Prediction 2010: New Home Construction Shifts from Job Site to Factory
Within the next 10 years pre-fabricated modular homes are going to take over the housing industry. Wait, before you start yelling, let me offer at least a brief explanation.
A perfect storm of changes
The whole industry is in a slump, we all know that. But it will rebound, and when it does, there will be more demand for a higher quality product. As energy costs increase and the existing housing stock dwindles, the average potential home buyer will want a house that’s well-built, energy-efficient, and affordable. The days of the big-box McMansion are coming to an end.
At the same time, more stringent energy codes will be here before you know it, forcing builders and developers of junk houses to put up or shut down. And the pool of experienced labor will continue to shrink as fast as the concept of a house as a complex of interdependent systems grows.
A glimpse at the future
And it’s starting already, albeit in dribs and drabs. (The slowdown hasn’t been much help to emerging companies.) People like Michelle Kaufmann/Blu Home, Resolution: 4, Rocio Romero and Bensonwood are just a quick sample of the people that are turning to a modern way of building. Why? It’s faster, the quality control is better so the product is better, and it costs less. It’s just what struggling builders and homeowners need.
Here’s what timberframer Tedd Benson has to say:
“In the next five years, there will be a huge transition on building sites where cutting and shaping will be rapidly eliminated, being replaced by value-added construction components, products and systems that will have been off-site cut, shaped and/or prefabricated, leaving the building site for assembly and installation only.
“I think this much is as inevitable as was the transition to off-site cabinets, windows, pre-hung doors and trusses. What is in question is the form that this pre-fabrication will take and what solutions will predominate. Answering that question is one of the biggest opportunities ever to come to the homebuilding industry.”
The notion of building a house by hand on-site is, in a lot of ways, a romance whose flame has died. There will always be a place for skilled people to build shelter, but the time will come when most of us won’t be able to afford to ignore a better house.
Fine Homebuilding Recommended Products
Fine Homebuilding receives a commission for items purchased through links on this site, including Amazon Associates and other affiliate advertising programs.
Handy Heat Gun
8067 All-Weather Flashing Tape
Reliable Crimp Connectors
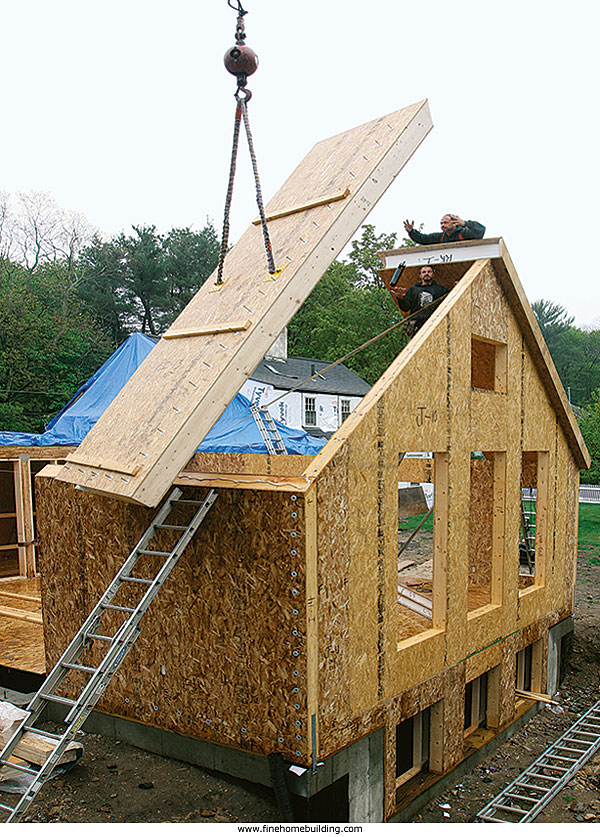
View Comments
The idea of manufacture, production line homes can be a sour subject. We know the route this type of operation can take in our country. I would hate to see our homes showing up at a NJ port in a box with a set of installation instructions. Please tread lightly.
I like this analogy.
Imagine that you finally decide to upgrade to fine luxury automobile like a Mercedes or Lexus. You visit with an automobile "general contractor, his designer or architect. They sketch out the new vehicle, you spend weeks emailing plans back and forth and reviewing 3D renderings online via "Gotomeeting". Finally you negotiate your trade in, get financing and sign the contract.
A week or so later, a crusher shows up. They take your old Lincoln out of the garage, crush it into a large metal cube and crane it into a dumpster.
Later that week, a variety of metal pieces are dropped next to the dumpster. Three workers in a huge Ford 350 pick up truck show up. They sit in the truck with the engine running for an hour, eating donuts and drinking coffee. Finally they come to the door and ask if the GC is inside your house. You say no, and they leave. You never see them again.
The next day a vacuum sealed, shrink-wrapped package of leather arrives via Fedex and 2 55 gallon drums of raw plastic blow molding compund show up on the lawn. Then the injection molder, sheet metal brake and portable hydraulic lift arrive.
A large wood box, 6 feet by 4 feet by 4 feet arrives, with "Do Not Open" printed all over it in the 30 EU languages. A worker shows up with a flat bed truck following and they crane a pile of aluminum and steel sheets next to the box. The crew covers the shiny, dry new metal with a tarp that looks like it was used for mortar practice at Ft. Bragg. It rains that night. Todays latet the rust stars forming.
You call your GC to discuss schedule and he promises that a large crew will arrive son. A week later they do and you are relieved. They spend all morning spreading the materials out, creating new piles. Five tires arrive. The crew goes for pizza and doesn't return.
The GC calls excitedly to tell you that the metal forming machine will arrive the next day. It does and a crew arrives to run it. Soon a huge amount of noise is coming from your front yard. It sounds like the boiler room scene from Titanic. Your neighbors call to ask when it will be over.
They work for three days and at sunset on the third day and you can see the front subframe coming together and smile. Your GC stops by at sunset, distributes a case of Miller Lite as the team opens the wooden box. They get it open and then spend a half an hour looking at it, reviewing paperwork and shaking their heads.
You watch with a feeling of doom as the GC trudges up to your door. You let him in and he explains that the over-seas engine and drive train supplier got the order wrong and sent two 4 cylinder engines instead of a V8. He mumbles something about taking 3 months to get the new one. You are disappointed and tell the GC that you are canceling the order.
Your spouse calls from work and asks how the "car" is coming. You tell her to meet you at the car dealership where you can order a car, built to your specifications and have it delivered in about 3 weeks.
Comment - We've been able to build and deliver modular homes since the Interstate highway system was completed in the US some 50 years ago. I just think the industry has been unwilling to give up their old ways. The new software allows consumers to walk around inside of a modular home with a builder, on line without the involvement of an architect. From final plans on a pc, a complete home can be sent out for bids. Factories can build to much tighter tolerances with predictable, qualified components to everyone's benefit.
And you know. If it's more profitable for homes to be designed online and the components to be built and delivered to a port in NJ by someone from another country working smarter, better, faster than competitors here, that's the American way. That's what the 'free market' is all about.
As my own contractor I just completed a 4,300 sq ft house that was in large part "factory" built. The timber framer brought the pre-cut timbers and assembled the frame. The SIPs manufacturer brought panels with door and window openings cut and framed and electrical boxes and conduit installed and hung them on the frame. Floor truss joists were made to order off-site. We still had to have traditional carpenters to lay the flooring, install windows and doors, frame the interior walls, hang the dry wall, trim and paint. We did use pre-finished fiber cement siding and trim and a standing seam metal roof rolled on site. Still a lot of traditional work was required: excavation, concrete and masonry work, plumbing and wiring and interior finishing. However traditional hand tools were rarely used. Nearly every nail was driven with a pneumatic nailer, screws with cordless impact drivers and cuts made with power tools of one form or another. At one point a cut had to be made that couldn't be made with a circular saw or a reciprocating saw. I said "I can cut that with my cordless saw." and the crew was a little chagrined to see me cut it with a traditional hand saw. (I don't think any of them had one.) House construction now is a far cry from the completely hand-built houses I watched built as a kid 60 years ago. Houses may not be "factory" built in the near future, but materials, tools and techniques will continue to evolve.
as we have experienced with cabinet fabrications, Europe is already ahead with prefabricated home construction.
Even foundationwalls can now be ordered made to measure.
Move - in dates can be as low as 3 weeks from completion of foundation subfloor.
In Vancouver BC some companies were up and running with this system until the Japanese market collapsed.
What will be next? Wal-Mart build your own?
I have an idea who's time has come: How about WE figure out how to do this more efficiently and ship the houses to THEM? Seriously, withoug getting dwelling on the whole globalization subject and who it has benefitted (and who it has not), I'd like to see the US pioneering technology in SOMETHING again. We're already behind Europe and China on some green power generation technologies, but it's not too late to forge ahead again. We can do the same with modular home technology, and perhaps even implement it all the way through the efficient manufacturing of integrated building components. I'm sure other nations can build warships pretty well too, but we build our own here anyway and have therefore become very good at it, - to the point where we can sell them abroad. We can do the same with building components.
As for eliminating Architects in the process: Who will design these houses? Interior Designers? And the need to knit together the multiple building codes that modular homes must satisfy will be done by____? Architects can make it meet the codes, fit the customer's needs, AND look good doing it. I don't know who else will be qualified enough to do so. (Please don't tell me that contractors will, - that's how we got a nation full of bloated McMansions in the first place).
I'm extremely enthused about the possibilities, but apprehensive that there are still so many people stuck in selfish mindsets, hoping to cling to the past just a little longer, mocking and undermining all efforts to improve the way we do things. They don't care if large numbers of people don't have housing, - that's not their problem. They don't care to do anything more efficiently unless either the government makes it unavailable or the cost goes through the roof (even then, some will still pay it). Since the price changeover takes time, they will procrastinate until there is no other option. You know, it's the same with bad teeth, - there are still a lot of people who only go to the dentist when they're ready to have them pulled.
So I say, bring on all the change now. The sooner we get on with it, the sooner we'll all feel some benefit.
We must not forget the many skilled tradesmen whose quality of life will be sacrificed. It seems that the more Corporate we become the less personal operations become. How many times has an experienced tradesperson had to correct the errors of so called professionals in order to satisfy the customer.
It goes without saying that our actions of "the past" affects our choices in the future. The need for quality, energy efficient, green homes exists regardless of where we live. However, the road to this goal should not be scattered with the corpses of skilled trades workers. We can not afford to lose skilled and knowledgable workers for the sake of producing houses even more quickly than we do today. The production of quality, environmentally friendly, energy efficient homes should be a "no brainer". Educating and training for future home builders needs to include the element of innovative change. Hopefully the homebuilding industry can avoid many of the problems that plague the North American automotive industry.
Can we learn and accept that a family of four does not need 4000sq.ft. of living space just because we can manage the mortgage at historically low rates?
Can the industry develope appropriate responses to meet the nations housing needs? It is not just a matter of new technologies and techniques but also of finding ways to provide affordable housing. Appropriate solutions that do not do to the building industry what poor planning and lack of vision has done to the automotive industry are what is required . This does not mean that every family will be able to afford to buy a home, but it should mean that they get to benefit from those changes that come from new improvements in the industry.
It may be wise to remember that while nature fills a vacuum that the vacuum shouldn't be between our ears.
cat 5 proof and affordable with many ancillary benefits:
http//:www.keywesthomescat5.com