High-Strength, Long-Life Lap Siding
A carpenter's guide to accurately laying out, cutting, gapping, and fitting engineered-wood clapboards.
Synopsis: Engineered-wood lap siding is a durable alternative to clapboards, and has been on the market long enough that we can be confident in its longevity. Carpenter Ben Bogie details an installation of LP SmartSide engineered-wood clapboards, covering the basics of setup, tools for installing and nailing the courses, the process of marking and cutting for cutouts and trim, and the final step of sealing the seams.
In the United States, there’s probably no more quintessential siding material than clapboards. Once hewn from logs and later sawn, clapboards were one of the earliest things used to clad American homes. Also known as lap or beveled siding, clapboards have pretty much always been a higher-end cladding. In the colonial era, if a homeowner couldn’t afford to cover the whole house in claps, they’d at least try to cover the front, and then clad the back and sides in cheaper cedar shingles. The size of the clapboards also said something about the wealth of the owners—the bigger the exposure, the more expensive the material.
The look is so archetypal that is has been simulated in nearly every kind of cladding that has come since, from aluminum and vinyl to fiber cement and fly ash. One of the better ones to show up—both in terms of its durability and ability to mimic the real thing—is lap siding made from engineered wood.
This isn’t to say engineered wood siding has always been great—an early version, LP’s Inner Seal, had issues that led to a class-action lawsuit. Their follow-up version, SmartSide, was launched in 1997, and has been on the market and on homes long enough now that we can be confident in its longevity. And with that confidence comes popularity— at least among the builders I speak to.
The lap version of SmartSide is a lot stronger than its fly-ash and fiber-cement rivals—a single person can carry a board or bundle over their shoulder without worrying about whether it’ll snap in half. Because it’s wood—basically a high-grade OSB with resins, waxes, and treatments to fend off water and rot—it cuts with standard wood blades, and you don’t need to take additional precautions for silica dust.
If there’s a downside to its strength, it’s that it can be incredibly hard to hand-nail. To ensure pieces stay where they’re supposed to while fastening, a nailer is pretty much necessary. Pay special attention to the nails—LP requires a minimum .113-in. shank, 8d hot-dipped galvanized nail with a .297-in.-diameter head, which is a special-order item in my neck of the woods.

Unlike original clapboards (or fiber-cement or fly-ash versions), SmartSide isn’t beveled across its width. There is an obvious face and back, but no top or bottom—both edges are essentially the same. That means if one edge gets a ding, you can just flip it around and hang it with the good edge down. But it also means that the bottoms of courses get kicked out more than with traditional claps. You need to use minimum 5/4 trim to prevent the bottom edge of the siding from sticking out past it. To keep the kickout angle constant, a starter strip under the first course is essential.
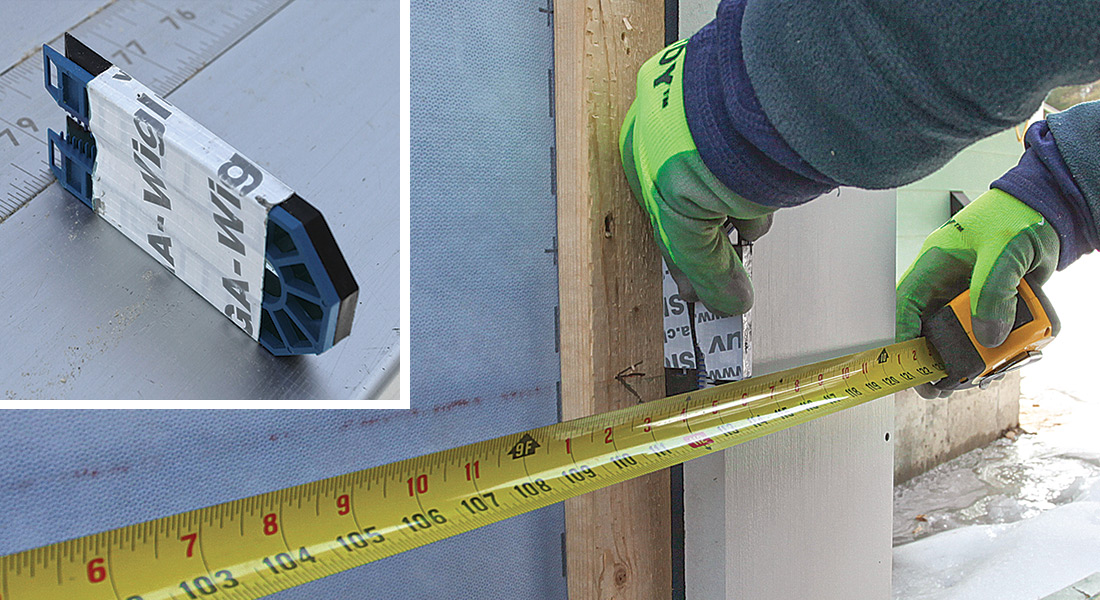
Another difference between this and solid-wood siding is the way you have to gap it. Because this is made from strands of wood, it has the potential to shrink and expand in all directions, while solid wood tends to move most tangential to the grain. While it’s best practice to gap solid-sawn claps at the ends and around penetrations to provide a space for sealant, SmartSide requires 3/16-in. gaps anywhere it butts into something—including butt joints between pieces of siding. As with any horizontal siding application, we stagger butt seams at least two studs away from each other and avoid creating a pattern with the seams.

A lot of what can make or break a lap-siding job is done long before any trim goes on. On a blank wall, it might not be obvious to the eye that windows are set at different heights. But if it’s clad in lap siding—or any other material that runs horizontally—even minor inconsistencies will be highlighted. We want the placement of electrical-outlet boxes, sconces, hose bibs, and other penetrations to look intentional, so we make sure that they appear in the same siding course.
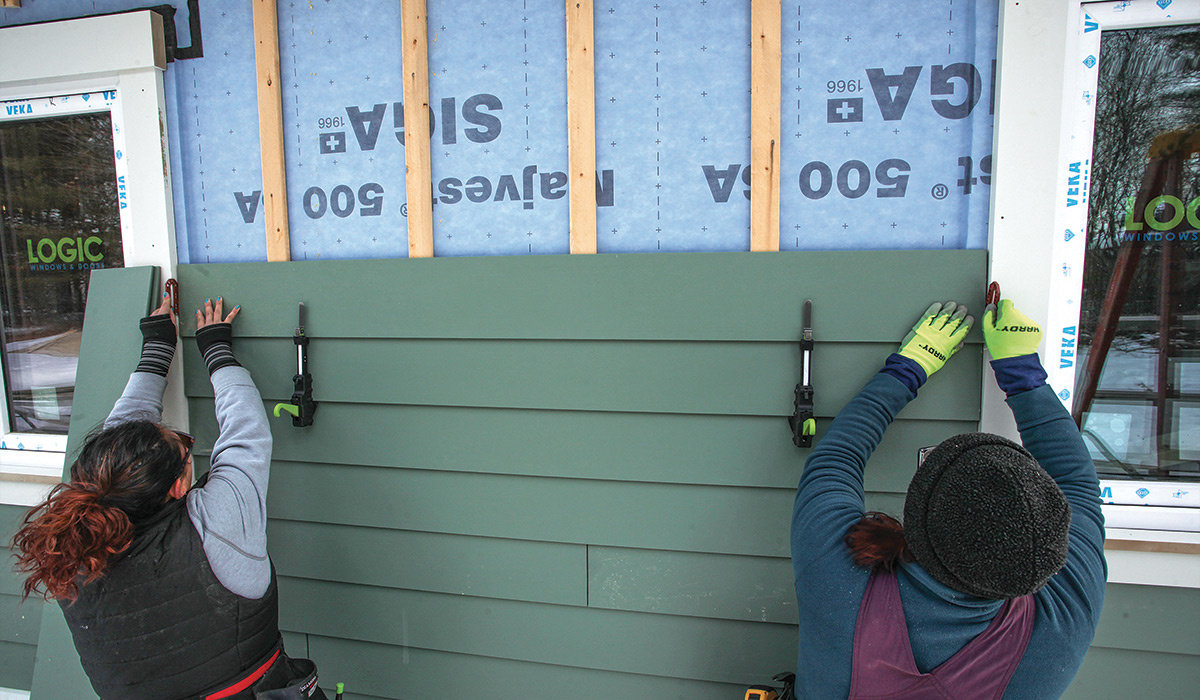
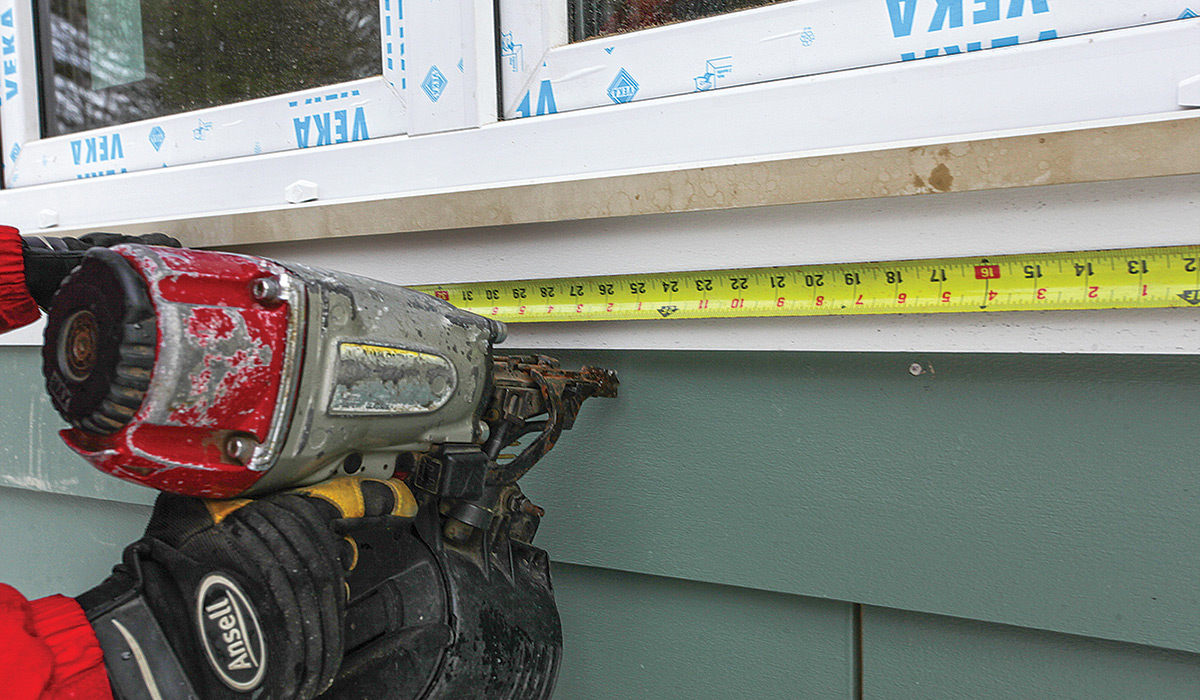
The SmartSide installed in this article is the 76 Series Smooth Finish Lap (8 in.). The standard version comes preprimed, but we had it custom-painted as well (LP also has prefinished options).
Set the course
There are two major schools of thought when it comes to laying out lap siding. The first is to lay out the courses on each wall so that they line up with the door and window trim, which usually requires adjusting the exposure of courses as you go up the wall. The eye typically has a hard time picking up these differences. On old New England houses, which usually started out as rectangles with no inside corners to speak of, this approach was long considered the “right way” of doing things.
But with more complicated buildings, especially ones with varying window and door sizes, this is next to impossible to achieve while maintaining the continuity of courses around corners. Unless things were planned to a T, it’s unlikely that the courses on one wall will wrap neatly around to the neighboring wall while falling perfectly in line with windows and doors. Corner trim can disguise minor discrepancies at outside corners, but inside corners are another story—trim there is usually narrow, so it’s obvious when the courses don’t line up.

For these more complicated situations, the approach I use is what I call “set it and forget it.” The most basic example of how this works is this: Simply measure the distance from the bottom of the wall to the bottom of the frieze or soffit and divide this measurement by your desired exposure. You’re likely left with a fraction. You can either round the number you get up or down. If the fraction is under 1/2 in., I usually round down. If it’s 1/2 in. or greater, I round up. This rounded number is the number of actual courses you’ll install. To get the actual exposure, divide the height measurement by the number of courses.

![]() |
![]() |
![]() |
Here’s an example: Say you have 8 ft. from the top of the water table to the bottom of your frieze. You have 8-in. lap siding, and the manufacturer requires at least 1 in. of overlap. So 7 in. is the maximum exposure. Divide 8 ft. by 7 in., and you get 13.714 courses. Round that up to 14. Then just divide the wall height by 14, and voila, you have your exposure—in this case 6-7/8 in. when rounded to the nearest 1/16th of an inch. Use the same exposure all the way around the house, and all corners will match up.
This method sounds easy, but it can be time consuming because pieces have to be cut to fit around door and window openings rather than simply adjusted up or down.
Installation basics
We use a laser level to establish control lines early on in the build, and use them to ensure the soffit is set level around the building. The control lines later get buried behind the peel-and-stick water-resistive barrier, so they aren’t visible here, but the soffit is. The soffit becomes the reference point for everything else that sits level, including the water table, which goes up before the siding. Corner trim—both inside and outside—needs to be plumbed in both directions, and also gets installed before the siding.
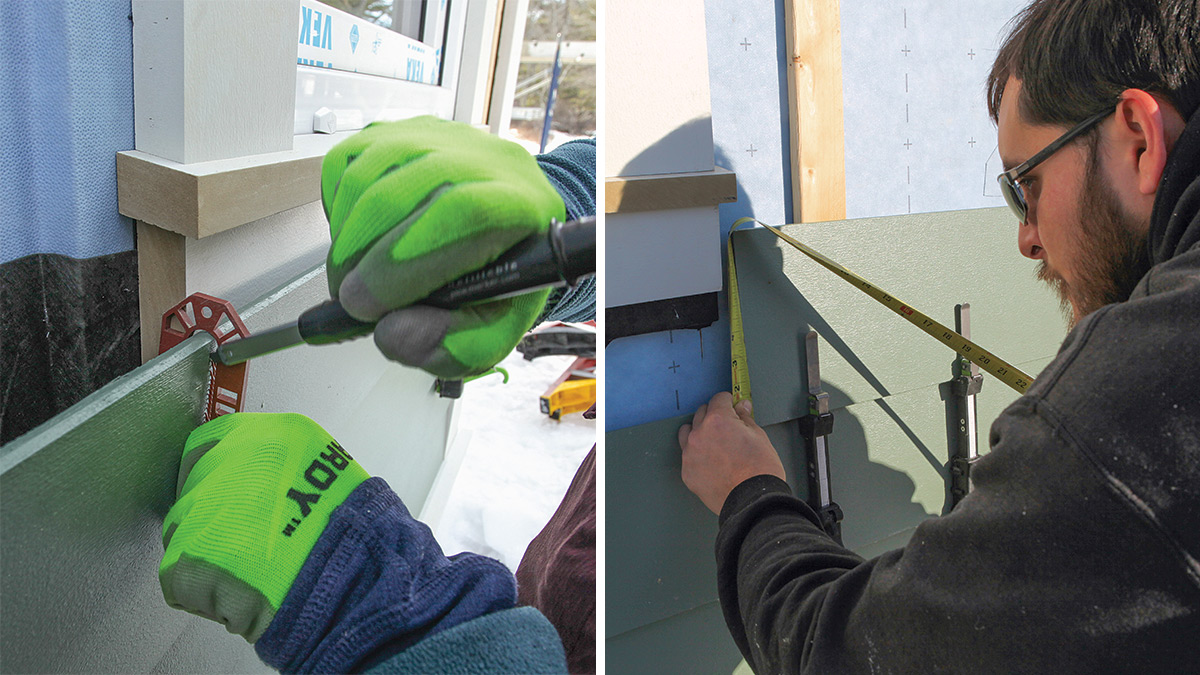
We snap level lines as reference for the top of the first two courses, but from there on, we use siding gauges to help keep everything on track. The ones used here, from SoloSider, are adjustable in 1/16-in. increments and hold pieces of siding in place at the correct exposure while marking for cutouts and nailing.
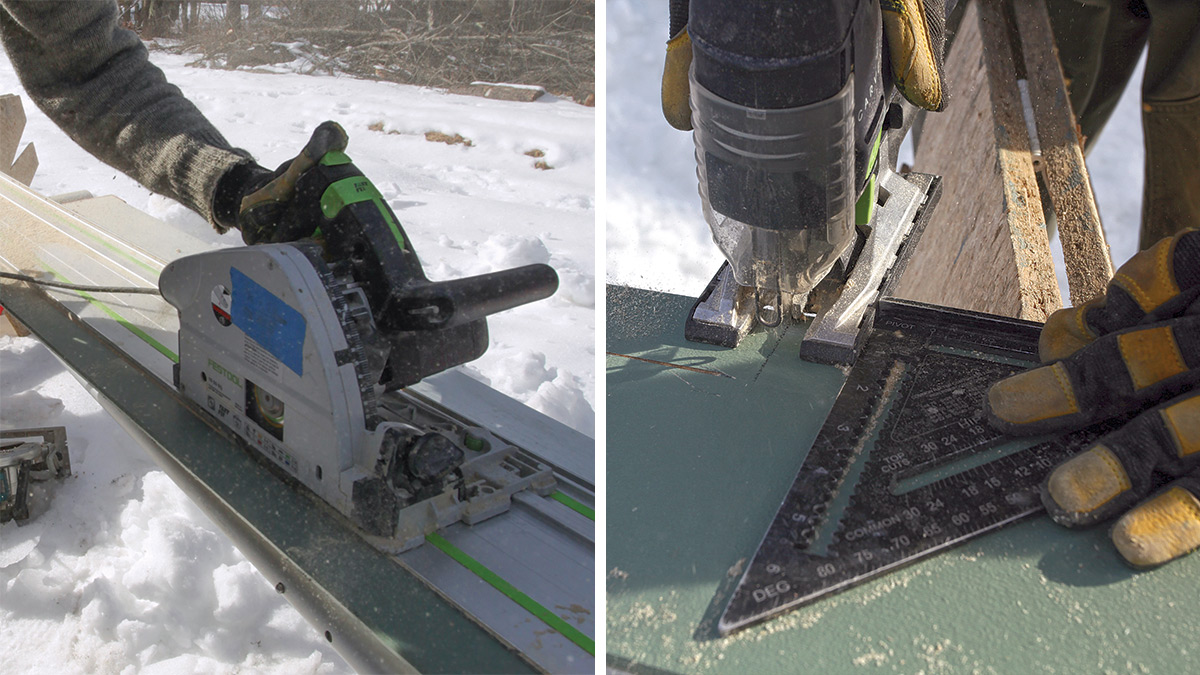
SmartSide should always be blind-nailed into studs with each course lapping the previous by at least 1 in. Maximum nail spacing generally depends on the thickness of the siding—for 3/8-in. siding, it’s 16 in. o.c.; for 7/16-in. it’s 24 in. o.c. It can’t be used in contact with masonry, and must be at least 6 in. above grade, but only has to sit 1 in. above the roofline, which makes for a clean transition at sidewall terminations.

Sealant is another big consideration. Anything that exposes the wood-strand core needs to be sealed. LP makes moldings that seal butt seams, but otherwise, all gaps, cuts, and exposed overdriven nails need to be sealed with an exterior elastomeric sealant. LP requires sealants that meet ASTM C920 and are a minimum of class 25—meaning they can stretch or compress one-quarter of the joint width. Higher classes can stretch and compress even more. We did this installation in late winter, but when it’s warmed up enough, we’ll come back and fill all of these joints and cover exposed nail heads under windows with color-matched OSI Quad Max.
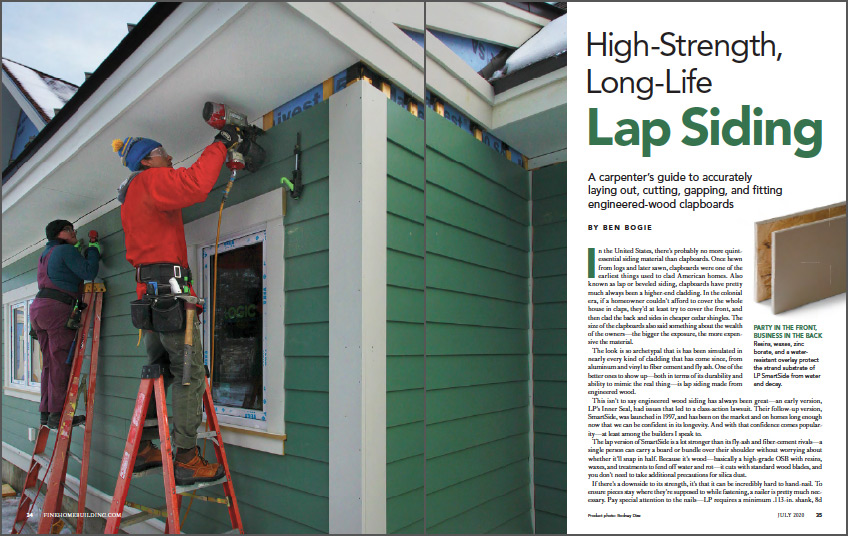
From FineHomebuilding #292
To view the entire article, please click the View PDF button below.
More about lap siding:
Siding to Last a Lifetime – Rainscreen details that improve the durability of any lap-siding installation.
Good-Looking, Long-Lasting Lap Siding – Clever details and flawless installation means this rainscreen wall assembly will weather the biggest storms.
Re-side Over Lead-tainted Siding – Covering old siding may be the simplest way to deal with toxic paint–plus it could be an opportunity to add exterior insulation.
View Comments
Do you like to use a different material for the trim around the windows to pair with Smartside lap siding?