challenges. For one, a completely evacuated core would pull the two outer layers of glass together. To prevent that, manufacturers insert tiny spacers between the glass so the layers don’t collapse into each other. These tiny pillars spaced 1 in. to 2 in. apart create a space of some 50 microns and are visible as a faint matrix if you look closely enough.
Manufacturers also wrestle with how to create a completely reliable edge seal. If that fails, the vacuum fails and the window is essentially junk. Curcija says the units can be sealed around the edges with molten glass, rather than the tapes or adhesives used on gas-filled IGUs. The trick is developing compounds that are soft enough to fuse at temperatures that don’t destroy the low-e coatings on the glass. With heat transfer across the unit limited to the pillars separating the two sheets of glass, R-values up to 20 should be possible.
Equipment for making VIG units is expensive, and the process isn’t as fast as it is for producing regular glazing, Curcija says. Despite the potential advantages for new technologies like these, a fundamental resistance to stricter energy and building codes in the building industry will slow progress.
VIG units are a potential game-changer when it comes to U-factors, says Larsen, but one problem window manufacturers will have to overcome is heat loss at the edge of the window. If the VIG can be buried in a more robust frame with better thermal properties, they would be a step forward, but they will never be a drop-in replacement for the industry-standard double-pane, gas-filled low-e unit.
An NSG subsidiary, Pilkington produces a line of VIG units called Spacia that have been used in both residential and commercial applications in the U.S., says Kyle Sword, manager of business development for Pilkington North America. Units are available in a number of configurations, including one just 1⁄4 in. thick. They consist of an outer layer of low-e glass, a 0.2-mm vacuum space, and an inner layer of clear float glass. Spacers 0.5 mm in diameter hold the two sheets of glass apart. The Super Spacia version is 10.2 mm (about 0.40 in.) thick and has a center-of-glass U-factor of 0.11 (R-9).
“The majority of the sales of our VIG units have gone into existing buildings,” Sword wrote in an email. “Much of this is for commercial, but we’ve done a wide variety of residential buildings as well. The product is commercially available and ordered to custom size.” Sword says a company called Heirloom Windows uses the vacuum units in the windows it produces, which are designed to look like original windows in historical buildings. “I’ve talked to quite a few residential window companies that could use our product,” Sword wrote. “However, most residential window companies today currently use IGUs about 1 in. thick, so their window designs and extrusions are set up to accommodate a thicker window.”
Sword says the cost of a VIG is roughly $14 to $15 per sq. ft., compared with the $8 to $10 per sq. ft. for a standard 1-in.-thick IGU.
Cost keeps new tech out of reach
Another possibility is making windows with aerogel, a type of material invented in 1931 that is made by extracting the liquid in a gel and replacing it with a gas. The result is a nearly weightless solid with very high R-values. Its application in glazing holds promise, Larsen says, with the potential to deliver better thermal performance than a triple-pane or vacuum IGU. The problem is its optical qualities—it’s not completely transparent.
There are even more promising technologies on the horizon, but they all share one stumbling block: higher cost. Without more stringent energy codes requiring better performance, some technologies will remain out of reach for the time being. “We’ve worked closely with a number of companies that are working with new glass technologies,” Montgomery says—“coatings, thermo/photo/electrochomic as well as [vacuum insulated glass]. While all of these enhance the performance of the window, the current cost structure will limit the adoption in the residential market.”
Consider the glazing
The thermal performance of an IGU and a complete window are not the same. This article focuses on IGUs, but often when you compare performance ratings for windows, particularly on the National Fenestration Rating Council’s stickers and manufacturers’ websites, you’ll find a “whole window” rating that considers the performance of the IGU and the window frame as a unit. Whole-window performance is invariably lower than the center-of-glass rating of an IGU. Here are three terms you’ll need to know to understand both the performance of an IGU and a complete window:
U-factor A measurement of the rate at which heat is transmitted through a material. U-factor is the reciprocal of the R-value—to get the R-value equivalent, divide 1 by the U-factor. Lower U-factors mean a higher resistance to heat flow and better thermal performance. A low U-factor is always desirable.
Solar Heat Gain Coefficient (SHGC) The fraction of solar radiation that passes through the glazing. The SHGC is a number between 0 (no transmission) to 1 (unrestricted transmission). Windows with low SHGCs are recommended for hot, sunny parts of the country to keep heat out of houses and lower cooling costs.
Visual transmittance (VT) The fraction of visible light that gets through the glass, also a number between 0 and 1 with higher numbers representing greater light transmission. This rating is often surprisingly low, but that’s because whole-window ratings include the frame.
Where do you want the Low-e Coatings?
When the sun shines through your windows, the light warms surfaces inside the house, and the indoor temperature rises. On a cold winter day in Maine, that’s a good thing. On a hot summer day in Texas, not so much. Windows with a low solar heat gain coefficient (SHGC) help to minimize heat transfer through the IGU. One way that manufacturers create low SHGCs is with low-e coatings. These transparent metallic coatings are designed to block UV light, allow visible light to pass, and control infrared heat appropriately for a house and its climate. This is not only a matter of using the right type of low-e coating, but also where it is applied. While there is no standard for where the low-e coatings are applied and it varies between manufacturers and types of coating, below are common examples.
Cooling climates The best way to minimize solar heat gain through windows is to shade them with overhangs and other shading devices. In hotter climates, it’s also a good idea to choose windows with a low SHGC achieved with low-e coatings. Windows for cooling climates often have the low-e coatings on the inner surfaces of the outer glass—surface two in double-pane windows and surfaces two and four in triple-pane windows. |
Heating climates If your house is in a colder part of the country and you hope to provide some of your winter heating though passive solar heat gain, you want the low-e coatings on the outer surfaces of the inner glass (surface three on a double-pane window and surfaces three and five on a triple-pane window). Choosing windows with the coatings in this location will not only allow more solar heat gain, but the windows will also help prevent radiant heat loss from inside the house. |
Triple panes
Have double the insulating gas. A standard double-pane IGU has two panes of 1⁄8-in. glass, an argon-filled 1⁄2-in. air space, and a low-e coating on at least one surface. To improve on the performance of double-pane windows, manufacturers added another piece of glass, which created an additional cavity for insulating gas. A standard triple-pane window has three pieces of 1⁄8-in. glass, two 1⁄2-in. gas-filled spaces, and a low-e coating in each cavity. Here are three examples of triple-pane windows from domestic manufacturers. U-factors and SHGCs are whole-window ratings.
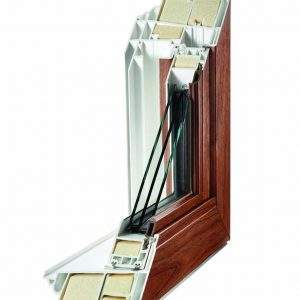
Eco with options.
The ecoSmart window from Great Lakes Window (a Ply Gem company) includes polyurethane-foam insulation in the PVC frame. The window can be ordered with double- or triple-pane glass and argon or krypton gas. Additional options include low-e coatings and a film coating called Easy-Clean. U-factors range from 0.14 to 0.20, and SHGCs run from 0.14 to 0.25.
From forest to fenestration.
Sierra Pacific Windows is a vertically integrated company. The extruded-aluminum-clad exterior covers a wood frame of ponderosa pine or Douglas fir that comes from its own Sustainable Forestry Initiative woodlands, according to the company. The Aspen unit shown here, with a 2-1⁄4-in.-thick sash, supports a 1-3⁄8-in.-thick triple-pane IGU. U-values range from 0.13 to 0.18 and SHGCs range from 0.16 to 0.36.
Making a double-hung work.
Marvin’s Ultimate Double Hung G2 window has an extruded aluminum exterior and an unfinished pine interior. The exterior finish on this window is a high-performance PVDF fluoropolymer paint, shown here in Cascade Blue. The triple-glazed sash is argon- or air-filled with U-factors as low as 0.25 and SHGCs ranging from 0.25 to 0.28.
Suspended film lightens the load
If triple-pane windows have a drawback, it’s the weight of the IGU. Some manufacturers have made triple-pane double-hung windows work, but more often triple-pane IGUs are limited to fixed, casement, and tilt/turn window operation. Suspended films are one of the ways manufacturers have made IGUs with triple-pane performance at a much lighter weight.
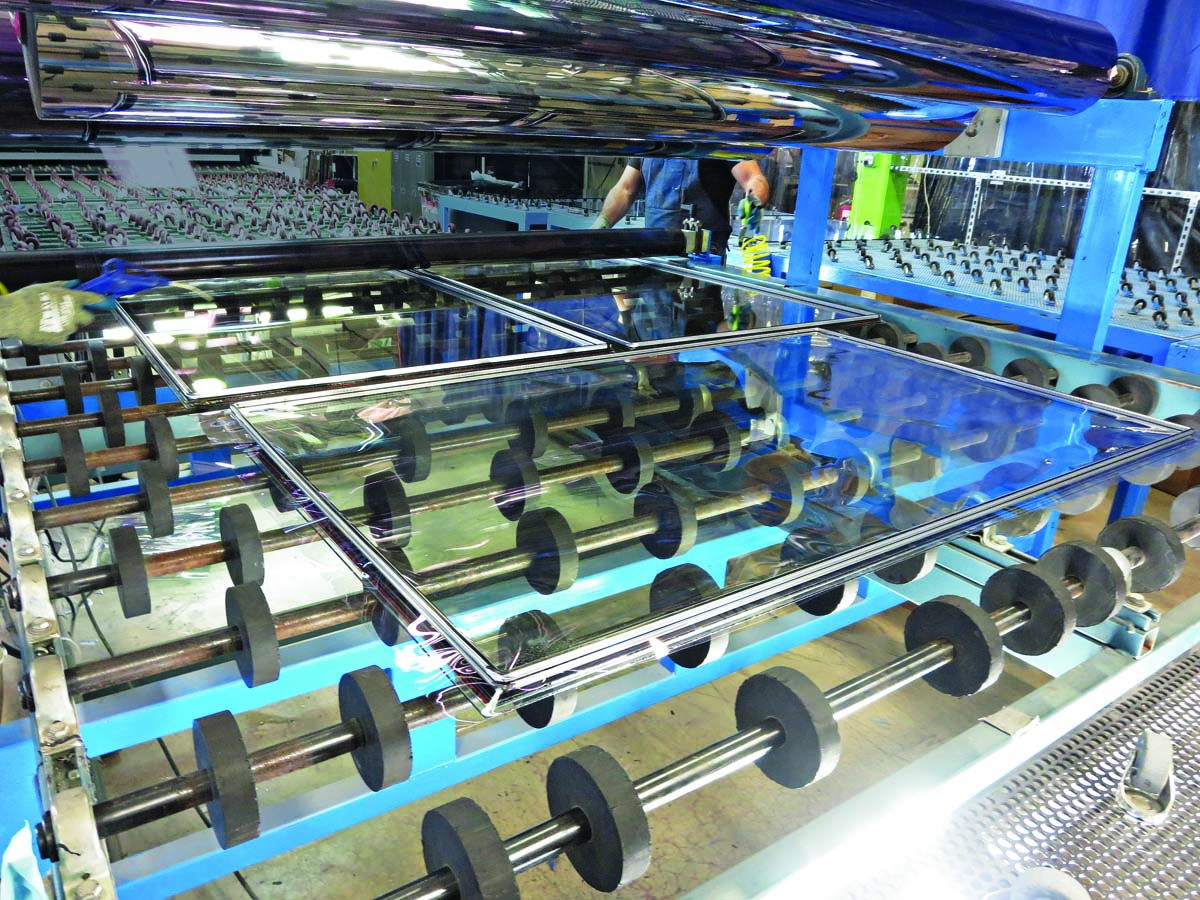
Making Triples Manageable Alpen offers Heat Mirror–film IGUs in configurations with two gas-filled chambers with a 0.16 U-factor and 0.24 to 0.51 SHGC up to configurations with four gas-filled chambers that have a 0.05 U-factor and range from an SHGC of 0.22 to 0.38. Using the film instead of additional pieces of glass reduces weight and bulk.
Pushing the limits LiteZone Glass makes IGUs up to 7-1⁄2 in. thick with as many as eight suspended films. You won’t find glazing like that in a standard double-hung, but in a fixed window, the extra thickness boosts center-of-glass R-values to 19.6. The spaces between the film layers are filled with air and connected with tubes that equalize pressure.
Vacuum-insulated Glass is thin, but complex
The slimmest IGU profile is found on VIG units, or vacuum-insulated-glazing units. A vacuum does a better job insulating an IGU than air or either of the gases commonly used for insulation, and it allows the space between windows to be as small as a couple millimeters. A vacuum also tries to collapse the unit, so these VIG units must be engineered to resist that force.
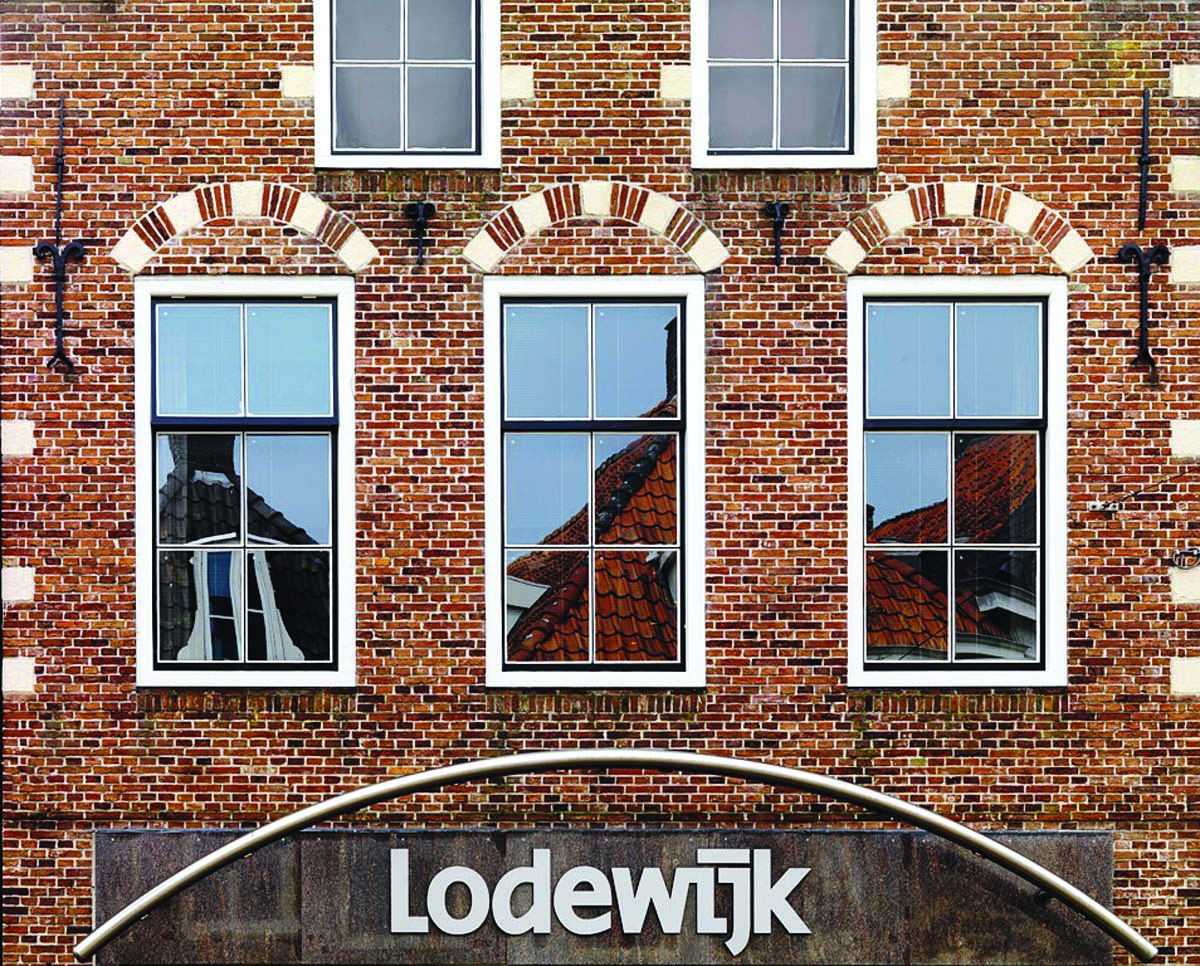
An option for preservation work
Pilkington’s Spacia is a VIG unit that is only 6 mm thick, which is why the company markets it as an option for historical preservation projects. The VIG offers “the thermal performance of conventional double glazing in the same thickness as a single glass pane,” according to company literature. Spacia is available with U-factors from 0.12 to 0.25 and SHGCs from 0.46 to 0.66.
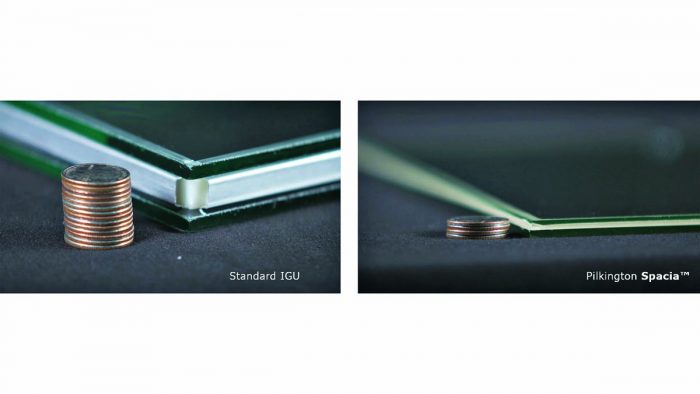
How it works
Pilkington’s VIG unit has an exterior pane of glass where the low-e coatings are applied and an interior pane of clear float glass. To keep the 0.2-mm vacuum space from collapsing, the inner and outer glass is held apart with 1⁄2-mm spacers. A protection cap covers the hole where the air was evacuated from the unit and remains in place for the life of the window.
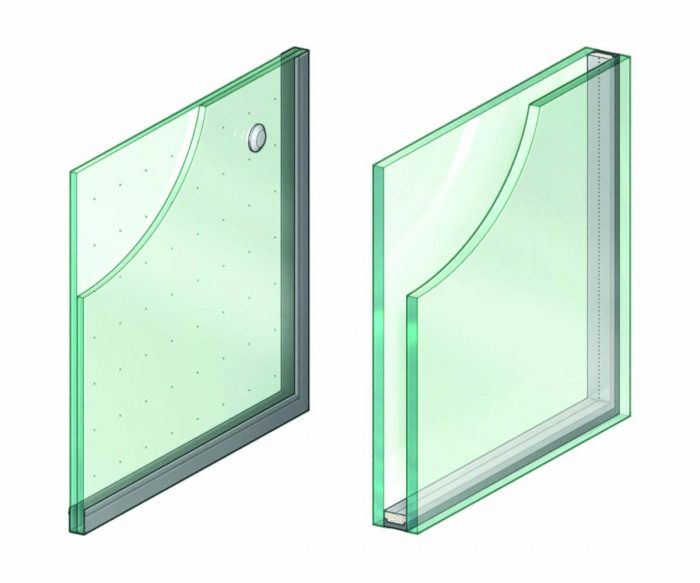
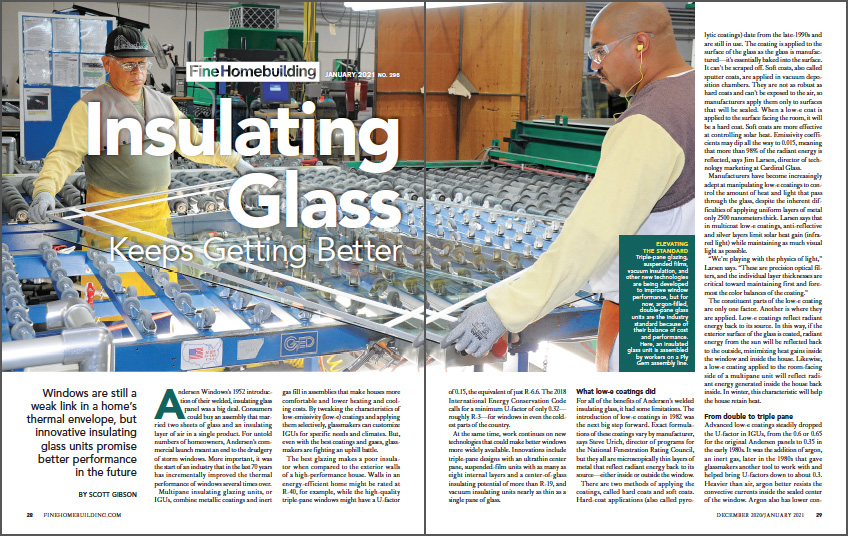
From Fine Homebuilding #296
To read the entire article, please click the View PDF button below.