Thermal- and Moisture-Control Layers for an Energy-Efficient House
Designer Mike Maines shares tips and tricks for choosing continuous exterior insulation that fits your home's needs.
When installed over an otherwise conventionally framed wall (or a wall built using advanced framing), continuous exterior insulation, also known as insulating sheathing, is a great way to improve whole-wall R-values and to keep the framing and sheathing dry. There are some tricks to choosing size and type of materials, though.
Depending on the situation, I use different wall systems. For low-energy new construction, the builders I work with often prefer either double-stud walls with cellulose insulation, or Larson-truss type outriggers with infill insulation over a standard stud wall. Both can work well, but they have their downsides, including cost, wall thickness, and water-vapor management. Many builders, including Mike Guertin, prefer continuous exterior insulation. Since builders seem to have strong opinions on which wall type they prefer, and I think they can all work fine if designed and detailed well, I worked with Mike to design a durable, efficient wall detail.
The wall is framed with 2x6s 24 in. on center and insulated with fiberglass batts. I have to say that fiberglass batts are rarely my first choice for insulation, but they are readily available and inexpensive, and in the right conditions — installed tightly in an airtight cavity with limited temperature differential across the batts — they can perform as intended. (The common assumption that they should not be compressed is wrong; if you compress them, their R-value per inch increases, up to a point.)
It’s important to have at least one really good air barrier somewhere in the wall assembly. It’s OK to have more than one air barrier, but it’s never OK to have more than one vapor barrier. I prefer to use vapor retarders rather than vapor barriers, as I’ll describe below. Air barriers and vapor barriers (or vapor retarders) can be one product that does double duty, or they can be dedicated layers. For the FHB House, we are using one air barrier and two vapor retarders.
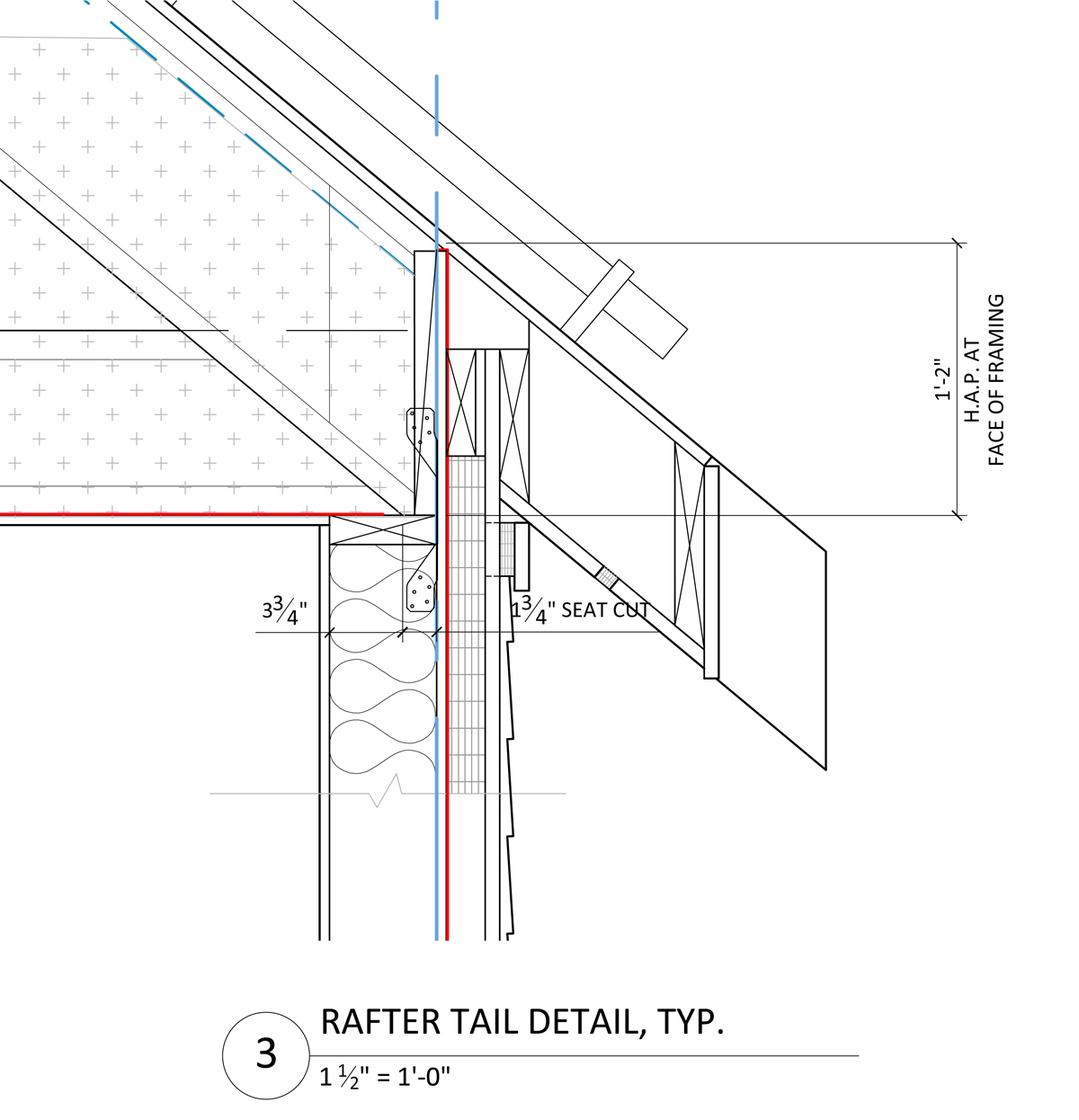
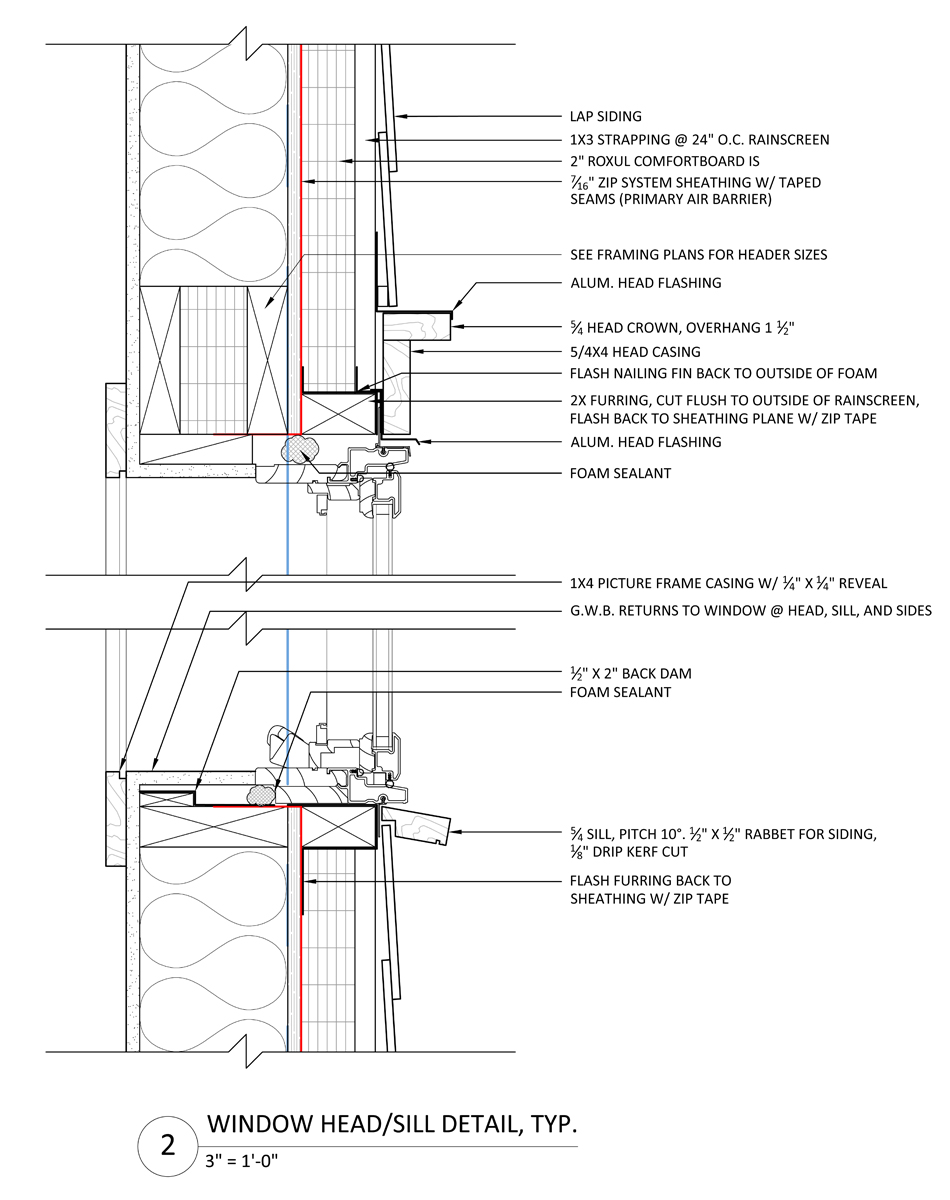
To meet code requirements for limiting vapor transmission by diffusion into the wall in climate zone 5, we needed a Class 1 or Class 2 vapor retarder on the interior, but with at least R-7.5 exterior insulation, code allows a Class 3 vapor retarder. (Class 1 is 0.1 perm or less; Class 2 is from 0.1 to 1.0 perms; Class 3 is from 1.0 to 10.0 perms. Over 10 perms is considered vapor-open.)
CertainTeed is now selling kraft-faced batts with its vapor-variable MemBrain vapor retarder adhered to the kraft paper. The MemBrain normally blocks most water vapor diffusion as a Class 2 vapor retarder, but when the relative humidity reaches about 60% (when bad things can happen), it opens up to be vapor-open, allowing the wall to dry to the interior. With airtight sheathing, vapor movement by diffusion is not considered to be a major issue by prominent building scientists, but the MemBrain gives us insurance. If we needed a functional air barrier at the interior, as some builders try to do with poly sheeting, then MemBrain in sheet form would be a better choice. Because we are using the Zip sheathing as the airtight layer for the walls, we don’t need to worry about the interior of the walls being perfectly airtight, although there would be no harm if it were a second airtight layer. The R-value of fiberglass batts is typically a bit more than that of cellulose and a bit less than mineral wool, but they’re all pretty similar.
For the all-important air barrier, we chose to use Huber’s Zip System oriented strand board (OSB) sheathing. Zip is denser and more airtight than regular OSB (I learned that the hard way on a Passive House project), and Zip’s tape system is now familiar to most contractors. Like other OSB products, though, it is more sensitive to moisture than materials such as plywood or solid lumber. That doesn’t mean it’s a bad product; just that moisture control needs to be considered when using any OSB.
The phenolic coating on Zip sheds liquid water effectively and is open to water vapor. Huber does not publish data for the actual OSB of its sheathing, but standard OSB is usually between 1.0 and 2.0 perms, with some third-party testing finding that Zip is below 1.0 perm. The permeability of OSB and plywood sheathing varies with relative humidity, so it’s hard to pin down. In any case, the Zip panel can be assumed to be borderline between a Class 2 and Class 3 vapor retarder, meaning that it will allow water vapor to pass through, albeit at a slow rate. If the sheathing temperature is below the dew point of the air, the water vapor will condense out of the air and onto the surface of the OSB. Capillary action will then draw the moisture into the OSB.
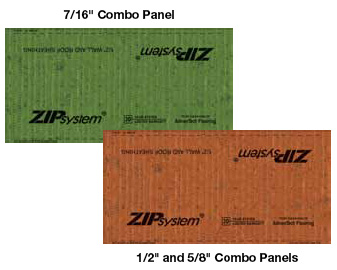
To reduce the chances of the OSB becoming saturated, our main defense is to keep air from flowing through the assembly, which we’ve already covered. The next defense is to keep the sheathing above the dew point by installing continuous exterior insulation. One of the key details of a wall with exterior insulation in climate zones 3 and higher is to make sure the proportion of exterior to interior R-value is high enough to prevent condensation most of the year. The exterior insulation keeps the sheathing warmer than the outdoor air, but insulation slows heat flow in both directions, so the cavity insulation keeps indoor heat from reaching the sheathing.
The 2012 IRC has a handy way to make sure the sheathing stays above the dew point most of the year: table R402.1.1, which shows the minimum R-value of cavity and exterior insulation. For Rhode Island (zone 5), it’s 13 + 5. In other words, minimum R-13 cavity insulation with minimum R-5 exterior insulation. What’s not clear from that table is that if you increase the levels of insulation, it’s very important to keep the proportional relationship the same, or to err on the side of additional exterior insulation. You can’t just keep code-minimum R-5 exterior insulation and bump the cavity insulation up to R-21; if you do, the sheathing will be too cold during a typical winter and condensation will occur.
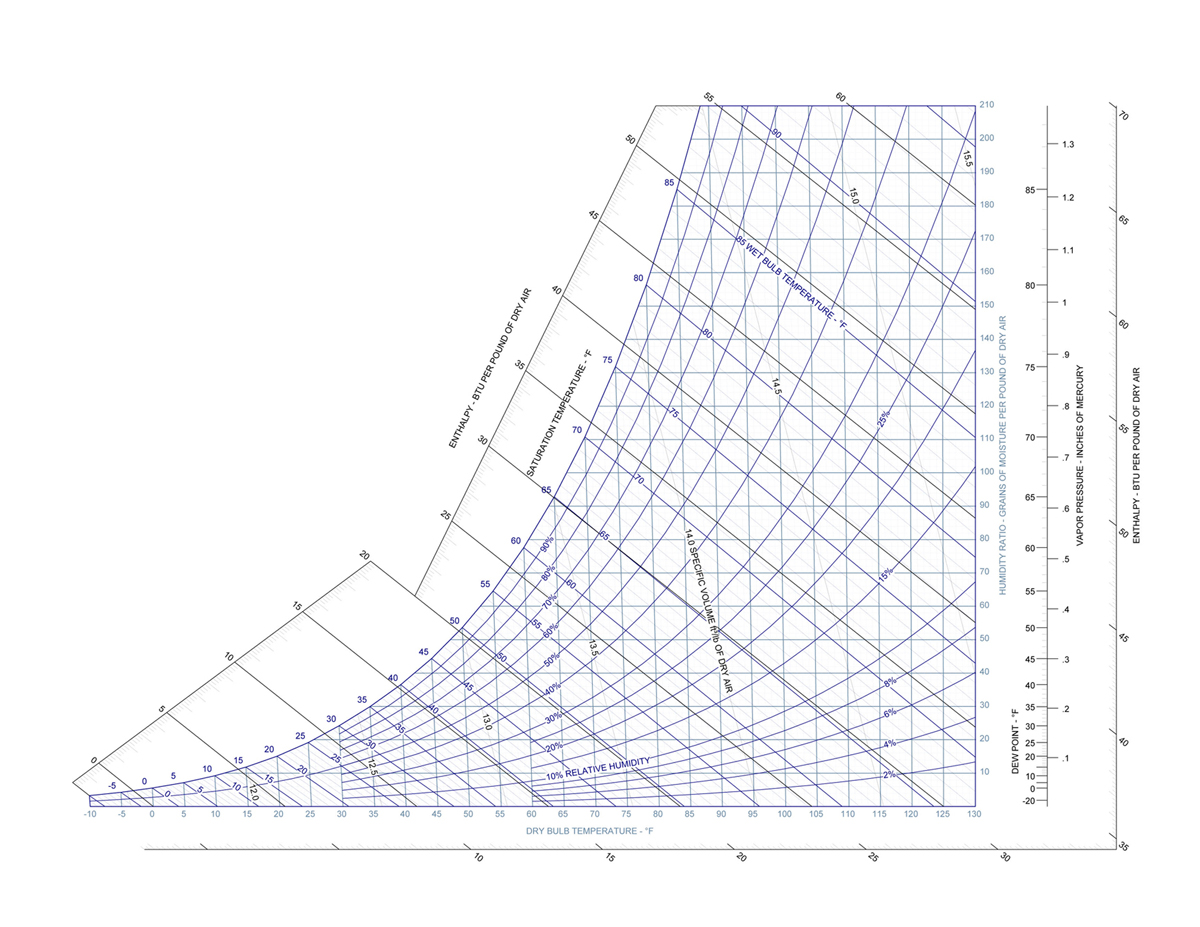
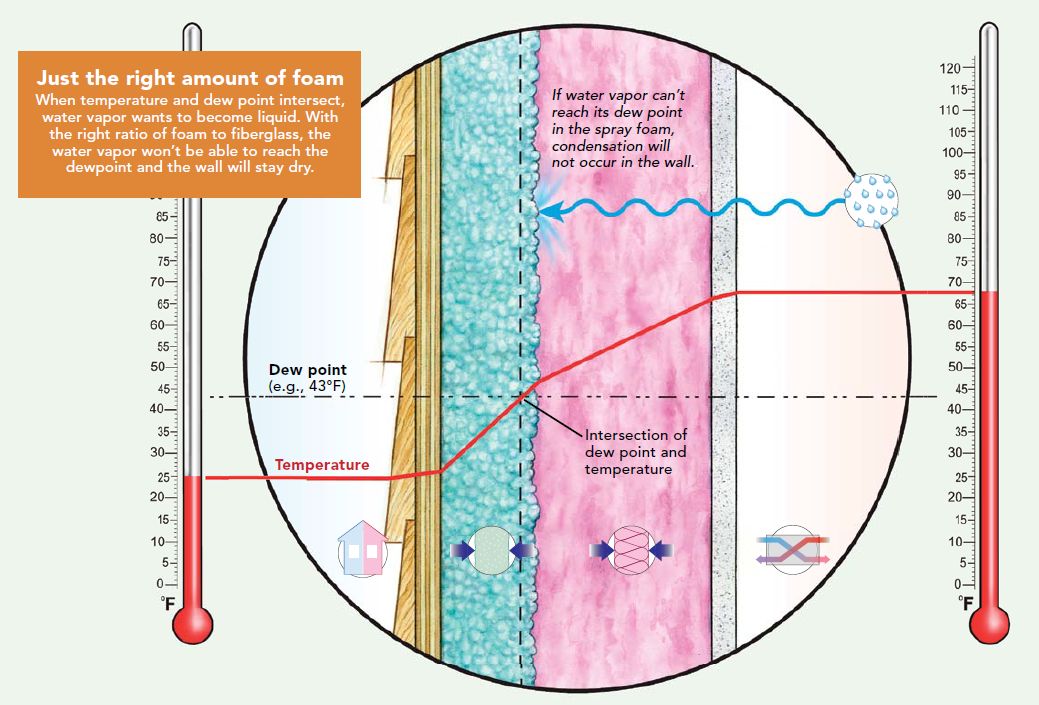
For zone 5, the relationship is 38% exterior to 62% cavity. We have R-21 cavity, which means that we need at least R-8 exterior insulation to control condensation. Table R702.7.1 supports this math, requiring at least R-7.5 for a 2×6 wall if you want to use a Class 3 interior vapor retarder.
We could have installed more exterior insulation; from an energy use point of view, more insulation is always better, but there are diminishing returns. Energy modeling showed that going from 2 in. to 4 in. of exterior insulation would save about 250kwh/yr—less than $40 worth of electricity and less than the annual output of a single PV panel. I have designed Passive Houses with R-40 exterior insulation, so I’m not afraid of using too much, but considering the added expense and hassle of installing thicker rigid insulation, we opted to stick with 2 in. At R-8 for the 2-in. thickness, we meet condensation-control requirements.
With those decisions made, what should we use for exterior insulation? The most common exterior insulation is rigid foam, either XPS (extruded polystyrene) or polyisocyanurate (PIC). A third option is EPS (expanded polystyrene).
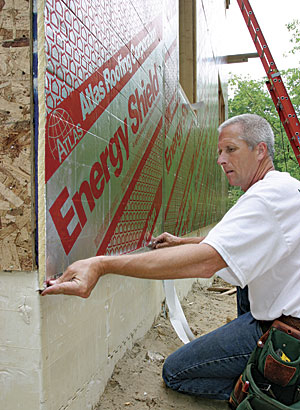
Although my feeling is that foam insulation is probably the best use for oil, in debating what materials to use, I argued strongly against XPS. XPS’s blowing agents are nasty—they stay in the atmosphere, and even though XPS insulation saves energy, in terms of global warming potential, XPS is usually a net loss to the planet (according to research by David White, see (Calculating Global Warming Impact Insulation). Additionally, as XPS ages, its R-value decreases, and at useful thicknesses, it’s fairly effective at blocking the ability of the wall to dry to the exterior. In the plus category, it’s readily available, has decent compressive strength, and is easy to work with. Until the industry changes to the more benign blowing agents used for XPS in Europe, though, it’s always my last choice for insulation.
PIC has fairly benign, pentane-based blowing agents, and it is advertised as having a high R-value per inch, but with its usual foil facing, it is a total vapor barrier. Not only does its R-value decline over time, but it also loses performance as the temperature drops, just when you need it the most.
EPS is vapor semipermeable at thicknesses less than 3 in., it has relatively safe blowing agents and stable R-value, plus it’s generally less expensive than the other options. It can be crumbly to work with, and it shares with XPS a brominated flame retardant that is not safe to ingest, but if I had to choose a foam, my first choice would be EPS. My second choice would be PIC.
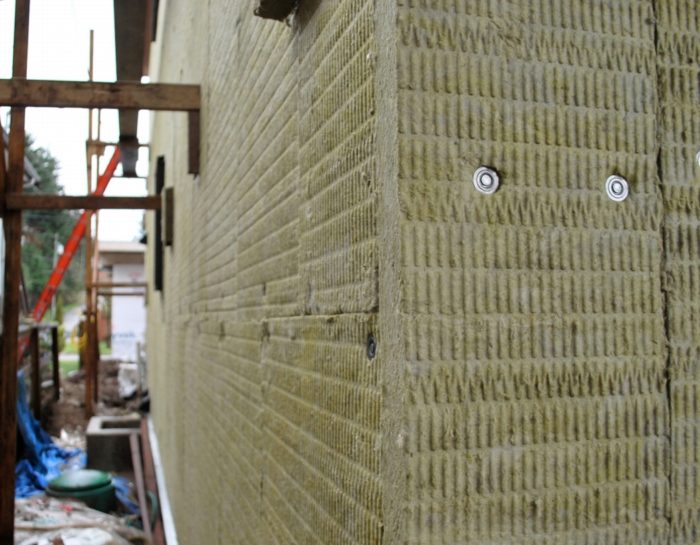
Fortunately, there is an alternative that is good for the house and good for the planet: rigid mineral wool, in the form of Roxul Comfortboard IS. (The IS is for “insulating sheathing.”) It will keep the sheathing warm and dry, and it has low global warming potential and stable R-values. It’s a lot like a wearing a wool coat compared to a rain slicker. It’s a bit of a pain to install compared to the other options, but it’s completely vapor-open. Not only will it allow the occasional raindrop that finds its way past the siding to drain freely, but it will let the wall sheathing dry to the exterior if and when it needs to. Installed with 1x strapping, it makes an excellent ventilated rain screen that is open to air movement at both the top and bottom of the wall. Considering my obsession with managing water and water vapor and my strong desire to build resilient yet energy-efficient homes, I am happy with the FHB House wall assembly.
Note: if you want to learn more about mineral wool, check out these articles: Mineral Wool Makes a Comeback and Detailing Walls with Rigid Foam.
Fine Homebuilding Recommended Products
Fine Homebuilding receives a commission for items purchased through links on this site, including Amazon Associates and other affiliate advertising programs.
Tajima Chalk Rite Chalk Line
Anchor Bolt Marker
Protective Eyewear
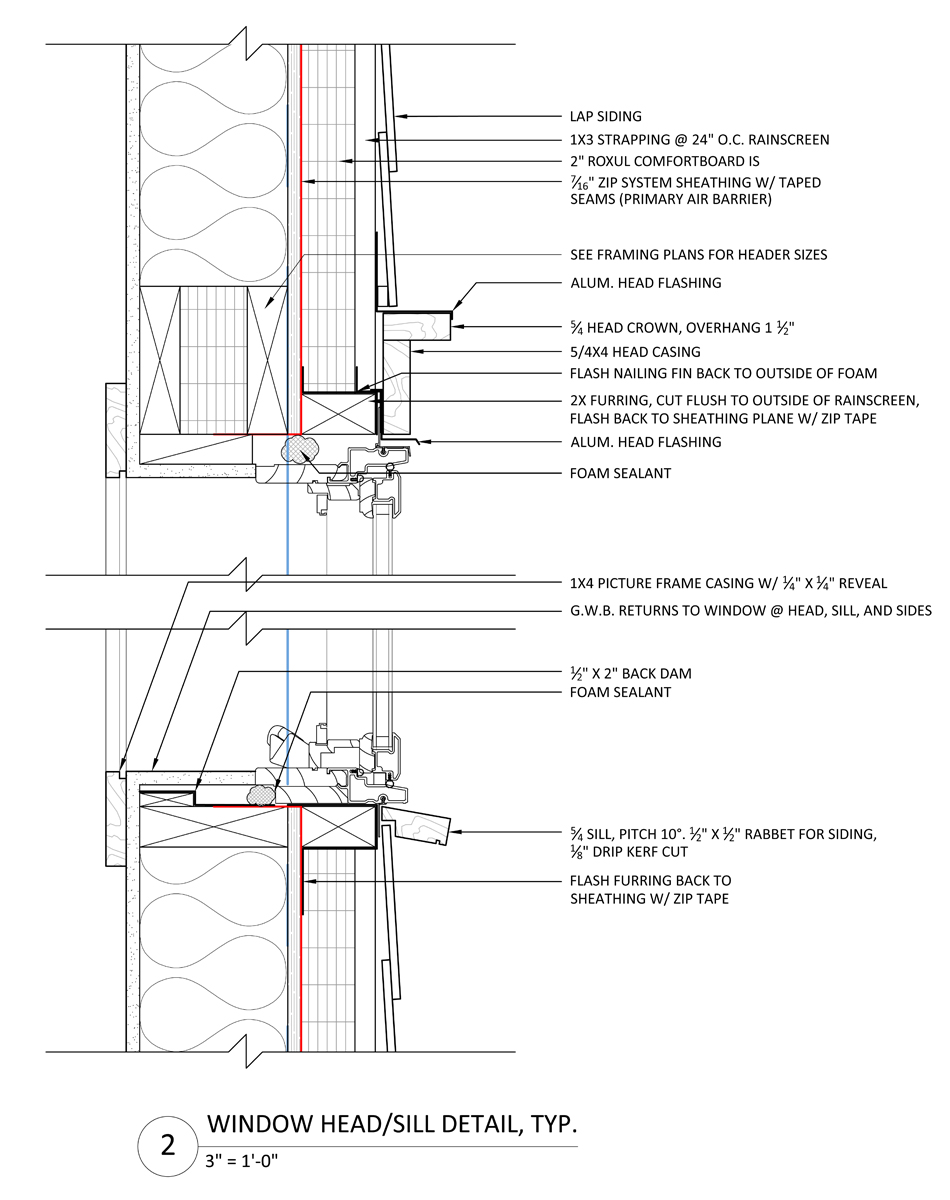
ProHOME construction detail
View Comments
You mention that fiberglass batts are rarely your first choice but go on to say that it was selected because of cost. I've been following these ProHOME posts closely and am curious how many of the products, assemblies, etc. were selected because they represent, in your view, the absolute best practice/products or because they fit this particular project's budget. In the case of the latter, it would be really appreciated by this reader if you could also tell us what the preferred approach would have been if budget weren't a consideration...or at least not the primary consideration. Thanks, Michael
It’s easy for me to answer your question, WinnDesign: if there were no other limiting factors, I would use the Ecocor panelized Passive House system (http://www.ecocor.us/). Their system is the best-built, best-insulated, most airtight, lowest-VOC and most resilient way to build a house I have seen. Full disclosure; it’s no secret that I worked at Ecocor as Operations Manager for a year and a half while they were transitioning from custom site-built homes to their panelized, factory-built system. Even if I hadn’t worked there, I would still hold it as the highest bar in terms of building performance, quality and global impact.
The reality is that there are always other factors involved, including cost, lead times, builder skills, and so on. I’ve designed and built for millionaires and billionaires as well as regular folks, and from what I’ve seen, everyone has a budget, so it’s important to consider both the upfront cost and how performance will affect the cost of ownership over time.
Another factor is who else is on the team. I really do work with builders who prefer different systems; I find it interesting how strongly every builder feels about their preferred method. I work regularly with two different builders who are big fans of double stud construction. As long as they are airtight, insulated with cellulose and have a rain screen, from all reports they perform great. Yet other builders say that it costs too much to frame two walls and that the sheathing is left vulnerable to moisture. The Passive House builders I work with, including a current project that is owner-built, often use conventional wall framing with airtight sheathing and TJI outriggers with a vapor-open WRB membrane and exterior insulation. That seems to be a very good way to reach Passive House levels of performance; I think the PH standard is great and I am a certified Passive House consultant, but I also recognize that there are diminishing returns and that the PH standard may not be right for every situation.
I mentioned that fiberglass is rarely my first choice because I prefer the hygroscopic properties and density of cellulose insulation, and I am lucky to live in an area with a lot of good cellulose installers. Fiberglass has some limitations but so do all materials. Many (or most?) parts of the country don’t have access to good cellulose installers, and many builders are leery of the material. Mineral wool is great in many respects but it’s expensive and heavy compared to fiberglass. Sometimes that matters, sometimes it doesn’t. If you’re hiring professional installers, they get a huge discount on fiberglass that they don’t get with mineral wool, so they can often provide and install fiberglass for about the same price as you can buy the material. To have them install mineral wool is expensive, but if you’re installing your own, it may make more sense. Foam is never my first choice but there are times and places where it’s clearly the right material for the job; in those situations, I compare pros and cons of various properties and the cost and availability of material. Although I don’t like XPS, it’s easy to get and performs ok, so when the builder or I don’t plan ahead properly, sometimes XPS is what ends up getting installed.
I guess the short version is that every project has many variables, and I (like most designers and architects) work with the other parties involved to find the best solution for the situation. I can’t think of anything on the ProHOME, to date or coming up, that is less than the best solution for the situation, all things considered.
You may have noticed in the recent issue that I was not thrilled with using double-glazed windows; I prefer triple-glazed for a few reasons, but the numbers did not pan out for triple glazing on this project, and the fact is that double glazing will work just fine, just not quite as well as triple glazing would have. I will be sure to address the windows in an upcoming blog post. I will continue trying to point out places where a decision was made that may not be what I would have preferred if it was all up to me, and the reasons why we went with the decision we did.
It would be interesting to see a variation of the Canadian REMOTE wall system, using Mineral Wool. I like the REMOTE system as the vapor barrier is at the exterior surface of the sheathing, and all of the insulation is outside of the vapor barrier - which means that no matter which season (or heating and cooling load), the dew point occurs outside the barrier.
I'd be interested in hearing more about the system/steps in the first picture (mineral wool being applied while wall is on deck). Specifically: window detail under mineral wool, type of fasteners (and how evenness is maintained for siding), and what the 2x lumber is for in the bottom right corner of photo (and why no mineral wool?). Seems like a good idea to do this before standing the wall!
Great article expressing th often require balance of budget vs. ideal energy efficiency measures. We have been using the Roxul Comfortboard IS for quite a few years now, on just about every new house we build, and one thing we've discovered is that it is NOT a commodity pricing system. Two layers of 1.25" thick material actually costs quit a bit less than one layer of 2" material, and still yields an additional ½" of insulation! Because the product is so fast to tack to the wall before applying rain screen, the extra labour of installing two layers is more than offset by the cost savings of the less expensive double layer of thinner material.
Tim_Strommen, using mineral wool in a PERSIST arrangement would be interesting. Not to plug them again, but Ecocor has a few different systems, including one that is similar to PERSIST but with all cellulose insulation. Their assemblies are the first outside of Europe to be certified by the International Passive House Association, which was a rigorous process. Another company near me, G•O Logic, is using thick exterior mineral wool as one of their offerings.
bwc, you might have missed Mike Guertin's blog post, which I think will answer some of your questions: https://www.finehomebuilding.com/2016/08/29/exterior-insulation. The attic will have loose-blown insulation on the attic floor (except for a few areas of insulated roof) and we didn't want to waste money putting mineral wool on the gable walls above the attic floor level, so Mike installed thick furring strips instead.
StollerB, that's interesting. I've found rigid mineral wool difficult to get at all in smaller quantities. Even when I wrote this article last year: https://www.finehomebuilding.com/2015/09/16/mineral-wool-makes-a-comeback, I couldn't get any local suppliers to send me just few sheets of Comfortboard, so I had to buy a similar product, Soundboard80, online instead. It was expensive and would not have been worth using on an entire house, but I needed something for the article. Anyway, I hope that rigid mineral wool becomes more popular and more available, instead of having to buy it by the truckload as is the case in many locations now.
Thanks Mike
Because I've read numerous articles and debates about the building strategies you address, I'm sold on the plans you use here. But I wonder when, if ever, the materials you speak of will be available to someone who doesn't wish to become their own distributor. Are there no incentives for building suppliers to try stocking new things, or are manufacturers unwilling to ramp up production until demand increases? It feels to me just like the situation with electric cars. Which comes first, the cars or the charging stations? Meanwhile new construction forges ahead with old ideas and materials that are easy to grab. It's really frustrating to meet people over the counter who have never even heard of any of this.
user-3976312, good question. Speaking for Roxul, the brand of mineral wool we are using on the ProHOME and the one that's most available in the Northeast, from what I understand they have the capacity to make nearly any thickness and any density. I talked to every distributor I could find and many lumberyards, and quite a few didn't even know what product I was talking about, much less have any interest in buying a truckload so they could sell me a few sheets. So I believe that consumer demand is going to have to drive suppliers to stock the product. If you target the most forward-thinking lumberyard in your area and bug them regularly, eventually they will think about carrying it.
The only supplier we have found that will get it for us is the local branch of a national drywall and insulation dealer (Winroc) in Canada. Because they have such a close relationship with Roxul for their typical Comfortbatt and Safe 'n' Sound wall cavity products, they have an easier time coercing Roxul distributors to send them the Comfortboard IS. However, they often bring in hundreds of bundles of the stuff, with the promise from us that we will be spec'ing and using it on future projects, since no other builders are working with it yet. Perhaps the same kind of conversation with your local drywall and insulation suppliers will help you set up that kind of arrangement?
Just curious...are you suggesting compressed fiberglass batts yield a higher r-value per inch? My HERS rater had an anxiety attack when i showed him that passage. and if so, please provide the research or reports that substantiate this claim. would like to forward to my architect.
Many thanks!
You mention the ratio is important to maintain - if one is not able to apply adequate exterior insulation to reach the proper ratio to interior insulation, would it be better to omit exterior insulation all together and just have a good rainscreen to whisk away moisture? In other words, does having some, but not enough exterior insulation run the risk of trapping condensation on the sheathing and creating more of a problem than solving one? Thanks