Drip Cap Design and Installation
The lowly drip cap needs to be taken more seriously to prevent leaks and rot.
Early in my building career we ordered the stock uncoated aluminum drip caps from our local building materials supplier to install over window and door head trim and skirt boards / band boards. The back leg was only an inch and drip leg was just a square 90 degree 1/4 in. drop — barely large enough to keep wind-driven water from getting behind the siding. And not very durable.
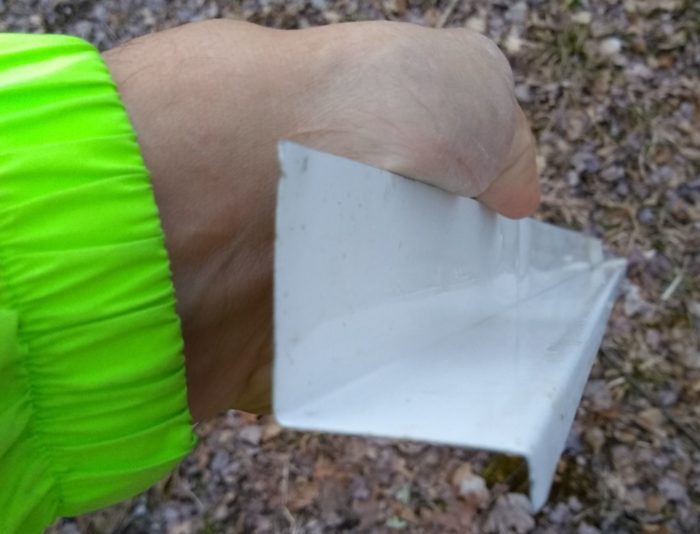
After years of making repairs to homes with insufficient drip caps, where water leaked by the flashing and rotted parts of the wall, I started making my own drip caps and installed them — and the siding over them — to perform their intended function: Keep water out of the wall and drain it away.
The damage from inadequate and improperly installed drip cap flashing can be devastating. Small water leaks into walls generally aren’t noticed by homeowners. Years can go by before a leak is discovered and by then the rot inside can be extensive.
Even if the flashing doesn’t leak it can be installed improperly and lead to siding decay. To work well, the top of a cap flashing has to slope away from the wall so water will drain. Too often the top of cap flashings are flat or even sloped back towards the wall. This is often the case when the siding is installed tight to the top of the cap flashing. Even the small amount of water that sits on a flat cap flashing can wick into the siding and over the years lead to decay.
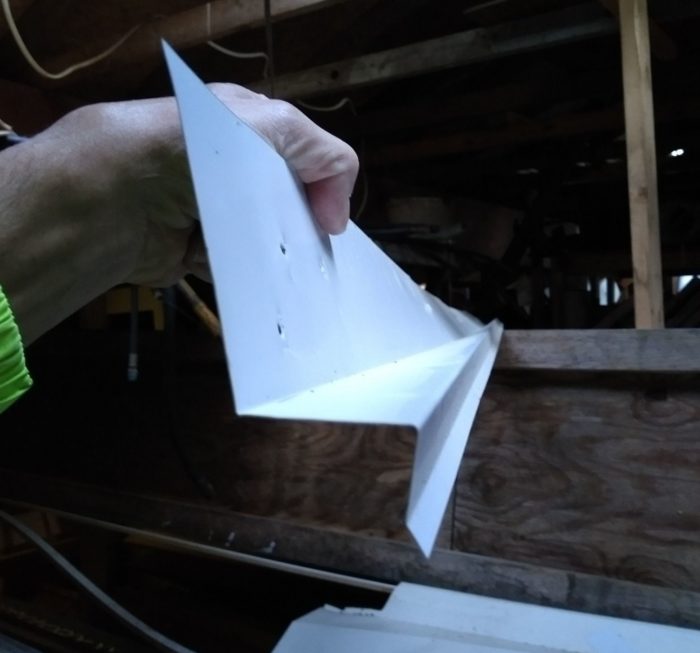
I make my own cap flashings. I start with a minimum of 0.019 in thick aluminum coil stock. 0.019 in. or 26 gauge is the minimum thickness called for in the building code for many specific flashings. Unfortunately, many cap flashings stocked at materials dealers are thinner, so they won’t even meet the code minimum.
I make the wall leg tall — 4 in. to 5 in. This provides for a decent overlap by the housewrap and the siding. A 15 degree slope on the top of the flashing helps water drain off rapidly. The drip leg is at least 3/4 in. and I include a 1/4 in. to 3/8 in. outward kick along the bottom. This does two things — it pushes the water a little further out away from the trim the flashing is protecting, and it helps stiffen the bottom edge so it stay straight as the metal expands and contracts with temperature.
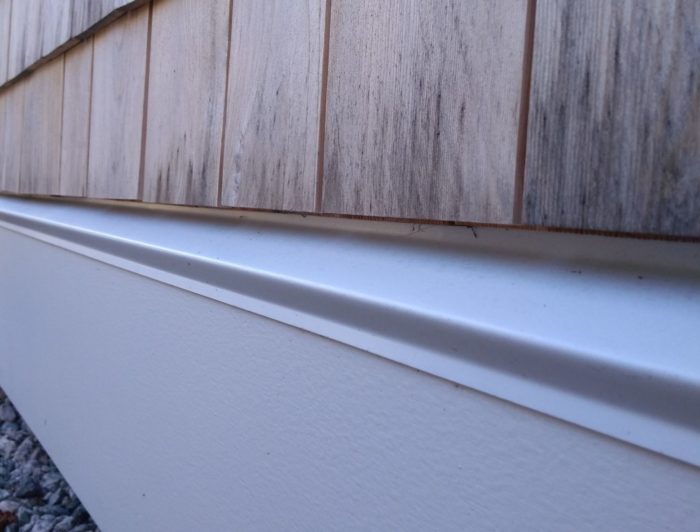
Then when it comes to installing the siding, I make sure to leave at least 3/8 in. gap between the flashing and bottom of the siding so water won’t wick.
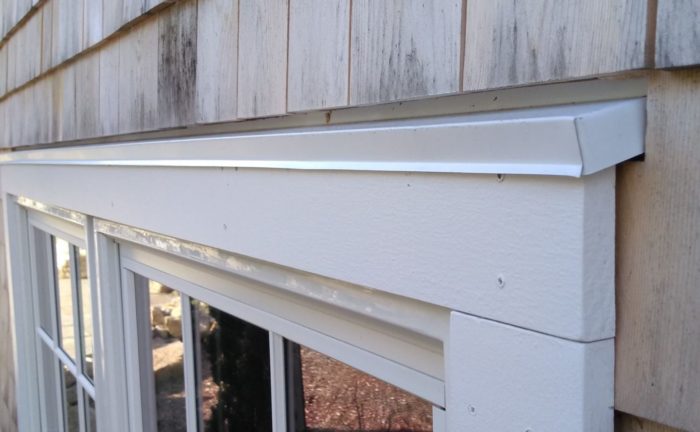
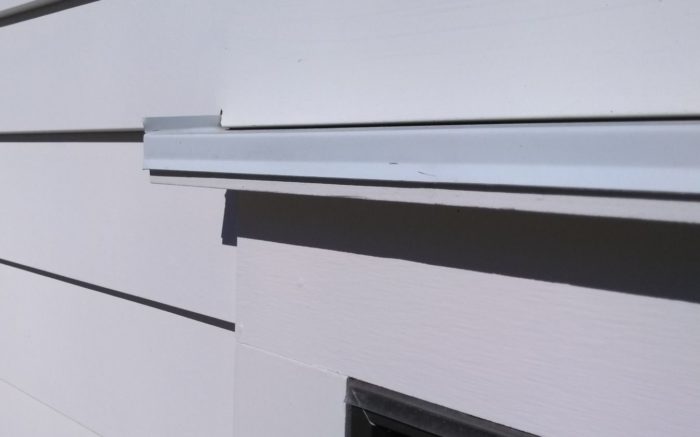
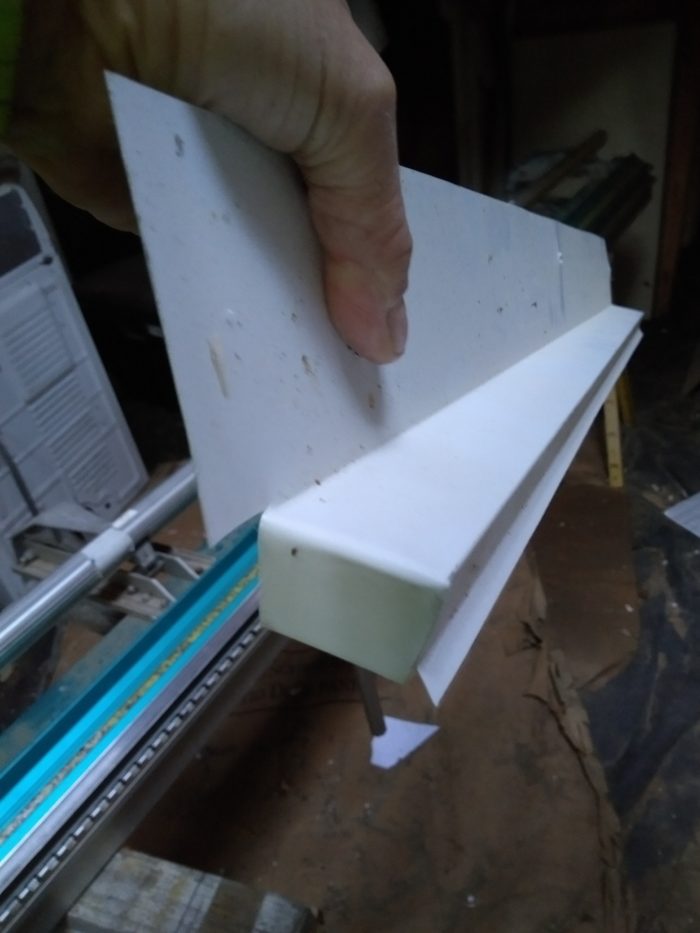
It takes a little more time to bend a nice drip cap flashing but it’s the right thing to do. And it no extra time to install a good cap flashing properly and the siding over it to avoid problems later – so there are no excuses.
www.mikeguertin.com @mike_guertin
View Comments
Mike:
This makes a lot of sense, and even more so in the coastal area in which we've built. Any chance you'll be posting more details about what is involved in rolling your own that way? That looks like some very clean edges on that cap, and would appreciate seeing how that's done.
Kevin,
These cap flashings are just bent using a regular aluminum break. The ends are formed using a pair of hand seamers. Nothing special otherwise.
Good work dude! Can lead be substituted? I would rather use copper but have read red cedar shingles will degrade the copper quickly. Thoughts?