What’s the Building Code for Housewrap Installation?
For best practice when installing WRBs, follow the IRC.
It’s common in my area to see housewrap installed improperly. Most city and town building inspectors only make four building inspections during the building process: (1) Footings/foundation before placing concrete, (2) Rough framing, after the utilities are roughed in, (3) Insulation / fireblocking / draftstopping, and (4) Final. Friends of mine in parts of Canada tell me that they are required to get a WRB/Window/Door installation inspection done. If we had that here, housewrap installation quality would probably rise significantly.
“It’s just housewrap. Who cares anyway? My siding doesn’t leak.”
Siding jobs do leak so when the water-resistive barrier leaks, water can get into the wall and lead to mold and rot. Often the leak can go on for many years inside the wall before anyone notices. And by the time it is discovered the damage can be extensive.
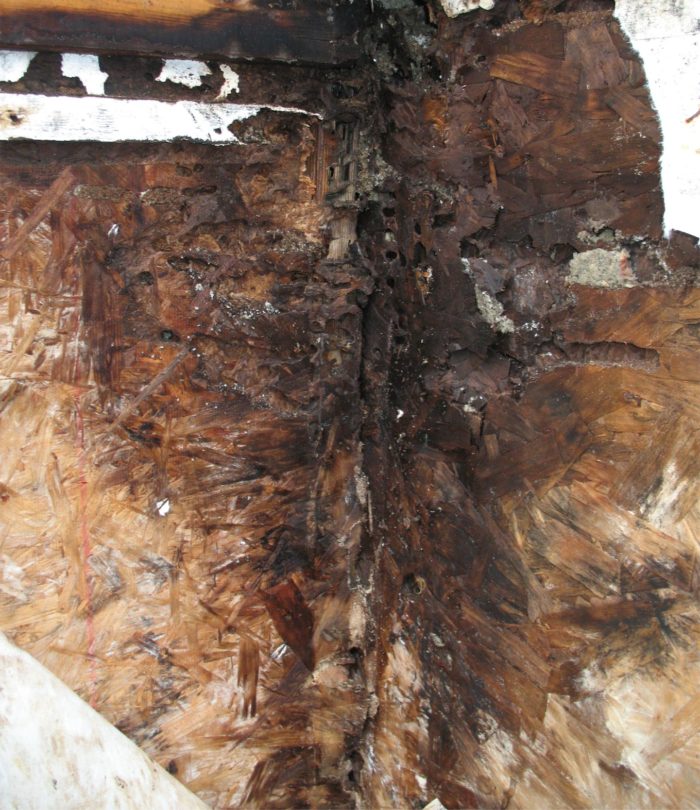
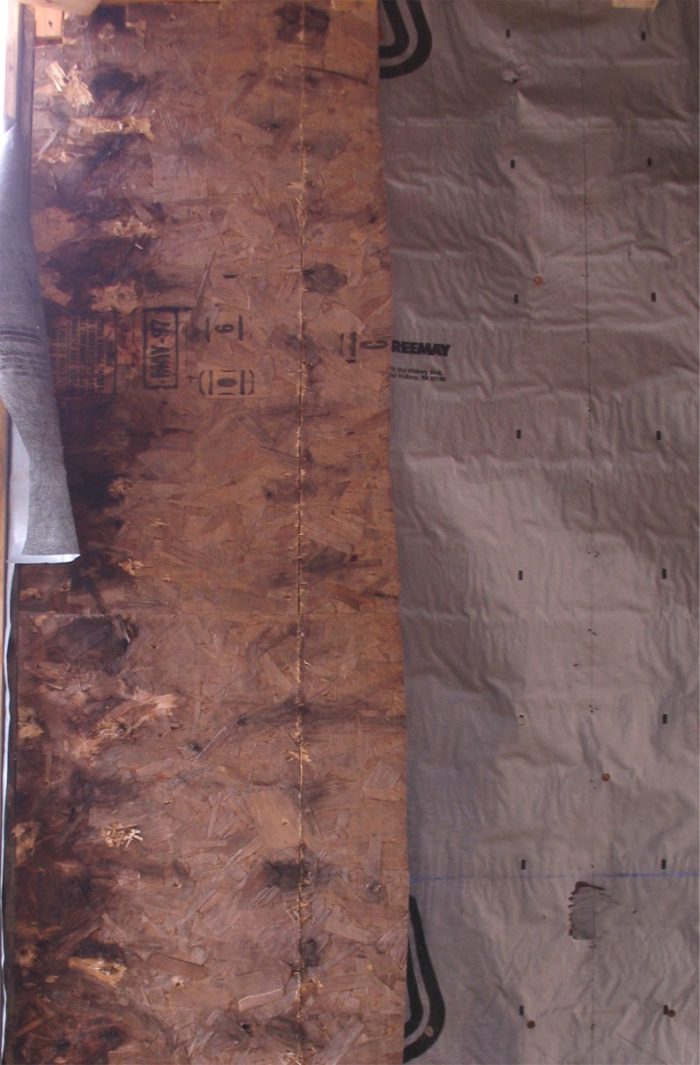
It’s all outlined in the code
Though many builders think of the IRC as a low bar / bare minimum, when it comes to WRB installation the code is actually ‘best practice.’ It’s all in section R703 – Exterior Covering of the 2018 IRC.
R703.1.1 “The exterior wall envelope shall be designed and constructed in a manner that prevents the accumulation of water within the wall assembly by providing a water-resistant barrier behind the exterior cladding … and a means of draining to the exterior water that penetrates the exterior cladding.”
R703.2 Water-resistive barrier
This section gives us two options for materials: #15 lb tar paper meeting ASTM D226 requirements OR “other approved water-resistive barrier” (Meaning: approved by the local building official.) The manufacturers of plastic housewraps and other WRB materials generally obtain an ICC Evaluation Service Report that code officials rely on when determining whether to accept an alternative material to #15 tar paper or not. Though I’ve never heard of a local code official denying approval of a housewrap but it is within his authority.
On the installation side, when tar paper is used it must be “free from holes and breaks,” “applied horizontally,” with laps “not less than 2 inches.” Vertical and other joints must be lapped 6 in. Fastening requirements for the WRB are not mentioned in the IRC. Figuring that tarpaper installation must be “free from holes and breaks,” it’s important to consider the effect of common installation practices like fine wire hammer-tacker staplers. Often the contact rim on a stapler rips a small hole each time the tacker is whacked. Another problem with fine wire staples is they frequently pull-through the WRB on windy days leaving holes that often don’t get patched.
And there are other WRB installation requirements that often gets overlooked “The No. 15 asphalt felt or other approved water-resistive barrier material shall be continuous to the top of walls and terminated at penetrations and building appendages in a manner to meet the requirements of the exterior wall envelope as described in Section R703.1”
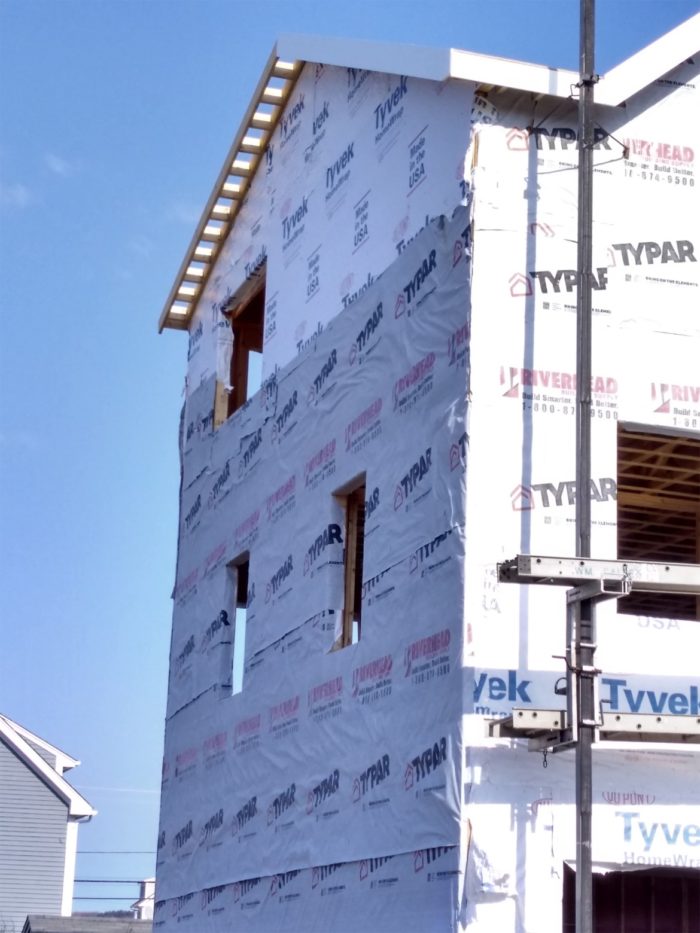
What about housewrap installation?
When “Other approved materials… are used as a WRB they shall be installed in accordance with the water-resistive barrier manufacturer’s installation instructions.” There it is — the manufacturer’s installation instructions are referenced in the code and are enforceable by the local official.
Housewrap manufacturers list their installation requirements in the instructions. I read through several major housewrap manufacturer installation instructions and most have minimum horizontal overlaps of 4 in. or 6 in. and minimum vertical overlaps of 6 in. to 12 in. Most also require or recommend 1 in. plastic or metal cap fasteners. The caps protect the housewrap from damage during installation and spread the surface area of the fastener over a broader area of the WRB so the fastener is less likely to tear through. The fastener spacing patterns vary widely between manufacturers. Some call for fasteners spaced as wide as 32 in. on center vertically and horizontally, others are as close as 12 in. oc in some circumstances.
Fine Homebuilding Recommended Products
Fine Homebuilding receives a commission for items purchased through links on this site, including Amazon Associates and other affiliate advertising programs.
Reliable Crimp Connectors
8067 All-Weather Flashing Tape
Handy Heat Gun
View Comments
In my part of Michigan we have WRB inspections, typically after window installation and before siding. This also means that they have not allowed one manufactures tape or flashing tape on anothers housewrap. For instance, Protecto wrap flashing tape on Tyvek. The reason for this is the housewrap manufacterers instructions call out their own product, not their competitors. The other wrinkle is that when using ZIP sheathing, very few manufactures include instructions for installation on that type of sheathing. I was able to get around it on that particular project by printing instructions off the window manufacturers website and taping them to each window. It's getting down right ridiculous sometimes.
BFRFAB It does sound over the top on the inspection side - especially not permitting cross-use of products between different brands.
When was the WRB requirement introduced? We purchased a home built about 12 years and during a remodel was shocked to discover there was no WRB and no window flashing. Aside from not following basic best practice for the era I was equally surprised the building inspector approved it. I went back to check the IRC requirements and it seemed to me WRB was a recent addition hence at the time of construction it was probably compliant (but poor practice), but I'm not a code expert, just a homeowner who was quite distressed. When did WRB become a requirement?
I had to look back through several versions of the IRC to see when Water-Resistive Barrier (WRB) became required. There was a big change in table R703.4 between the 2003 version and the 2006 version that governed (along with a couple other sections) which siding materials must have a WRB.
For homes built under the 2003 IRC most siding did not require a WRB. Homes built under the 2006 IRC and later versions, most siding is requires a WRB.
In the 2015 IRC the column in table R703.4 was eliminated and most of the exceptions to the required WRB in section (R703.2) describing Water-resistive Barrier were eliminated. The only remaining exception where a WRB is not required is in detached accessory buildings (think garage or shed).
What we think of as a modern window flashing system incorporating a sill pan and flashing applied to the sides and head of windows and doors was not specifically prescribed until the 2012 IRC. The 2012 IRC and subsequent versions require installation follow the window or door manufacturer's flashing instructions or the flashing manufacturer's instructions. Prior to that window and door flashings were required but the details of what would comply were vague or nonexistent.
Local code officials can only enforce what their code jurisdiction (state, county, city/town) permits them to. In some areas the local official is allowed to enforce standards that go above and beyond what is prescribed in the adopted building code. In other areas code officials can only enforce what the adopted building code requires and nothing exceeding that. Sometimes there is room for interpretation in the code but usually the code is pretty clear.
It is likely that the model IRC code in force at the time your house was built 12 years ago was the 2000 or 2003 version. Many jurisdictions don't adopt a new model code for several years after it has been published. So it could be that the local building official enforced the code properly; which, depending on your siding, didn't require a WRB or special flashing around the windows and doors. The 2000 and 2003 versions of the IRC permitted 'self-flashing' windows with 1-1/8 in. wide flanges. No WRB, no sealant, no additional flashing - just the window nailed to the framing or wall sheathing met the code.
While we wouldn't consider your 12 year old house built to the old standards "code compliant" today it is viewed as through the lens of the code at the time it was built. Each new IRC version includes a section for Existing Structures "The legal occupancy of any structure existing on the date of adoption of this code shall be permitted to continue without change". With a couple of exceptions for heath and safety.
FHB posted an excellent article on waterproofing with WRB around windows that seemed to go beyond what this covers. https://www.finehomebuilding.com/2008/07/03/installing-and-flashing-windows-correctly
We don't have a required inspection here in Seattle however most of the A/E I work with require independent inspections for items such as this.
If a house passes inspection when it shouldn't have because the construction didn't meed the code requirements of the time, who is responsible?
I haven't had a house built or had a remodel of an existing house, but when I do in the future, can I expect that there will be a warranty in the contract with the contractor that the construction is built to or exceeding minimal code standards, regardless of whether an inspector "signed off" on it? I have read enough to know that bad things can happen when best-practices aren't followed, but don't know nearly enough to recognize when shortcuts are taken. Do I have to rely on a building inspector to make sure that I get what I paid for?
The building inspector is not responsible for consumer protection with reguard to ensuring that everything the contractor and trade contractors have done on a project completely meet building code. In order to ensure everything is done to the letter of the building code, an inspector would have to inspect each and every operation while they were being conducted - they'd have to be at the jobsite every day someone was working on it. Even when they 'sign off' they are not stating that the builder has completed everything in compliance with the code.
Ultimately it is up to the builder and trade contractors to comply with the building code. Liability varies state by state, county by county. In my state there is case law precedent whereby a contractor can be held reponsible for code violations a decade (and several owners of the property) later. Some places have implied warranties for code compliance and negligence for not following code.
I don't know of any way to ensure that you are getting what you paid for. Best advice is hiring a reputable contractor from the outset.