A Case for Composite Wood Siding
Gone are the days of old-growth timber, but there's still good reason to use wood for siding. Fernando Pagés Ruiz makes a compelling case for the use of engineered wood siding.
Wood is one of the most environmentally benign building products. Not only does it extract carbon during tree growth and then sequester it as lumber, it provides us with a low-polluting, guilt-free renewable resource when extracted from well-managed forests. Unfortunately, in exchange for not cutting old-growth timbers, modern forestry has brought us fast-growth timber with inferior structural characteristics.
Because today’s young timber does not make a lasting siding like the old-growth trees of the past, a large market of wood alternatives like vinyl and fiber cement has taken hold. For those who still prefer wood, manufactures now turn wood chips into the base ingredient of a new generation of engineered cladding, a category that has evolved over the last 20 years, becoming more durable, and in some cases, environmentally responsible. I recently was asked to develop a continuing education course for the American Institute of Architects on wood composite siding, namely LP SmartSide and Kaycan Eco-Side from KWP Engineered Wood Products. The following is a summary of what I included in the class.
A brief history of modern wood siding
We associate the architecture of antiquity with great stone monuments like the Parthenon. Yet the most common material for construction was then, like it is today, wood. Without the benefit of chemical preservatives, these early wooden structures succumbed to biodegradation. Only the important buildings—the temples and coliseums—survived.
If you travel around the United States, visiting old towns just off the highway, you will note a similar pattern, where historical civic buildings and important religious structures employed durable materials, like masonry and stone, while homes and small commercial structures were constructed with wood. Most of these old wood buildings have newer siding.
Siding takes almost as much environmental punishment as a roof does. We all know wood and asphalt roofs have a limited lifespan, shorter than the building’s life. Yet we have gotten used to claddings that guarantee a lifetime of service, with long and transferable warranties. This was not always the case. You can see it in historic towns, such as St. Augustine, Florida, where buildings from the 19th century have 20th-century siding; just look closely at siding profiles.
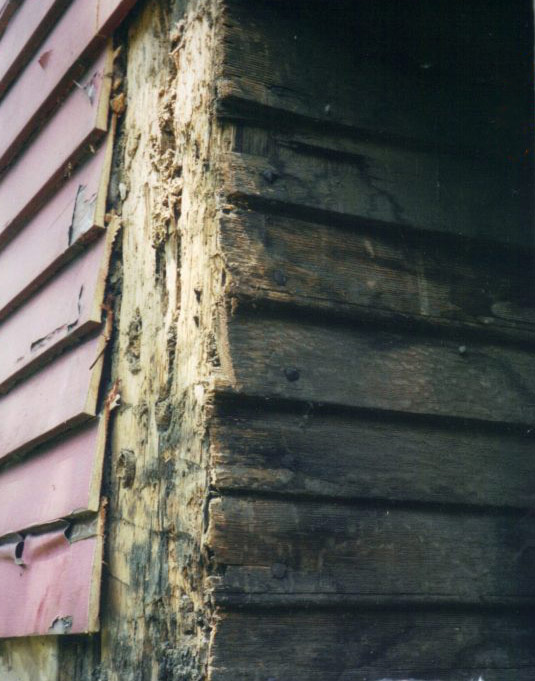
The original American cladding was wood shakes, which were easy to make on-site from locally harvested logs cut into rounds, then split with a froe—a shake ax used to cleave wood by splitting it along the grain. Clapboard siding was also cleaved on-site from smaller-diameter logs, but its length was limited, usually to about 4 ft. You could not split a 16-ft. board by hand. The long, milled siding we now associate with traditional wood claddings became popular in urban areas in the mid to late 1800s with the proliferation of sawmills.
The preservation of wood siding became a matter of science and art, with painters playing the leading role in keeping wood siding from following the course of nature with rapid biodegradation. The best paints for the job were anything but environmentally friendly, containing arsenic and lead to fight off insects and decay.
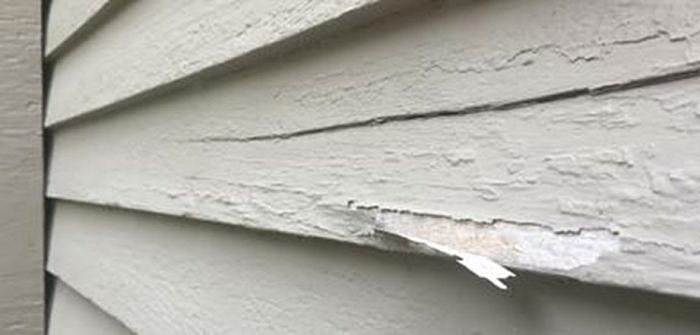
The evolution of siding
Despite having older (better) trees; effective, albeit highly toxic preservatives; and carpenters that knew how to install wood siding properly—three elements we lack today—lumber claddings rotted, and even lead paints blistered and peeled. Scraping off old paint to apply a fresh coat became the typical homeowner’s summer vacation. Consumers didn’t like it. Manufacturers responded with new, industrial claddings made of asbestos (very durable, but we cannot use it anymore), brick-pattern embossed asphalt siding (yuk), aluminum, and polymeric (vinyl) claddings. These products provided exceptional durability with questionable esthetics.
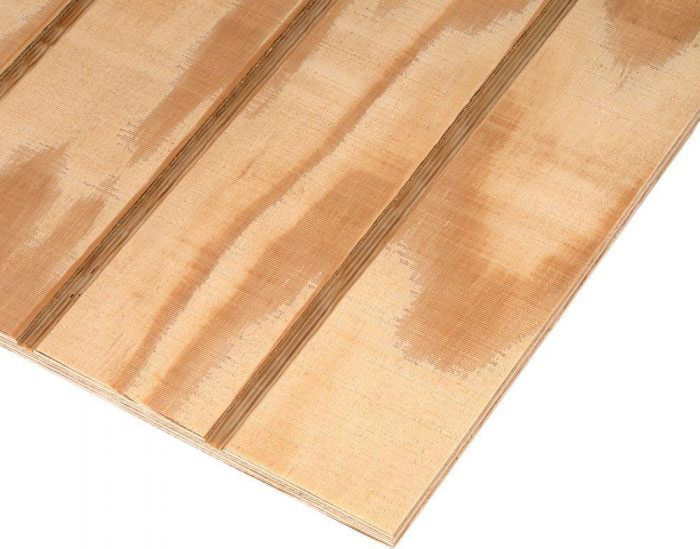
In the mid-1950s, the APA trademarked T1-11, a textured (that’s the “T” part) plywood with grooves cut at an 8-in. or 4-in. pattern, imitating board-and-batten siding. The material provided both lateral bracing and a finished exterior cladding. It became popular for more economical buildings as T1-11 can perform double-duty as siding and shear panel. (I sided my first house with T1-11. I intended to eventually re-side on top of it with a better-looking material. I never did.)
Until the early 1960s, the choices for artificial wood remained limited. The building industry introduced hardboard siding, a composite of wood chips with binders and biocides, such as formaldehyde, designed to provide durability. But during the 1970s, health and safety policies enacted by the Environmental Protection Agency to prohibit the use of formaldehyde in building panels led manufacturers to shutter production. A few reformulated their products without formaldehyde, but these products failed with exposure to household sources of moisture, such as lawn sprinklers. Class action lawsuits ensued.
In time, a very small number manufacturers soldiered on—I know of two—and formulated new wood composites without human toxins, better binders, and applied finishes that have led to a revival in engineered wood cladding products. The leads are LP SmartSide and Kaycan Wood Products (KWP).
Reconstituted wood-fiber siding
Like all engineered wood products, wood composite siding uses wood flakes, shavings, or sawdust as a base, fibrous material, chopped or ground, denatured, and recombined with binders, biocides, and stabilizers. These binders and biocides provide predictable longevity that manufacturers use to issue limited but long-term warranties.
Since fiber cement looms large as a competing siding technology, the manufacturers of wood composites offer more robust warranties; in some cases, decades longer than fiber-cement manufacturers like James Hardie. Since OSHA began to regulate worker exposure to silica dust while tooling fiber-cement siding, manufacturers of wood composites have also emphasized the relative health, safety, and installation-cost benefits of their products. Although to be fair, inhaled wood dust is also a known carcinogen.
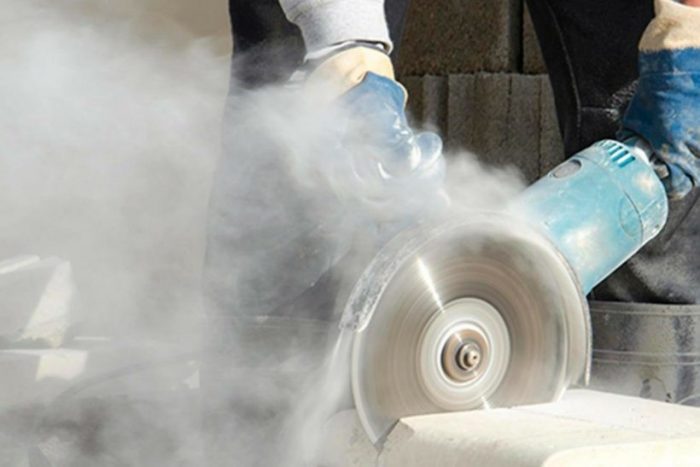
LP SmartSide: Strand Substrate Engineered Wood Siding
The older and dominant composite siding is Louisiana-Pacific’s (LP) SmartSide, which also includes trim. Louisiana Pacific pioneered the production of oriented strand board (OSB) products, of which SmartSide is an offshoot. The material is made of wood strands coated with a resin binder and then compressed—hence the popular term, pressboard. Each piece is treated with LP’s proprietary SmartGuard zinc-borate treatment to protect against termites and rot and coated with primer at the factory. While deemed toxic, no occupational exposure limits exist for zinc borate. No known long-term cancer or reproductive effects exist.
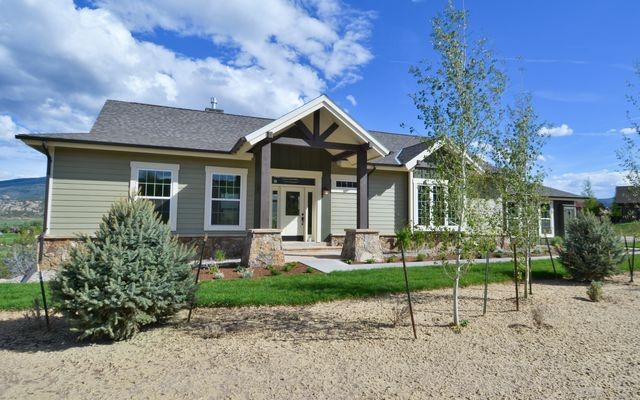
The lumber strands used to make SmartSide do not hold paint well, so the company overlays a resin-treated paper with a smooth or embossed texture. According to the terms of LP’s application instructions, “All exposed edges of LP SmartSide siding and trim must be primed and painted with approved paint to protect the siding substrate.” Unlike traditional lumber siding, the backside is better left unpainted. The company recommends acrylic latex coatings designed specifically for wood composites. You can also purchase prefinished LP SmartSide siding and trim through a network of third-party finishing companies.
Green bonafides: SmartSide is manufactured using logs harvested from forest resources managed sustainably through the Sustainable Forestry Initiative (SFI), an environmental certification pioneered by the American Forest & Paper Association in 1994. LP states that 100% of its United States and Canadian fibers come from SFI-managed forests, and their lumber sources outside North America, notably Chile and Brazil, are administered to the same standards, although not certified. LP publishes a comprehensive brochure providing detailed information on the company’s environmental policies, including the results of third-party audits.
The US Green Building Council’s (USGBC) Leadership in Energy and Environmental Design (LEED) rating system does not afford points for SFI certifications. An exception exists through the Alternative Compliance Path in LEED v4, a pilot program used to achieve green building credits using an alternative approach to what is specified in the existing rating tool.
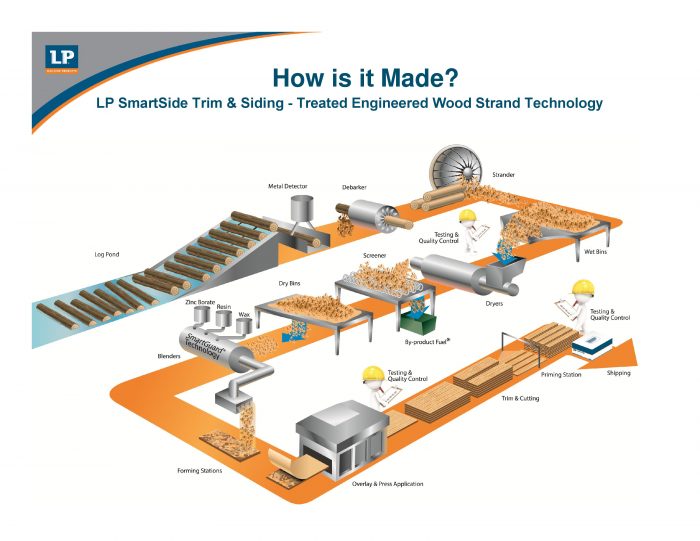
Kaycan Eco-Side: Granular Strand Engineered Wood Siding
A newer entrant to the engineered siding market, Kaycan Wood Products (KWP) Eco-Side Engineered Wood Siding, consists of an engineered wood substrate treated with resin binders or pMDI (polymeric diphenylmethane diisocyanate) resins. These pMDI resins are a non-formaldehyde-based polymer.
The material is not treated with zinc borate, which can cause lung, skin, and eye irritation when cut and sanded. Instead of zinc borate, the biocide used in most engineered siding, KWP developed a proprietary resin system that the company claims provides a barrier resistant to water, insects, and fungal decay.
Unlike older strand lumber products, KWP is manufactured using fine-ground recycled hardwood shavings and sawdust reclaimed from the sawmilling industry. The company claims this allows a higher percentage of waterproofing and preservative agents on the board.
An advantage of granular composites is that they come with a denser core of edge-grain lumber, less susceptible to wicking moisture. This allows tighter butt joins, 1/8-in. vs. 3/16-in. gaps.

Because the substrate is a grain, vs. a strand (like edge-grain vs. flat-grain lumber), Eco-Side does not require a paper layer to hold paint. The top surface of the substrate is embossed during the manufacturing process with a smooth or simulated cedar texture. Because the texture is embossed onto the substrate and not an overlay, the company offers a deeper wood grain than competitors. KWP claims the siding will never delaminate.
KWP applies its paint in house, so the warranty for substrate and color comes from a single source. Their primer has enough plasticity to act as a slip-sheet layer under the finished paint, providing topcoat protection from seasonal expansion and contraction—the paint will not crack, even in extreme climates, the company claims. Their coatings are applied through a multipass process yielding a variegated appearance on their deeply embossed products, which appears like stained wood.
Green bonafides: Eco-Side is made with 100% pre-consumer recycled hardwoods, Forest Stewardship Council–certified (FSC C01700) fiber. The manufacturing plants producing the siding substrate used by KWP are certified to the Eco-Certified Composite (ECC) Sustainability Standard, which requires the manufacturer comply with CARB and EPA for formaldehyde emission and demonstrate the full compliance of the following criteria:
- Carbon footprint: The panels act as carbon sinks—that is, that they store enough carbon to offset their cradle-to-gate carbon footprint, as determined in kg-CO2 equivalents of greenhouse gas (GHG) emissions.
- Locally sourced wood: At least 85% of the total wood fiber used annually must be sourced within 250 miles of the manufacturing plant.
- Recycled content: Products must contain either a minimum of 75% recycled or recovered fiber; or at least 50% recycled or recovered fiber and a minimum of 5% post-consumer fiber.
- Sustainability: The plant must have documentation to show that more than 97% of fiber furnish brought on-site is either converted into composite panels or other non-waste products.
- Wood sourcing: The plant shall hold a valid certificate from a recognized certifying agency such as the Forest Stewardship Council (FSC—Controlled Wood Standard or Chain of Custody Standard) or the Sustainable Forestry Initiative (SFI—Fiber Sourcing Standard).
More details are available at the Composite Panel Associations Website. The ECC standard requires complying with three of five criteria, but KWP complies with the full set of five. KWP Eco-Side offers the potential of up to eight LEED points.
Originally published on GreenBuildingAdvisor.com.
View Comments
KWP appears to have dropped their engineered wood siding product. https://www.kaycan.com/engineered-wood-siding/