Most of this roof was stick framed, except for a section of flat top trusses to span the width of the front room which was around 38′ wide. All stick framing had to tie in to the trusses with hips, valleys and the largest barrel which was over 16′ wide. The ribs for the barrels were two plies of 3/4 CDX plywood, manufactured on site. Typically, these would just progress up between two built up common rafters. In the case of the barrel framing pic, the ribs had to tie into a hip and valley as I worked toward the top, making it tricky to maintain a true centerline.
Up Next
Video Shorts
Featured Story
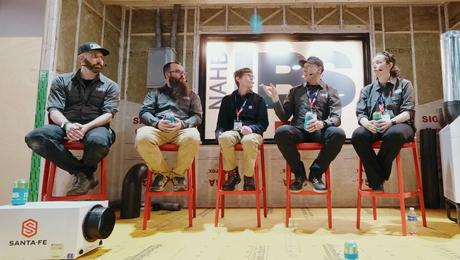
Tune in for part two of Patrick's conversation with the BS* + Beer crew at this year's International Builders' Show.
Discussion Forum
Highlights
"I have learned so much thanks to the searchable articles on the FHB website. I can confidently say that I expect to be a life-long subscriber." - M.K.
Fine Homebuilding Magazine
- Home Group
- Antique Trader
- Arts & Crafts Homes
- Bank Note Reporter
- Cabin Life
- Cuisine at Home
- Fine Gardening
- Fine Woodworking
- Green Building Advisor
- Garden Gate
- Horticulture
- Keep Craft Alive
- Log Home Living
- Military Trader/Vehicles
- Numismatic News
- Numismaster
- Old Cars Weekly
- Old House Journal
- Period Homes
- Popular Woodworking
- Script
- ShopNotes
- Sports Collectors Digest
- Threads
- Timber Home Living
- Traditional Building
- Woodsmith
- World Coin News
- Writer's Digest
View Comments
That's a roof that would raise a few eyebrows!
(sorry, couldn't resist!)
I believe mine may have been the first raised Huck. I had done a few barrels and eyebrows previously, but not any that required more than an 8' sheet to get the width. I think the final sheet count to complete these barrels was about 110.