Dutch Door Done Easy
A layered assembly and clever installation make building and hanging this door a breeze.
Synopsis: This article gives details for building and installing a Dutch door using a layered-assembly technique. Illustrations show the dimensions of each layer, and a series of photographs demonstrate the method of building the door (including the sequence of cutting the rabbets to keep the piece stable) and then fitting it into the opening before cutting the door in two and adding weatherstripping and hardware.
Ever since I bought my house, I’ve wanted to replace the back door with a Dutch door. There are a lot of aesthetic and practical justifications—you can get a cooling breeze off the porch while keeping the dog inside, for instance—but there are also some fun challenges associated with the build, and that’s always a good motivator for a craftsman. The method I’ve landed on uses a layered-assembly technique, so you don’t need any plunge routers or mortise machines, or cope-and-stick router-bit sets. Instead, the door is built in three layers, yielding a stiff, strong finished product. I’ve also discovered that the best approach to fitting a Dutch door is to build it as a single piece, hang it in the opening, and then remove it so that it can be cut in two. When the top and bottom halves are put back on the hinges, it’s much less difficult to bring everything into alignment than if everything were installed separately.
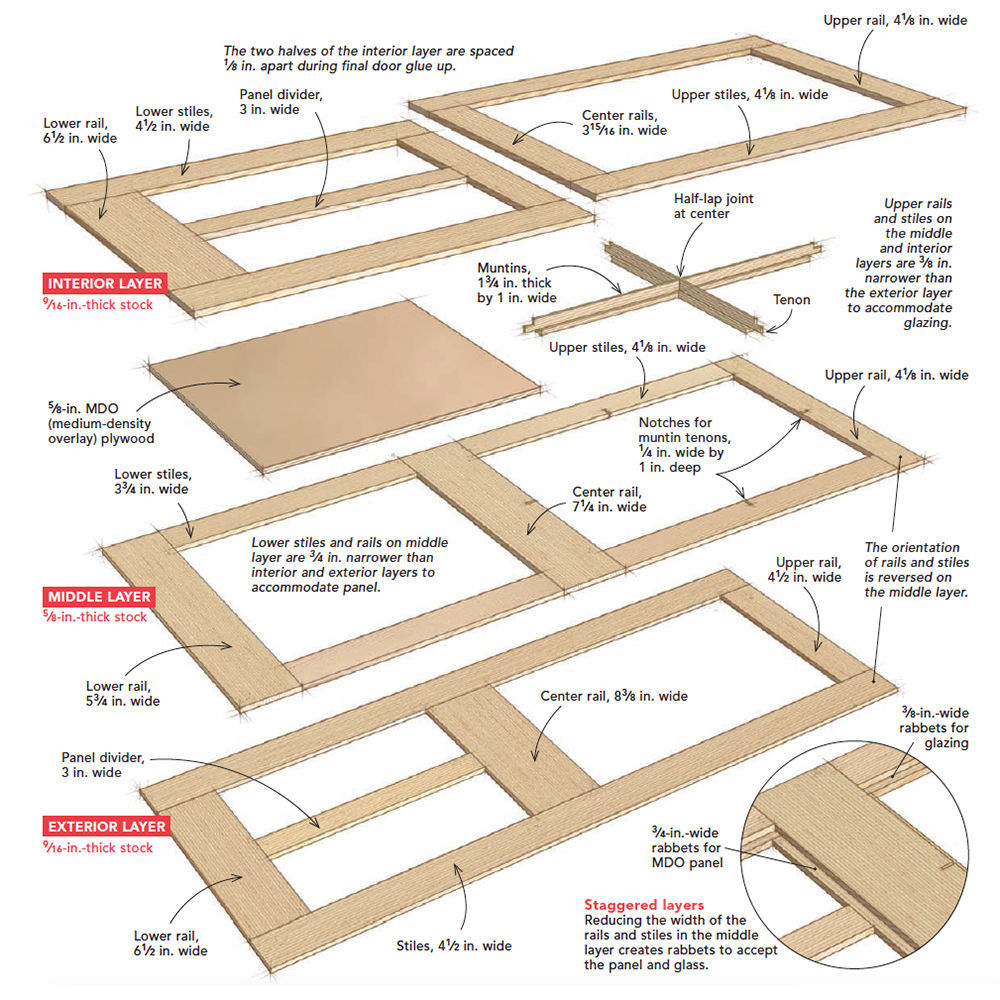
Multilayer door frame is simple and strong
This 13/4-in.-thick exterior door is built in three overlapping layers, providing all of the strength of traditional mortise-and-tenon joinery, but without the fuss. the rails and stiles on the interior and exterior sides of the door are oriented conventionally, with rails butting into stiles, but in the center layer the orientation of the pieces is switched in order to stagger the joints.
![]() |
Saw-friendly assembly. Although pocket screws would also work for all the rail and stile joinery, I used 5×30 Domino tenons, which won’t cause problems when cutting to size and notching the door. |
Build The Door One Layer At A Time
After cutting all the parts to size and thickness, each layer of the door is assembled separately and eventually laminated together.
Lap the muntins. A tight-fitting half-lap joint is key, so sneak up on the fit until the pieces slide together snugly without forcing them. |
![]() |
![]() |
Fit the panel. Drop the 5⁄8-in.-thick MDO panel—a type of waterproof plywood—into the middle layer, where it will be captured by the interior and exterior layers. |
![]() |
![]() |
Roll on the glue. I recommend using Titebond III glue, which is waterproof and has a long open time ideal for a complicated glue up. Use a mini paint roller to apply a thin coat onto both mating surfaces, overlapping the edges of the MDO panel. |
Installing The Door Is Half The Fun
The secret to a perfect fit is to hang the door before cutting it. After fitting the door to the opening, cut the door in two, add the shelf, and rehang. With quality hinges, the two halves should align correctly with an even reveal.
Milling Muntins On The Tablesaw
![]() |
Ready For Glass After assembly, insulated glazing units are bedded in silicone and secured with nail-on interior stops. |
ALSO SEE: Video: Build a Dutch Door
From Fine Homebuilding #282
To view the entire article, please click the View PDF button below.
Fine Homebuilding Recommended Products
Fine Homebuilding receives a commission for items purchased through links on this site, including Amazon Associates and other affiliate advertising programs.
Code Check 10th Edition: An Illustrated Guide to Building a Safe House
Homebody: A Guide to Creating Spaces You Never Want to Leave
Get Your House Right: Architectural Elements to Use & Avoid