How To Prevent Spray-Foam Problems
Prep the space, test the equipment, keep the subcontractors happy, and verify coverage to get your money's worth when installing polyurethane foam insulation.
Author Doug Horgan’s full time job is identifying and communicating best practices for construction projects. That’s why we asked him to write a comprehensive guide to executing a spray-foam insulation job—something that has to be done carefully and meticulously in order to keep the job site clean, ensure that the foam adheres to the surfaces you’re applying it to, and make sure it cures properly to create a healthy, well-insulated home.
My job at our remodeling firm is largely to work with our staff and subcontractors to prevent and solve problems with our builds. This includes our insulation work and subs. We’ve used every kind of insulation over the years: fiberglass batts of every type, mineral-wool batts, dense-pack and loose-fill cellulose, blown fiberglass, even dense-packed fiberglass. These materials are safer for workers and homeowners and cost less than spray foam, and they all work perfectly well as insulating materials assuming the assembly is well-built and air-sealed.
But there are times when spray foam is the right choice—for condensation control in unvented roofs, for example, and for a combination of air-sealing and insulation in places like leaky attics and brick foundations. We also turn to foam when we need high insulating value in a small cavity. It works great for all of these things.
The downside of foam is that making it uses a lot of energy, and the common blowing agents used in its formulation are powerful greenhouse gasses. In many cases, the carbon impact of manufacturing the foam chemicals plus the global-warming potential from blowing agents exceeds the carbon saved from insulating. This is a dismal prospect, so we only use it when we have to. In these cases, we’ve had great success using spray foam, but we’ve also encountered a few problems along the way, which taught us the things to look out for. Now we haven’t had a serious problem in years.
Make it easy for the crew
Spray-foam crews arrive with a truck (or trailer) full of materials and equipment. We always leave them the best parking spot; ideally a clean, level spot near a main door. We try to make their setup easier so less of their time and energy goes into logistics and they can do a better job for our clients. If we make them park in the mud far from the house, we have burned any goodwill, and getting great work can be harder.
As the crew is getting set up, we review the materials, areas, directions, and thicknesses with their lead installer. We don’t want them to have to redo work or add foam. Then we leave the job site to them and make sure everyone else is out too. The spray-foam process uses two hazardous chemicals mixed at the sprayer to make the foam, and the air is unsafe to breathe while the foam crew is working. We keep our workers and subs off the job the day of the install, and move renovation clients out for at least 48 hours.
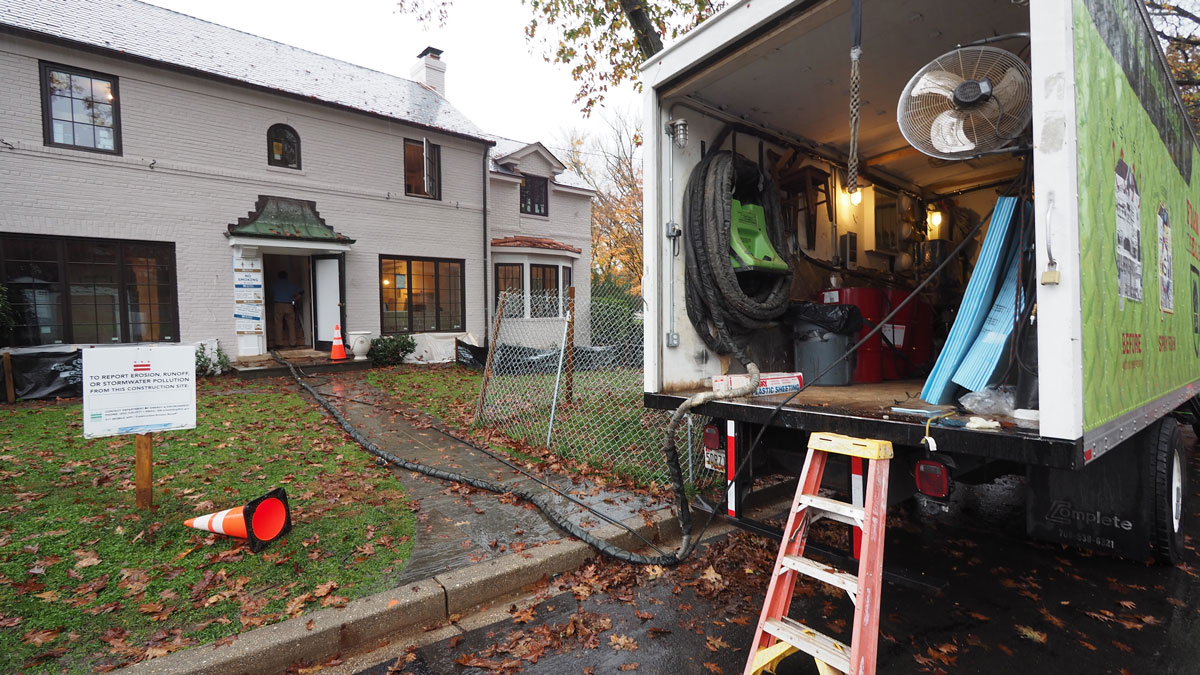
The crew brings their own ventilation fans, eye and skin protection, and air-supplied respirators.
Solid, safe scaffolding is needed for spraying any high areas, because the crew has to get close to the work to do a good job. A framer can climb around a truss system, but a spray tech with a Tyvek suit, full-face respirator, and heavy hose needs better access.
We often do thick layers of closed-cell spray foam. Most closed-cell foams must be sprayed in 1-in. to 2-in. layers (called “lifts”) with a cooling-off period between lifts. The cooling period prevents a dangerous amount of heat buildup within the insulation as the chemicals react, which can start a fire if the installers aren’t careful. Most crews are aware of this hazard, but a few years back we had a close call, so we now make sure everyone knows the fire risks before spraying starts.
To read the entire article, please click the View PDF button below.
RELATED LINKS
Fine Homebuilding Recommended Products
Fine Homebuilding receives a commission for items purchased through links on this site, including Amazon Associates and other affiliate advertising programs.
Staple Gun
Foam Gun
Disposable Suit
View Comments
Keep in mind that the blowing agents used in these chemicals are continually being changed to be more and more environmentally friendly.