Making Modular-Home Building More Efficient
High-quality products are helping to revolutionize modular construction.
Sponsored by USG
Tag along as Aron Jones of Big Dog Construction makes a special visit to the Champion Homes Strattanville, PA factory where USG Sheetrock® Brand UltraLight Panels and USG Sheetrock® Brand MH UltraLight Panels Tuf-Base™ help make the modular-home building process successful.
Here’s the Transcript:
Aron Jones (AJ): I’m here today in Strattanville, Pennsylvania, to see Champion modular homes and their partnership with USG.
Erik Kriebel (EK), Assistant Production Manager: This is the beginning of it, where everything starts with the houses.
AJ: The first thing I noticed is it’s dry in here.
Mark Kriebel (MK), Materials Manager: It’s climate-controlled, which is one of the advantages of building inside.
Greg Baumcratz (GB), Sales Manager: Modular houses are built in a controlled environment, allowing us to build a house quicker, more efficiently. We can also control the entire process from start to finish, versus a stick builder out in the field dealing with material delays, weather delays, and things of that nature.
EK: Down here is the actual floor-framing process.
AJ: Built over there, the crane picks it up, and we set it here. Can I play with the crane?
GB: We have a whole network of vendors bringing materials into the factory. We have great partnerships like USG that allow us to streamline efficient builds for the houses.
AJ: You’re framing on an elevated platform with 54-in. UltraLight Sheetrock® panels. What’s the installation process for that?
MK: It’s pretty simple: You just slide it right from the cart onto the actual wall. We’ll put our adhesive on the studs. The drywall is ultralight — way lighter than your standard drywall. Once the wall is built, the crane picks it up and puts it into the holding rack.
AJ: Can I use the crane to lift the wall?
MK: I’m afraid not.
AJ: So USG will custom-cut drywall to a specific length, whatever your clients needs are?
Cameron Kemp (CK), USG Technical Sales Specialist: Correct. Depending on what size of wall system or ceiling system they’re building, we can actually make a specific size, not just the standard 8s, 10s, or 12s. This allows them to put board up with less cuts on the wall, less butt joints, and less taping, which means the unit is going to move down the line a little faster.
MK: The two stations we walked past here are the drywall hanging station and the finishing process — the mud.
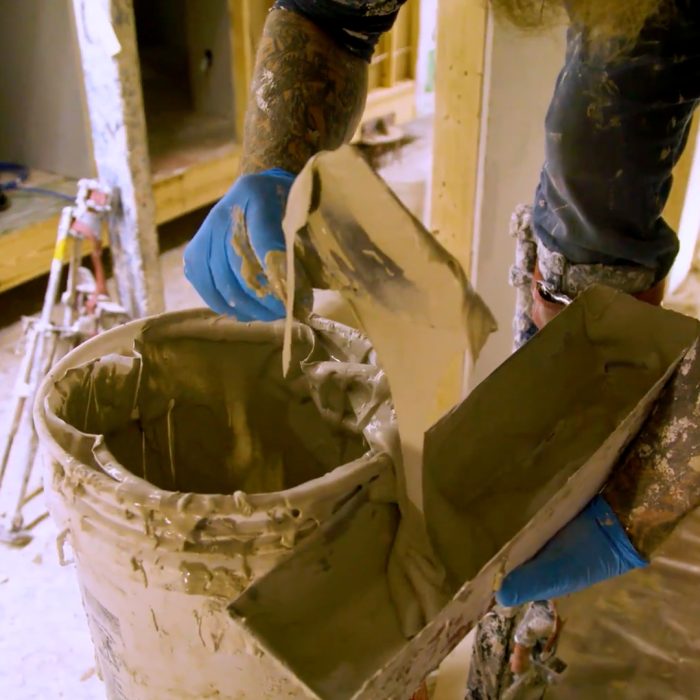
EK: And it’s all USG.
AJ: You guys make a pretty special compound for the modular industry.
CK: We have a product called Tuf-Set™ HES (high early strength). It comes in 20-, 45-, or 90-minute set times. As the guys are moving units down the line, this allows them to move without having any cracking down the line. Because of that early set time, it actually gives them some strength.
AJ: So you’re just making everybody’s lives easier?
CK: The name of the game is to have the quality that is involved in it as well as to access the speed to move these products down the line.
MK: Everything’s happening at one time. Your taping, your second coating, and some may even be doing a third coat. Using USG brand offers the ability to go fast.
GB: You have butt joints, end joints, you have nail holes, so we use different compounds at different steps of the process so that we can basically get those dry and sanded faster to get it moved on to the next station.
AJ: So it sounds to me like USG is a pretty important part of the daily things that happen here.
GB: Yeah, very crucial. I’d say 75%, give or take, of our line is strictly drywall — whether they’re hanging, mudding, or finishing, it’s the biggest part of what we do here.
AJ: It’s an important part because once you’re in your home, what do you see every day? You see your walls, you see your ceilings, so having a nice finish — that’s really important.
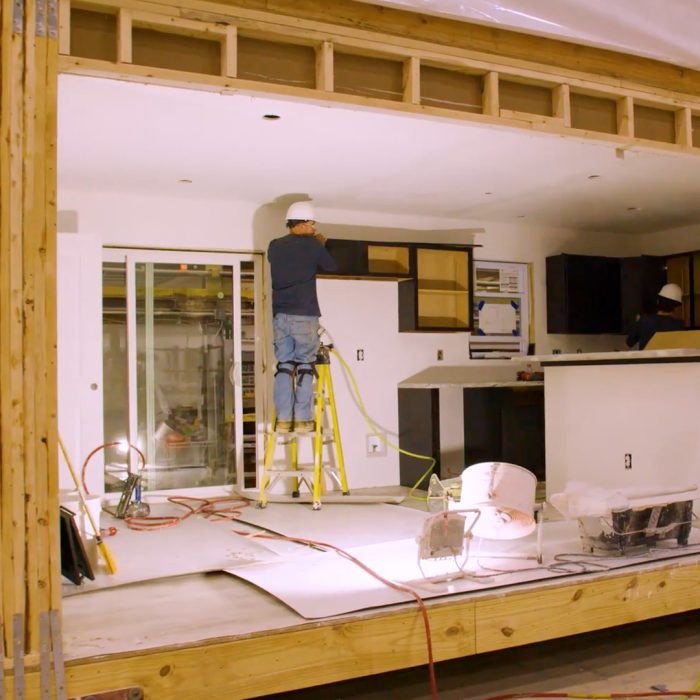
MK: This is the final stage. The house has the trim on the windows and the doors. You have your shower fixtures installed, any cleaning that might need to be done, final touch-up, and it’s done.
AJ: So if I start digging a hole today and I order a house from Champion Homes, how soon could you have a house ready for me?
GB: A good time frame is usually about 6 to 8 weeks. You can be putting your foundation in the ground as we’re building your house on the line.
AJ: So I could order a house from you while I’m still in the permitting process?
GB: Absolutely. As soon as retailers and builders get permits, they usually are ordering the house as soon as that permit’s applied, and then we get into our schedule to meet their time frame on-site.
MK: You have a carrier that the house is shipped on. They’ll back it in, they’ll drop the house down onto it, and the house gets lagged to that carrier ready for shipment.
AJ: Can I set the house down?
MK: Can’t set the house down, Aaron.
AJ: Modular’s been on a slow, steady climb for the last 20 years, and I think in the next 10 years you’re going to see a dramatic spike in the amount of modular. We are facing a labor shortage. We’re already in a housing shortage. Modular is going to allow us to meet some of those demands. The other thing is efficiency. We can produce more affordable houses with less waste and hopefully bring them to market in a much more timely fashion.
AJ: What, in like half an hour, they’re going to roll that carrier underneath here?
MK: I would say roughly a half hour, 45 minutes, and it’s ready for the customer.
RELATED STORIES
View Comments
I am amazed that so much of the construction is by humans rather than by assembly line automated systems and robots. I think that is good for the workers and the communities in which they live. But I suspect that in the future modular building companies will turn more toward automated systems and robotic production lines. I also think that panelized construction of larger and wider homes will compete with modular home builders that produce more complete boxes. Finally, I hope modular builders will be able to produce much more energy efficient designs.