How to Repair Broken Bricks
Learn to assess the extent of damage in a brick wall, repoint mortar joints, and even make color-matched repairs to damaged bricks.
Synopsis: Bricks and mortar crack with time. In this article, expert mason John Carroll delves into the tools and techniques for repairing damaged brick masonry, including how to match the colors of new material to old, the type of mortar to use, and how to repair a brick without replacing it.
Editor’s note: This article was written before OSHA released their guideline about the dangers of breathing in silica dust when cutting or grinding masonry. Be sure to protect yourself, your coworkers, and your clients if you take on a project like this.
There are a lot of reasons people choose brick for a building material. It doesn’t provide an endless buffet for termites or serve as a building site for carpenter ants. Woodpeckers do not delight in drilling holes in it. It’s dimensionally stable, doesn’t rot or burn, and never needs to be painted. With all these things going for it, though, brick has an Achilles heel: It’s hard and inflexible, and it cracks under certain conditions.
Whether the cracks are caused by movement, insufficiently filled joints, or simply too many decades of being exposed to the weather, the owners of brick houses in Durham, N.C., often call me to fix them. The reason they call me is because I do more than slop mortar into the cracks. I make an effort to match the color of the existing mortar, and when bricks are cracked, I repair the cracks with mortar dyed to match the color of the bricks. I also prep the surface properly, use the correct mortar, and keep the joints as neat as possible. After packing the joints with mortar, I tool them to match the profile of the joints on the rest of the wall. My goal is always to make the cracks disappear.
Why brick cracks
Masonry structures crack for several reasons. The first is because the footing or slab the masonry rests on moves. (Many older houses don’t even have what we’d consider footings today; the structural brick wall rests directly on the soil.) The first building material is not the footing but the soil that it bears on. Footings should be placed on virgin soil or soil that has been mechanically compacted to reach the proper bearing capacity.
Water can cause some otherwise sound soils to become soft and plastic, reducing their bearing capacity and resulting in differential settlement that cracks the footing. Saturated soil that freezes can push sections of a footing up, or it can push laterally on a below-grade masonry wall. Another problem is that structures such as foundation walls and retaining walls are often underbuilt. Masonry that’s subjected to strong lateral forces, such as those imposed by soil, should be reinforced with steel.
A well-planned system to drain water away from the foundation is essential. But the work of even the most careful builder can be undone later by changes to the grade around the house. Landscaping that piles up mulch and dirt a few feet from the house often holds water that soaks in and eventually causes cracks in footings and concrete slabs.
Steel lintels support brick as it passes over windows and doors. Steel that is too small for the span can deflect, causing cracks in the masonry above. In addition to sizing lintels correctly, it’s important that they bear on the brick at each side of the opening and not be attached to the wood framing behind. Wood expands and contracts more than masonry. Fastening the lintel to the framing can cause cracks in the bricks.
Rusting lintels also can damage bricks. Steel expands as it rusts, lifting the masonry. The stair-shaped cracks that run up and away from the top corners of door and window openings are usually caused by this rust. The best way to avoid them is, once again, to manage the water. Lintels should be flashed carefully to keep them dry and to shed any water that gets behind the brick veneer.
Cracks are also caused by poor workmanship. Over the long haul, joints that are packed solid with mortar perform a lot better when exposed to the elements than joints that have voids under the surface. Although builders should take the steps described here to minimize movement in masonry structures, movement can’t be eliminated completely. At least some movement is inevitable, so repairs will become necessary eventually.
Sizing up the job
When people call me to repair brickwork, my first task is to look closely at the area in question and decide whether the work is going to be cost-effective or even feasible. In general, I encounter three types of problems. The first is old mortar that’s loose in spots and has some visible fissures and voids. In these cases, all that’s needed is to grind out the mortar and repoint the joints.
The second type of problem occurs when the brickwork has moved and created cracks, some of which run through the bricks. In this case, the homeowner has to make a difficult decision. The only way to ensure that the brickwork won’t crack again is to address the cause of the movement. Since this often involves replacing a lintel, or even repairing a footing, addressing the root cause can be very expensive. On the other hand, it may be reasonable to assume that a house that has been sitting in the same spot for fifty or more years has done all the settling it’s going to do. Managing the water around the foundation may be enough to stop any further progress of the underlying cause, and simply repairing the masonry becomes acceptable. I’ve made many repairs in such cases that have held up well for over a decade.
The third type of problem is when the masonry is falling apart and can’t be repaired. A common example is brick stairs that were built without a concrete footing. No amount of repointing can repair these crumbling structures, and I advise the homeowners that the best solution is to tear the whole thing out, dig and pour a proper footing, and build a new set of stairs. Brickwork on houses themselves rarely reaches this state because it’s usually repaired before then.
I frequently encounter poorly done repairs. The mortar is often the wrong type and the wrong color. It’s smeared on the face of the bricks and finished in a manner that doesn’t come close to matching the joints on the rest of house. Cracks that run through bricks are simply filled with gray mortar. The repaired cracks might keep water out, but they are an eyesore. I often end up redoing these botched fixes as I work my way around the house repairing other cracks.
Make the mud to matchA common mistake is mismatching the mortar color. Achieving a perfect match is hard; old mortar can display a range of shades, and sometimes it was dyed. Prior to the 1960s, portland-cement/lime mortars prevailed and tended to be light tan in color. Masonry-cement mortars have gained popularity since then and are generally gray but also come in white, tan, and buff. You can get a good match by making samples using mixes from different manufacturers and letting them harden for a week or so; mortar lightens as it dries.When standard materials don’t match, I bring a chunk of the mortar to Custom Match Colors (custommatchcorp.com), a local company with scores of powdered mortar dyes. If I get close to the existing color, then time, dust, pollen, and algae make small differences disappear. ![]() ![]() ![]() ![]() |
Use the right mortar
Mortar should be softer than the bricks so that small stresses are absorbed by the mortar rather than damaging the bricks. Before the late 19th century, mortar was very soft, consisting of lime and sand, and worked well with the soft bricks of the time. Beginning in the late 19th century, improved kilns and manufacturing techniques created harder bricks, and portland cement became commonly available. Modern mortar always contains portland cement and sand, which sets up harder than straight lime mortars. To improve workability and soften the mortar, masons add hydrated lime to the portland cement. In the 1920s, masonry cement came on the market. Masonry cement contains portland cement but uses proprietary ingredients in place of site-added lime.
Varying the ratio of portland cement and lime (or the proprietary ingredients in masonry cement) to the sand yields different classifications of mortar with different compressive strengths. Both portland-cement/lime mortar and masonry-cement mortar are classified in three types: M, S, and N, with Type M being the hardest and Type N the softest. An even softer mortar, Type O, is not available as a masonry-cement mortar and can be made only by mixing portland cement and lime. To repair cracks in brick walls, Type N is considered ideal for most buildings built after 1900. For historic buildings with soft bricks, Type O or lime mortar without portland cement is usually specified.
Type M, Type S, and straight portland-cement mortar with no lime shouldn’t be used to repair cracks in brick walls. They are hard and inflexible, adhering to the bricks so tenaciously that the slightest movement can cause the bricks to split and spall.
Fill the joints![]() To transfer the mud from the hawk to the wall, I use tuck pointers in several widths (1⁄4 in., 3⁄8 in., 1⁄2 in., 5⁄8 in., and 3⁄4 in.), choosing the widest that will fit in the joint I’m filling. When possible, I work directly from the hawk. But sometimes there are obstructions such as sills, or it’s too close to the ground to hold the hawk, so I transfer the mud on the tuck pointer. I apply the mud in layers and allow each to set up a bit before applying the next. I continue until the joints are packed full. For carrying the mortar to the joint, I use the tuck pointer to cut a 1⁄2-in. strip of mortar on the hawk. I make a long motion of pulling the mortar along the surface of the hawk. This adheres the mortar to the tuck pointer so that I can carry it to the joint without dropping it. I keep a 4-in. brick trowel handy for patting down and shaping the mortar on the hawk; this helps keep the pancake of mortar together and at the right thickness. ![]() ![]() ![]() ![]() ![]() |
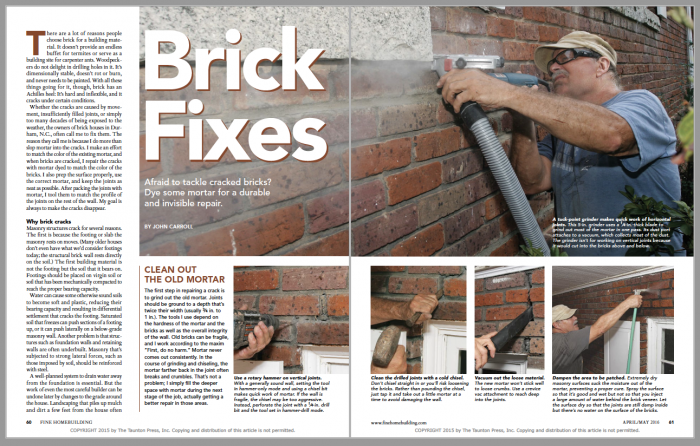
Click the View PDF button below to see the entire article:
This article appears in Fine Homebuilding issue #258 titled “Brick Fixes”