Will Vinyl Windows Last?
They don’t have the track record of wood windows, but chosen and installed with care, modern vinyl products can compete.
Synopsis: It is easy to see why vinyl windows now make up about two-thirds of all window sales in the United States: They are less expensive than wood, they are impervious to moisture, they don’t rot, and they don’t need to be painted. In this article, contributing editor Martin Holladay addresses the important issue of how vinyl windows will look and perform when today’s homes become historic. He states that vinyl windows are better made than they were 30 years ago, attributing this in part to a certification program launched in 1985 by the American Architectural Manufacturers Association. In order to become certified, windows must pass tests for impact resistance, dimensional stability, heat resistance, weight tolerance, and colorfastness. Still, a window is only as good as its installation and maintenance, so Holladay provides a list of tips to help ensure that these windows perform as they are designed to do. Finally, Holladay explores the three phases of vinyl-window construction—formulation, extrusion, and fabrication—and takes a look at vinyl-clad windows.
In many American neighborhoods, houses that are more than 100 years old still have their original double hung wood windows. Although long-lived, wood windows have some drawbacks: They need to be repainted regularly (a complicated chore, because old layers of paint usually contain lead), they have energy wasting single glazing, and they are difficult to seal against air leaks.
Because of these drawbacks, many homeowners have abandoned their historic windows in favor of double-glazed vinyl replacement windows. The advantages of vinyl windows are fairly appealing: They are less expensive than wood, don’t absorb moisture, don’t rot, and don’t need to be repainted. These advantages are largely responsible for vinyl windows’ share of the current U.S. window market, which has grown from 24% in 1990 to about 66% in 2010.
Vinyl windows do, however, have drawbacks. They are difficult to repair; they are available in a limited number of colors that can’t be repainted as styles change; and according to Consumer Reports tests, the average vinyl window leaks more air than the average fiberglass or wood window.
With so many houses now being fitted with vinyl windows, a burning question is beginning to surface: How will these modern vinyl windows look and perform when today’s homes become historic?
Manufacturers’ warranties are driven by marketing rather than logic, and window experts are cautious with their predictions. The relatively short 40-year history of vinyl windows provides only limited data, and our need for long-lived windows must be balanced against practical considerations, including the ever-changing demands of consumers, building codes, and energy guidelines. If vinyl windows have been specified for a project, the best option is to choose a top-quality model and install it impeccably.
Better windows through stricter guidelines
Ever since vinyl windows were developed in the 1970s, they have been subject to a certain amount of derision. According to Gene Summy, a window expert and president of TLS Laboratories in Laguna Niguel, Calif., much of this scorn is unmerited. “When vinyl windows first came out, a lot of the so called experts said that vinyl was nothing but a liquid in a solid state, and that they were destined to crack and fall apart,” Summy recalls. “But I have not seen any of those predictions become a reality. As long as the windows aren’t abused or misused issues that would affect any window they will provide a long, useful life.”
Vinyl windows have been proving skeptics wrong due in part to a window-certification program launched by the American Architectural Manufacturers Association (AAMA) in 1985. Since its inception, the certification program also has been embraced by almost all U.S. vinyl-window manufacturers. The program has been endorsed by the International Residential Code, which now requires vinyl windows to be certified.
To obtain AAMA certification, a vinyl window must be made from vinyl extrusions that have survived a battery of tests performed by an accredited third-party laboratory. Tests include impact resistance, dimensional stability, heat resistance, weight tolerance, and colorfastness. The extrusion samples also must survive outdoor-weathering tests for at least one but in most cases two years. Assembled windows are also tested for structural performance under wind loading, as well as for resistance to air leakage, water penetration, and forced entry.
Today’s vinyl windows are better made than the windows of 30 years ago. “In the late ’70s and early ’80s, there were a lot of vinyl windows with mechanically assembled corners,” says Kevin Seiling, vice president of engineering at Veka, a vinyl-window manufacturer. “Back then, the vinyl compounds may have had less impact resistance. But since the AAMA certification program was established, the quality of vinyl windows has gotten pretty good.” Sean Flanigan, a research-and-development engineer at Paradigm Window Solutions in Maine, agrees. “Some manufacturers formerly used materials with lesser amounts of the additives needed to control weathering and to provide UV-resistance. With AAMA certification, though, there is definitely a change.
Although it’s hard to predict the service life of today’s vinyl windows, Seiling points out that many people replace windows before they are worn out. “It’s possible that today’s vinyl windows could have a 50-year life,” he says. “But the insulated-glass technology is changing so fast that in 50 years, you’d want to change your glazing anyway.”
Paul Adams, director of materials research for vinyl-extrusion company Deceuninck North America, is more conservative with his forecasting. “I think these windows will last 35 years or more,” he says.
Shopping for a quality window
Unfortunately, warranties aren’t much help in figuring out which companies have faith in their products’ long-term performance. Most window warranties include lots of exclusions. Paradigm’s warranty doesn’t cover problems from normal weathering caused by exposure to the elements, and Interstate Building Systems’s warranty specifically excludes problems arising from normal weathering of the vinyl surface. Alside’s warranty doesn’t cover problems caused by oxidation or problems due to “stresses resulting from localized heat sources which cause excessive temperature differentials over the glass surfaces or edges,” or problems that arise from the normal weathering of sash frames and the main frame.
Warranties aside, there are two excellent reasons to purchase windows from a major manufacturer rather than a small local outfit: Large manufacturers are more likely to have invested in expensive corner-welding equipment, and they are more likely to remain in business if you ever need service.
Finally, it’s worth noting that fiberglass windows usually outperform vinyl windows. Pultruded fiberglass has improved resistance to UV-light, a lower coefficient of thermal expansion, and much greater stiffness. Of course, these performance advantages come with a higher price tag.
Only as good as the installation
Even the best window will suffer if installed poorly or maintained carelessly. For the best results, consider this checklist of important notes:
- Vinyl becomes brittle when cold, so cold-weather installation requires care. Because a poorly aimed blow with a framing hammer can ruin a window, it’s often advisable to install windows with screws or a pneumatic nailer.
- In hot weather, store vinyl windows carefully before they are installed. If you lean them against a wall in the hot sun, their frames can warp.
- Never paint a vinyl window; dark-colored paint is especially dangerous because it can cause the window to overheat and soften.
- Shallow scratches in vinyl windows can be rubbed out with light steel wool or fine emery cloth. Deeper gouges often can be repaired with a liquid vinyl product called Stelmax Gap Filler, although it’s best to contact the window manufacturer before attempting job-site repairs.
- Because of vinyl’s high rate of thermal expansion and contraction, be sure that the rough opening is sized to allow movement. A 6-ft.-wide vinyl window can expand about 1⁄4 in. from winter to summer, so it’s important to leave a gap between the window frame and the siding.
What is vinyl-clad?
These days, window manufacturers are building a variety of hybrid windows that combine materials in new ways, so it’s harder than ever to divide residential windows into clear categories like “wood windows,” “aluminum windows,” and “vinyl windows.”
One of the most common hybrid options is the vinyl-clad wood window. From the exterior, it’s often difficult to tell the difference between a vinyl window and a vinyl-clad wood window. If you look at the interior, however, the difference is obvious.
In most cases, a vinyl-clad wood window is a conventional wood window with thin (0.03-in. to 0.05-in.) vinyl cladding protecting the exterior. The purpose of the vinyl cladding (like aluminum cladding) is to reduce the need for frequent repainting of exterior window components. At least 93% of all wood windows sold in the United States are now partially protected with either aluminum or vinyl cladding. Although vinyl cladding is available in a more limited range of colors and is more susceptible to shattering in cold temperatures than aluminum cladding, it has a few advantages over aluminum: Its seams can be welded, it resists corrosion from salt spray, and it is less conductive. In terms of expansion and contraction, though, treat a vinyl-clad window the same as a wood window, because at the core, that’s what you have.
3 phases of vinyl window construction
Formulation
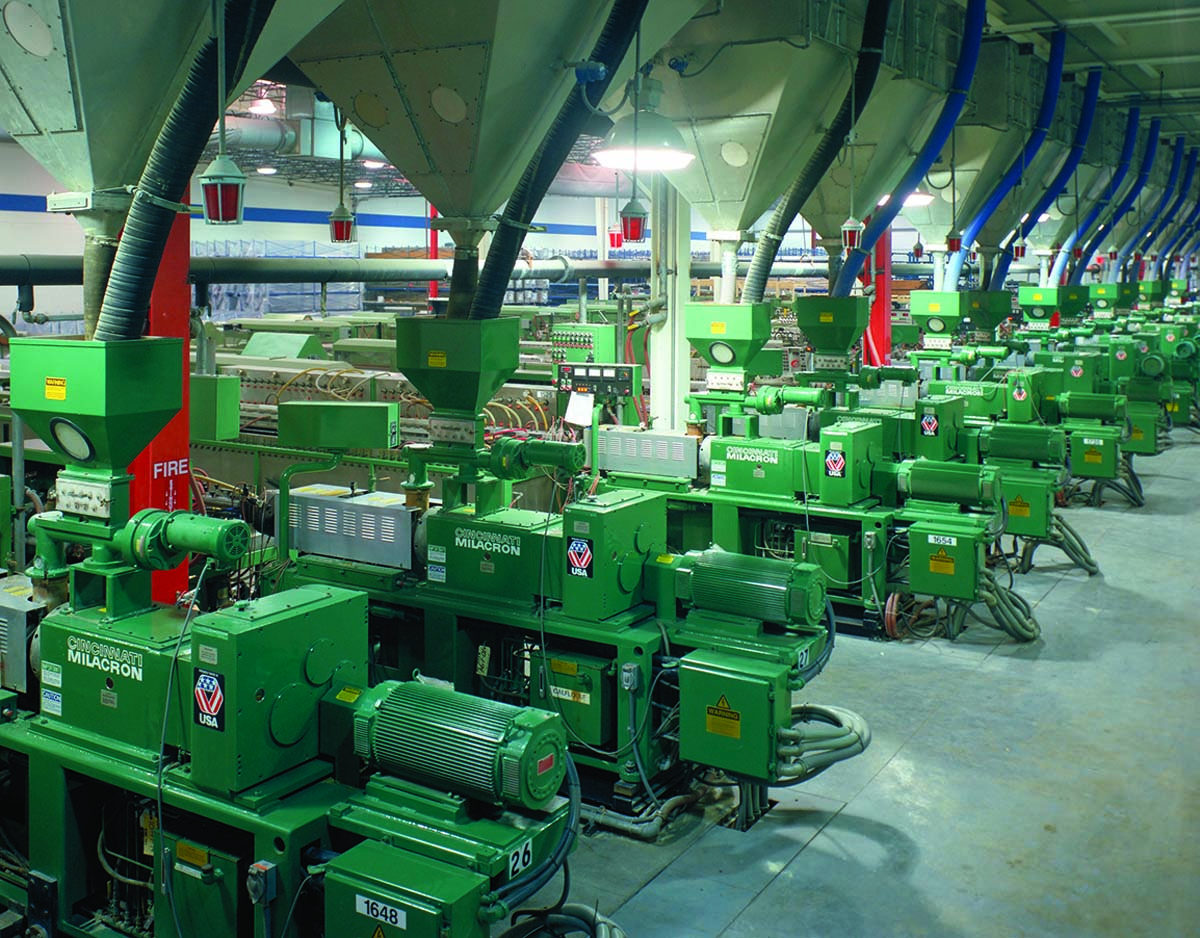
Manufacturing begins with the formulation of the plastic compound used to make vinyl extrusions. The compound consists of 80% to 85% PVC pellets mixed with 15% to 20% other ingredients, including heat stabilizers such as organo-tin mercaptides and a pigment (usually titanium dioxide) that helps to protect the vinyl from the harmful effects of UV-light (photo below).
Because these additives are relatively expensive, extruders are always striving to achieve a balance between durability and price. When I last reported on vinyl windows over a decade ago, I spoke with Kevin Jones, vice president of Dallas Laboratory, one of the third-party labs that reviewed test reports for the American Architectural Manufacturers Association (AAMA) certification program. At that time, Jones told me, “Some compounds are better than others. Some plants might produce inconsistent vinyl. In the weathering tests, we have seen some white vinyl that has gone brown, and some light browns that have gone chalky.”
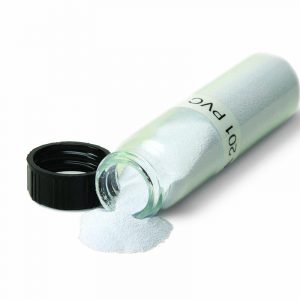
Fortunately, these low-quality vinyl compounds are usually weeded out by the AAMA test protocol. “In the course of the past 15 years, the PVC hasn’t changed, but there have been major advances in the additives,” explains Paul Adams of Deceuninck North America. “The formulations are different from what they were even five years ago. The stabilizers have improved. Each category of additives has improved.”
According to Kevin Seiling of Veka, window buyers don’t have to worry about the quality of the vinyl used to make today’s windows. “If the profiles are made from an AAMA-certified compound, there really aren’t any substantial differences between the different compounds used by manufacturers,” says Seiling.
Extrusion
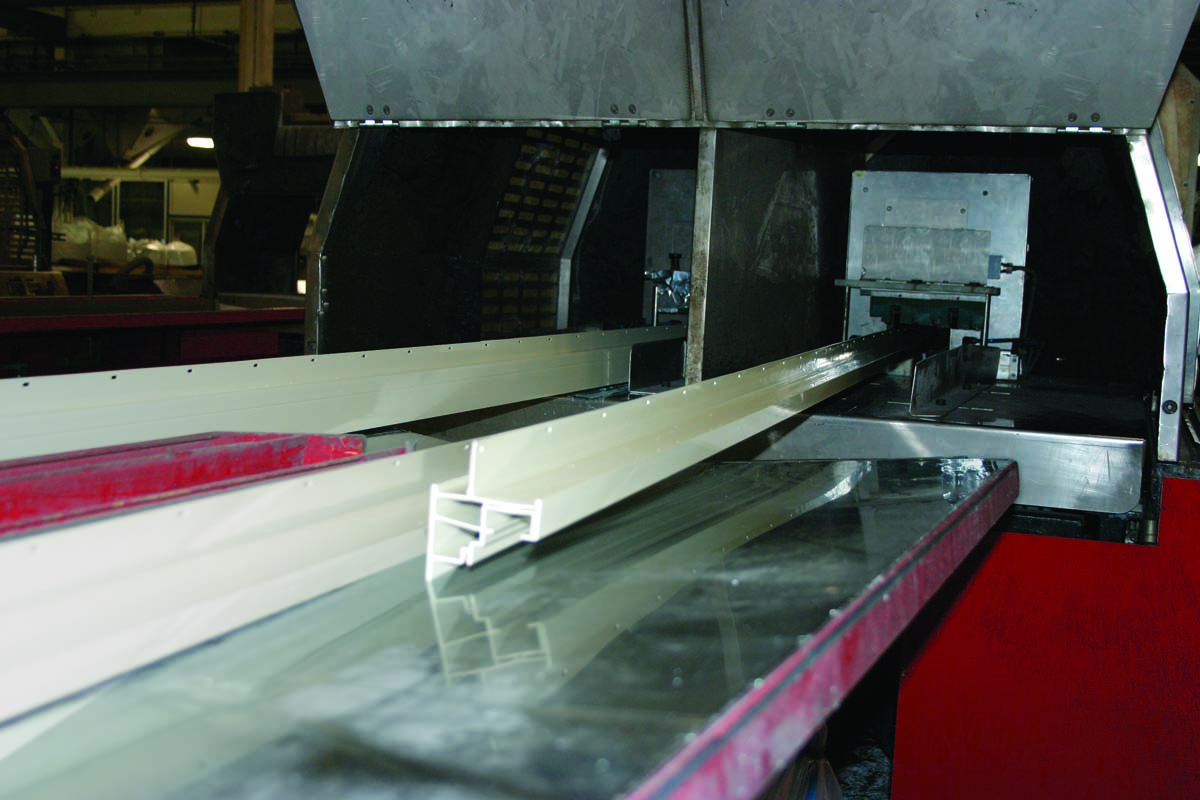
Vinyl extrusions (also known as profiles or lineals) are made by forcing hot PVC compound through a die. The resulting extrusion is a long, rail-like piece of plastic that includes webs and voids to provide rigidity (photo left).
Extruders keep prices low by manufacturing profiles with thin PVC walls. While European window profiles have a wall thickness of 0.125 in., U.S. profiles have much thinner walls, usually only 0.06 in. to 0.09 in. thick.
Extrusions with thicker walls are stiffer, but that doesn’t necessarily mean they will be more durable than thin-walled extrusions. “The European community regulates windows by the wall thickness of the vinyl profiles,” says Seiling. “They set minimum profile-wall thicknesses. But profile-wall thickness has very little bearing on longevity.”
Sean Flanigan of Paradigm Window Solutions agrees. “Durability is not related to wall thickness,” he says. “But wall thickness does make a difference when you are looking at structural performance.” According to Flanigan, the reason that European manufacturers use profiles with thicker walls is simply because European windows—generally tilt/turn units—operate differently from U.S. windows. Like casement sash windows, tilt/turn sash units need to be stronger than double-hung units, which always stay within their frames.
Fabrication
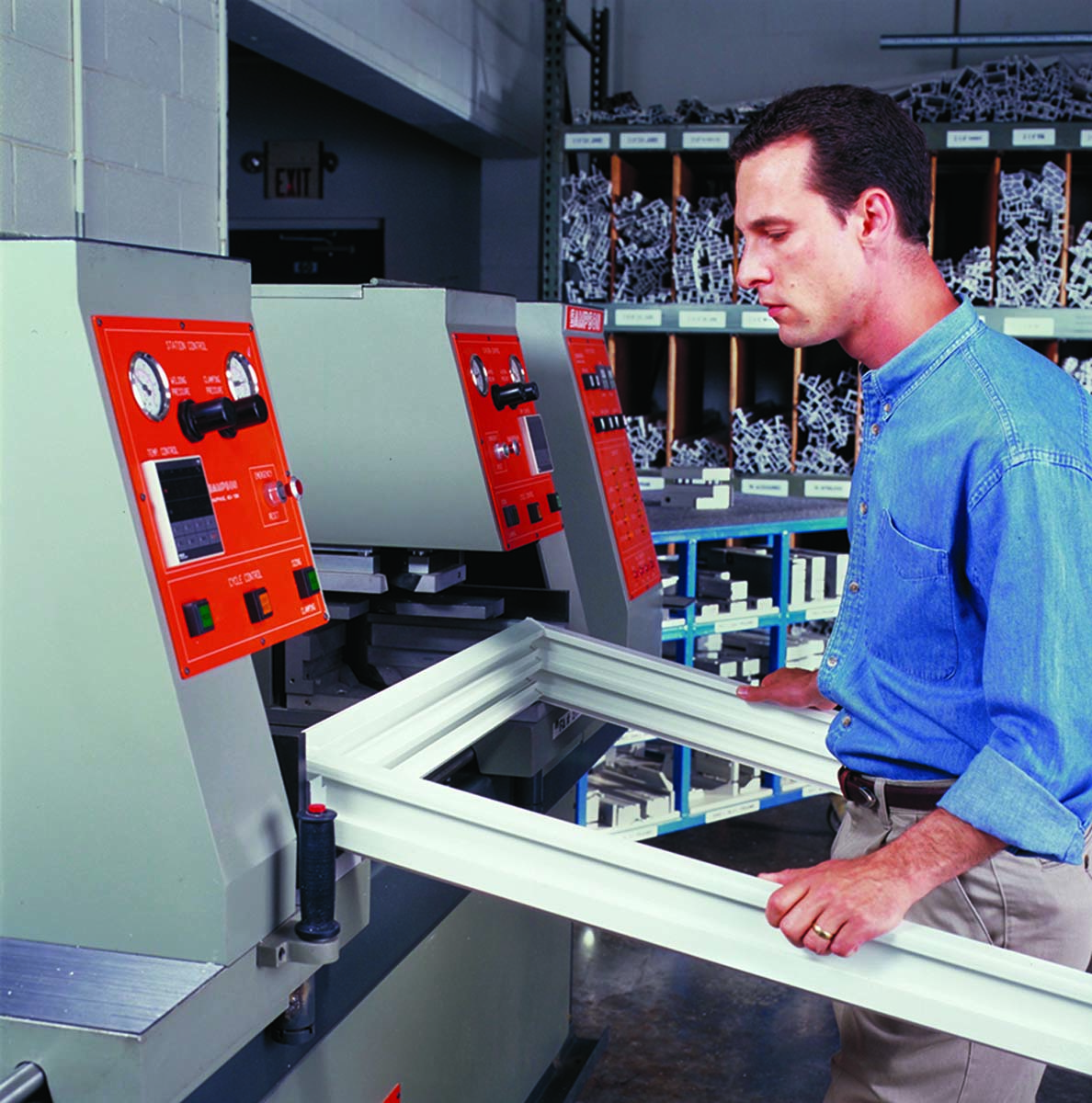
While the largest manufacturers may make their own profiles, many buy profiles from extruders. These long extrusions are then cut to size and joined together to make sashes and frames (photo above).
Mechanically fastened corners are still sometimes used, but most large manufacturers weld the corners of vinyl sashes and frames, a method that is both stronger and more watertight.
Ordinary unreinforced vinyl extrusions are stiff enough to make small sash and window frames, but large windows need steel or aluminum reinforcement to prevent bowing or sagging. Window manufacturers reinforce vinyl profiles by inserting pieces of metal into hollow sections of the profiles before the windows are assembled. Although metal reinforcement improves the strength of a vinyl window, it usually decreases thermal performance slightly.
“The biggest concern out there is a property of many plastics called creep: If you apply a load to the vinyl over time, it might deflect and stay in that shape permanently,” says Flanigan. “That’s one reason why manufacturers use reinforcement. Steel is better thermally and stronger than aluminum, but aluminum is easier to process. The U-factor of the vinyl is skewed a little bit by the aluminum reinforcement, but for typical windows, it doesn’t seem to be that big a deal. As you approach U-factors below 0.25, the aluminum becomes a much bigger player. Vinyl extruders are now working on reinforced composites to replace aluminum.”
Although hollow vinyl profiles (including reinforced profiles) can be insulated with foam, few window manufacturers bother to do so. “Most profiles can be foam-filled, either with expanding foam or by inserting die-cut foam that slides into the chamber,” says Seiling. “But the overall window U-factor is lowered—that is, improved—by only about 0.04 when you fill the profiles with foam.”
For more photos and details on the longevity of vinyl windows, click the View PDF button below.
View Comments
Wonderful house design