Foundation Insulation Strategy
Our system has evolved as we've driven down costs while maintaining performance.
Like my head of hair, our foundations designs have changed over time. What once was full and blonde is now looking thinner with a few random grays, and what once was known as a standard foundation is quickly becoming obsolete.
While the various past designs we have used are energy efficient, not all were the most efficient in terms of cost, especially with how they would work for the FHB House. Reducing building cost is critical for this project as we are trying to meet existing home prices with new construction, but sacrificing energy efficiency is not an option. It’s situations like this that spur innovation and leave crews saying things like, “What in the world is this?”
Insulating Concrete Forms (ICFs) have been a go-to foundation system for us, but one disadvantage is the extra cost incurred to finish the exterior of the form that is exposed above grade. It doesn’t take long before a couple thousand dollars in labor and materials has been spent on a finish worthy of standing up to the elements. To overcome this, we moved the insulation to the interior of the foundation, thereby removing the cost to finish the exterior.
The 2017 FHB House has a slab-on-grade foundation comprised of footings, 4-ft.-high frost walls, and a slab. We installed 2 in. of foam on the interior side of the frost wall to help mitigate horizontal frost movement, and 4 in. of foam directly underneath the slab. Those are the simple steps.
The challenging part is the vertical slab edge insulation detail. Allowing the slab to be indirect contact with the outside world is not exactly energy efficient. To overcome this, we decided to pour a notch at the top of the interior side of the frost wall that would receive vertical insulation to act as a buffer between the slab and the exterior. A 2×6 plate is then secured to the frost wall that acts as a screed when pouring the slab and holds the vertical insulation so it doesn’t float up during the concrete pour.
It’s admittedly the weakest link in the foundation energy detail, but it’s pretty good in terms of balancing a lower upfront cost to the build while still providing a solid thermal boundary.
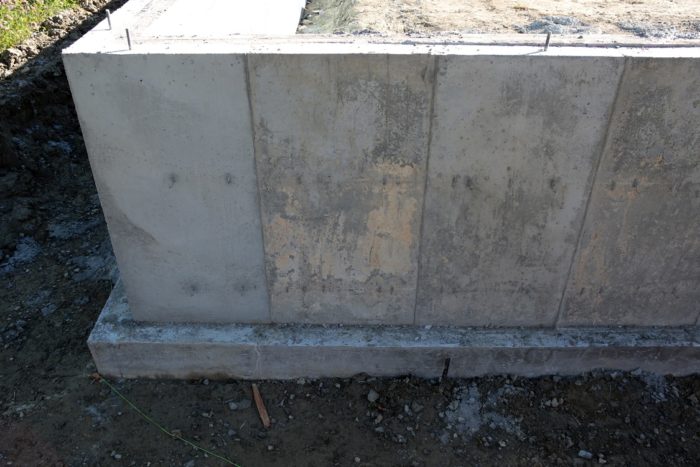
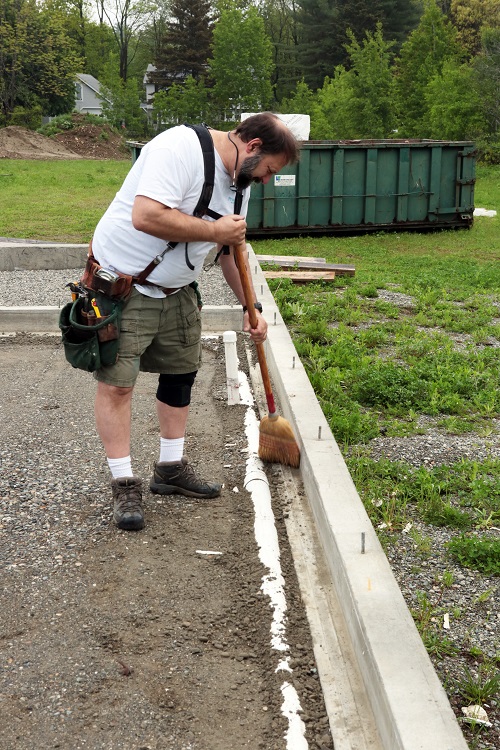
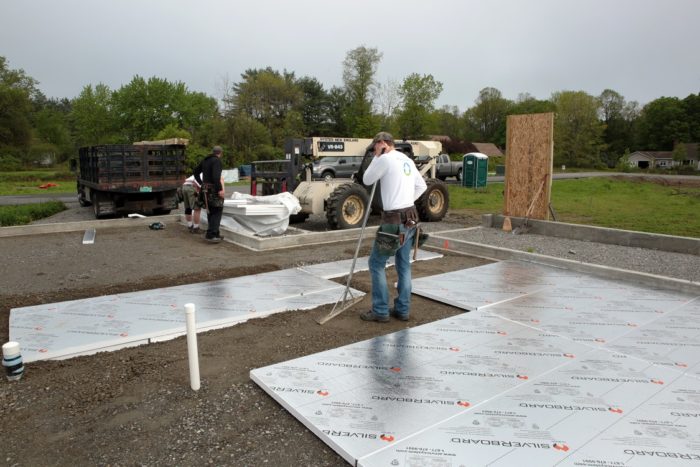
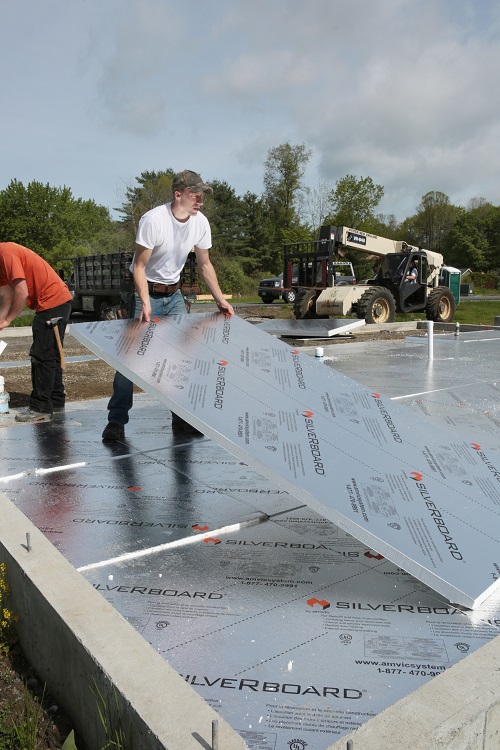
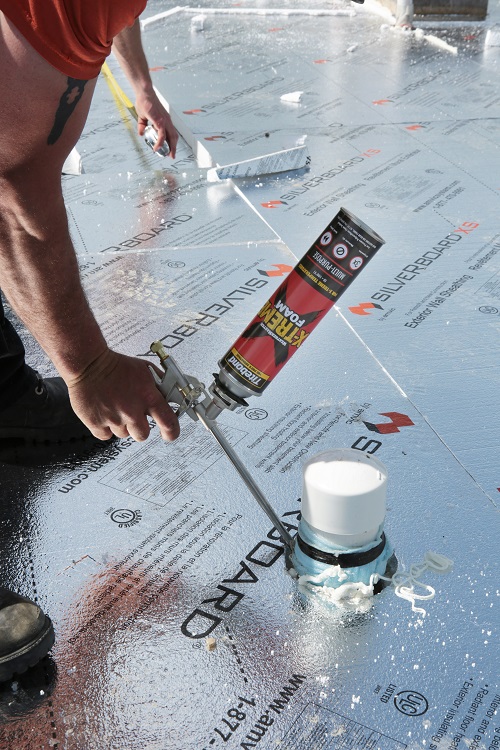
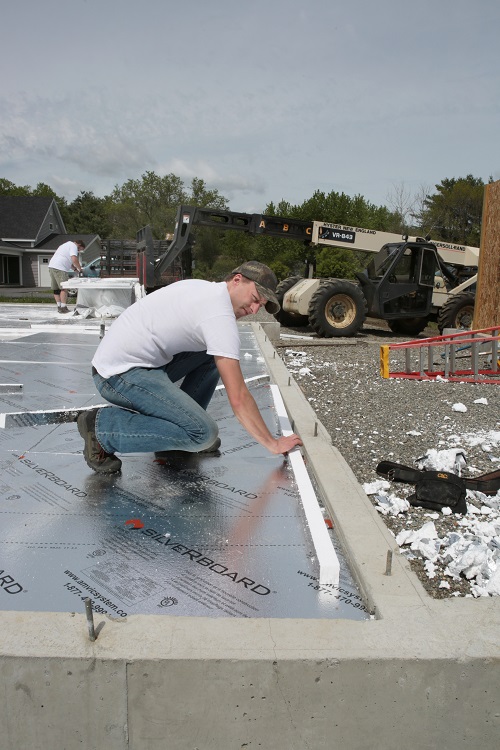
Fine Homebuilding Recommended Products
Fine Homebuilding receives a commission for items purchased through links on this site, including Amazon Associates and other affiliate advertising programs.
100-ft. Tape Measure
Utility Knife
Nitrile Work Gloves
View Comments
I need some better visuals for this one. I'm not following.
Please provide some images or illustrations. It would a lot! Thanks.
No horizontal rebar or wire mesh necessary?
I've said it before and I'll say it again. If you're only going to use, say, 4 inches of foam insulation, it is idiocy to put 2 inches on the outside, as with ICF. There is no reason why one would want to partly heat a heavy basement wall that is partly above ground. It takes vast quantities of energy to heat and cool that concrete wall, even to a nominal level. I regularly see it here on vacation homes in Ontario, where we get 3 feet ice on the (camp/cottage) lakes--yes 3 feet of ice. ...Get to the vacation place on Friday evening and the basement with the pool table is finally warm on Sunday morning, just in time to turn the thermostat down and leave for the week. (Great, it stays warm until Tuesday morning /sarc/) Does no one even turn down their thermostat when they go to work? Please don't tell me otherwise. I was a professor of engineering before retiring and I've experienced it at a friend's vacation retreat. If you're in one of those few rare areas that can almost get by without HVAC and this thermal mass can be of benefit, then OK.
Agreed, a drawing on this assembly would be super helpful. The article leaves too many details unanswered :(