Get the Right Windows
Follow these three basic steps to make sure you’re up to date with the changing window market.
Synopsis: Asa Christiana details the three basic steps when it comes to choosing windows: choosing function, material, and glass. He outlines the different types of windows, from tilt-turns to fixed-frames to swingers and sliders, along with details of the performance pros and cons of each. He describes relative costs of different materials from vinyl to aluminum to fiberglass, composites, and wood, along with their durability and popularity. Finally he discusses glazing, including the use of double-pane vs. triple-pane and the prevalence of low-e glass. The article also breaks down a ratings label for window glass and what the various numbers mean, from U-factor to solar heat-gain coefficient (SHGC) to air leakage (AL).
Whether you’re building or remodeling, you’ve got one good shot at getting the shell of the house right. In terms of energy efficiency, windows are always the weakest link in the building envelope. So it pays to make a wise choice. Windows also have a big effect on the way a house looks, feels, and functions.
Contrary to popular belief, your builder or local window dealer might not be the best source of information. Most builders’ main incentive is to keep things straightforward and minimize risk, so they tend to stick with the same suppliers. Window dealers also have established relationships, limiting your product selection. More than ever, it pays to hire an architect or designer, who will be open to a wider variety of solutions.
Window performance should be kept in proportion with the performance of the rest of the building envelope. With glass making up only 20% of the walls of the average home, and windows being a lot pricier per square foot than the rest of the shell, you should invest first in better-performing walls, roofs, and basements. But if you’ve already upgraded the rest of the house to better than average, you can take the comfort, efficiency, and functionality of your home to a new level with new window options. It takes just a little bit of inside knowledge.
Performance translates to comfort
While most homeowners think about price and aesthetics first, experts recommend flipping the script and focusing first on performance and long-term value. Energy savings add up quickly, and energy-efficient windows make a home more comfortable. For instance, the innermost pane of a triple-pane window is much closer to room temperature than the inner pane in a double-glazed unit, letting you sit close to the window without feeling heat or cold radiating off it (a situation that is often confused for a draft).
Low-cost windows can often be pricier than they first appear. Like any weak link in the building envelope, poor-performing windows require a larger HVAC system and ducting, which is more expensive up front and more costly in the long run. For Steve Baczek, a Boston-area architect who specializes in high-performance homes, it’s a simple dollar shift. “With much better-performing windows, I can sometimes do one $5000 minisplit HVAC system instead of a $30,000 ducted distribution system.”
Whenever possible, experts also recommend choosing tilting or swinging windows over sliding models like traditional double-hungs. That’s because swinging casements, awnings, hoppers, and tilt-turns have hardware that pulls them tightly against their frames, with compression gaskets that leak far less air than the weather seals around sliders, no matter how good the seals are.
Old answers don’t always hold up
Window categories and materials have changed in the last decade, and yesterday’s biases and assumptions don’t always hold true. The vinyl (PVC) category is being transformed by new formulations that are more stable and more durable, as well as new window innovations adopted from Europe. The composite category has also expanded, with true fiberglass windows sometimes confused with composite blends of PVC and sawdust. Products vary widely in the wood and clad-wood markets, too, where some older designs are beginning to find new favor.
Glazing is just one more area that is being disrupted and transformed. Once-exotic features like low-emissivity coatings and gas fills are now standard on higher-quality windows, and increased demand for triple-pane glass units are bringing their prices down across the globe.
As building-science experts evaluate the latest window technologies, we are learning that where you live doesn’t matter quite as much as it once did when it comes to choosing windows. Well-insulated windows with low-e coatings that block solar heat gain help lower heating and cooling costs almost as much in New Mexico as they do in New Hampshire.
Price ranges are harder to pin down within various window categories. With technological advances in every area, from frame to glass to function, and a new emphasis on energy efficiency, performance and prices range widely. In general, though, vinyl tends to be the least expensive, followed by fiberglass and composites, with clad wood remaining the highest-ticket option. But there are exciting new outliers in every category.
Step 1: Choose a function
The options for window function are often tied to their size. For instance, if your design calls for large expanses of glass, it could limit your options for frame material, and whether those windows can open and close. That’s because some materials are too flexible to support a very large, heavy window that hangs on hardware. On the other hand, if you make your largest windows fixed, you’ll have a wider range of choices for the frame and glazing, and are likely save money at the same time.
Tilt-turns are an exciting new option
If your windows face a porch, deck, patio, or path, where an outswinging casement window would pose a safety hazard, you might consider the latest tilt-turn models, popular in Europe for decades but only now making major inroads in North America. Thanks to clever engineering, these windows can tilt backward like hopper windows, opening at the top to let hot air escape, or swing in sideways for stronger breezes and easy cleaning. Their robust hardware also means that tilt-turns can support more glass than other swinging models.
The perks of a fixed frame
Aside from heat and cold radiating through the glass, the largest loss of efficiency happens around the edges of a window sash, in the form of air leakage. The best option is to have no edges at all, just one more advantage of picture and detail windows. Fixed windows are also the least expensive, all other things being equal. So where four double-hung, double-pane windows might cost $2000, one single, fixed, very high-performing European triple-pane window can cover the same square footage at the same cost, while delivering two or three times the comfort and energy efficiency. That’s partly because triple-pane glass is so cheap overseas, due to longstanding use.
Swingers beat sliders
When it comes to the rest of the windows in the house—the ones that need to open and close—swinging and tilting windows have a big advantage over those that slide. Window sashes that tilt or turn to open can be drawn tightly against their seals, while sliding windows can’t. Another advantage to windows that swing outward is easier access to screens, which are attached on the inside. If you want a more traditional look, almost all windows, sliding or swinging, are available with internal or external grilles in a variety of styles.
Sliding windows for a traditional look
Windows that slide have simpler hardware and cost significantly less. And for some traditional home styles, vertical sliders (called double-hungs or single-hungs) are a must-have for a cohesive design (and happy neighbors in a historic district). Today’s models often tilt inward for easier cleaning. Single-hung models are usually limited to less-expensive builder-grade models, as the fixed upper sash is hard to clean and limits ventilation.
Step 2: Pick a material
Your next decision is what the window is made of; specifically, the sash and frame. Technically, the frame is what attaches to the house, and the sash holds the glass, but both are frames in the general sense. These two frames are usually made with the same materials and a similar anatomy, which have a big effect on everything that matters about a window: durability, function, looks, sightlines, and thermal performance.
Vinyl ranges from low to high
Low maintenance and generally low in cost, vinyl windows dominate the marketplace. Some manufacturers, like Milgard, offer color finishes, but vinyl is largely available in white only.
While low-end models are still prone to some of the problems associated with the first vinyl windows sold in North America—typically related to seasonal movement—all vinyl windows perform better now than before. And on the premium side, new technologies borrowed from Europe have boosted performance to unprecedented levels.
The transformation starts with better materials. The latest formulations are less prone to UV damage, lasting many more years before they become brittle or oxidize and turn chalky. This has greatly extended the warrantees manufacturers offer on vinyl windows, which also means less impact on landfills.
Anatomies have improved, too. With multichamber construction and reinforcing rods, today’s premium products are much more rigid, stable, and energy efficient than old ones.
As they have been in Europe for decades, very high-end vinyl windows with triple-pane glass and thermal performance well above R-5 are now being made in North America as well, by companies like Logic and Ventana. The very best models have dry seals around the glass (vs. silicone that goes on wet), letting the frame expand and contract without compromising airtightness. But these very high-end products are also among the most expensive windows on the market, spreading vinyl’s price curve wider than any other material.
Even at the high end, though, vinyl has drawbacks. Its thick frames and welded joints look plasticky at close range. And vinyl’s probable lifespan still tops out around 25 years for premium models, which is less than some other window types.
Fiberglass offers unmatched value
Pultruded fiberglass is the same supertough material used in boat hulls and safety helmets. At prices just a tad higher than premium vinyl, all-fiberglass windows offer similar thermal performance, longer life, and smoother operation. Fiberglass also offers great value as a cladding over wood windows, though profiles are not as crisp as aluminum can deliver. Much stronger than extruded vinyl, all-fiberglass sashes can be thinner by comparison, yet support larger glass assemblies and excel in high-wind areas and coastal zones. Due to their thin frames, some fiberglass windows do not offer triple-pane glass. Fiberglass is also paintable, either at the factory or later, meaning it’s available in a wide range of colors inside and out. Like wood and unlike vinyl, fiberglass has a stability almost identical to glass, which means that the seals around the glass are less likely to be compromised, and windows will slide and swing like new for many years.
Composites can be confusing
Designed to be more durable and handsome than vinyl windows, and at only a slight premium, composite frames are usually a blend of wood chips and molten vinyl, similar to composite decking. Some composite units include fiberglass and are marketed as such, but these lack the performance of true fiberglass. While composite windows deliver the low maintenance and thermal performance of vinyl with durability similar to true fiberglass, they are priced closer to fiberglass without the same strength and stability. Due to the PVC binder, composites expand and contract more than the glass unit inside, threatening the seals over time. Most composites also lack fiberglass’ and reinforced vinyl’s ability to support larger moving windows. And like vinyl, composites are not paintable.
Wood has unmatched appeal
Wood is still one of the priciest options, but it pairs nicely with natural wood trim and boasts crisply milled profiles.
Like fiberglass, wood has excellent stability along its length, with minimal expansion and contraction, meaning the seals around the glass unit should stay intact over many seasons. Wood’s thermal performance is also good, as are its durability and strength, due to time-tested joinery methods that have been perfected over centuries.
While all-wood windows might seem like a maintenance nightmare, they still have their place in historic homes, as well as in some high-performance designs, where thick, thermally broken wood frames are often inset.
For everyone else who wants wood inside, cladding is the answer. Many manufacturers cap wood windows with vinyl, fiberglass, composites, or aluminum. Fiberglass wins the day on price and value, and aluminum is favored for its crisper profiles, which can closely match the wood-molding profiles on a historic home.
Aluminum, a dying breed?
Once popular as a low-cost, low-maintenance option, extruded-aluminum windows are almost gone from the U.S. market, replaced by vinyl models for builders and homeowners on a budget. That said, a few well-insulated, high-end aluminum windows are still hanging on. With unmatched strength-to-weight ratios, aluminum is still the frame of choice for very large windows in some designs. When his low-energy homes in Maine call for big expanses of triple-pane glass, designer/builder Michael Maines turns to aluminum windows from Schüco, and in Texas, custom builder Matt Risinger uses double-pane aluminum windows from companies like Fleetwood.
Step 3: Get good glass
There is big news in the world of glazing, too. Glass units are manufactured by just a few companies, making them less proprietary than window-frame anatomies, for example, and more of a commodity. That’s good news for consumers. As energy-efficiency expectations have climbed, glazing has improved dramatically with once-costly elements coming way down in price, and with lower-priced options now standard.
Double-pane or triple-pane?
While double-pane glass is the still norm, triple-pane glass is on the rise. Once very costly, triple-pane glass was hard to justify over the life of a window in all but the most frigid zones, with energy savings never quite matching the price of the initial upgrade. So the conventional wisdom was to spend those dollars on the rest of the house’s shell, where they would go much further.
But triple-pane glass has comfort benefits, and continues to gain popularity despite the high cost. As demand has gone up, so has supply, and prices have dropped. The same goes for energy-efficient gas fills between panes, and suspended films that can make two panes perform like three, without the added weight.
Today, the upgrade from double- to triple-pane glass can be as low as $50 to $100 for a standard-size double-hung window, which is much easier to justify over the life of the home.
On the other hand, triple-pane might be overkill in more moderate climates, where you’d be better off spending your window upgrade dollars on the airtightness of a casement, or just choosing a better window overall.
Low-e has become standard
Once a premium option on premium windows, low-e glass coatings are now standard on high-quality windows in the U.S. As one builder put it, if your window dealer asks if you want low-e, just walk out.
Low-e coatings block UV rays without affecting overall light, using superthin metallic layers that resist infrared light yet are transparent to the eye. This not only reduces solar heat gain, as well as transmission of heating and cooling to the exterior, but it also keeps your carpets and furniture from fading in the sun like they once did.
The NFRC label: Behind the numbers
The good news about choosing energy-efficient windows is that much of the work has been done for you, and the results are posted on every window sold in the U.S. In 1993, the National Fenestration Ratings Council (NFRC) developed the first universally adopted method for evaluating the energy performance of windows, along with an info-packed ratings label. Here’s what the numbers mean
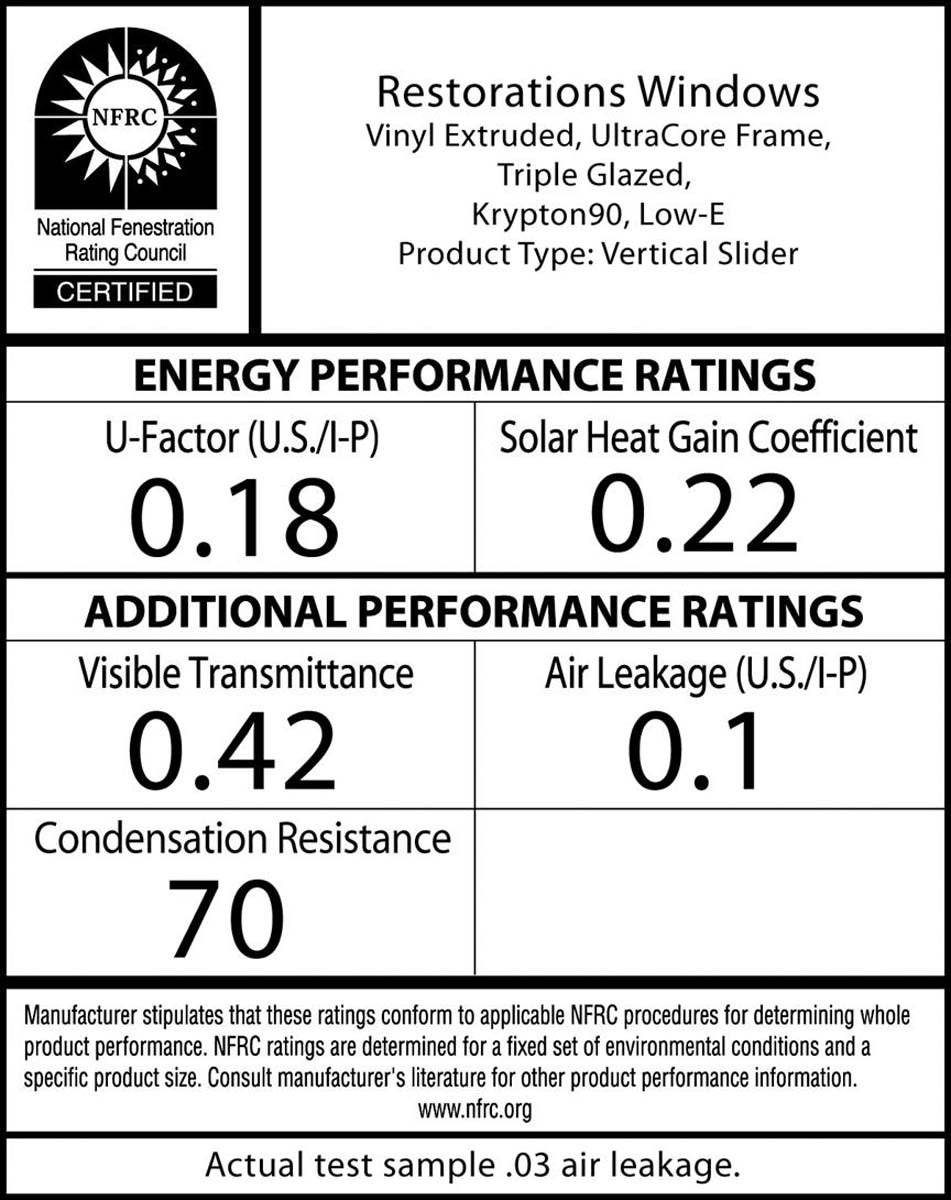
U-factor is the most important rating for a window, and measures the heat transmission of the entire window unit, from the glass to the frame to the air that slips by the sashes. The U-factor is similar to an R-value for insulation, but the inverse, so a lower number is better. For instance, a window with a U-factor of 0.33 is equivalent to R-3. To figure out an ideal U-factor for your next home or remodel, architect Steve Baczek recommends a 1:7 to 1:8 ratio. So, if the walls are R-30, your windows should be roughly R-4, or U-0.25. U-factors also measure how well a window keeps heat out, making them almost as important in cooling climates as they are in heating climates. U-factor is also affected by air leaks and the emissivity of the glass, so it’s more of a universal window rating than the other numbers.
The solar heat-gain coefficient (SHGC) is the percentage of the sun’s heat that will radiate through. In general, and especially in the sunny south, aim for a SHGC of 0.3. The main exception is south-facing windows in cold climates, where a higher SHGC is preferred.
Air leakage (AL) ratings are expressed in cubic feet per minute through 1 sq. ft. of window, and low numbers are better than high. Generally, air leakage is higher for sliding windows than ones that pull closed, such as casements.
The visible transmittance (VT) is a rating of how much light gets through the glass, on a scale of 0 to 1, which is important when designing for natural light.
Condensation resistance (CR), rated on a relative scale ranging from 0 to 100, ranks the likelihood of moisture forming on the interior of the glass—a situation common to cold glass in warm rooms. Higher numbers mean less likelihood of condensation.
Click here for other great articles about windows.
For more photos and information related to this article, please click the View PDF button below.