How to Choose the Right Siding for Your House
Learn about the costs, pros, and cons of the 3 most common siding materials: wood, fiber cement, and vinyl.
Synopsis: While the exterior of a house can be clad with any number of materials, most houses in the United States sport one of three popular types of siding. In this article, FHB contributing writer Scott Gibson takes a look at those three products: fiber cement, vinyl, and wood.
No siding is more dominant in new residential construction than vinyl. Near-universal availability, low cost, and minimal upkeep all helped to make it the principal siding material in one-third of all new houses built in 2012, according to the U.S. Census Bureau.
But what if—despite its widespread appeal—you’re not a fan of plastic siding? If you’re aiming for a traditional shingle or clapboard style on your house, your alternatives include a variety of solid-wood species, as well as engineered wood and fiber cement. While the low cost and low-maintenance requirements of vinyl may have overshadowed its competitors in the broader market, a side-by-side comparison still can be worthwhile when you’re choosing a cladding for your new house or re-siding project.
Regardless of the type of siding you’re considering, it makes sense to look at three criteria: appearance, durability, and cost (including the cost of installation). Here’s a look at how the three big siding categories—wood, fiber cement, and vinyl—compare on these points. Although brick and stucco are strong regional players (brick is the single most common choice in the South), they call for specialized installation techniques outside the skill set required for the options considered here.
![]() |
![]() |
![]() |
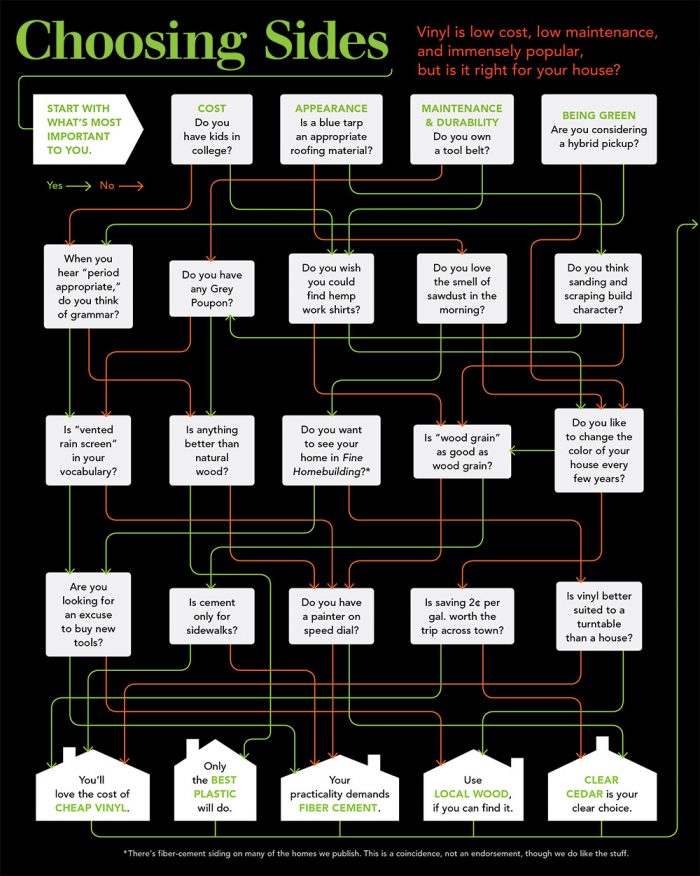
Wood
Staunchly traditional, fading market share
Early settlers used mostly wood siding because that’s what was available. In terms of market share, however, it’s been downhill ever since. In no part of the country does wood siding currently account for even one-tenth of new single-family homes. In the South, it’s a faint blip on the screen (3%), according to Census Bureau figures.
Wood siding is made from solid material or short scraps and offcuts glued together with finger joints. Species commonly used for siding run the gamut from cedar and redwood to pine, fir, and other locally available woods. When sourced locally, wood siding can be sustainable in every sense of the word.

Nothing looks quite like wood
Wood siding is available in many forms: sawn shingles, split shakes, tapered clapboards, and planks that can be applied either horizontally or vertically. It’s adaptable to a range of architectural styles, and for certain types of houses, such as New England Capes, it has been the choice for generations of builders. In terms of appearance, wood remains the ideal against which all its lookalike substitutes are measured.
There’s no durability without maintenance
The best grades of wood (clear heartwood of western red cedar, Alaskan cedar, and redwood, for example) have a long life expectancy if they’re installed correctly. Lesser grades, such as pine, won’t last as long. All types of wood are more durable with a coat of paint or stain. That means regular maintenance for the life of the product. Depending on climate, weather exposure, and other factors, paint may need attention in seven to 10 years. Leaving wood untreated is an option with some species (cedar shingles, for example, are often left unfinished), but expect the color to fade to gray. Untreated shingles and clapboards may curl or split.
Wood siding can last a long time when properly installed and maintained, but it can rot quickly when installed poorly. Wide eaves, protective porches, and good air circulation may not matter for vinyl or fiber cement, but it can help to extend the life of wood siding.
Top grades for top dollar
Wood siding comes in a broad range of profiles, grades, and wood species, all of which affect its cost. Top grades of clear siding are expensive: In material cost alone, cedar siding averages $459 per square (100 sq. ft.), the highest of any siding discussed here (see chart, p. 81). Local species can cost much less. You’ll still pay a premium for the best material, however, and availability and quality vary widely depending on the lumber supply where you live.
Wood siding is installed relatively easily, and it has unrivaled workability. It’s easily cut and shaped with simple carpentry tools, is light in weight, and is safe to handle. Wood siding probably lasts longer when installed over a vented rain screen, which aids drying and prevents water from being trapped between the back of the siding and the sheathing. While very effective, it’s an extra construction step with added costs. The cost of proper installation, as well as the costs involved in periodic maintenance, should be considered when comparing wood to other siding options.
![]()
|
![]()
|
![]()
|
Fiber Cement
Durable and noncombustible
Patented in Austria more than a century ago as Eternit, fiber-cement siding is made of sand, portland cement, and cellulose fiber. It’s sold under at least a half-dozen brand names in the United States. Fiber cement may look like painted wood, but, say manufacturers, it is impervious to wood-boring insects and won’t rot. Fiber-cement siding is noncombustible and comes with warranties of up to 50 years. On the downside, it’s heavy and brittle, and cutting it produces dangerous silica dust.

Think hard, brittle wood
From a distance, fiber cement and wood are visually indistinguishable. Like vinyl, fiber-cement siding is available in a number of forms that look much like traditional wood siding. Lap siding is typically 5⁄16 in. thick and 12 ft. long and available in widths of 5-1⁄4 in. to 12 in. It’s installed with an overlap of 1-1⁄4 in.
In addition to smooth and textured lap siding, there are individual and panelized shingles as well as panels in sheets up to 4 ft. by 10 ft. One company, Nichiha, manufactures panels made to look like brick and stone.
Fiber-cement siding can be ordered primed, unprimed, or factory-finished in one of nearly two dozen colors. Fiber cement must be painted; manufacturers recommend 100% acrylic latex paint.
Tough to the core
With an inherent resistance to fire, insect damage, and rot, fiber-cement siding comes with lengthy warranties, which are often transferable. CertainTeed and Maxitile, for example, offer a 50-year prorated warranty. James Hardie offers a 30-year nonprorated warranty on its fiber-cement products.
Factory-finished products require minimal maintenance. James Hardie offers two climate-driven paint formulations for its factory-finished siding; both finishes have a 15-year warranty. CertainTeed’s ColorMax finish has a 15-year warranty covering peeling, flaking, and cracking.
Installation boosts cost
National averages indicate that it costs as much to install a square of fiber cement—$121—as it does to buy it. There are a few reasons for this: Fiber-cement siding is relatively heavy (a 4-ft. by 8-ft. panel weighs 73 lb., compared to about 20 lb. for a 12-ft. piece of 8-1⁄4-in. lap siding). It’s also somewhat brittle. More important, cutting fiber-cement products can create dust that contains crystalline silica, a serious health threat. Special vacuum-equipped saws or shears should be used. Proposed OSHA rules designed to protect workers may tighten job-site regulations in the future.
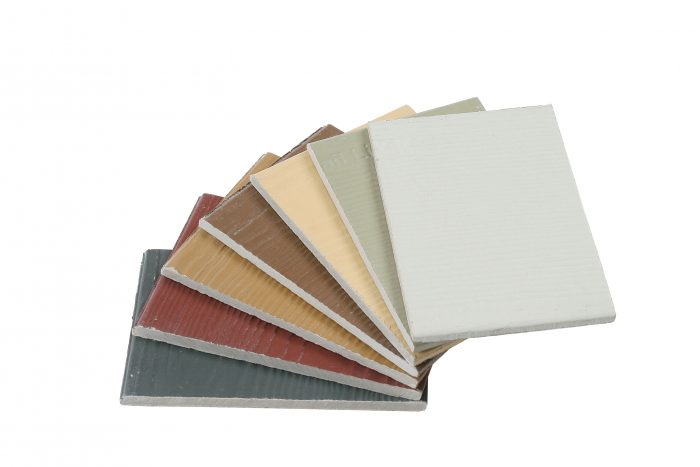
Vinyl
Low price, long life
Combining durability and low maintenance with a low price, it’s no mystery why vinyl (PVC) has become a dominant siding material. Pricier plastic options include polymer (polypropylene) siding, which uses an injection-molding process to give products a highly defined, three-dimensional profile; and cellular PVC, which has a weight and density similar to wood.
Despite its practical advantages, some homeowners and builders just don’t like plastic siding. It has been attacked for everything from unsightly trim details to the inherent toxicity of manufacturing polyvinyl chloride. Two common criticisms of PVC involve the release of vinyl chloride and dioxin, both carcinogens, either during the manufacturing process or when PVC is burned. The vinyl-siding industry, however, says that manufacturing was modified years ago to control exposure to vinyl chloride and that vinyl is an “extremely small source of dioxin.”
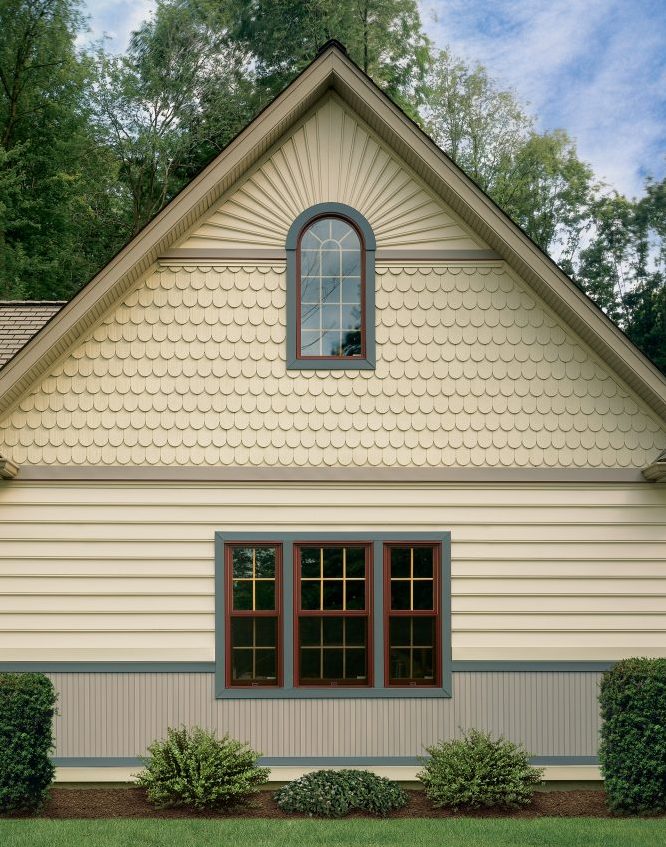
If wood can do it, so can plastic
Plastic siding is manufactured in a number of profiles meant to look like traditional wood siding, including shingles, clapboards, shiplap, and board and batten. It’s available in hundreds of colors, including dark colors, and can be purchased with an integral EPS backing to increase overall R-values.
According to David Johnston, senior technical director of the Vinyl Siding Institute, insulated siding can add between R-2.5 and R-3 to a wall’s R-value. Although it’s somewhat more expensive than other grades of vinyl siding, it tends to appear flatter on the wall.
The thickness of vinyl siding ranges from 1⁄25 in. to 1⁄20 in. (builder grade). Thicker and more expensive grades of vinyl siding are stronger and more rigid than entry-level products.
Two words: Plastic lasts
Low cost is an important advantage of vinyl, but it’s not the only one. Vinyl siding requires virtually no maintenance, lasts for decades, and won’t trap moisture against the sheathing as other types of siding can. With no wood-fiber content, it won’t absorb water and won’t rot.
The right vinyl will stand up in a storm. According to the Vinyl Siding Institute, some products meet 150-mph building-code requirements in Miami and Texas, and several can withstand 190-mph winds.
Expensive is better than cheap
There’s no formal grading system for vinyl siding as there is for wood, but three important variables are the thickness of the material, the type of nail hem, and the type of capstock, which is co-extruded with the substrate as a color layer. Economy vinyl is light and easy to install. National data indicates the installation cost of polymer siding is higher than for any other siding.
![]()
|
![]()
|
How green is your vinyl?Few questions can touch off an argument faster than this one. Bill Walsh, founder of the Healthy Building Network, points to a variety of concerns, including PVC’s reliance on chlorine gas for its manufacture and the toxicity of its chemical components and by-products. In a blog post at GreenBuildingAdvisor.com, Walsh called vinyl “the worst plastic for the environment and the antithesis of a green building material.” Yet the U.S. Green Building Council’s LEED program does not prohibit PVC building products, and the vinyl industry has prepared a lengthy report to document its claim that vinyl siding has a much lower environmental impact than brick, fiber cement, or stucco. Writing in Fine Homebuilding a few years ago, Betsy Pettit, an architect and the president of Building Science Corp., noted that all siding materials have environmental costs. Because of vinyl’s long service life, its suitability for recycling, and its track record for trouble-free installations, however, Pettit concluded, “Yes, vinyl siding is green.” The answer? PVC is not a perfect material for siding, but neither are most alternatives. |
Still undecided? Engineered options have improved—and multiplied
Engineered-wood siding, including hardboard and oriented-strand-board products, got off to a rocky start in the 1990s.
Made with wood fibers and resin, engineered siding was marketed by a number of companies as a lower-cost, better-performing alternative to solid wood. Early versions of the siding often failed, though, none so spectacularly as Louisiana-Pacific’s Inner-Seal. The OSB siding ultimately cost the company $460 million in payouts. Class-action suits over faulty hardboard siding haunted other manufacturers, including Georgia-Pacific, Weyerhaeuser, and Abitibi-Price.
After the Inner-Seal debacle, LP regrouped and went on to develop an OSB-like board called SmartSide that uses a different kind of resin and incorporates zinc borate to protect it against decay. SmartSide carries a 50-year, prorated warranty against fungal degradation, buckling, and cracking, and a five-year warranty covering labor and materials. LP says it has sold 6 billion sq. ft. of SmartSide siding and trim since 1998 without a single claim for rot or decay.
Engineered-wood siding is less expensive than many types of wood siding but more expensive than vinyl. Its main competitor is probably fiber cement, over which LP’s SmartSide claims three advantages: It’s more impact resistant, it’s not as susceptible to freeze-thaw damage, and it’s easier to install.
Norandex manufactures an entirely different type of composite siding, one that contains no wood fiber of any kind. Everlast is a mix of stone dust and polymers. It’s guaranteed for the lifetime of the original owner, and a 50-year prorated warranty can be transferred to a new owner. The cost of Everlast falls in the upper end of the wood-siding range.
![]()
|
![]()
|
![]()
|
![]()
|
Siding Costs Compared
“Bare costs” include siding, installation labor, and finish, but not profit or overhead, scaffolding, housewrap, or trim. Prices may vary significantly by region.
Used with permission from RSMeans, a division of Reed Construction Data, LLC.
This article appeared in issue #240 titled “Choosing Sides”.