Structural engineers are concerned with various types of loads, the main ones falling into the categories of gravity loads and horizontal loads. A third category is uplift, which also relates to the first two.
Gravity loads include the dead load of the lumber and other material that is part of the building; live loads include occupants, snow, furniture, or other temporary loads. The simplest way to calculate loads is to simply add up the worst case: the full dead load of the building, plus a fully occupied space (typically 40 lb. per sq. ft. for residential living spaces) plus, in the case of a deck or roof, the full snow load.
Horizontal loads primarily include wind and seismic loads. I have almost always worked in New England, which is in Seismic Category B; we get occasional small earthquakes, and I have heard that on a geological timescale we may be due for a “big one,” but in practical terms we don’t have to worry too much about earthquakes shaking our buildings into submission. Builders on the west coast and other seismically active areas have a whole other level of things to worry about.
What we do have in the coastal areas where I have mostly worked is wind. Not necessarily “Miami-Dade” wind, which is industry shorthand for the highest wind zone, where building have to regularly withstand 140 mph storms, but coastal New England is mostly in 100 or 110 mph zones, with some areas even higher, particularly hilltops or bluffs near the ocean.
Quick story: I never fully appreciated the power of the wind until my brother and I were putting the finishing touches on a rooftop “widow’s walk” deck on a Nantucket roof. It was a breezy day, as usual, but just as I picked up a full sheet of plywood we were using to protect the decking, a wind gust pushed me hard against the railing we had just finished. Fortunately, the railing held, saving me from a 30-foot drop, but it was a good wakeup call.
The way that wind at a given speed affects a building varies depending on the building geometry and topography, but there is a convenient chart, Table 301.2.2 in the 2012 IRC, that shows “component and cladding loads.” In other words, the wind pressure on the building at various locations. They break the pressures down into what are essentially small, medium and large areas, but the differences are not that significant in most cases. According to the chart, in a 110 mph zone, walls experience about 20 lb. per sq. ft., and closer to 30 lb. per sq. ft. at the outside corners (where the wind accelerates to get around the building, like air over an airplane wing). Both positive and negative pressures are listed. A steep roof like ours has similar wind pressure numbers to the walls.
The site topography can have a big effect on the effective wind speed. A house in a 110 mph zone near the top of a hill or escarpment with a moderate 10% slope will experience 120 mph winds. At 15% slope, it increases to 130 mph. Houses in a 110 mph zone near the top of a steep slope, like a lot of shorefront homes, see effective winds up to 150 mph.
The FHB House is in a 110 mph wind zone but in a fairly protected area, with tall trees and other homes on all sides, so topography is not a concern. The wind across the south wall and roof is pushing at roughly 500 pounds per liner foot along the 34 foot length of the house, or about 17,000 pounds in all. Considering the 24-foot depth of the house, there is no danger of it being pushed over by the wind; if you imagine a south wind pivoting the entire house over the north foundation wall, it would take less than 400 pounds per linear foot to hold the house down, easily met by the building’s dead load and a few anchor bolts. (That’s not to say that it’s a good idea to skimp on anchor bolts!) My own home, built in 1830, is still resting passively on dry-laid stone walls, but I have to say that I worry a bit when the wind really blows.
As we head up the exterior walls, though, there is less building material to resist the wind. At the lower edge of the roof, for example, the rafters can experience 240 pounds of uplift, minus the dead load of the roof framing and cladding, which is no more than 10 lb. per sq. ft., or a maximum of 120 pounds at each rafter seat cut. Add in another 65 pounds per rafter from wind blowing up against the soffit, and we have to worry about at least 185 pounds of uplift at each rafter. IRC 2012 table R802.11 shows similar values already worked out for a situation like ours, as well as other situations.
In building design, a 185-pound load is pretty small, but to visualize what the rafter seat cuts are “feeling,” imagine that you are a 185-pound person dangling from a very high wall. What connection would you feel comfortable trusting your life to? The IRC 2012 allows two 16-penny toenails as long as the roof does not experience 20 lb. per sq. ft. or more of uplift. While they may hold and prevent you falling to your death, what if the wood splits? I’m not being overly dramatic; that’s the responsibility you take on when you build a house. Personally, I would feel more comfortable with some additional metal up there, and because the FHB House is subject to greater than 20 lb. per sq. ft., we have to use additional hardware. While many people use hold-downs that are nailed to the wall’s top plate, I feel more confident going around the plates and attaching directly to the studs below. Simpson Strong-Tie’s H2A tie, properly nailed, contributes 495 pounds of resistance to uplift — easily enough for our situation.
Some jurisdictions require metal straps or ties to span across rim joists from floor to floor. Rhode Island allows 7/16″ sheathing, spanned 16″ beyond the joint, to serve as a hold-down. Is that really strong enough? Consider the same 185-pound uplift load. The method of failure would likely be either the nails pulling through the sheathing, the nail head separating from the shaft, or the sheathing itself failing around the nails. The 16″ of sheathing remaining at each stud should have at least four nails, breaking the load down to about 46 pounds at each nail. 8 penny nails can easily handle that load, and as long as they are not over-driven and the sheathing remains in good condition, the sheathing will not fail at that load either.
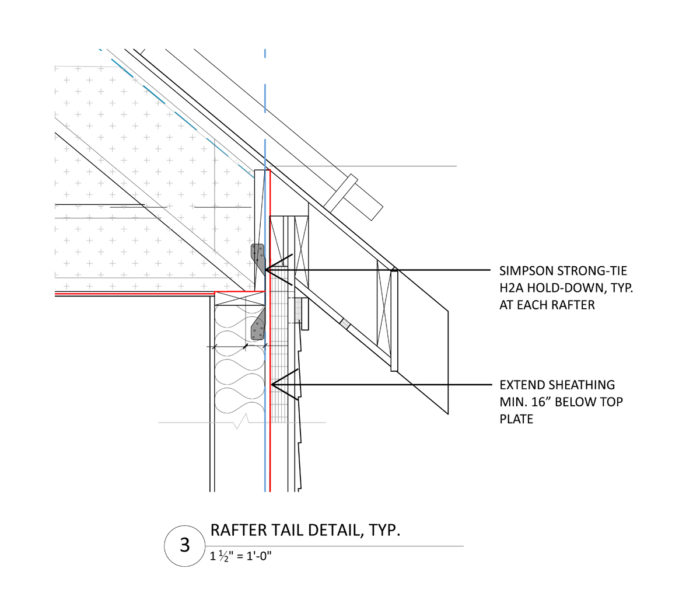
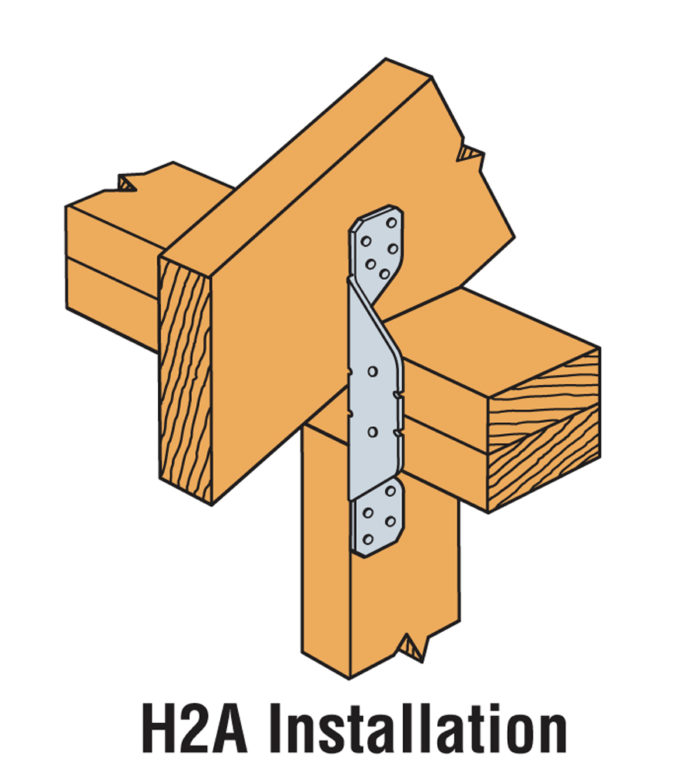
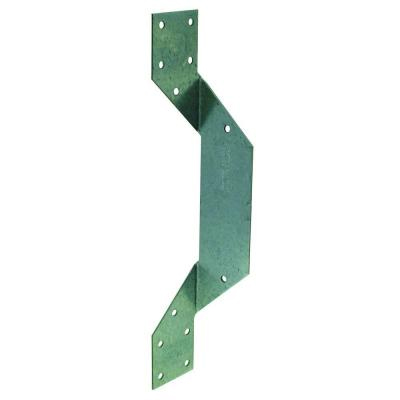
(Note: the numbers above are my own calculations for discussion purposes only; we had a licensed structural engineer do his own analysis for the FHB House.)
Fine Homebuilding Recommended Products
Fine Homebuilding receives a commission for items purchased through links on this site, including Amazon Associates and other affiliate advertising programs.
Protective Eyewear
Stabila Extendable Plate to Plate Level
Pretty Good House